Lean Project Management: Maximizing Value and Eliminating Waste
According to a recent McKinsey study, organizations that implement lean project management principles can substantially improve productivity, sometimes by 50–60% in construction, but results vary by industry and implementation.
These aren’t just impressive numbers—they represent a fundamental shift in how successful teams approach project execution.
Transform your project delivery with proven lean techniques
Learn directly from industry-leading Master Black Belt instructors with Lean Fundamentals.
Lean project management combines time-tested efficiency principles with modern project delivery methods to eliminate waste and maximize value.
Key Highlights
- Essential lean principles for project success
- Waste elimination strategies that work
- Practical implementation steps and tools
- Real-world case studies and results
For those looking to formalize their process improvement knowledge, our six sigma certification program offers complementary skills that pair perfectly with lean methodologies.
What is Lean Project Management?
Lean project management focuses on maximizing customer value while minimizing waste throughout all project phases.
This methodology strips away unnecessary activities, streamlines workflows, and centers every decision around what truly matters to stakeholders.
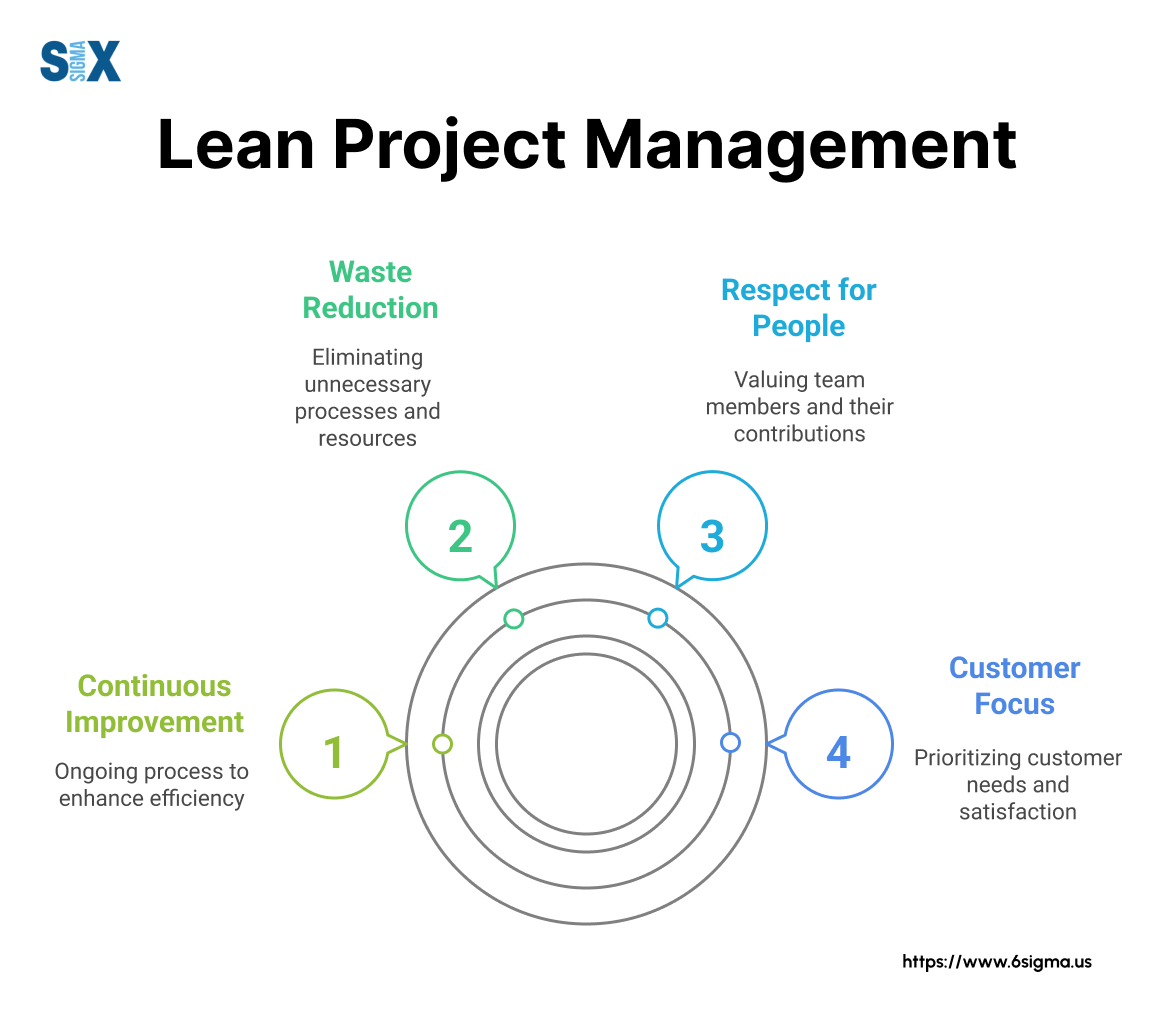
Unlike traditional approaches that often emphasize rigid planning and extensive documentation, lean project management embraces flexibility, continuous improvement, and customer-defined value.
The story of lean project management begins with Toyota in post-WWII Japan. Facing material shortages and limited resources, Toyota engineers Taiichi Ohno and Eiji Toyoda developed the Toyota Production System (TPS) during the 1950s and 1960s.
This revolutionary approach enabled Toyota to produce high-quality vehicles with fewer resources than their American competitors.
The system focused on eliminating three types of waste: muda (non-value-adding activities), mura (unevenness), and muri (overburden).
Western manufacturers took notice of Toyota’s success, with researchers from MIT coining the term “lean” in the late 1980s.
James Womack, Daniel Jones, and Daniel Roos documented these principles in their influential 1990 book “The Machine That Changed the World“, bringing lean thinking to a global audience.
The leap from manufacturing to project management occurred gradually throughout the 1990s and early 2000s.
Project managers in various industries began adapting lean principles to knowledge work, service delivery, and project execution. The publication of “Lean Thinking” by Womack and Jones in 1996 helped codify the five core principles that now form the backbone of lean project management methodology.
Today, organizations across sectors apply lean project management to deliver projects more efficiently.
From software development to construction, healthcare to financial services, the lean project management methodology helps teams eliminate waste and focus resources on value-creating activities.
This customer-centric approach represents a significant departure from traditional project management’s focus on delivering predefined outputs according to plan.
For teams new to these concepts, our lean introduction program provides valuable context, while those ready to dive deeper might explore the fundamentals of Lean to build a stronger foundation in project management lean methodology.
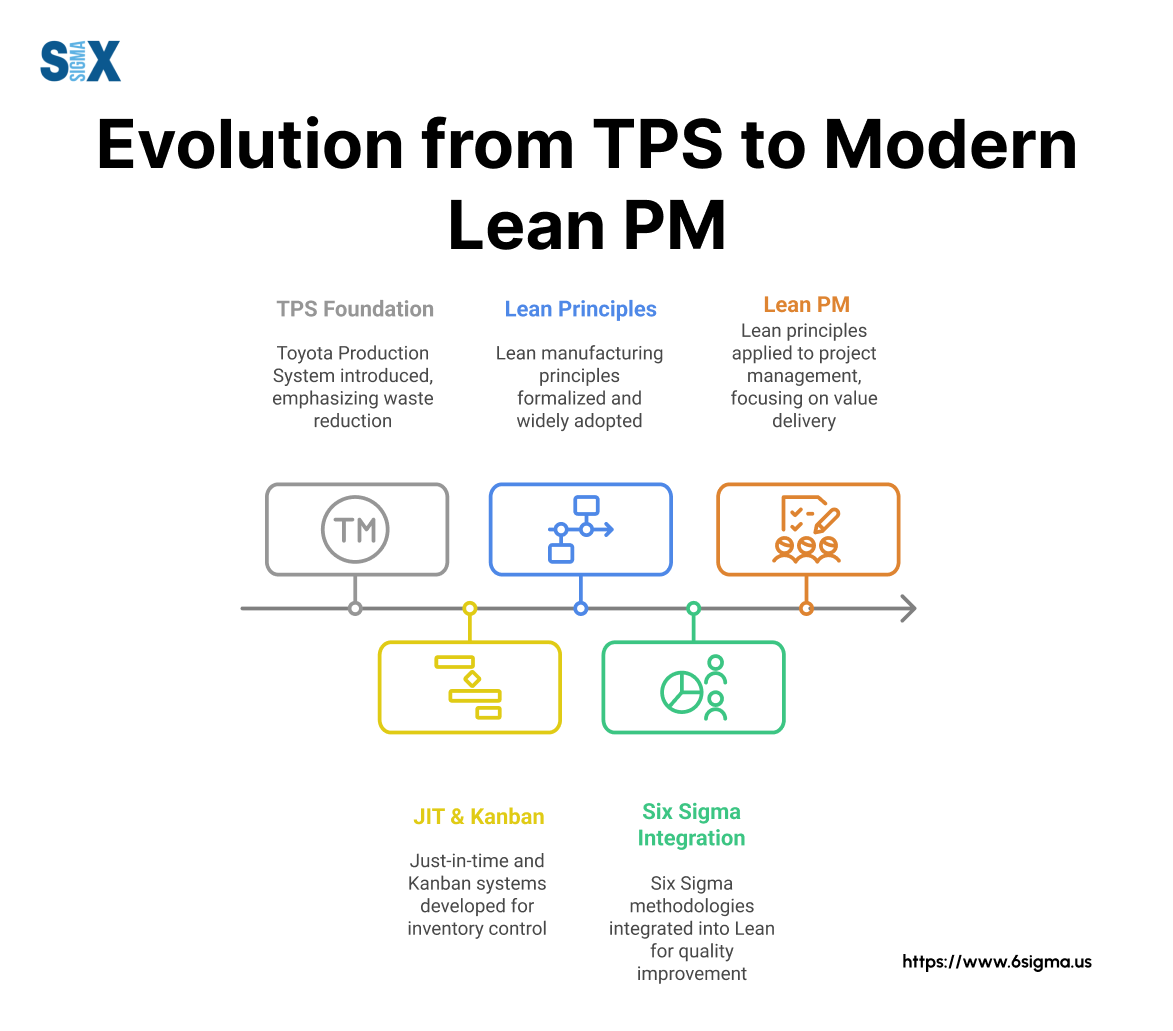
The Five Core Principles of Lean Project Management
Lean project management transforms how teams deliver projects by following five essential principles.
These principles, first outlined by James Womack and Daniel Jones in their book “Lean Thinking“, provide both the philosophical foundation and practical framework for eliminating waste and maximizing value in project environments.
Value Definition
The journey toward lean project management begins with a laser focus on value—specifically, value as defined by the customer or stakeholder.
This principle requires project teams to look beyond internal assumptions and directly engage with stakeholders to understand their true needs and expectations.
Many projects fail because teams assume they understand what customers value without proper validation.
Defining value requires answering critical questions: What problem are we solving? What benefits must our deliverables provide? What would make this project a success in the customer’s eyes?
Value Stream Mapping
Once value is clearly defined, lean project teams map the entire process required to deliver that value from start to finish.
Value stream mapping visualizes all activities, information flows, and dependencies involved in delivering the project outcomes.
This critical step reveals where value is created and where waste exists in the current process.
A typical value stream map shows all activities required to deliver the project, time requirements for each activity, waiting periods between activities, decision points, information flows, and quality control checkpoints.
Flow Creation
After identifying the value stream, lean project teams work to create smooth, uninterrupted flow through the entire process.
Flow means work progresses steadily without bottlenecks, batching, or stop-start cycles that introduce delays and inefficiencies.
Creating flow often requires breaking down organizational silos, reducing handoffs between teams, minimizing work-in-progress, and establishing clear visual management systems.
Teams might implement daily stand-up meetings, Kanban boards, and other visual management tools to ensure work flows smoothly.
The goal is to eliminate common project management pitfalls: work sitting idle, frequent context switching, and resource bottlenecks that delay project completion.
When work flows smoothly, teams complete projects faster with fewer resources and higher quality.
Pull Establishment
Traditional project management often pushes work through a predetermined schedule regardless of system capacity.
Lean project management reverses this approach by establishing pull systems where new work is started only when there’s capacity to handle it.
Pull systems prevent overloading team members, reduce multitasking, and ensure work isn’t started until the system is ready to process it efficiently.
This principle helps teams maintain flow and prevents the waste of partially completed work sitting idle.
Continuous Improvement with Lean Project Management
The fifth principle, sometimes called “pursuit of perfection“, embeds continuous improvement into the project management approach.
Lean project teams don’t just execute projects—they constantly look for ways to improve their processes, eliminate additional waste, and deliver more value.
This principle is implemented through regular retrospectives, kaizen events (focused improvement workshops), and establishing metrics that highlight opportunities for enhancement.
Teams adopt a scientific approach to improvement, testing changes on a small scale before implementing them more broadly.
This principle connects lean project management principles with our six sigma certification methodologies, which provide structured approaches to process improvement and problem-solving.
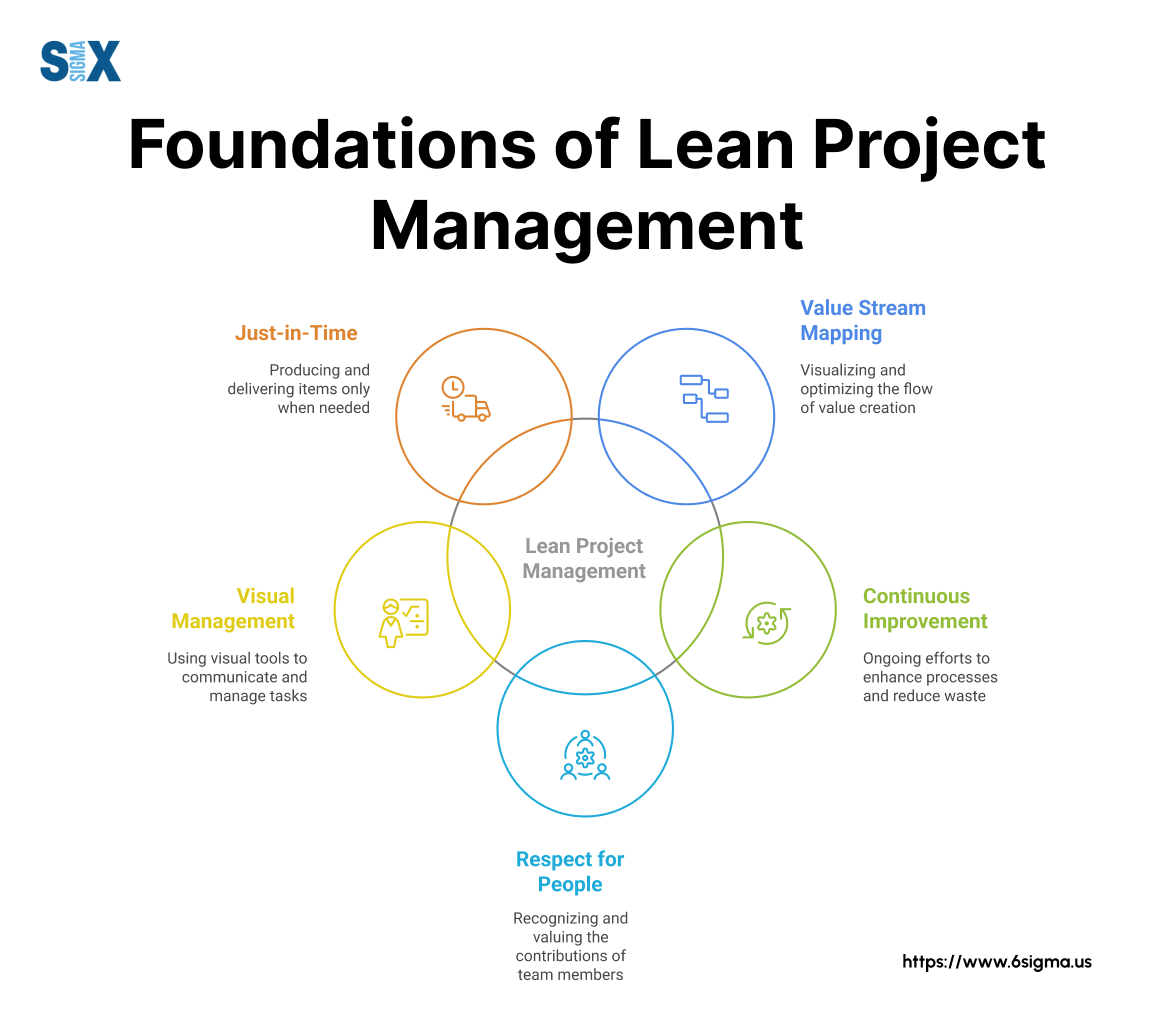
What is Waste in Project Management?
Identifying and eliminating waste stands as the cornerstone of lean project management.
Waste represents any activity, resource, or process that consumes time, money, or effort without adding value from the customer’s perspective.
The Japanese lean tradition categorizes waste into three fundamental types, known as the “3Ms”:
Muda refers to activities that consume resources without creating value. This is the most commonly addressed form of waste in lean project management and includes the eight specific types we’ll explore below.
Mura describes unevenness or inconsistency in workflow or demand. In project environments, mura appears as unpredictable workloads, rushed deadlines followed by idle periods, or unbalanced resource allocation across team members.
Muri represents overburden placed on people, equipment, or systems. When project teams face unrealistic deadlines, excessive overtime, or constant context-switching between tasks, muri occurs.
This overburden typically leads to quality issues, team burnout, and increased defects.
Within the Muda category, project managers focus on eight specific types of waste, commonly remembered by the acronym “TIM WOODS“:
Transportation waste occurs when information, materials, or deliverables move unnecessarily between processes or team members. Examples include excessive email chains, multiple handoffs between departments, or unnecessary approval loops that don’t add value.
Inventory waste in projects manifests as excess work-in-progress, unprocessed information, or stockpiling of resources. This includes partially completed deliverables waiting for action, unread documents, or features developed far ahead of when they’re needed.
Motion waste involves unnecessary physical or digital movement by people. Project teams experience this as excessive meetings, poorly organized digital workspaces requiring extra navigation, or team members traveling between locations when virtual collaboration would suffice.
Waiting represents delays between process steps or idle time when team members wait for information, decisions, or resources. This extremely common project waste appears as approval delays, dependency bottlenecks, or resource availability issues that stall progress.
Overproduction happens when teams produce more than needed or earlier than required. In project contexts, this includes creating deliverables not requested by stakeholders, excessive documentation, or developing features that exceed requirements without adding value.
Over-processing adds more work or complexity than the customer values. Common examples include excessive reviews, unnecessary reports, or gold-plating deliverables beyond what stakeholders need or want.
Defects encompass errors, mistakes, or quality issues requiring rework. For project teams, defects might include bugs in software, errors in deliverables, or misalignment with requirements that forces teams to redo work.
Skills Misuse occurs when organizations underutilize people’s talents, assign tasks to team members without proper training, or fail to leverage available expertise. This waste appears when specialized team members spend time on administrative tasks instead of applying their core skills.
Real project examples of these wastes appear throughout typical project lifecycles:
A marketing team creates detailed specifications for website features the client never requested (overproduction). Development teams wait days for security approval before deploying code changes (waiting).
Construction projects require multiple levels of management approval for minor change requests (over-processing). Team members attend status meetings where only a fraction of the information is relevant to them (motion).
Identifying these wastes requires critical examination of current processes, often through root cause analysis techniques like the 5 Whys or fishbone diagrams.
By systematically identifying and eliminating these non-value-adding activities, lean project management teams dramatically improve efficiency, reduce costs, and accelerate delivery timelines.
Discover systematic techniques to identify and reduce project inefficiencies
Gain practical skills to boost your project performance with Lean Six Sigma Green Belt Certification.
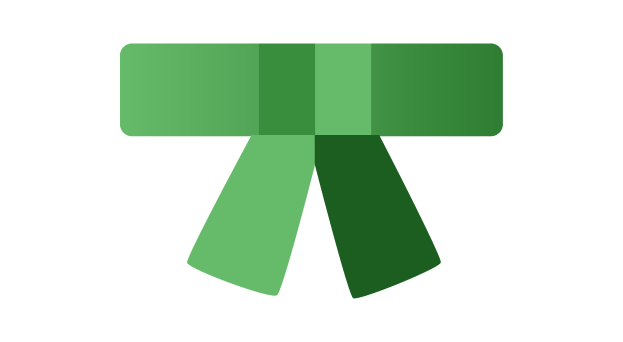
Essential Lean Project Management Tools
Implementing lean project management requires more than understanding principles—it demands practical tools that teams can use daily to eliminate waste and improve flow.
Value Stream Mapping
Value stream mapping (VSM) serves as the foundation for waste identification and process improvement in lean project management.
This powerful visualization tool documents every step required to deliver a product or service, from initial concept to customer delivery.
A typical value stream map shows the flow of both materials and information, highlighting where value is added and where waste occurs.
VSM differs from traditional process mapping by focusing specifically on value creation and including data about time, resources, and flow efficiency. For project teams, VSM reveals shocking truths: often less than 10% of total project time actually adds value from the customer’s perspective.
Project managers use VSM to identify bottlenecks, eliminate unnecessary approvals, reduce handoffs between teams, and streamline information flows.
This lean project management tool provides the data needed to make informed process improvements rather than relying on gut feelings or assumptions.
Kanban Boards
Kanban boards provide visual management of workflow and serve as one of the most accessible lean techniques in project management.
Originally developed at Toyota to control inventory levels, Kanban has evolved into a flexible system for managing knowledge work and project tasks.
A basic Kanban board divides work into columns representing process stages (e.g., To Do, In Progress, Review, Done).
Teams place tasks on cards that move across the board as work progresses. The visual nature of Kanban makes workflow problems immediately obvious—bottlenecks appear as clusters of cards in specific columns.
More sophisticated Kanban implementations include work-in-progress (WIP) limits that prevent overloading the system and ensure smooth flow.
The simplicity and flexibility of Kanban make it one of the most widely adopted lean project management tools across industries.
A3 Problem Solving
A3 problem solving provides a structured approach to identifying, analyzing, and resolving issues in project environments.
Named for the international paper size on which it was traditionally documented (roughly 11×17 inches), A3 thinking condenses complex problem-solving into a single-page format that forces clarity and focus.
The A3 process follows a standard format:
- Problem statement: Clear definition of the issue and its impact
- Current condition: Analysis of the present situation with data
- Root cause analysis: Deep investigation into underlying causes
- Target condition: Description of the desired future state
- Countermeasures: Proposed solutions to address root causes
- Implementation plan: Action steps with responsibilities and timelines
- Follow-up: Verification of results and lessons learned
This lean project management tool embodies scientific thinking—teams develop hypotheses about root causes, test countermeasures, and verify results with data.
5S Methodology
The 5S methodology organizes work environments for efficiency and effectiveness.
While originally developed for physical workspaces in manufacturing, 5S principles apply equally well to digital environments and project management processes.
The five S’s represent:
- Sort: Eliminate unnecessary items, files, or process steps
- Set in order: Arrange remaining items for efficient access and use
- Shine: Clean and inspect the environment regularly
- Standardize: Create consistent procedures and visual controls
- Sustain: Maintain the system through discipline and continuous improvement
Project teams apply 5S to organize shared drives, standardize document naming conventions, structure communication channels, and create efficient digital workspaces.
Integration of Lean Project Management with Six Sigma
Many organizations combine lean project management with Six Sigma methodologies to create a powerful improvement approach that addresses both process flow and quality issues.
While lean focuses primarily on eliminating waste and improving flow, Six Sigma targets variation reduction and defect prevention through statistical analysis.
The integrated Lean Six Sigma approach provides project teams with complementary tools: lean tools quickly identify and eliminate obvious waste, while Six Sigma tools address complex quality problems requiring deeper analysis.
This combination proves particularly effective for organizations dealing with both efficiency and quality challenges.
Project managers interested in this integrated approach often pursue a six sigma green belt certification to develop foundational skills, while those leading major transformation efforts might advance to a six sigma black belt certification.
These certifications provide structured training in both lean and Six Sigma tools, creating versatile improvement professionals.
The result: faster delivery, lower costs, higher quality, and improved stakeholder satisfaction.
Combine powerful methodologies to revolutionize your project management
Learn how top organizations optimize efficiency and quality with Lean Six Sigma Overview.
Implementing Lean Project Management
Transitioning to lean project management requires thoughtful planning and systematic execution.
Successful adoption follows a structured approach that builds organizational capability while delivering measurable improvements.
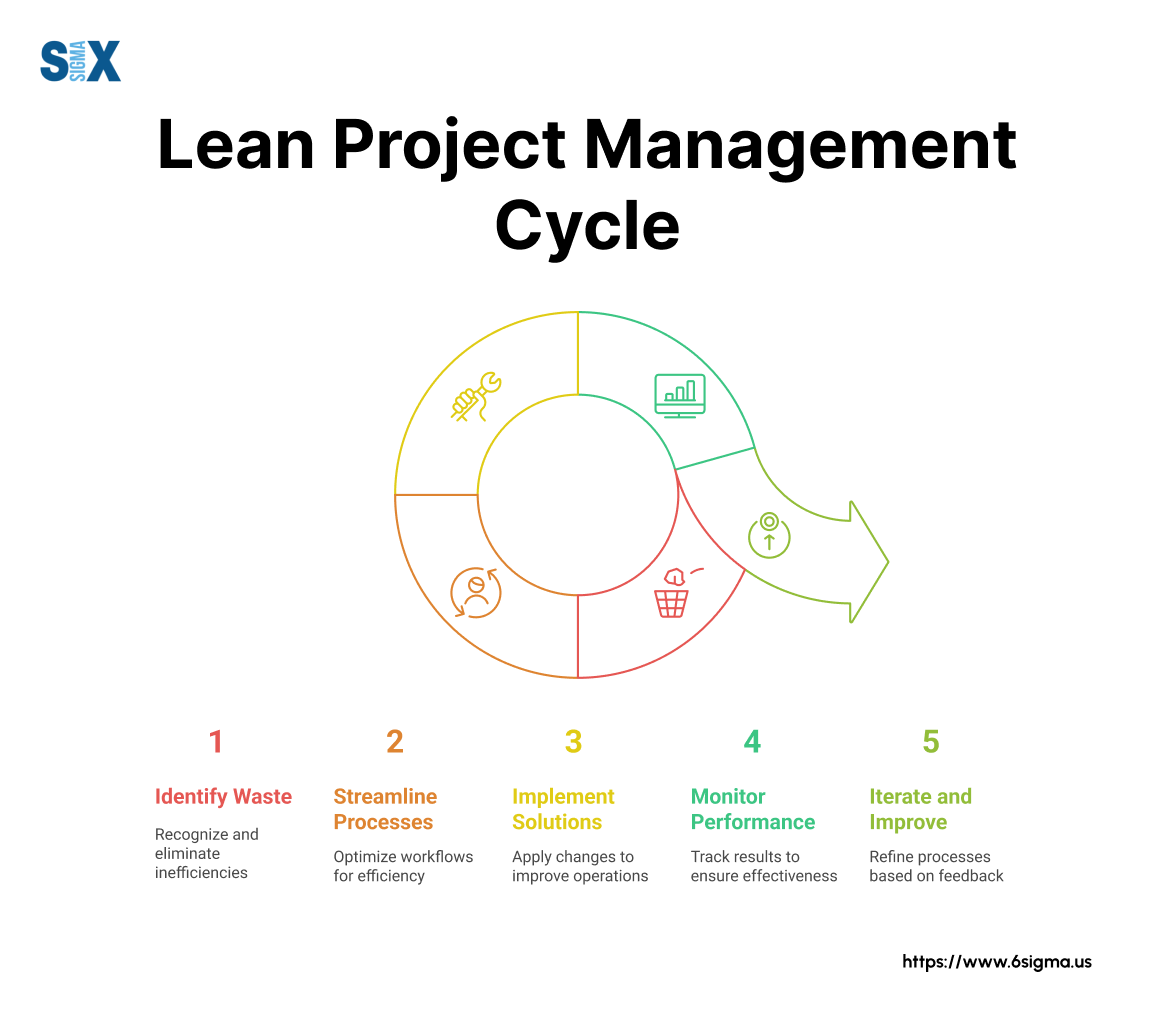
Assessment and Planning Phase
Before implementing lean project management, organizations must honestly assess their current state and readiness for change.
This assessment examines existing project management practices, organizational culture, leadership support, and potential barriers to adoption.
The readiness evaluation should examine several critical factors.
First, leadership commitment must extend beyond verbal support to include resource allocation and personal involvement.
Second, the current project management maturity level determines the appropriate starting point and implementation pace.
Third, the organization’s change history provides insights into potential resistance patterns and successful change strategies.
Effective lean project management implementation requires tailored engagement strategies for each stakeholder group—from executive sponsors who need ROI data to front-line team members concerned about job security.
Goal setting establishes clear, measurable objectives for the lean implementation. Effective goals follow the SMART framework (Specific, Measurable, Achievable, Relevant, Time-bound) and connect directly to organizational priorities.
Rather than vague aspirations like “become more efficient“, successful organizations set specific targets such as “reduce project delivery time by 25% within 12 months” or “decrease project budget variances to less than 5%“.
The assessment and planning phase culminates in a detailed implementation roadmap that sequences activities, assigns responsibilities, establishes milestones, and defines success metrics.
Team Training and Development with Lean Project Management
Successful lean project management methodology implementation depends on developing new skills and mindsets throughout the organization.
Training programs should build capabilities progressively, from foundational awareness to advanced application.
Core competencies for lean project management include waste identification, value stream mapping, root cause analysis, visual management, and continuous improvement facilitation.
Beyond these technical skills, teams need to develop critical thinking abilities, data-driven decision making, and collaborative problem-solving approaches.
Training program structure typically follows a tiered approach. Organizations often begin with broad awareness sessions that introduce lean concepts to all affected staff.
These sessions explain the “why” behind the change and create a common language around lean project management.
Many organizations incorporate formal certification paths to build internal capability and recognize achievement. Entry-level options like six sigma white belt certification provide foundational knowledge, while our six sigma yellow belt certification program equips team members to participate actively in improvement projects.
These certifications complement lean project management implementation by providing structured problem-solving methods and analytical tools.
The implementation journey requires patience and persistence. Organizations typically need 12-18 months to see significant, sustainable changes in how projects are managed.
Real-World Applications and Case Studies
Lean project management delivers measurable results across diverse industries and project types.
Manufacturing Projects
Manufacturing represents the birthplace of lean thinking, and its project applications continue to evolve. Aerospace manufacturer Boeing applied lean project management to its 737 fuselage assembly process, reducing production time by 50% and defects by 75%.
The company mapped the entire value stream, identified non-value-adding activities, and redesigned workflows to create continuous flow.
These manufacturing examples highlight how lean project management can transform both production processes and new product development initiatives when teams focus relentlessly on value creation and waste elimination.
Software Development
Software teams have enthusiastically adopted lean project management, often blending it with agile methodologies.
Spotify’s engineering organization implemented lean principles to scale their development process while maintaining quality and speed.
Their approach included visualizing workflow with digital Kanban boards, limiting work-in-progress, and conducting regular retrospectives to drive continuous improvement.
Financial software provider Intuit applied lean project management to reduce their development cycle time.
They achieved this dramatic improvement by eliminating handoffs between specialized teams, reducing batch sizes, and implementing rapid customer feedback loops. The results included not just faster delivery but also higher customer satisfaction scores.
These examples demonstrate how lean project management helps software teams eliminate common wastes like partially done work, task switching, and delays while creating faster feedback loops that improve product quality.
Service Industry Applications of Lean Project Management
Service organizations increasingly apply lean project management to improve customer experience and operational efficiency.
Global consulting firm McKinsey used lean principles to redesign their client proposal process.
By mapping the value stream and eliminating unnecessary reviews and approvals, they reduced proposal creation time while improving win rates.
Healthcare provider Virginia Mason applied lean project management to their facility design projects. Using value stream mapping and 3P (Production Preparation Process) workshops, they designed spaces that reduced staff walking distance and improved patient flow.
These improvements translated to higher patient satisfaction scores and reduced operating costs.
These service industry examples show how lean project management principles apply beyond manufacturing to knowledge work and facility design projects, delivering tangible benefits to both providers and customers.
Construction Projects
Construction has embraced lean project management to address chronic challenges with schedule delays and budget overruns.
General contractor Sutter Health used lean techniques for their hospital project, finishing three months ahead of schedule.
Their approach included co-locating design and construction teams, using pull planning for scheduling, and implementing Last Planner System to improve workflow reliability.
Commercial builder Boldt Construction applied lean project management to reduce construction waste and improve safety.
Their implementation of 5S on construction sites reduced material waste and improved safety incident rates. Daily huddles and visual management boards helped teams identify and resolve issues quickly before they impacted project schedules.
These construction examples highlight how lean project management addresses industry-specific challenges through improved coordination, reduced variability, and systematic waste elimination throughout the project lifecycle.
Across all these sectors, successful lean project management examples share common elements: clear value definition, systematic waste elimination, improved flow, pull-based scheduling, and continuous improvement cycles.
Lean vs Traditional Project Management
Understanding what is lean in project management becomes clearer when contrasted with traditional approaches.
These methodologies represent fundamentally different philosophies about how to plan, execute, and control projects.
The table below highlights the key differences between these approaches:
Aspect | Traditional Project Management | Lean Project Management |
---|---|---|
Planning Approach | Comprehensive upfront planning | Just-in-time progressive planning |
Success Metrics | On time, on budget, to specification | Customer value delivered, waste eliminated |
Change Management | Formal change control processes | Embraces change as opportunity for improvement |
Work Organization | Work breakdown structure, Gantt charts | Value stream maps, Kanban boards |
Quality Focus | Inspection at completion | Built-in quality, prevent defects |
Team Structure | Specialized roles, hierarchical | Cross-functional teams, collaborative |
Risk Approach | Risk register, mitigation plans | Fail fast, learn quickly |
Documentation | Extensive, formal documentation | Minimal, just enough documentation |
Decision Making | Centralized with project manager | Decentralized to appropriate level |
Improvement | Post-project lessons learned | Continuous improvement throughout |
The benefits of traditional project management include clear accountability, predictability in stable environments, and well-defined processes that work effectively for novice teams.
This approach excels in projects with fixed requirements, regulatory constraints, and limited uncertainty.
Lean project management delivers different advantages: faster delivery through waste elimination, higher quality through built-in verification, greater flexibility to changing requirements, and improved team engagement through empowerment.
These benefits translate to competitive advantages in dynamic markets where customer needs evolve rapidly.
When should organizations choose each approach? Traditional project management works best for projects with well-defined requirements, low uncertainty, regulatory constraints, and contractual obligations tied to specific deliverables.
Examples include construction of standard buildings, implementation of established technologies, and compliance-driven initiatives.
Lean project management proves most effective for projects with evolving requirements, high uncertainty, competitive time pressures, and opportunities for innovation.
Software development, new product creation, process improvement initiatives, and research projects typically benefit from lean approaches.
Common Challenges and Solutions
Even the most promising lean project management initiatives encounter obstacles.
Organizations that successfully navigate these challenges distinguish themselves from those whose efforts stall or fail entirely.
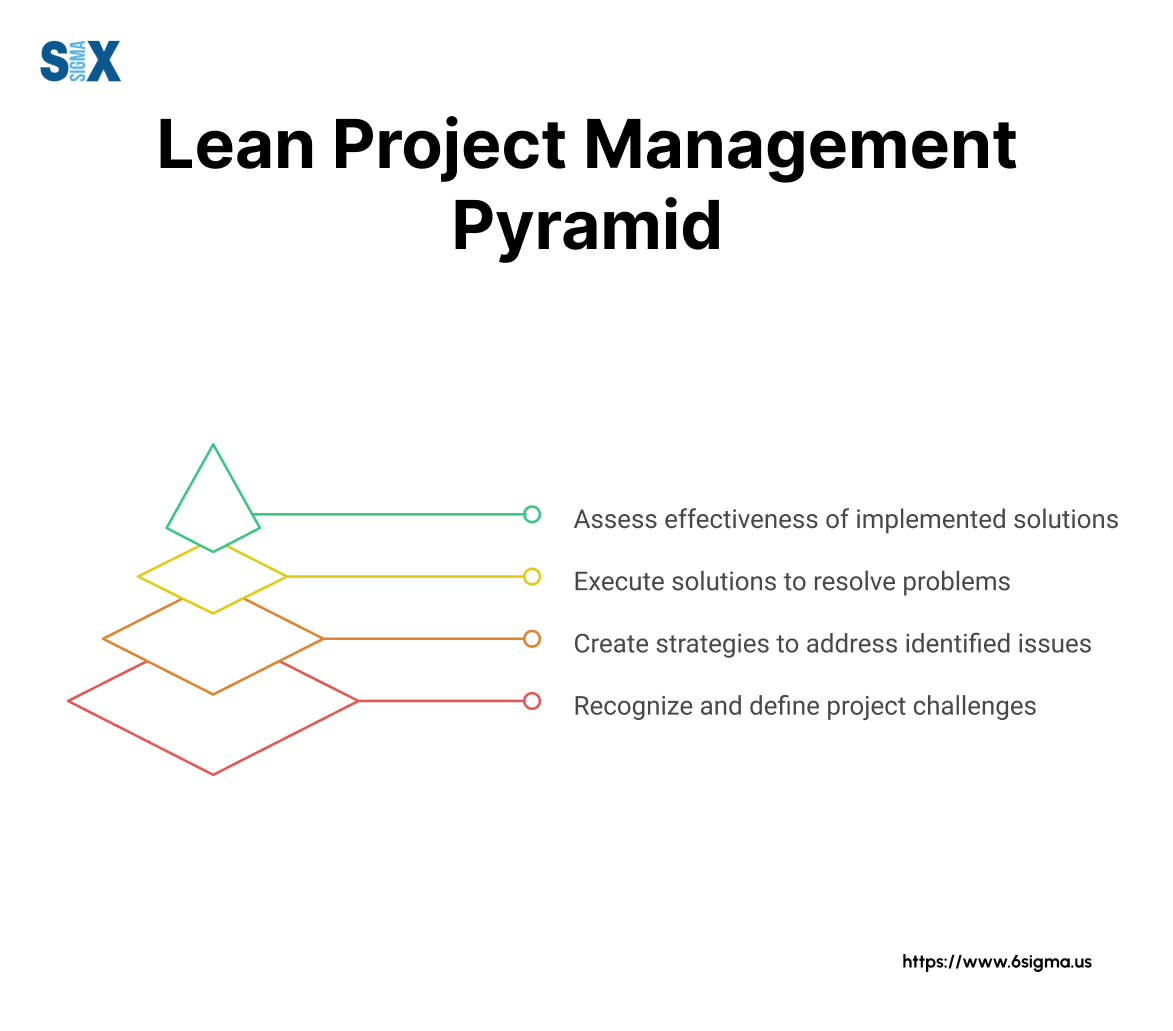
Cultural Resistance
Cultural resistance represents the most persistent barrier to lean project management adoption. Team members often view lean initiatives as threats to established ways of working or, worse, to their job security.
This resistance manifests in various forms: passive non-compliance, active sabotage, or the dreaded “we’ve always done it this way” mentality.
Successful organizations counter this resistance by involving team members early in the transformation process.
Rather than imposing changes from above, they engage employees in identifying problems and developing solutions. This participation creates ownership and reduces fear of the unknown.
Communication proves equally critical. Leaders must clearly articulate why lean project management matters, how it benefits both customers and employees, and what the journey will involve. Transparency about challenges and setbacks builds trust during the transformation process.
Implementation Hurdles of Lean Project Management
Beyond cultural issues, organizations face practical implementation hurdles when adopting lean project management.
Common obstacles include insufficient resources, competing priorities, lack of technical knowledge, and difficulty sustaining initial momentum.
Resource constraints can derail implementation efforts before they gain traction. Successful organizations dedicate adequate time, budget, and personnel to their lean transformation.
This might include creating dedicated improvement roles, allocating protected time for training and implementation, or bringing in external expertise during initial phases.
Knowledge gaps present another significant hurdle. Many organizations lack internal expertise in lean tools and techniques.
Effective solutions include partnering with experienced consultants, developing internal champions through training programs, or pursuing advanced certifications like our six sigma master black belt certification program for key personnel.
Maintaining Momentum
Many lean project management initiatives start strong but gradually lose momentum as initial enthusiasm wanes or organizational attention shifts elsewhere.
This challenge becomes particularly acute after early wins have been achieved and the more difficult, systemic issues remain.
Leadership commitment provides the foundation for sustained momentum. When executives visibly participate in improvement activities, regularly review progress, and recognize achievements, lean initiatives maintain their priority status.
This commitment must extend beyond verbal support to include resource allocation and personal involvement.
Governance structures help institutionalize lean project management practices. Successful organizations establish regular cadences for improvement activities, create clear accountability for results, and integrate lean metrics into performance management systems.
These structures prevent lean from becoming “the program of the month“.
The journey requires persistence, but the rewards—faster delivery, higher quality, lower costs, and more engaged teams—make the effort worthwhile.
Measuring Success in Lean Project Management
Effective measurement drives successful lean project management implementation. Without clear metrics, organizations struggle to demonstrate value, sustain momentum, and guide improvement efforts.
Key Performance Indicators
Lean project management requires balanced measurement across multiple dimensions. Leading organizations typically monitor four categories of key performance indicators (KPIs):
Time-based metrics measure how quickly work moves through the system. These include cycle time (how long work takes from start to finish), lead time (total elapsed time from request to delivery), and takt time (the rate at which work must be completed to meet demand).
Reducing these times indicates improved flow and waste elimination.
Quality metrics assess how well deliverables meet stakeholder requirements. Defect rates, first-pass yield, and rework percentages provide insights into process capability. Customer satisfaction scores and net promoter scores measure quality from the stakeholder perspective.
Efficiency metrics evaluate resource utilization and waste elimination. Value-added ratio (percentage of time spent on value-creating activities), setup or transition times, and resource productivity help quantify efficiency improvements. These metrics highlight opportunities for further waste reduction.
Financial metrics translate operational improvements into business impact. Project cost variance, return on investment, and cost of poor quality connect lean project management to organizational financial goals. These metrics help secure continued support from executives and stakeholders.
Metrics That Matter in Lean Project Management
Not all metrics deliver equal value. Effective lean project management focuses on measurements that drive desired behaviors and outcomes. The most valuable metrics share several characteristics:
They align with strategic objectives, connecting project-level activities to organizational goals. They focus on processes rather than just outcomes, enabling teams to identify improvement opportunities.
They balance leading indicators (predictive measures) with lagging indicators (result measures). They remain simple enough for teams to understand and influence.
Continuous Improvement Tracking
Beyond static performance measures, lean project management requires systems to track improvement over time. Visual management boards, trend charts, and improvement kanbans help teams monitor progress and identify new opportunities.
Regular review cadences ensure metrics drive action rather than simply reporting history.
Daily huddles might focus on immediate flow issues, weekly reviews on short-term improvements, and monthly sessions on systemic challenges.
These structured reviews create accountability for continuous improvement.
Waste Identification Tool
Drag waste types into process steps below. Assign scores and review the analysis. You can remove items or reset everything.
TIM WOODS Checklist
Process Mapping
Priority Scoring
Future Trends and Evolution
Lean project management continues to evolve as organizations face new challenges and technologies create new possibilities. Several trends are shaping the future of this methodology:
Digital transformation dramatically impacts lean in project management. Digital kanban boards, automated value stream mapping tools, and real-time performance dashboards make lean principles more accessible and effective.
Artificial intelligence and machine learning offer new capabilities for waste identification and process optimization.
Remote and hybrid work models create both challenges and opportunities for lean project management. Virtual visual management, digital collaboration tools, and distributed problem-solving approaches help teams maintain lean practices regardless of physical location.
Industry 4.0 concepts like IoT sensors, digital twins, and smart connected products generate real-time data that transforms lean project management.
These trends don’t change the fundamental principles of lean project management but provide new tools and approaches for implementation.
Getting Started with Lean Project Management
Implementing lean project management requires a structured approach that builds capability while delivering tangible results.
This step-by-step guide helps organizations start their lean journey effectively:
- Build awareness and commitment: Educate key stakeholders about lean project management principles and benefits. Secure leadership support by connecting lean to strategic priorities. Identify an executive sponsor who will champion the initiative.
- Assess current state: Evaluate existing project management practices against lean principles. Identify pain points, waste sources, and improvement opportunities. Measure baseline performance on key metrics to quantify future improvements.
- Select pilot projects: Choose 1-2 initial projects that offer high visibility, manageable scope, and meaningful impact. Select motivated team members who will embrace new approaches. Define clear success criteria for the pilots.
- Provide focused training: Train pilot teams on essential lean tools and techniques. Start with value stream mapping, visual management, and basic problem-solving methods. Provide just-in-time training that teams can immediately apply.
- Implement core practices: Begin with visual management to create transparency. Map the value stream to identify improvement opportunities. Establish daily stand-ups to maintain flow and quickly address issues. Implement simple pull systems to control work-in-progress.
- Measure and adjust: Track performance using simple, visible metrics. Conduct regular reviews to identify what’s working and what needs adjustment. Make changes based on team feedback and performance data.
- Expand and standardize: After successful pilots, expand lean practices to additional projects and teams. Standardize successful approaches while allowing for context-specific adaptation. Build internal coaching capability to support expansion.
- Establish continuous improvement: Create mechanisms for ongoing improvement after initial implementation. Develop team problem-solving capabilities. Implement regular retrospectives and improvement cycles.
Essential resources for this journey include executive sponsors who provide visible support, trained facilitators who guide initial implementation, and team members who contribute their process knowledge.
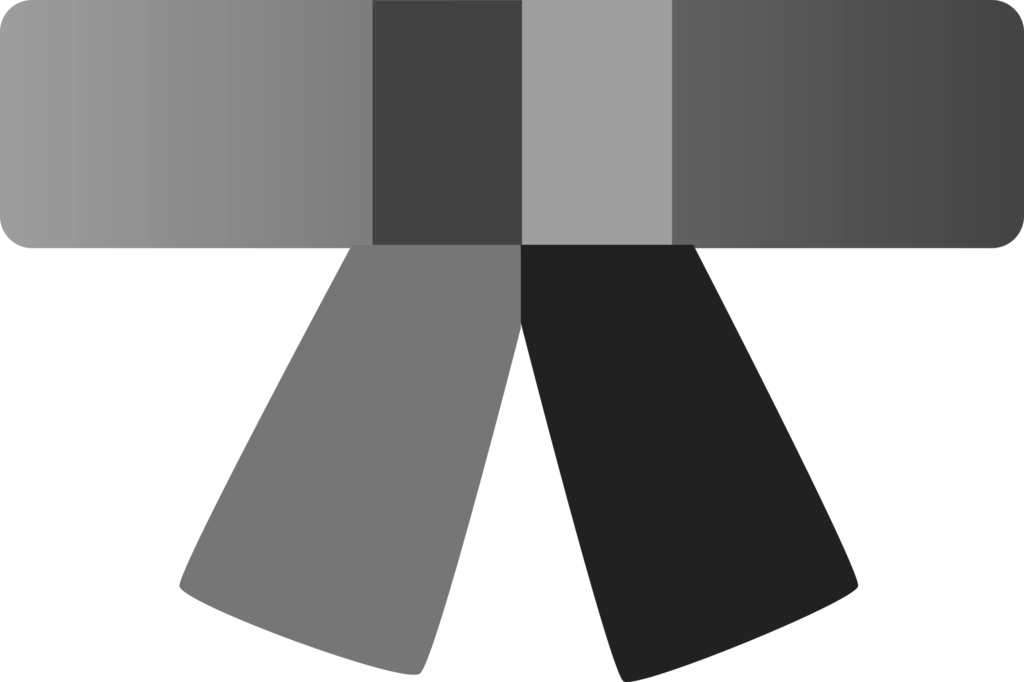
Transform organizations through strategic problem-solving
Become a Lean Project Management Leader with Six Sigma Black Belt Certification.
Moving Ahead
Lean project management offers a powerful approach for delivering more value with less waste.
By focusing on what matters to customers, eliminating non-value-adding activities, and creating smooth workflow, organizations achieve faster delivery, higher quality, and improved stakeholder satisfaction.
The journey begins with understanding lean principles—defining value, mapping the value stream, creating flow, establishing pull, and pursuing continuous improvement.
It continues with applying specific tools like value stream mapping, kanban boards, and A3 problem-solving to address project challenges. Throughout implementation, organizations must measure results, address cultural barriers, and continuously refine their approach.
The most successful organizations don’t just adopt lean project management techniques—they embrace the underlying mindset of customer focus, waste elimination, and continuous improvement. This cultural transformation ultimately delivers the greatest and most sustainable benefits.
Ready to start your lean project management journey? Begin by assessing your current processes against lean principles, identifying your biggest sources of waste, and selecting a pilot project where you can apply these concepts.
Remember that lean implementation itself should follow lean principles—start small, learn quickly, and continuously improve your approach based on results.
SixSigma.us offers both Live Virtual classes as well as Online Self-Paced training. Most option includes access to the same great Master Black Belt instructors that teach our World Class in-person sessions. Sign-up today!
Virtual Classroom Training Programs Self-Paced Online Training Programs