Control Plan in Lean Six Sigma. Key Elements and Strategies
Quality control is a critical aspect of any manufacturing or service delivery process, and a well-designed control plan serves as a powerful tool to achieve this objective.
It is a proactive approach to identifying and addressing potential sources of variation that could impact the quality of the final output.
Transform your approach to quality management with proven methodological frameworks
Master Quality Control with Lean Six Sigma Green Belt Certification!
Quick Overview
- A control plan is a comprehensive document that outlines the methods, procedures, and processes for ensuring quality control during product manufacturing or service delivery.
- It serves as a roadmap for identifying, monitoring, and controlling potential sources of variation that could impact product or service quality.
- Control plans are essential tools in quality management systems, helping organizations comply with industry standards and customer requirements.
- They are widely used in various industries, including automotive, aerospace, medical devices, and general manufacturing.
- Control plans integrate with tools like APQP, PPAP, and Failure Mode and Effects Analysis (FMEA), and those with Six Sigma certification often develop and implement them to meet quality goals.
- Developing, implementing, and maintaining effective control plans requires cross-functional collaboration, comprehensive documentation, and continuous improvement efforts.
More about Control Plan in Lean Six Sigma
The primary purpose of a control plan is to ensure that all quality requirements are met consistently, whether they are internal organizational standards, industry regulations, or customer-specific specifications.
By establishing a structured framework for quality control, control plans help organizations minimize defects, reduce waste, and improve overall efficiency and profitability.
Control plans are widely adopted across various industries, including automotive, aerospace, medical devices, and general manufacturing.
They are often a mandatory requirement for companies seeking certification or compliance with quality management standards, such as ISO 9001, or industry-specific standards like IATF 16949 for the automotive sector.
What is a Control Plan?
A control plan is a comprehensive document that outlines the specific methods, procedures, and processes for monitoring and controlling product or service quality throughout the entire production or delivery cycle.
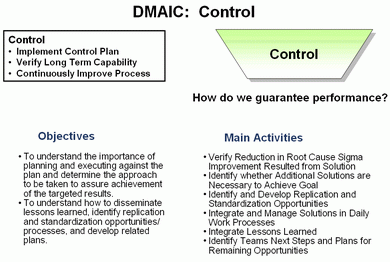
A control plan defines the methods used to ensure that all process inputs and outputs remain within acceptable limits.
Purpose and Benefits of a Control Plan
The primary purpose of a control plan is to prevent defects and minimize variation in manufacturing processes.
It acts as a communication tool to ensure everyone involved understands the controls needed to ensure quality.
Key benefits include:
- Identifying critical product/process characteristics to control
- Documenting process controls and quality checks
- Enabling consistent execution of quality processes
- Facilitating continuous improvement efforts
- Demonstrating compliance with quality standards/requirements
- Reducing costs associated with poor quality
A robust control plan helps an organization produce products that consistently meet customer requirements. It provides a structured approach to quality planning and control across the entire product lifecycle.
Control plans complement Lean fundamentals by minimizing waste through proactive defect prevention.
Control Plan Requirements
A control plan is a critical document in quality management systems, and it is essential to ensure that it meets the necessary industry standards and regulations, as well as any customer-specific requirements.
Industry Standards and Regulations (ISO, IATF, etc.)
Various industries have established standards and regulations that govern the development and implementation of control plans.
These standards provide a framework and guidelines to ensure consistency, quality, and compliance across different organizations and products.
One of the most widely recognized standards for control plans is ISO 9001, which outlines the requirements for quality management systems.
Control plans play a crucial role in meeting the requirements of ISO 9001, such as monitoring and measuring processes, product conformity, and continuous improvement.
In the automotive industry, the International Automotive Task Force (IATF) has developed the IATF 16949 standard, which is a sector-specific interpretation of ISO 9001.
This standard includes specific requirements for control plans, including their development, implementation, and maintenance throughout the product lifecycle.
Other industries, such as aerospace, medical devices, and electronics, may have specific standards and regulations that control plans must adhere to.
For example, the AS9100 standard is widely used in the aerospace industry, while the ISO 13485 standard governs quality management systems for medical devices.
Customer-specific Requirements
In addition to industry standards and regulations, control plans must also meet any customer-specific requirements.
These requirements may be more stringent or include additional controls or specifications unique to a particular customer or product.
Customer-specific requirements can stem from various sources, such as contractual agreements, design specifications, or special product characteristics.
These requirements are typically communicated through documents like purchase orders, engineering drawings, or customer-specific quality manuals.
Organizations must carefully review and understand these customer-specific requirements during the control plan development process.
Please meet these requirements to avoid product non-conformities, customer dissatisfaction, and potential legal or financial consequences.
To ensure compliance with customer-specific requirements, organizations often involve their customers or representatives in the control plan review and approval process.
This collaboration helps to identify and address any specific needs or concerns early on, preventing potential issues down the line.
By adhering to both industry standards and regulations, as well as customer-specific requirements, organizations can develop robust control plans that support quality management systems, ensure product conformity, and foster customer satisfaction.
Components of a Control Plan
A comprehensive control plan consists of several key components that work together to ensure product and process quality.
These components include:
Process Controls
Process controls define the methods, activities, and criteria used to monitor and control manufacturing or service delivery processes.
Examples include machine setup instructions, operating parameters, preventive maintenance schedules, and in-process inspections.
The control plan specifies which process characteristics are critical and how they will be controlled.
Product Controls
Product controls focus on evaluating the final product or service against specifications and requirements.
This includes incoming material inspections, first-piece inspections, product audits, and final inspections before shipment or delivery.
Detailed inspection criteria, sample sizes, and acceptance criteria are outlined.
Methods and Measurement Techniques
The control plan prescribes the specific methods, instruments, and techniques to be used for monitoring processes and inspecting products.
This covers areas like measurement system analysis, gage repeatability and reproducibility studies, and statistical process control techniques.
Proper methods ensure accurate, consistent, and capable data collection.
Sampling Plans
Most control plans utilize sampling plans rather than 100% inspection, especially for high-volume production.
Sampling plans define the sampling approach (e.g. random, stratified), sample frequency, and sample sizes for different inspections and tests.
Sampling risks are analyzed during development.
Reaction Plans
Reaction plans detail the specific actions to be taken when nonconformities or deviations from requirements are detected.
This may include containment, correction, root cause analysis, and recurrence prevention activities.
Escalation criteria and responsibilities are established based on the severity of the issue.
By comprehensively addressing these components, a control plan provides a robust framework for achieving quality objectives through prevention and continuous monitoring rather than just detection.
The specific elements are customized based on the product, process, and business requirements.
Effective reaction plans rely on structured problem-solving techniques, such as those taught in root cause analysis training, to address systemic issues.
Developing a Control Plan
Cross-functional Team Involvement
Creating an effective control plan requires input and collaboration from various cross-functional teams within an organization.
This ensures that all relevant aspects of the product or process are considered and addressed.
Teams often include members with Six Sigma Green Belt certification, ensuring rigorous problem-solving and data-driven decision-making during development.
Key stakeholders typically involved in developing a control plan include:
- Quality engineers/managers
- Process engineers
- Manufacturing engineers
- Design engineers
- Suppliers/sub-contractors
- Customer representatives (for customer-specific requirements)
Having a cross-functional team brings together diverse expertise and perspectives, leading to a more robust and comprehensive control plan.
It also promotes buy-in and ownership across different departments involved in executing the plan.
Inputs (FMEA, Flow diagrams, Lessons learned)
Control plans don’t start from scratch but leverage existing information and documentation.
Common inputs utilized in developing a control plan include:
Failure Mode and Effects Analysis (FMEA): Identifies potential failures, their effects, and current controls. This helps determine additional controls needed.
Process Flow Diagrams: Provide a visual representation of the process steps, enabling the identification of critical characteristics and control points.
Lessons Learned: Previous experience from similar products/processes, including issues faced and effective countermeasures taken, can inform the new control plan.
Voice of the Customer: Customer requirements, specifications, and expectations guide which characteristics need stringent controls.
Capability Studies: Data on process performance and capability helps set appropriate control methods and sampling plans.
Utilizing these inputs ensures the control plan addresses known risks, integrates best practices, and aligns with customer and organizational requirements.
Control Plan Lifecycle (Prototype, Pre-launch, Production)
A control plan is a living document that evolves through different stages of a product’s lifecycle:
Prototype Phase: An initial draft is created during design/prototyping to identify potential issues early and plan for controls. This is revised as the design matures.
Pre-launch Phase: The control plan is updated with manufacturing process details, supplier controls, and pre-production trial runs. It undergoes rigorous review before sign-off.
Production Phase: Once manufacturing launches, the control plan guides the day-to-day execution of process controls and reactions to non-conformances. It is periodically reviewed and updated based on data, audits, and changes.
The level of detail and specificity increases as the product moves from concept to mass production.
Having a robust control plan in place before launch is critical to ensuring quality and minimizing disruptions.
Implementing and Managing Control Plans
Training and Awareness
Proper training and awareness are crucial for the successful implementation and management of control plans.
All personnel involved in the process, from operators to quality inspectors and managers, must understand the purpose, requirements, and components of the control plan.
Organizations may integrate Six Sigma certification programs into their training curricula to build proficiency in statistical process control and defect reduction.
Awareness campaigns can also be beneficial in promoting the importance of control plans and their role in maintaining product quality and process control.
Posters, newsletters, and other communication channels can be used to reinforce the significance of control plans and encourage adherence to the established procedures.
Documentation and Record-keeping
Comprehensive documentation and record-keeping are essential for maintaining control plan integrity and ensuring compliance with industry standards and customer requirements.
The control plan itself should be a well-documented and controlled document, with clear revision history and approval processes.
In addition, all data and records generated during the implementation and execution of the control plan should be accurately documented and maintained.
This includes inspection records, test results, non-conformance reports, corrective and preventive actions, and any other relevant information.
Proper record-keeping not only supports auditing and continuous improvement efforts but also serves as evidence of compliance with regulatory requirements.
Auditing and Continuous Improvement
Regular auditing of control plans is necessary to ensure their effectiveness and identify areas for improvement.
Internal audits should be conducted periodically to assess compliance with the control plan and verify that the defined processes and controls are being followed correctly.
External audits by customers or third-party certification bodies may also be required, depending on the industry and specific requirements.
These audits provide an independent assessment of the control plan’s effectiveness and can identify potential gaps or non-conformities that need to be addressed.
Continuous improvement is an integral part of control plan management.
Based on the findings from audits, process data analysis, and feedback from stakeholders, control plans should be regularly reviewed and updated to reflect changes in processes, product designs, or customer requirements.
This iterative approach ensures that control plans remain relevant and effective in maintaining product quality and process control.
Software Tools and Automation for Control Plan
Software tools and automation can greatly facilitate the implementation and management of control plans.
Quality management software solutions can streamline the creation, revision, and distribution of control plans, ensuring that the latest version is always accessible to relevant personnel.
Automated data collection and analysis tools can be integrated with control plans, enabling real-time monitoring of process parameters and product characteristics.
This not only improves the efficiency of data collection and analysis but also provides timely alerts and notifications when deviations or non-conformances are detected, allowing for prompt corrective actions.
Additionally, software tools can aid in the documentation and record-keeping processes, ensuring that all relevant data and information are centralized and easily accessible for auditing and reporting purposes.
By leveraging software tools and automation, organizations can enhance the effectiveness and efficiency of their control plan implementation and management, leading to improved product quality, process control, and overall operational excellence.
Advanced tools for statistical analysis, often mastered through Six Sigma Black Belt certification, enhance automation accuracy.
Control Plans in Different Industries
Control plans are critical tools for ensuring product and process quality across various industries.
While the core principles and components remain the same, the specific requirements and focus areas may vary depending on the industry and its unique challenges.
Automotive
The automotive industry has stringent quality standards and regulations, such as IATF 16949, and customer-specific requirements from original equipment manufacturers (OEMs).
Control plans in this sector are essential for managing the complex supply chain, ensuring compliance with safety and regulatory requirements, and maintaining consistent quality across high-volume production runs.
Automotive control plans often place significant emphasis on process capability studies, measurement system analysis, and statistical process control (SPC) to monitor and control critical characteristics.
Aerospace and Defense
In the aerospace and defense industries, control plans play a crucial role in managing the risks associated with mission-critical applications and ensuring compliance with rigorous safety and quality standards, such as AS9100 and NADCAP.
Control plans in these sectors typically focus on stringent documentation requirements, traceability, and rigorous inspection and testing procedures.
They also address the unique challenges of low-volume, high-mix production environments and the need for effective configuration management and change control processes.
Medical Devices
The medical device industry is heavily regulated, with strict quality requirements imposed by regulatory bodies like the FDA and international standards such as ISO 13485.
Control plans in this sector are essential for ensuring patient safety, product efficacy, and compliance with regulatory requirements.
They often emphasize risk management, design controls, validation activities, and comprehensive documentation to demonstrate traceability and adherence to quality system regulations.
General Manufacturing
While control plans are widely adopted across various manufacturing sectors, their specific focus and level of detail may vary depending on the industry, product complexity, and associated risks.
In general manufacturing environments, control plans help organizations establish consistent quality practices, identify and mitigate potential risks, and promote continuous improvement.
They typically cover aspects such as process monitoring, inspection and testing, supplier management, and corrective and preventive actions.
Regardless of the industry, effective control plans require cross-functional collaboration, clear communication, and a commitment to continuous improvement.
By tailoring control plans to the specific needs and challenges of each sector, organizations can enhance their ability to deliver high-quality products and services while maintaining compliance with relevant standards and regulations.
Best Practices and Common Pitfalls for Control Plan
Alignment with APQP and PPAP
A control plan is closely linked with the Advanced Product Quality Planning (APQP) and Production Part Approval Process (PPAP) methodologies.
APQP provides a structured approach for defining and establishing the steps necessary to ensure product quality, while PPAP is the process of obtaining approval from customers for a design before full production.
Aligning the control plan with APQP and PPAP is considered a best practice as it ensures that the control plan is developed in conjunction with these critical quality planning processes.
This alignment helps to identify and address potential issues early on, reducing the risk of quality problems and ensuring that the control plan is comprehensive and effective.
Effective Review and Revision Process
Control plans are not static documents; they should be regularly reviewed and revised to ensure that they remain relevant and effective.
An effective review and revision process is essential for maintaining the accuracy and effectiveness of the control plan.
Best practices for Review and Revision Include:
- Establishing a regular review schedule (e.g., annually or when there are significant process or product changes).
- Involving cross-functional teams, including representatives from production, quality, engineering, and other relevant departments.
- Incorporating feedback from internal audits, customer complaints, and other quality data sources.
- Documenting all changes and revisions, including the rationale and approval process.
- Providing training and communication to ensure that all relevant personnel are aware of and understand the changes.
Common Challenges and Solutions
Implementing and maintaining an effective control plan can present several challenges.
Some common challenges and potential solutions include:
Lack of Buy-in or Support from Management and Employees
- Solution: Provide training and education to emphasize the importance of control plans and their role in ensuring product quality and customer satisfaction.
- Involve cross-functional teams in the development and implementation process to foster ownership and commitment.
Difficulty in Maintaining Accurate and Up-to-date Documentation
- Solution: Implement a robust document control system and establish clear responsibilities for updating and maintaining control plan documentation.
- Leverage software tools and automation to streamline documentation processes.
Insufficient Resources or Expertise
- Solution: Allocate adequate resources (e.g., personnel, time, and budget) for control plan development, implementation, and maintenance.
- Provide training and development opportunities to build internal expertise.
- Consider outsourcing or seeking external support if necessary.
Resistance to Change or Complacency
- Solution: Continuously communicate the importance of control plans and the benefits of continuous improvement.
- Celebrate successes and share best practices to encourage adoption and engagement.
- Identify and address root causes of resistance through training, coaching, and process improvements.
By addressing these common challenges proactively, organizations can increase the likelihood of successful control plan implementation and reap the benefits of improved quality, reduced costs, and enhanced customer satisfaction.
SixSigma.us offers both Live Virtual classes as well as Online Self-Paced training. Most option includes access to the same great Master Black Belt instructors that teach our World Class in-person sessions. Sign-up today!
Virtual Classroom Training Programs Self-Paced Online Training Programs