3P Lean Methods in Six Sigma. A Definitive Guide (2025)
It is critical to optimize processes for effectiveness and the production of value for customers. To align processes with lean concepts and client objectives, the 3P (Production Preparation Process) methodology offers an organized approach to process design or redesign.
Learn practical strategies to eliminate waste and create value from day one
Master the Art of Process Optimization with Lean Fundamentals!
Fundamentally, 3P Lean entails cross-functional teams working together to assess the current state, find waste and areas for improvement, and, using fast prototyping and testing, create an optimal future state process.
This proactive strategy is in contrast to conventional techniques of process improvement, which frequently deal with issues as they come up reactively.
Key Highlights
- A lean manufacturing technique called the 3P (Production Preparation Process) is used to completely rethink or rebuild a process.
- Cross-functional teams work together to assess present procedures, spot inefficiencies, and create a better state of affairs for the future.
- The 3P Lean methodology places a strong emphasis on comprehending client needs, quickly developing solutions, and testing them before going live.
- 3P Lean is in line with lean concepts like respect for people, constant improvement, and waste elimination.
- The impact of 3P may be increased by combining it with lean techniques like value stream mapping and kaizen events.
- Change management, training, leadership support, and a continual improvement attitude are necessary for the successful implementation of the three Ps.
More about 3P Lean in Six Sigma
By leveraging the diverse perspectives and expertise of team members from various functions, 3P ensures a comprehensive understanding of the process, its inputs, outputs, and stakeholder needs.
This collaborative effort results in innovative solutions that streamline operations, reduce waste, and enhance customer satisfaction.
The 3P Lean methodology aligns seamlessly with the overarching lean manufacturing philosophy, emphasizing principles such as waste elimination, continuous improvement, respect for people, and creating value for the customer.
When integrated with other lean tools like value stream mapping, kaizen events, and visual management, 3P becomes a powerful catalyst for sustainable process optimization and organizational transformation.
What is 3P (Production Preparation Process)?
The 3P (Production Preparation Process) is a lean manufacturing tool that focuses on designing and developing new products, processes, or services in a structured and efficient manner.
It is a collaborative approach that brings together cross-functional teams to thoroughly plan and prepare for the implementation of a new process or product launch.
The key concepts behind 3P Lean are:
Rapid Prototyping: Creating inexpensive prototypes early in the process to test ideas and gather feedback.
Process Design: Carefully designing the entire production process before implementation, considering factors like flow, layout, standard work, and mistake-proofing.
Cross-Functional Teams: Involving team members from various departments (engineering, manufacturing, quality, etc.) to leverage diverse expertise.
Customer Requirements: Ensuring the new process or product meets customer needs and expectations.
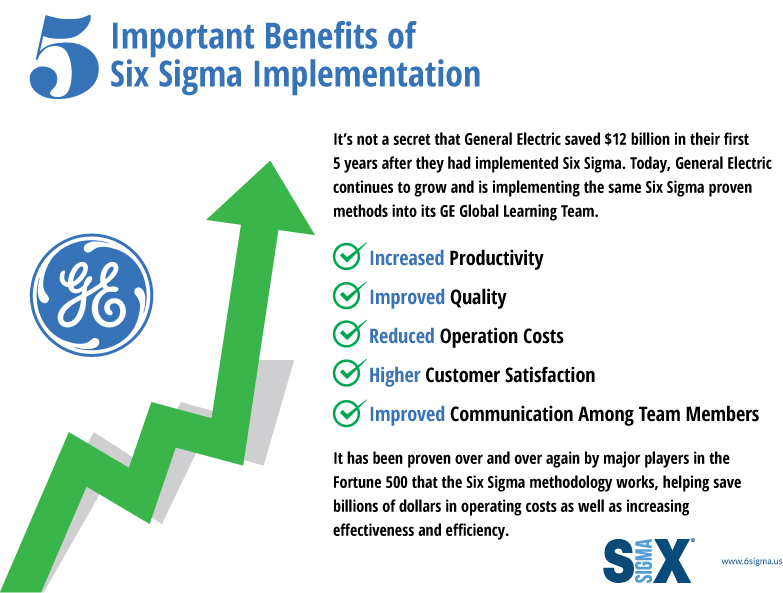
Benefits of 3P Lean
Implementing the 3P Lean methodology offers several benefits to organizations, including:
- Waste Elimination: By designing efficient processes from the start, 3P helps eliminate various forms of waste (overproduction, waiting, transportation, etc.).
- Cost Savings: Thorough planning and prototyping upfront can prevent costly mistakes and rework during implementation.
- Improved Quality: Designing processes with quality in mind and incorporating mistake-proofing techniques leads to better products and services.
- Reduced Lead Time: Streamlined processes resulting from 3P can shorten lead times and improve responsiveness to customer demand.
- Employee Engagement: The collaborative nature of 3P promotes cross-functional teamwork and employee involvement in continuous improvement efforts.
By following the structured 3P approach, organizations can effectively plan and prepare for new product or process introductions, minimizing risks and maximizing efficiency from the outset.
Dive deep into advanced process design and waste elimination techniques
Become a Process Improvement Expert with Lean Six Sigma Green Belt!
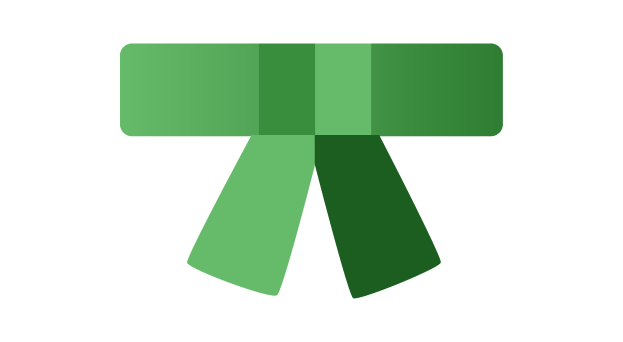
Phases of the 3P Lean Process
The 3P (Production Preparation Process) typically consists of several key phases to systematically design and implement improved processes. The first critical phase is to clearly define the problem or business case driving the need for process improvement.
Define the Problem and Business Case
The 3P process begins by identifying a specific process or value stream that needs to be enhanced. This could stem from issues like excessive waste, quality problems, long lead times, or inability to meet customer requirements.
The team must analyze current state metrics and gather the voice of the customer data to build a compelling business case. Defining the problem with supporting data helps justify the effort and secure leadership buy-in.
Set Goals and Objectives
Once the problem is well-defined, the 3P team establishes specific goals and objectives for the improved future state process.
These should be SMART goals (specific, measurable, achievable, relevant, time-bound) focused on eliminating waste, reducing costs, improving quality, increasing capacity utilization, etc.
Clear targets allow the team to generate and evaluate ideas against these objectives throughout the 3P process.
The goals may include quantifiable metrics like:
- Reducing defects by X%
- Decreasing cycle time by X days
- Increasing first pass yield to X%
- Lowering inventory costs by X%
By starting with a solid problem statement and well-defined goals, the 3P process is centered on achieving meaningful results aligned with customer needs and business strategy.
This lays the foundation for successful process design in subsequent phases.
Analyze Current Processes and Gather Data
A crucial step in the 3P Lean process is to thoroughly analyze the current state of operations. This involves mapping out existing processes, identifying pain points, and gathering relevant data.
Cross-functional teams conduct gemba walks (go and see) to observe processes firsthand and collect insights from frontline workers.
Value stream mapping and process mapping techniques visually depict the flow of materials and information, highlighting areas of waste and inefficiency.
Data collection is key during this phase. Teams gather cycle time data, defect rates, inventory levels, and other process metrics to establish a baseline.
Root cause analysis tools like fishbone diagrams and the 5 Whys help uncover the underlying reasons for problems. This analysis provides a solid foundation for generating improvement ideas in the next phase.
Generate and Screen Ideas
With a clear understanding of the current state, the 3P team engages in brainstorming sessions to generate a wide range of ideas for improving the process.
Techniques like brainwriting and mind mapping encourage creative thinking and prevent anchoring bias.
The team also reviews best practices, benchmarks successful projects, and considers integrating lean principles like just-in-time production and mistake-proofing (poka-yoke).
Once ideas are compiled, the team screens and prioritizes them based on criteria such as feasibility, cost, and impact on customer requirements. Multi-voting and impact-effort matrices help objectively evaluate options. The most promising ideas move forward to the prototyping phase.
Prototype and Test Solutions
Rapid prototyping allows the 3P team to quickly build and test potential solutions iteratively. Low-cost materials like cardboard and foam facilitate the creation of physical models of new layouts, workstations, or product designs.
Virtual simulations provide another avenue for testing before full implementation.
The team conducts kaizen events and plan-do-check-act (PDCA) cycles to fine-tune the prototypes. Structured experiments validate hypotheses and quantify improvements.
Continuous feedback from stakeholders, including customers when possible, shapes the evolution of the prototype into an optimized solution ready for rollout.
Select and Implement the Best Process
After thorough prototyping and testing, the team selects the most robust process for implementation. A comprehensive plan outlines actions, responsibilities, timelines, and required resources like new equipment or training.
Effective change management principles smooth the transition and overcome resistance.
The new standardized process becomes the established way of working, with clear documentation and visual controls to sustain gains.
Total productive maintenance (TPM) plans to maintain equipment in optimal condition. The 3P team closely monitors performance metrics and makes adjustments through additional kaizen events as part of the continuous improvement mindset.
This rigorous approach of analyzing the current state, innovating with prototypes, and implementing an optimized process exemplifies the power of the 3P methodology to drive dramatic process improvements and operational excellence.
3P in the Lean Manufacturing
The 3P process is deeply rooted in the principles of lean manufacturing, which aim to eliminate waste and create value for customers.
Lean manufacturing emphasizes continuous improvement, respect for people, and a relentless focus on identifying and eliminating non-value-adding activities (waste) from processes.
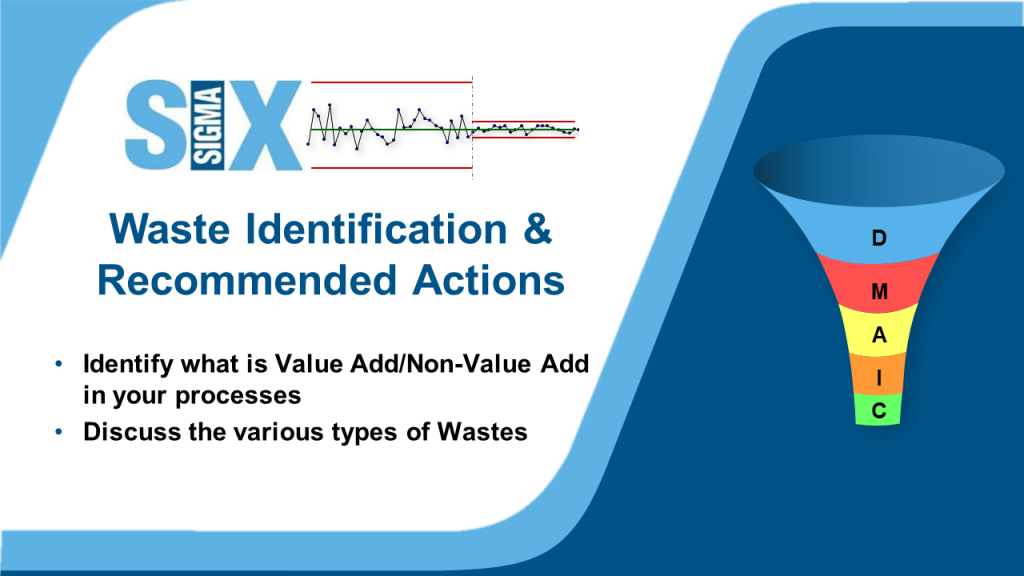
Lean Principles and Waste Elimination
The 3P Lean process aligns with several key lean principles, including:
- Value: The 3P process starts by defining customer requirements and identifying value from the customer’s perspective. This ensures that the new process or product design meets the needs of the end-user.
- Value Stream: The 3P team maps out the current state value stream, identifying waste and opportunities for improvement. This value stream mapping exercise is a crucial step in the 3P process.
- Flow: By analyzing the current process and generating ideas for improvement, the 3P process aims to create a smooth, continuous flow of value-adding activities, minimizing interruptions and non-value-adding work.
- Pull: The 3P process incorporates the lean principle of pull production, where products or services are produced only when there is customer demand, reducing overproduction waste.
- Perfection: The 3P process embodies the lean principle of continuous improvement (kaizen) by encouraging the team to continuously refine and optimize the process, even after implementation.
Integrating 3P Lean with Other Lean Tools
The 3P process is often used in conjunction with other lean tools and techniques, creating a powerful synergy for process improvement and waste elimination. Some common lean tools that complement the 3P process include:
- Gemba Walks: Observing the actual work environment (gemba) is crucial for gathering data and understanding the current state during the 3P process.
- Kaizen Events: The 3P process itself can be structured as a rapid kaizen event, bringing together a cross-functional team to focus on process improvement over a short period.
- Root Cause Analysis: Techniques like the 5 Whys and fishbone diagrams can be used within the 3P process to identify and address the root causes of process inefficiencies.
- Mistake-Proofing (Poka-Yoke): As part of the 3P process, the team can incorporate mistake-proofing mechanisms to prevent errors and defects in the new process design.
Value Stream Mapping and Process Mapping
Value stream mapping and process mapping are essential tools used within the 3P Lean process to analyze and visualize the current state of the process. These mapping techniques help the team identify waste, bottlenecks, and opportunities for improvement.
Value stream mapping provides a high-level view of the entire value stream, from raw materials to the finished product or service delivered to the customer. It helps identify waste and non-value-adding activities across the entire process.
Process mapping, on the other hand, provides a more detailed look at specific processes or sub-processes. It breaks down the process into individual steps, allowing the team to analyze each step in detail and identify opportunities for improvement.
By combining value stream mapping and process mapping, the 3P team can comprehensively understand the current state, enabling them to design a more efficient and streamlined future state process.
Forming a 3P Team
A critical success factor for any 3P initiative is having the right cross-functional team in place. The 3P process requires collaboration across different areas of expertise to analyze the current state, identify improvement opportunities, and design an optimized future process.
Cross-functional Team Structure
A typical 3P team comprises representatives from various departments affected by the process under review. This cross-functional structure ensures that diverse perspectives and knowledge areas are considered during the 3P event. Team members may include:
- Process operators or line workers with hands-on experience
- Industrial engineers or process excellence professionals
- Quality assurance/control experts
- Maintenance technicians
- Logistics and material handling personnel
- Customer service or sales representatives (voice of the customer)
- Suppliers or partners impacted by the process
Bringing together this cross-functional mix fosters a holistic view of the process and promotes idea-sharing across silos.
Roles and Responsibilities
Within the 3P team, key roles and responsibilities should be defined, such as:
Team leader/facilitator: Guides the team through the 3P phases, manages timelines, and ensures alignment.
Subject matter experts: Provide technical expertise in their respective areas (e.g., manufacturing, quality, logistics).
Process owner: The individual accountable for the process being improved.
Data analysts: Collect, analyze, and present process data to identify improvement opportunities.
Lean/3P coach: Ensures adherence to lean principles and 3P methodology.
Clearly defining these roles upfront sets expectations and allows the team to function cohesively.
Facilitating Effective Collaboration with 3P Lean
Fostering an environment of open communication, respect for diverse viewpoints, and constructive conflict resolution is crucial for the 3P team’s success. Effective collaboration techniques include:
- Team building exercises to build trust and rapport
- Visual management tools (e.g. whiteboards, process maps) to align understanding
- Rotating responsibilities to ensure shared ownership
- Frequent team updates and retrospectives
- Celebrating small wins to sustain momentum
By promoting active engagement and leveraging the collective intelligence of the cross-functional team, organizations can maximize the impact of their 3P Lean initiatives and drive process excellence.
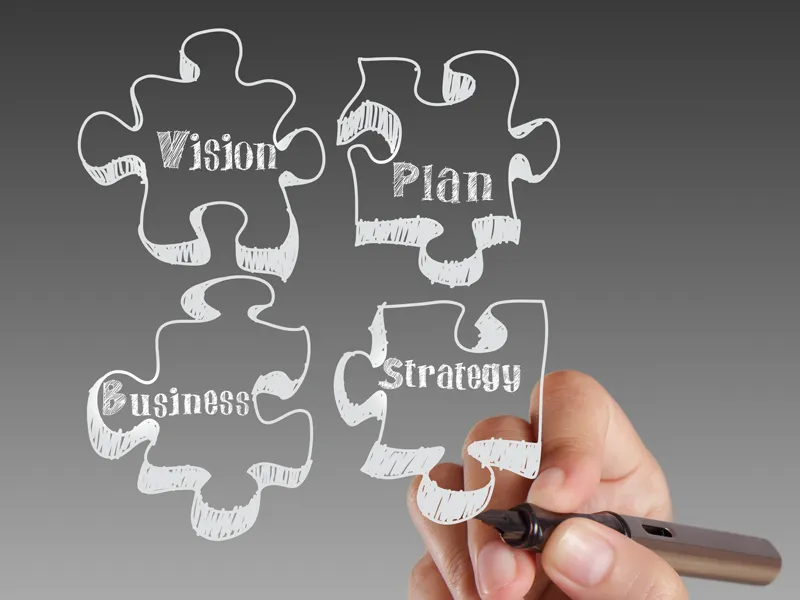
3P Lean Implementation and Challenges
Implementing the 3P Lean (Production Preparation Process) methodology can present several challenges that organizations must be prepared to address. Effective change management is crucial for the successful adoption of 3P Lean across the organization.
Change Management
Introducing a new process like 3P can face resistance from employees who are accustomed to traditional methods. Proper change management strategies are essential to overcome this resistance and ensure a smooth transition.
This may involve clear communication about the benefits of 3P, addressing concerns, and providing adequate training and support.
Leaders should champion the change and actively involve employees in the implementation process to foster ownership and buy-in.
Training Requirements
Implementing 3P requires a significant investment in training and education for all involved personnel. Employees must understand the principles of lean manufacturing, the 3P Lean methodology, and the tools and techniques used in the process.
Cross-functional teams must be trained in collaboration, problem-solving, and decision-making techniques. Ongoing training and coaching may be necessary to reinforce the concepts and address any knowledge gaps.
Sustaining Improvements
While 3P projects can deliver significant process improvements, sustaining these gains over the long term can be challenging.
Organizations must establish a culture of continuous improvement and embed the 3P methodology into their standard operating procedures.
Regular audits, performance monitoring, and continuous improvement cycles (Plan-Do-Check-Act) are essential to maintain the optimized processes and prevent backsliding.
Common Pitfalls to Avoid
When implementing 3P Lean, organizations should be aware of common pitfalls that can hinder success:
- Lack of leadership commitment: Without strong leadership support and active participation, 3P initiatives may lose momentum and fail to achieve their full potential.
- Insufficient resources: Implementing 3P requires dedicated resources, including time, personnel, and funding. Inadequate resource allocation can compromise the quality of the process and the resulting improvements.
- Siloed approach: 3P relies on cross-functional collaboration and input from various stakeholders. Failing to involve all relevant parties can lead to suboptimal solutions and resistance during implementation.
- Inadequate data collection: Accurate data collection and analysis are crucial for identifying opportunities for improvement and measuring the impact of 3P projects. Insufficient or inaccurate data can undermine the entire process.
- Lack of standardization: Failing to standardize and document the improved processes can lead to inconsistencies and a gradual erosion of the gains achieved through 3P.
By proactively addressing these challenges and pitfalls, organizations can increase their chances of successful 3P Lean implementation and sustained process improvements.
Case Studies and Examples of 3P Lean
Successful 3P Lean projects have been implemented across a wide range of industries, demonstrating the versatility and effectiveness of this lean manufacturing tool.
Manufacturing
An automotive manufacturer used 3P Lean to redesign their engine assembly line. A cross-functional team mapped the current process, identified waste and bottlenecks, and developed a new cellular layout.
They prototyped multiple line configurations using cardboard models before settling on the ideal design.
The new pull production system with point-of-use storage reduced walking distances by 40% and cut cycle time by 25%. Overall productivity increased by 18%.
Healthcare
A hospital applied 3P principles to improve its emergency department triage process. The team analyzed data on patient volumes, wait times, and process steps.
They rapidly prototyped new layouts using tape on the floor. The future state design incorporated parallel processing, visual cues, and cross-trained staff.
This reduced average triage time from 22 minutes to 7 minutes and increased patient satisfaction scores.
Service Industry
A financial services call center used 3P to redesign their workstations and information flow. Customer requirements around response times were gathered.
The team created full-scale mock-ups with input from employees. The new standardized workspace gave reps quick access to customer data and enabled seamless hand-offs.
This improved first-call resolution by 28% and lowered handle times.
Quantifying Results and ROI of 3P Lean
Rigorously measuring results is crucial to highlight the impact of 3P Lean and justify future investments. Some key metrics to track would be:
- Cycle time/lead time reductions
- Productivity/throughput increases
- Reductions in labor hours, distance traveled, inventory levels
- Improvements in quality, customer satisfaction, on-time delivery
- Space utilization and layout efficiency
- Financial returns from cost savings and increased revenue
By quantifying the before-and-after performance, organizations can calculate the ROI and payback period for 3P events.
This data-driven approach builds leadership buy-in and a business case for broader continuous improvement efforts using 3P.
Best Practices for 3P Lean
Integrating Customer Requirements
One of the core principles of lean manufacturing and the 3P Lean process is to focus on creating value for the customer.
To truly optimize processes through 3P, it’s critical to deeply understand customer requirements and ensure they are integrated into every step. This involves techniques like:
- Voice of the Customer analysis to capture customer needs, expectations, and pain points
- Defining clear customer value metrics to measure process performance
- Involving customers directly in 3P kaizen events for feedback
- Translating customer requirements into specific design criteria for the process
By keeping the customer at the center, 3P teams can prevent process redesigns that improve efficiency but fail to enhance the customer experience or meet their true needs.
Continuous Improvement Mindset
While a 3P event is focused on making a concentrated process improvement, it should be viewed as just one cycle of an ongoing journey of continuous improvement.
The best organizations instill a continuous improvement mindset where 3P is just one essential tool in a broader lean transformation.
This means building a culture of regularly revisiting and refining processes using lean principles like:
- Encouraging all staff to identify waste and potential process improvements
- Conducting smaller kaizen blitz events between larger 3P projects
- Implementing visual management so process issues are transparent
- Following the PDCA (plan-do-check-act) cycle to iterate on process changes
- Capturing lessons learned to improve the next 3P event
With a relentless continuous improvement mindset, 3P can drive significant organizational change over time.
Leadership Support and Engagement
Effective 3P implementation requires strong leadership support and engagement from top management. This helps ensure teams have:
- Sufficient resources and staffing allocated to 3P projects
- Authority to make process changes across functions
- Access to training on 3P methods and lean tools
- Incentives or motivation to redesign processes
Beyond just endorsing 3P, leaders should actively participate by defining strategic goals, reviewing progress, helping remove roadblocks, and recognizing team successes.
When leadership prioritizes and models behaviors like gemba walks and kaizen participation, it reinforces a transformation toward a truly lean culture.
By integrating customer requirements, fostering continuous improvement, and securing leadership commitment, organizations can derive maximum value and sustainable results from their 3P initiatives.
SixSigma.us offers both Live Virtual classes as well as Online Self-Paced training. Most option includes access to the same great Master Black Belt instructors that teach our World Class in-person sessions. Sign-up today!
Virtual Classroom Training Programs Self-Paced Online Training Programs