How to do Root Cause Analysis? Everything You Need to Know
Performing a root cause analysis is an invaluable problem-solving tool for any organization. At its core, root cause analysis (RCA) aims to uncover why issues arise by systematically evaluating contributing factors.
Once the underlying causes behind these problems are understood, teams can not only address the immediate symptoms but also take proactive preventative measures for the long term.
Learn systematic methods to prevent problems before they escalate!
Master Root Cause Analysis and transform problem-solving approach
Utilizing a data-driven methodology, root cause analysis gets to the bottom of quality, reliability, safety, and process inefficiencies.
By figuring out the true roots instead of just the obvious proximal causes, you diagnose the real reasons defects emerge, errors happen, failures occur or goals aren’t met.
The goal extends beyond resolving a one-time incident – it’s about fixing systemic gaps to avoid repeated future stumbles while continuously improving performance.
What is Root Cause Analysis?
Root cause analysis (RCA) refers to a set of approaches leveraged to uncover the underlying explanatory factors or root causes behind problems.
Essentially, RCA provides a structured investigation process for identifying the true sources from which issues emerge in systems, products, workflows, or outcomes.
Whereas our instinct is often to address the most visible or proximate causes behind defects, errors, or negative events, root cause analysis deliberately digs deeper.
RCA diagnosis traces behind the symptoms to the source inputs, process weaknesses, and capability gaps giving rise to those surface-level problems.
This tracing back from consequence to cause requires analyzing the interconnected relationships within a system to find originating triggering points upstream where sustainable solutions can be targeted.
Goals of Performing Root Cause Analysis
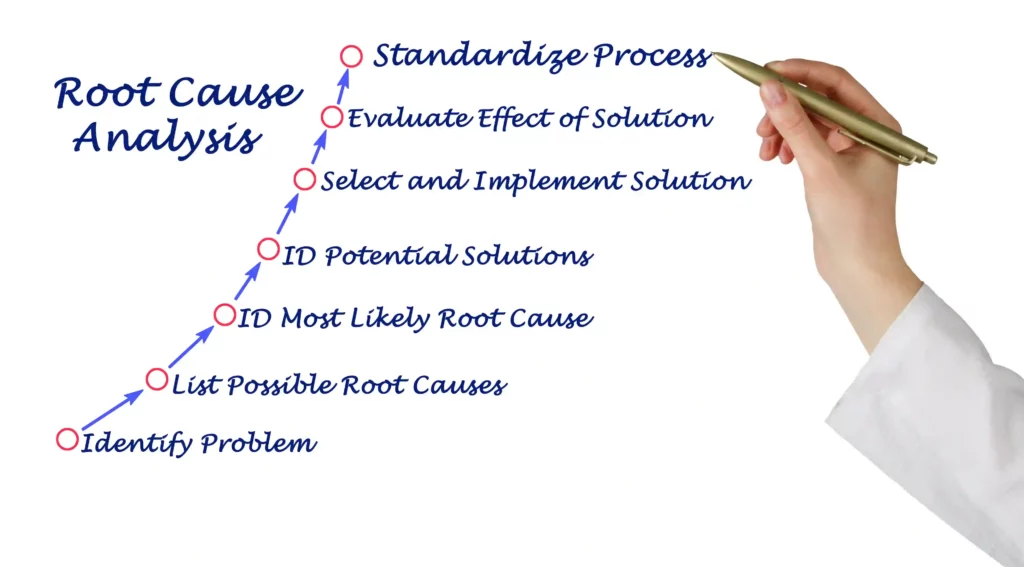
There are three overarching goals fueling investments in root cause analysis initiatives:
Identify Underlying Problems
The foremost objective is to systematically diagnose the fundamental breakdowns or gaps responsible for the manifestation of issues.
As opposed to only compiling a list of contributing factors or observable indicators, RCA pursues the identification of the truly originating root deficiencies being tapped as the problem’s supply source.
Take Corrective Action
The second purpose is to facilitate solution development targeting root causes for resolution.
Armed with insights linking specific deficiencies to negative outcomes, corrective interventions can be scoped to strategically address the problem’s inputs rather than applying superficial Band-Aids to outputs.
Investing in fixing root drivers substantially increases the soundness and sustainability of corrective actions taken.
Prevent the Recurrence of Issues
Lastly, the ultimate motivation is the prevention of issue recurrence through eliminating or controlling the root sources.
By remediating root causes and monitoring to confirm resolution, RCA strengthens system reliability and performance to avoid repeated failures manifesting in the future.
Hence required effort for rework decreases as problems stemming from the same unchecked root weaknesses cease to persist.
Steps for Conducting Root Cause Analysis
When executing a root cause analysis, there is an overall investigatory process containing key phases to follow for orderly problem diagnosis.
Walking through these main RCA steps lends structure to facilitate systematic root cause identification.
They provide foundational guidelines while deploying the specialized root cause analysis tools and methodologies covered later.
Define the Problem
The first step when approaching any root cause analysis is to clearly articulate the problem you aim to address. This includes accurately describing the issue’s observable characteristics and quantifying the impacts witnessed thus far.
Define Specific Symptoms
Closely detail what is going awry to precisely scope the problem. Document factual indicators tied directly to performance shortfalls rather than vague hunches something is amiss.
Quantify discrepancies between expected versus actuals. Capture failure modes. Outline errors committed or protocol breaches. Log quality defects surfacing. Probe to gather data-backed specifics.
Understand Current Impacts
Quantify how these presenting symptoms translate into tangible setbacks. Connect observable indicators back to resulting consequences like goals underachieved, costs incurred, risks introduced, and other impacts.
Dimension the scope of influence including breadth across the customer base, affected product lines, or process phases. Demonstrate why solving this problem merits prioritization based on the depth of existing impacts.
Solid problem definition focusing on the analysis ultimately determines how effectively root causes will be found.
An accurate statement captures factual symptom patterns plus impact measurable tied to those reliability, quality, or performance defects witnessed.
That evidential grounding seeds direction for the data gathering and causal evaluation ahead.
Gather Information & Data
With a well-defined problem statement guiding the root cause analysis, attention next turns to gathering contextual input and evidence associated with the issue.
Create a Timeline of Events
Work backward chronologically to chart out key events preceding and proceeding with observable defect occurrences. Capture operational data, process logs, related audit records, and other artifact sources to reconstruct event sequences.
Consider perspectives like:
When exactly did defect indicators initially surface? Under what conditions or phase activity? After what system, input, or human touchpoint? Any correlative or high probability causal associations?
Seeking process flow understanding, catalog multi-tiered sequences of events, including upstream supplier activities, to identify potential propagation pathways giving rise to defects.
Document Contributing Factors
Beyond driving process factors and event chronologies, also gathers ancillary variables that likely influence or contribute to issue occurrence even if not as primary drivers.
Consider documentation, insights from staff interviews, related incidents, past mitigation actions, and other clues that shed light.
Record as many hypothesized contributing factors as possible early on. This compilation supports connecting the dots during causal analysis without prematurely dismissing the potential relevance of surrounding variables.
Through compiling events data and rounding out clues, these background informative sources feed into the causal analysis techniques to next diagnose just what latent weaknesses propagate or allow these problems to keep resurfacing.
Identify Causal Factors
With foundational information gathering completed, the next phase applies analytic techniques to start unraveling contributory causal linkages tied to the focal problem.
A diversity of root cause analysis tools can methodically assess hypotheses on factor interdependencies.
Use Analysis Tools Like 5 Whys and Fishbone Diagram
Structured brainstorming combined with visual mapping formats help investigates the likelihood of causal relationships across documented contributing variables and process flow events. For example:
– The 5 Whys approach sequentially probes with “why” questions to follow explanatory chains probing closer to root causes.
– Fishbone diagrams visually organize causal factors under typical categorical influence dimensions like manpower, machinery, materials, methods, and more.
These analysis tools support rooting out key drivers versus ancillary variables amongst the stack of hypothesized factors initially compiled.
Determine Relationships Between Factors
Beyond naming factors, RCA analysis seeks to assess interrelationships – which elements potentially influence other elements either directly or in relayed sequences.
This mapping of connections across current state process steps, inputs, human decision points, and other variables constructs the pathway model of how certain vital few deficiencies propagate to enable the ultimate problem manifestation.
Solid analysis output accounts for factor likelihood and strength of relationships across the mapped flow.
Statistical, experiential, and consensus estimation techniques help qualify those key linkages for further root cause assessment.
Pinpoint the Root Cause(s)
Having constructed a relationship model across contributing variables and process flow events, attention hones in on tracing the originating root causes behind the mapped issue.
This diagnostic phase isolates the vital few originating causes to target for correction.
May Be Multiple Root Causes
Especially for complex problems, multiple root failure points may independently or jointly propagate deficiencies tied to the end observable defect.
Isolate multiple contributing root causes rather than stopping at just one initial discovery.
Distinguish Between Causal Factors
When analyzing to pinpoint the deepest root sources, it is critical to differentiate causal factors from root causes.
Causal factors directly contribute to the problem but are not the underlying deficiencies enabling the causal chain.
True root causes originate upstream as the vital inputs or process weaknesses initiating the downstream consequence cascade.
Confirm root cause isolation by assessing if its resolution would eliminate the issue while simply addressing each causal factor alone would not resolve the problem long term.
This testing of whether fixed roots would break the failure sequence helps verify root cause validity for targeted corrective action ahead.
Implement Preventative Solutions
With verification of the root factors enabling the business problem’s occurrence, attention lastly turns to enacting changes to address exposed deficiencies for prevention.
Develop a Corrective Action Plan
Define a project plan oriented around enhancing control of the vital root inputs or strengthening process elements to minimize propagation likelihood going forward.
Corrective actions directly target diagnosed deficiencies rather than applying generalized fixes.
Attach owners driving execution of enhancements like input specification improvements, adding process controls, capability development interventions, technology system changes, and more as tied to root issue resolutions.
Allocate Resources
Determine appropriate budget, staffing, infrastructure, and stakeholder access supports to facilitate execution against planned corrective initiatives. Resource design elements of the improvement plan for priority consideration.
Assign Responsibilities
Designate owners to carry through and sustain fixes critical for remediating diagnosed root weaknesses.
Assign subject matter experts tailored to focus areas like procurement, quality assurance, data analytics, applications, and more.
Maintain accountability via governance check-ins to validate containment of root factors enabling the original business problem faced.
Getting ahead of problems requires getting beyond just reactive firefighting. Root cause analysis provides an alternate mindset and procedural approach to transform from responsive defense to reliable prevention.
Leveraging the steps outlined transforms troubleshooting guesswork into solid problem diagnoses for impactful corrections that stick.
Integration of Root Cause Analysis (RCA) into Lean Six Sigma Methodologies
It states that RCA goes beyond addressing surface-level symptoms by systematically uncovering underlying causes to improve quality, reliability, safety, and efficiency.
The key takeaways extend into three overarching goals: identifying underlying problems, taking corrective action to address root causes, and preventing the recurrence of issues.
Various analytical tools, such as the 5 Whys and Fishbone Diagram, are discussed, showcasing how RCA can be effectively applied across various sectors to enhance performance.
Connection to Lean Six Sigma Principles
Root cause analysis encapsulates a systematic approach that mirrors key principles within Lean Six Sigma.
Both methodologies emphasize the necessity for thorough data collection and structured problem-solving, aiming to identify not just immediate issues but rather the systemic root causes allowing those problems to persist.
Earning a Six Sigma certification equips practitioners with the analytical rigor to apply RCA within Lean Six Sigma’s DMAIC (Define, Measure, Analyze, Improve, Control) framework, ensuring sustainable solutions.”
Focus on Continuous Improvement
RCA is inherently aligned with the Lean Six Sigma ethos of continuous improvement (CI).
By addressing root causes rather than merely symptoms, organizations can enhance their processes to prevent future issues.
This focus on sustainable performance improves not only current outcomes but builds a foundation for ongoing excellence—a central tenet of Lean Six Sigma culture.
Data-Driven Methodologies
RCA’s reliance on data is an integral connection to Lean Six Sigma practices.
Emphasizing facts and evidence over assumptions, both methodologies work hand-in-hand to drive informed decision-making.
Custom Integration of RCA Concepts into Lean Six Sigma Practices
Professionals pursuing Six Sigma certification often learn to integrate RCA into Lean Six Sigma projects, enabling them to diagnose systemic issues while driving process optimization.
This would ensure teams not only understand RCA as a standalone process but can also effectively employ it within the broader context of continuous improvement efforts.
Establishing RCA Governance Mechanisms
Establishing governance around RCA practices allows organizations to create a framework for accountability and oversight.
Implementing standardized protocols and documentation processes strengthens RCA efforts and enhances quality control.
By adopting these principles, Lean Six Sigma practitioners can maximize the benefits of RCA, embedding it within their structures to promote ongoing enhancements in quality and efficiency throughout their operations.
This proactive approach to understanding and addressing challenges positions organizations for sustained success.
For teams seeking structured RCA and Lean Six Sigma training, our Six Sigma Green Belt certification offers hands-on practice with tools like Fishbone Diagrams and Control Charts.
Tools for Root Cause Analysis
While the root cause analysis steps provide an overarching process, there are also many specific tools and techniques leveraged by practitioners to enable effective problem diagnosis.
These methodologies lend rigor and an evidence-based lens guiding productive analysis execution.
No one-size-fits-all tool exists as finding root causes encompasses a toolkit approach aligning techniques to problem complexity, organizational maturity, and analytics staff capabilities.
A variety of options cater better to deductive versus inductive analysis styles. Certain tools simplify tackling human versus process-driven deficiencies.
Below we will describe some of the most popular and impactful options as an introductory sampling of root cause analysis tooling available to drive actionable findings.
Looking across the techniques, common elements like visual mapping combined with iterative questioning enable unraveling factor connections. Statistics quantitatively point toward viral variables.
While no single method will perfectly fit every business environment, evaluating options against internal needs allows customizing an RCA toolbox for repeating success.
Let’s look at how to use 5W, fishbone diagram, fault tree, etc. to run a Root Cause Analysis.
5 Whys Technique
The 5 Whys approach represents one of the simplest root cause analysis tools, asking “why” iteratively to trigger deeper-dive brainstorming on contributory factors. By sequentially questioning “why” around five times, analysis can often get to root causes efficiently.
Ask “Why” Questions Iteratively
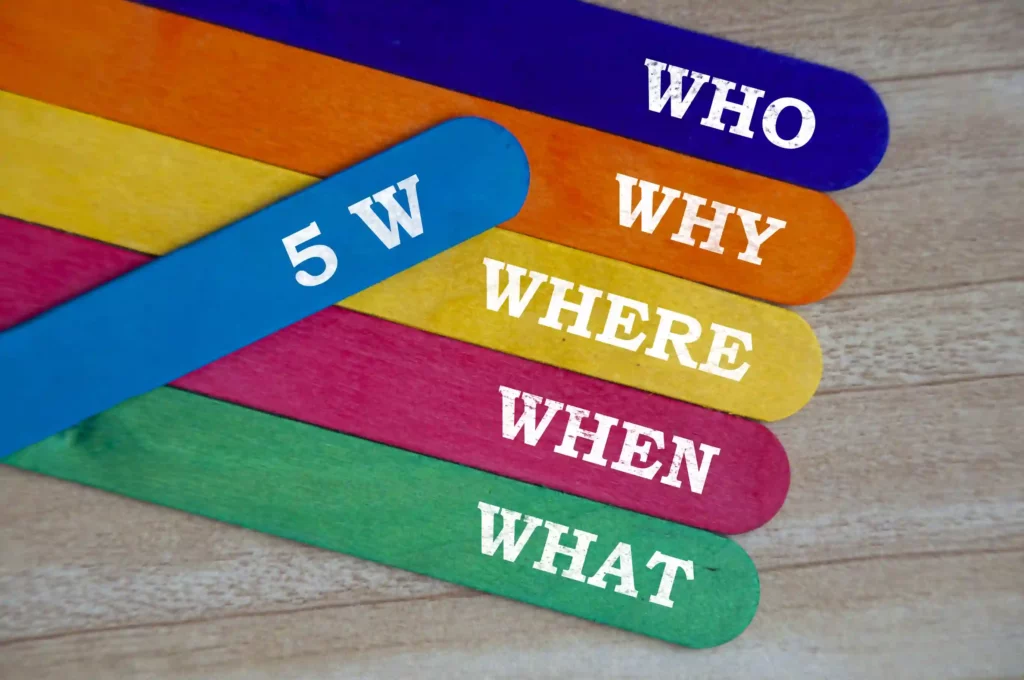
Start with the problem indicator as documented. Ask why it is occurring. For the explanation received, again ask why regarding that reason.
Continue asking why around five+ times until reaching a root originating cause rather than just symptoms or intermediate factors.
The key is not stopping at superficial responses. Use follow-on probing around systemic relationships to get beyond guesswork into sourcing vital causal inputs behind issues. Answer chains build an explanatory logic trail.
Fishbone Diagram
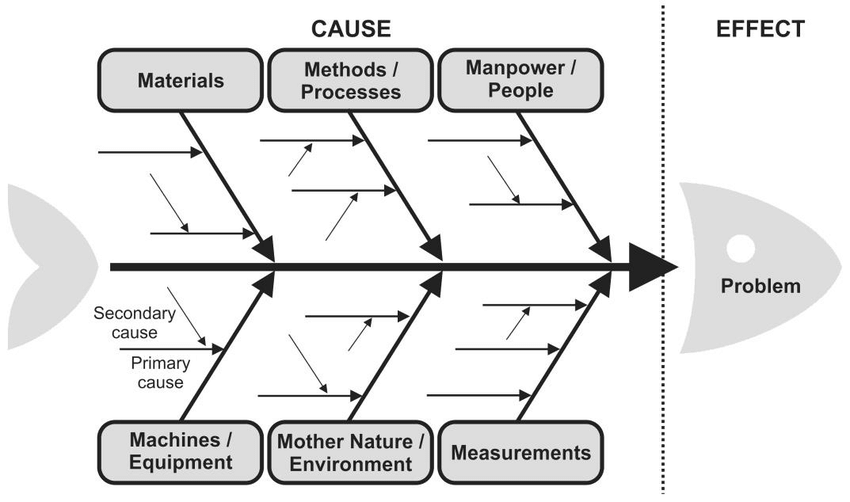
The fishbone diagram compiles a visual catalog of causal variables for organized analysis facilitating potential root cause identification.
As factors accumulate and interrelate in complex ways, this format supports assessment efficiency.
Visually Map Causal Factors
Fishbone diagrams provide an intuitive visual roadmap of multiple categories of influencing factors like materials, machinery, staffing, and methods.
This organization into standard dimension groupings eases assessing angle applicability to the issue context. Breaking down by factor type combined with team discussion aids in root cause emergence.
Fault Tree Analysis
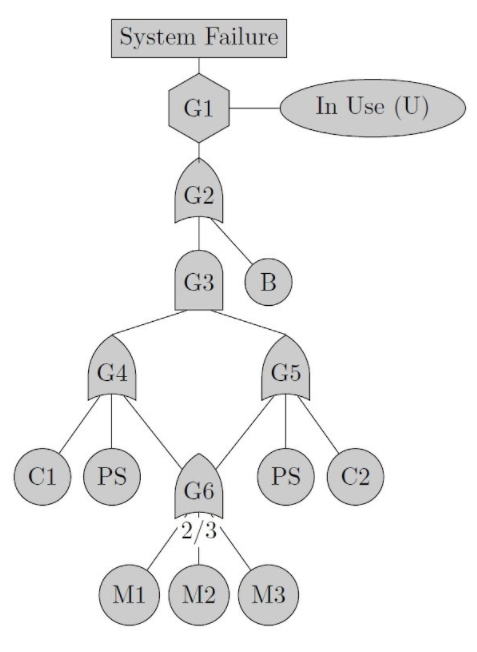
Fault Tree Analysis offers a structured deductive approach applying boolean logic for disciplined qualification of factor likelihood and interconnectedness to narrow resolving power onto root causes.
Deductive Root Cause Analysis
In a fault tree diagram, the undesired state requiring diagnosis sits at the top. Sub-branches then visually map how that state could logically occur based on combinations of certain lower-level events and conditions using “AND” and “OR” logical operators.
Walking through documented branches and assessing the likelihood of reaching originating root factors at the base of the tree provides evaluation rigor.
Fault tree branches knocked out via factor improbability allows deductively focusing in on the active root causes behind an issue.
Failure Mode & Effects Analysis (FMEA)
Failure Mode and Effects Analysis offers an anticipatory approach to risk analysis applied for early identification of vulnerabilities permitting problems before they emerge. It statistically quantifies criticality toward issues to guide control priorities.
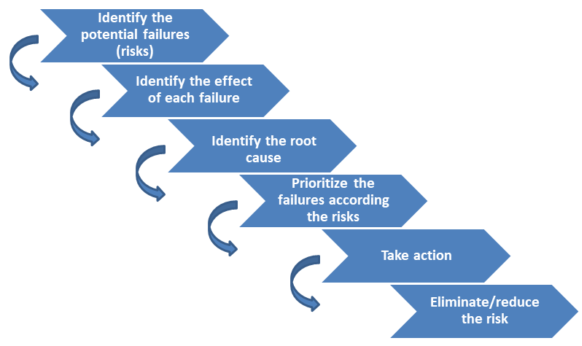
Predictive Identification of Failures
Potential failure modes are hypothesized along with estimating their likelihood to manifest and the severity of impact if occurring. A risk priority number mathematically combining probability and consequence severity indicates the highest priority vulnerabilities for proactive mitigation efforts.
FMEA analysis flows through these steps:
- Documenting process flows and system design specifications.
- Cataloging where and how failure could theoretically occur.
- Rating probability and severity estimates for each failure mode.
- Calculating weighted risk priorities steering mitigation targeting.
- Developing controls and contingency responses aligned to top risks.
Getting ahead of downstream issues, FMEA provides an alternate lens complementary to retrospectively investigating executed failures through other root cause analysis approaches.
It serves prevention needs rather than just diagnosis for organizations’ maturing quality system reliability and performance benchmarks.
Applications of Root Cause Analysis
While originally pioneered in industrial environments, root cause analysis has expanded across functions from product design through end-user support to unlock business performance, operational efficiency, and continuous improvement advances.
Root cause analysis seamlessly integrates into Lean Six Sigma cultures demonstrating infrastructure capabilities enabling reliable prevention. However, any organization in search of elevating standards, systematizing enhancements, or diagnosing tricky recurring issues can benefit from instituting RCA capabilities.
Manufacturing & Quality Control
Eliminating waste while improving quality, safety, and delivery benchmark attainment all require understanding vital causes behind unacceptable variation. RCA offers manufacturing analytics to optimize flow.
Reduce Defects & Waste
Learn why rejection and rework rates fail to meet control standards. Identify source impurities decreasing yield. Discover where bottleneck throughput lags emerge.
Optimize prevention resources against diagnosed vital few equipment failure modes. Get to root design weaknesses prompting field failures.
RCA provides manufacturing analytics illuminating upstream process vulnerabilities and product robustness gaps that quality engineers can re-engineer to reduce downstream waste.
The evidence-based insights fuel continuous improvement prioritization essential for operational excellence.
Software Development
IT leaders applying root cause analysis to diagnose tricky software defects optimize quality assurance. Pinpointing true error triggers versus symptoms provides effective resolutions by seasoned developers.
Bug Tracking and Resolution
Applying investigative questioning around runtime errors and customer-reported issues provides clarity to trace back through requirements, architecture, and code base vulnerabilities introducing those bugs.
Similarly, managing outages and performance degradations benefits from RCA lifting the hood on dependencies and resource contention under the covers.
Business Process Improvement
Every business leverages processes crossing functional teams, underlying technology, and spanning external partners.
Root cause analysis gifts a microscope to optimize flow efficiency, reliability, and experience.
Identify Process Inefficiencies
Document as-is workflow steps, decision points, and outputs. Measure improvement needs around cycle time, work transfers, rework loops, constraints impacting costs or service levels, and roadblocks frustrating customers. Construct current state process maps highlighting pain points.
Conduct RCA to diagnose root design, capability, and capacity gaps disadvantaging flow. Re-engineer based on evidence vs. assumptions alone.
From manufacturing shop floors to software quality assurance to overall business productivity, root cause analysis crosses functions to drive operational gains.
RCA provides insights to strengthen the weakest links recognized across integrated processes and systems that compromise broader performance.
Best Practices
While the methods and tools empower root cause analysis execution, real-world success also depends on engagement, analysis, and implementation excellence.
Various best practices should be fostered around the people, process, and leadership elements involved with RCA.
Involve Cross-Functional Teams
Gathering a diversity of experts across functions touched by the problem to be diagnosed provides analytical breadth bolstering findings. Cross-functional collaboration harnesses different vantage points, experiences, and expertise to enrich RCA direction and outcome integrity.
Harness Different Perspectives
Multidisciplinary participation facilitates a well-rounded understanding of the current state, ideas on latent improvement opportunities, and balanced decision-making interpreting causes.
Consistent involvement across phases also strengthens buy-in critical for solution adoption success downstream.
With a breadth of lenses applied, creative identification of root causes overlooked otherwise comes to light.
Expanding beyond just technical leads or coaches facilitating RCA, hands-on participation across the various functions interfacing with the process or system under review will enhance analysis productivity and solution integrity.
Such collective ownership through the root cause journey propagates engagement critical for executing against recommended enhancements as well.
Create Blameless Culture
Effectiveness finding actual root causes relies on an environment promoting open transparency rather than fear of retribution. When people feel psychologically safe to share knowledge of vulnerabilities, higher quality analysis unfolds.
Encourage Transparency About Problems
Leaders must nurture a “blameless culture” where the focus stays on collective learning rather than targeting culpability.
Model inquisitive questioning, acknowledge contributions, and recognize success in uncovering insights. Establish RCA as an ongoing collaboration operating across functional boundaries.
Proactive sharing accelerates and enhances analysis, whereas environments allowing blame induce hiding failure observations essential for follow-on diagnostics.
Focus on True Root Causes
The end objective focuses on remediating deficiencies at originating sources instead of addressing symptoms alone. Repeatedly confirmed analysis dives deeper beyond the superficial factors initially evident.
Don’t Just Address Superficial Factors
Guard against analysis stagnation at intermediary contributors versus tracing further upstream toward vital root causes.
Leaders should constantly calibrate direction to pursue root factors that if remedied would prevent issue recurrence as the litmus test qualifying properly scoped RCA.
The core principles empowering successful root cause analysis encompass engagement models promoting transparency rather than fear while enabling deep analytic rigor refusing to settle on surface causes.
Adhering to these foundational practices pays dividends with more impactful insights and solution implementation.
Key Takeaways on How to do Root Cause Analysis
Root cause analysis provides a vital capability for any organization seeking to move beyond reactive firefighting toward reliable prevention.
While requiring investment and competency development, proficiency in paying RCA dividends emerges across operational efficiency, quality, customer experience, and financial performance outcomes.
RCA Helps Diagnose and Prevent Recurring Issues
Whether tackling sporadic issues or systemic defects, RCA gifts objective precision guiding corrective enhancements aligned to true underlying failure points.
The evidence-based analytical approaches uncover root causes that if remediated proactively contain issue recurrence likelihood.
Next Steps
The foundational overview shared introduces what, why, and how regarding root cause analysis. Several next milestone steps merit consideration for instituting RCA practices tailored to your organization’s needs.
Implement RCA Methodology Tailored to Your Needs
- Build Leadership Alignment: Confirm executive support to foster an engagement model and allocate resources enabling RCA productivity as a priority capability.
- Launch Training: Organizations can accelerate RCA adoption by enrolling teams in Six Sigma certification programs, which blend root cause analysis with Lean tools like Value Stream Mapping and waste reduction strategies.
- Standardize Governance: Define policies and collaborative forums providing oversight, best practice sharing, efficiency optimizations, and corrective action accountability across the RCA lifecycle.
- Start Small, Demonstrate Quick Wins: Pilot RCA diagnosis and solution implementation for an important business issue to showcase capability value realized.
Root cause analysis success requires work – from leadership, staff skill development, and process adoption. However, embracing RCA thinking and methods delivers a multiplier effect on operational gains to continue building competitive advantage.
Now is the time to get started or expand your RCA journey!
Summary
The root cause analysis is a very helpful process in understanding as well as finding solutions to the problem. These indispensable tools will help you conduct this process more efficiently.
Stop by and contact us at 6Sigma.us and find out how we can positively help you plan and change the culture and operations of your organization. We offer Six Sigma Green Belt and Six Sigma Black Belt training programs, as well as a Master Black Belt program.
SixSigma.us offers both Live Virtual classes as well as Online Self-Paced training. Most option includes access to the same great Master Black Belt instructors that teach our World Class in-person sessions. Sign-up today!
Virtual Classroom Training Programs Self-Paced Online Training Programs