Lean Enterprise: Transforming Your Organization Through Lean Principles
Did you know that the average organization wastes 30% of its effort on non-value-adding activities? That’s nearly one-third of your company’s resources being poured down the drain daily.
Lean enterprise represents a systematic approach to identifying and eliminating waste while simultaneously creating value throughout an entire organization.
Discover proven waste elimination techniques
Learn directly from Master Black Belt and Lean Master instructors with Lean Fundamentals course.
Unlike traditional management approaches that focus on departmental optimization, lean enterprise takes a holistic view, connecting every business function into a seamless value stream focused on delivering what customers truly want.
Key Highlights
- Proven waste elimination techniques
- Value stream mapping essentials
- Digital transformation integration methods
- Implementation roadmap and pitfalls
The journey toward operational excellence begins with understanding lean fundamentals. While lean thinking originated in manufacturing, today’s most successful organizations—from healthcare providers to software companies—have adapted these principles to create remarkable results across every industry.
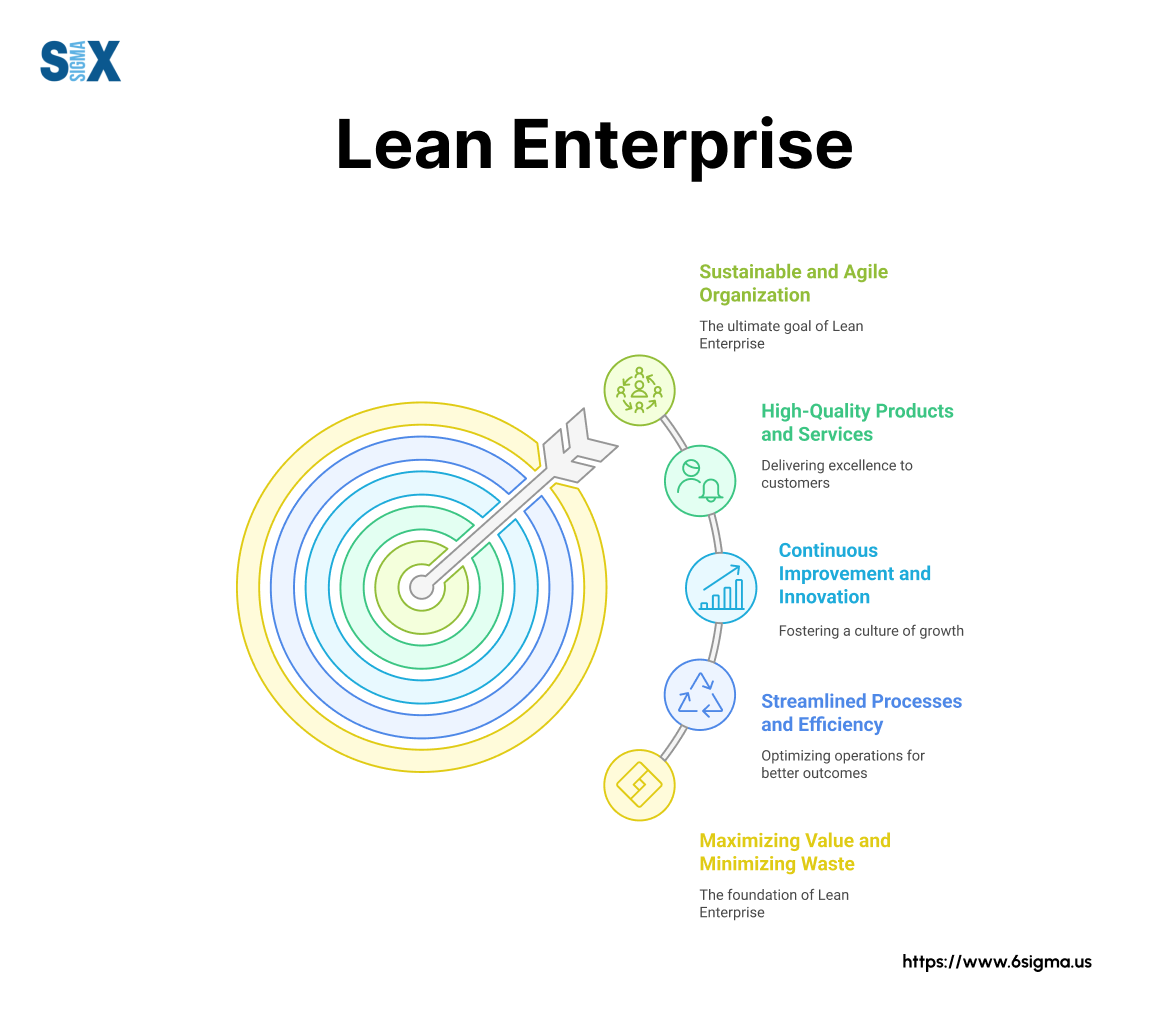
What Is Lean Enterprise?
Lean enterprise represents an organizational model where every aspect of the business focuses on delivering maximum value to customers while minimizing waste.
Unlike traditional improvement approaches that target isolated departments, lean enterprise extends efficiency principles across the entire organization—from product development and manufacturing to marketing, sales, and customer service.
Historical Evolution of Lean Enterprise from Toyota Production System
The concept emerged from Toyota’s revolutionary production methods in post-World War II Japan.
Facing resource scarcity and intense competition, Toyota engineers Taiichi Ohno and Eiji Toyoda developed the Toyota Production System (TPS)—a methodology that prioritized flow, pulled production based on actual demand, and relentlessly eliminated waste.
These innovations helped Toyota produce higher-quality vehicles with fewer resources than their Western competitors.
Western businesses largely ignored these methods until the 1980s when Toyota began outperforming American automakers. The publication of “The Machine That Changed the World” in 1990 introduced the term “lean” and documented Toyota’s superior performance metrics.
Companies worldwide suddenly scrambled to adopt these principles, though many initially focused narrowly on manufacturing techniques rather than the broader management philosophy.
Connecting lean introduction and modern applications
True lean enterprise goes beyond factory floors. Healthcare organizations now apply lean thinking to improve patient care and reduce costs. Software companies use lean principles to eliminate development bottlenecks.
Government agencies streamline citizen services through lean methods. This widespread adoption demonstrates the versatility of lean thinking across sectors.
The lean introduction often pairs with Six Sigma methodologies to create powerful improvement frameworks. While lean focuses primarily on flow and waste elimination, Six Sigma targets variation reduction and process control.
Integration of Lean Enterprise with Six Sigma methodology
Together, they form Lean Six Sigma—a methodology that many organizations implement through structured six sigma certification programs that build expertise through progressive belt levels.
Modern lean enterprise has evolved to incorporate digital transformation tools. Organizations increasingly leverage AI in healthcare, telemedicine platforms, and other technologies to enhance their lean initiatives.
These digital tools help identify waste patterns, optimize value streams, and deliver faster feedback on improvement efforts.
Calculate your waste with a Waste Identification Tool →
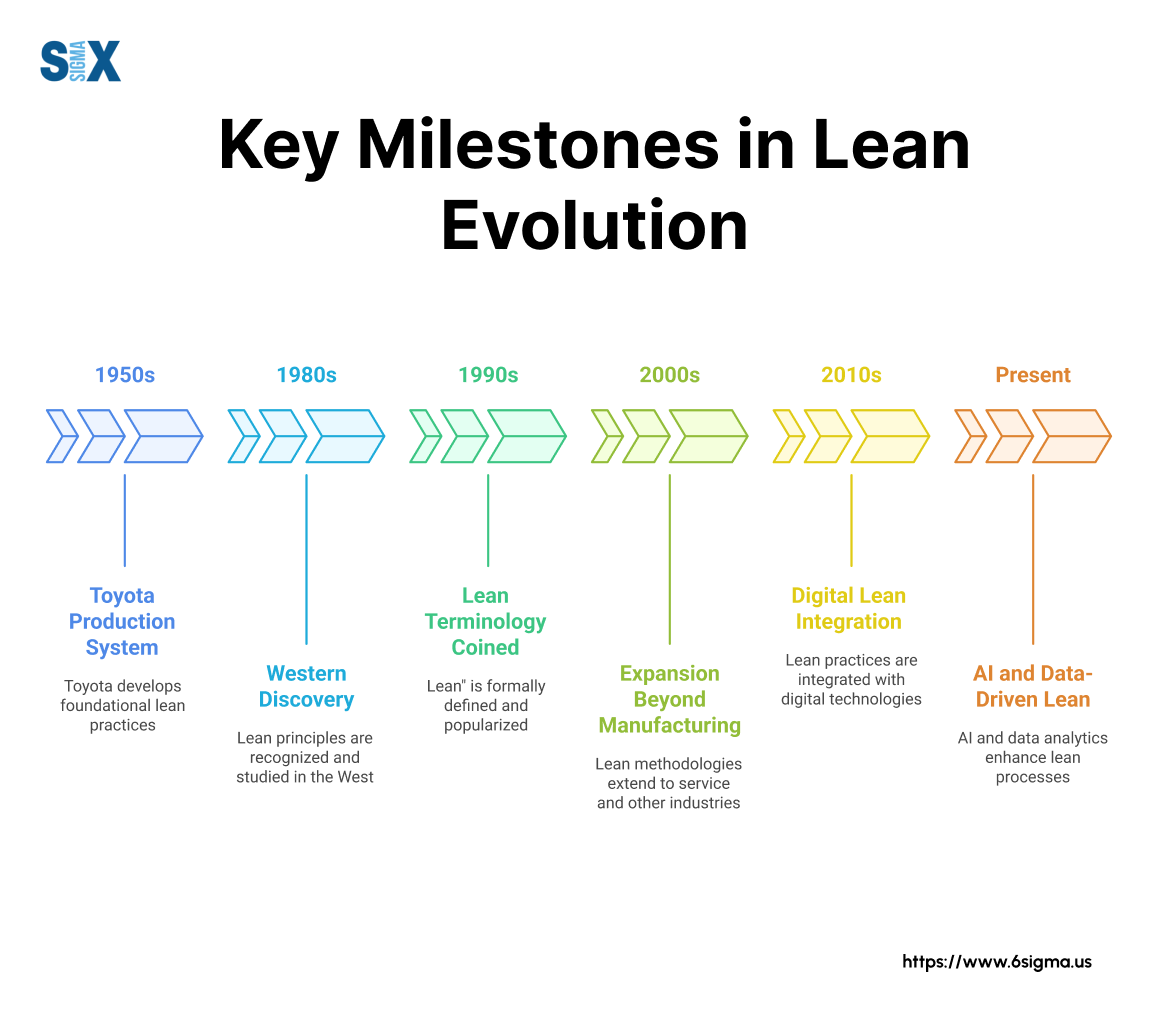
The Five Core Principles of Lean Enterprise
The foundation of any successful lean enterprise rests on five fundamental principles first articulated by James Womack and Daniel Jones in their influential book “Lean Thinking“.
These principles provide a roadmap for organizations seeking to transform their operations and culture.
When implemented properly, they create a self-reinforcing system that drives continuous improvement throughout the enterprise.
Value Definition
The lean journey begins by defining value strictly from the customer’s perspective. This means identifying exactly what customers are willing to pay for and, equally important, what they aren’t.
Many organizations struggle with this principle because they define value based on internal metrics or assumptions rather than genuine customer needs.
For example, a healthcare organization implementing digital health transformation must define value in terms of patient outcomes and experiences, not just operational efficiency.
This shift in perspective often reveals that many long-standing activities add no value whatsoever from the customer’s viewpoint.
Value Stream Mapping
Once value is properly defined, the next step involves mapping the entire value stream—the sequence of activities required to design, produce, and deliver a specific product or service.
Value stream mapping exposes three types of activities: those that clearly create value, those that create no value but are currently necessary (Type One waste), and those that create no value and can be eliminated immediately (Type Two waste).
This visual exercise often reveals shocking inefficiencies. Manufacturing companies typically discover that less than 10% of activities actually add value, while service organizations often fare even worse. The mapping process provides the blueprint for lean transformation by highlighting where waste exists.
Flow Creation
After removing obvious waste, the third principle focuses on making the remaining value-creating steps flow without interruption. Traditional batch-and-queue thinking must give way to continuous flow wherever possible.
This might involve reconfiguring production lines, reorganizing department layouts, or rethinking how information moves through an organization.
In telemedicine applications, for instance, flow creation might involve streamlining the virtual patient journey from appointment scheduling through follow-up care.
The goal is to eliminate waiting, backflows, and detours that interrupt the smooth delivery of value to customers.
Pull Systems
The fourth principle establishes pull systems where nothing is produced until requested by a downstream customer.
This contrasts sharply with traditional push systems that produce according to forecasts and schedules, often resulting in overproduction—considered the most serious form of waste in lean thinking.
Pull systems minimize inventory, improve responsiveness, and ensure resources are dedicated to actual customer needs.
Organizations implementing AI in healthcare often use pull systems to allocate computational resources based on actual clinical demand rather than predetermined schedules.
Continuous Improvement
The fifth principle—pursuing perfection through continuous improvement—transforms lean enterprise from a one-time project into an ongoing journey. Once the previous principles are in place, organizations discover that opportunities for improvement become endless.
This principle demands creating a culture where everyone constantly questions current processes and seeks better ways to define value, map value streams, create flow, and establish pull.
Organizations that excel at this principle make improvement part of everyday work rather than a special initiative.
Together, these five principles form an integrated system that guides the lean enterprise transformation.
They work synergistically—each principle reinforcing the others—to create organizations capable of delivering maximum value with minimum waste.
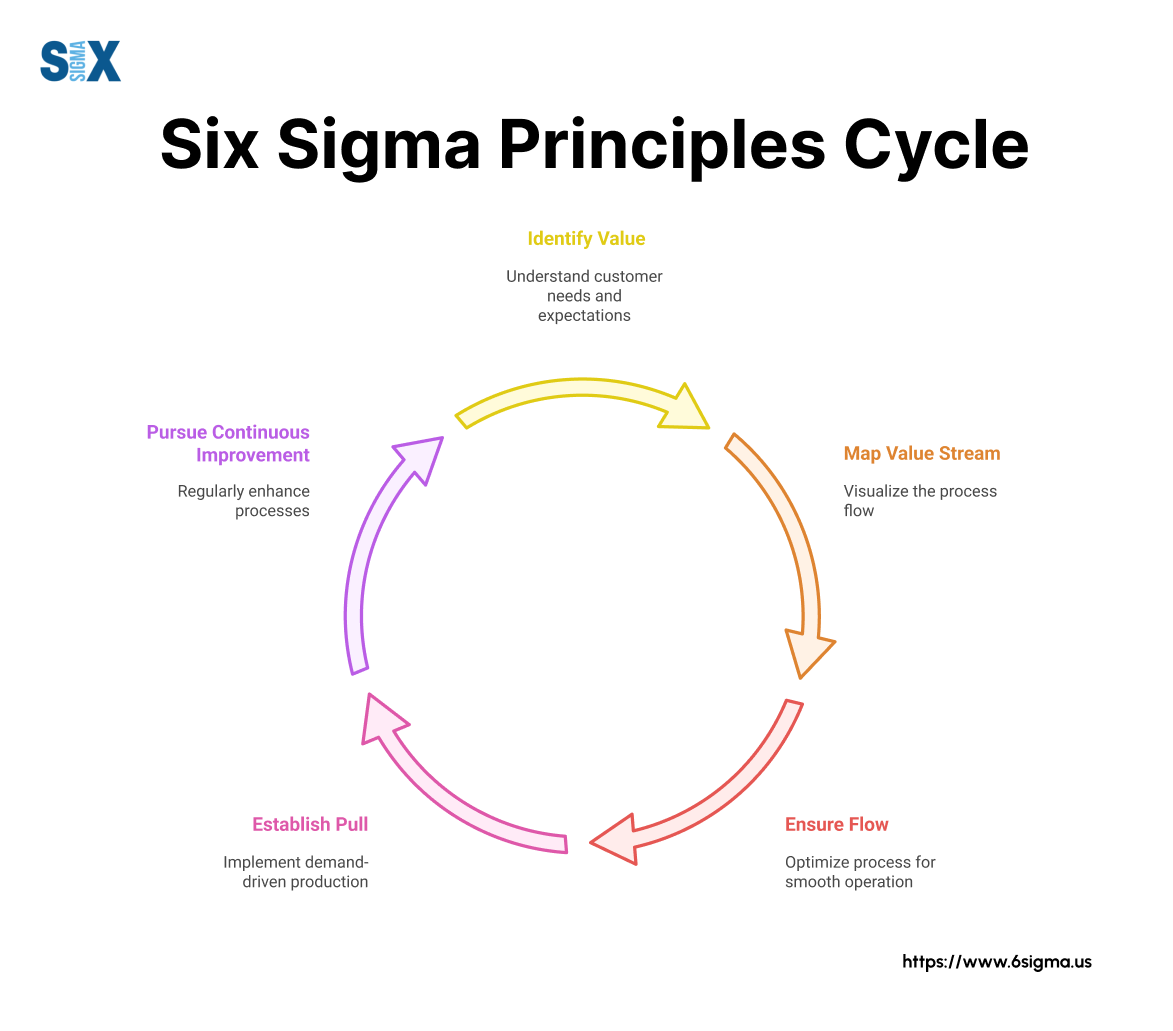
Lean Enterprise and Six Sigma Integration
While lean enterprise focuses on eliminating waste and optimizing flow, Six Sigma targets variation reduction and process control.
These methodologies emerged from different origins but have converged into powerful improvement approaches that complement each other perfectly. Many organizations now implement them together as Lean Six Sigma to achieve superior results.
The integration makes practical sense. Lean principles help identify and eliminate non-value-adding activities, while Six Sigma provides the statistical rigor to solve complex problems and reduce defects.
For example, a healthcare organization might use lean methods to streamline patient flow in telemedicine services, then apply Six Sigma tools to reduce diagnosis errors.
This combined approach addresses both efficiency and quality simultaneously.
Different certification levels
Organizations typically build capability through structured six sigma certification programs. These programs establish a common language and methodology across the enterprise while creating improvement specialists at various expertise levels.
The six sigma white belt certification provides awareness-level training for all employees, while yellow belt holders support projects part-time. Green belts lead smaller projects, and black belts tackle complex, cross-functional improvements. Organizations often develop master black belts to coach others and drive strategic initiatives.
Role of Root Cause Analysis in Lean Enterprise
Root cause analysis plays a crucial role in lean enterprise improvement efforts. Rather than treating symptoms, lean practitioners dig deeper to identify and address underlying causes of waste and inefficiency.
Tools like the 5 Whys, fishbone diagrams, and failure mode effects analysis help teams move beyond superficial explanations to discover fundamental issues. This investigative approach prevents the common trap of implementing quick fixes that fail to deliver sustainable results.
Digital health transformation initiatives particularly benefit from this integrated approach. Healthcare organizations can use lean principles to eliminate administrative waste while applying Six Sigma methods to ensure patient data accuracy.
AI in healthcare applications often combines both methodologies—using lean thinking to streamline workflows and Six Sigma statistical methods to validate algorithm performance.
The most successful lean enterprises recognize that these methodologies aren’t competing approaches but complementary tools in the improvement toolkit.
Organizations that integrate them effectively develop the ability to both streamline processes (lean) and make them more precise and reliable (Six Sigma), creating a powerful engine for continuous improvement.
Become a Lean Six Sigma Problem-Solving Expert
Lead impactful improvement projects that drive real organizational change with Lean Six Sigma Green Belt Certification.
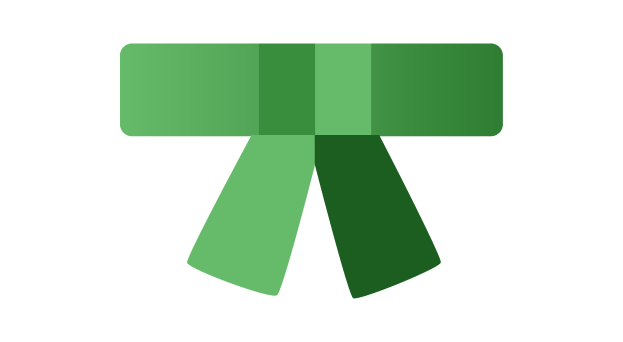
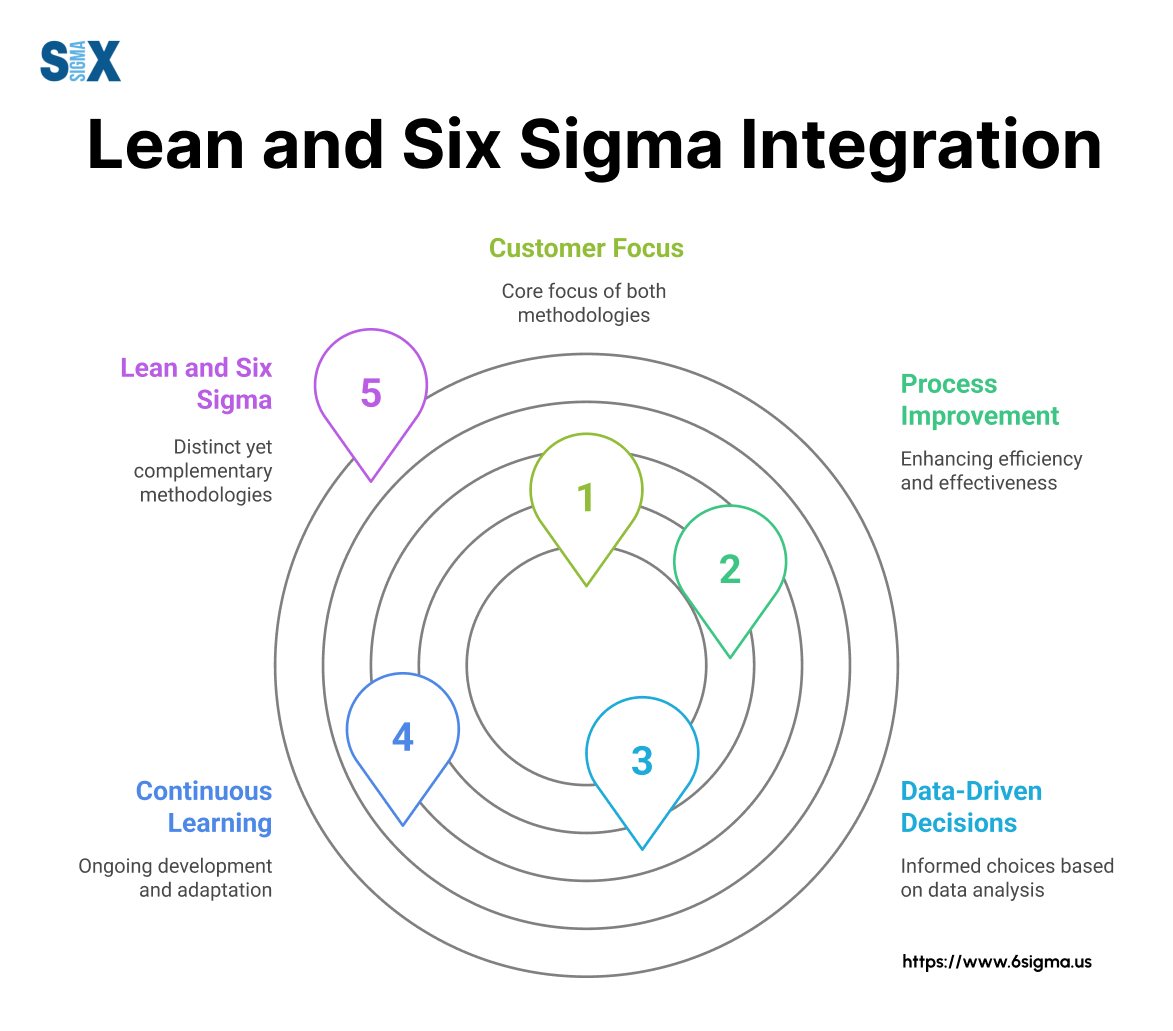
The 8 Wastes in Lean Enterprise
Waste elimination forms the backbone of any lean enterprise transformation.
The Japanese term “muda” (waste) refers to any activity that consumes resources without creating value for customers.
DOWNTIME Framework
Lean practitioners use the DOWNTIME framework to identify and target eight specific types of waste that plague organizations across all industries.
Defects represent the most obvious form of waste. Every error, mistake, or quality issue requires rework, consuming additional resources while delaying value delivery.
Examples of Enterprise Lean Across Industries
In healthcare settings implementing digital health transformation, defects might include incorrect patient records or medication errors.
Manufacturing defects lead to scrap, warranty claims, and damaged reputation.
Service organizations suffer from defects like incorrect billing or mishandled customer requests.
Overproduction occurs when organizations produce more than customers need or before they need it. Often considered the most serious waste, overproduction triggers other wastes by creating excess inventory that must be stored, moved, and managed.
Software companies fall into overproduction traps by building features users don’t want, while hospitals waste resources by scheduling unnecessary tests.
Waiting appears whenever people, information, or materials sit idle. Examples include patients waiting for telemedicine appointments, manufacturing components waiting for processing, or employees waiting for approvals.
Waste Identification Techniques
This waste often hides in plain sight because idle time becomes normalized within organizations.
Non-utilized talent represents the squandered creativity, skills, and knowledge of the workforce. Organizations implementing lean enterprise principles recognize that front-line workers possess valuable insights about process improvements.
When companies fail to engage employees in problem-solving, they miss significant opportunities for innovation.
Transportation waste happens when materials, information, or people move unnecessarily. Every movement creates opportunities for damage, delay, and miscommunication.
Healthcare organizations often struggle with transportation waste when moving supplies, equipment, or patients through complex facilities.
Inventory excess ties up capital and space while hiding problems and increasing handling costs. This waste extends beyond physical goods to include information backlogs and work-in-process in service environments.
AI in healthcare initiatives often reveal hidden information inventory problems in clinical workflows.
Motion waste involves unnecessary physical movements by workers. Poorly designed workstations, illogical process layouts, and inefficient procedures force people to reach, bend, walk, and search unnecessarily.
This waste not only reduces productivity but also contributes to ergonomic injuries.
Extra processing represents effort that adds no value from the customer’s perspective. Common examples include redundant approvals, unnecessary reports, excessive documentation, and features customers don’t use or value.
Organizations must constantly question whether activities truly add value or merely represent organizational habit.
Identifying these wastes requires systematic observation and analysis. Lean enterprises employ techniques like gemba walks (going to where work happens), waste walks (focused observation sessions), value stream mapping, and process observation.
Many organizations create waste identification checklists tailored to their specific operations. Digital tools increasingly support waste identification through automated data collection and analysis.
Waste Identification Quiz
This interactive quiz reveals which types of waste may be most relevant to your organization — and gives instant suggestions for reduction opportunities.
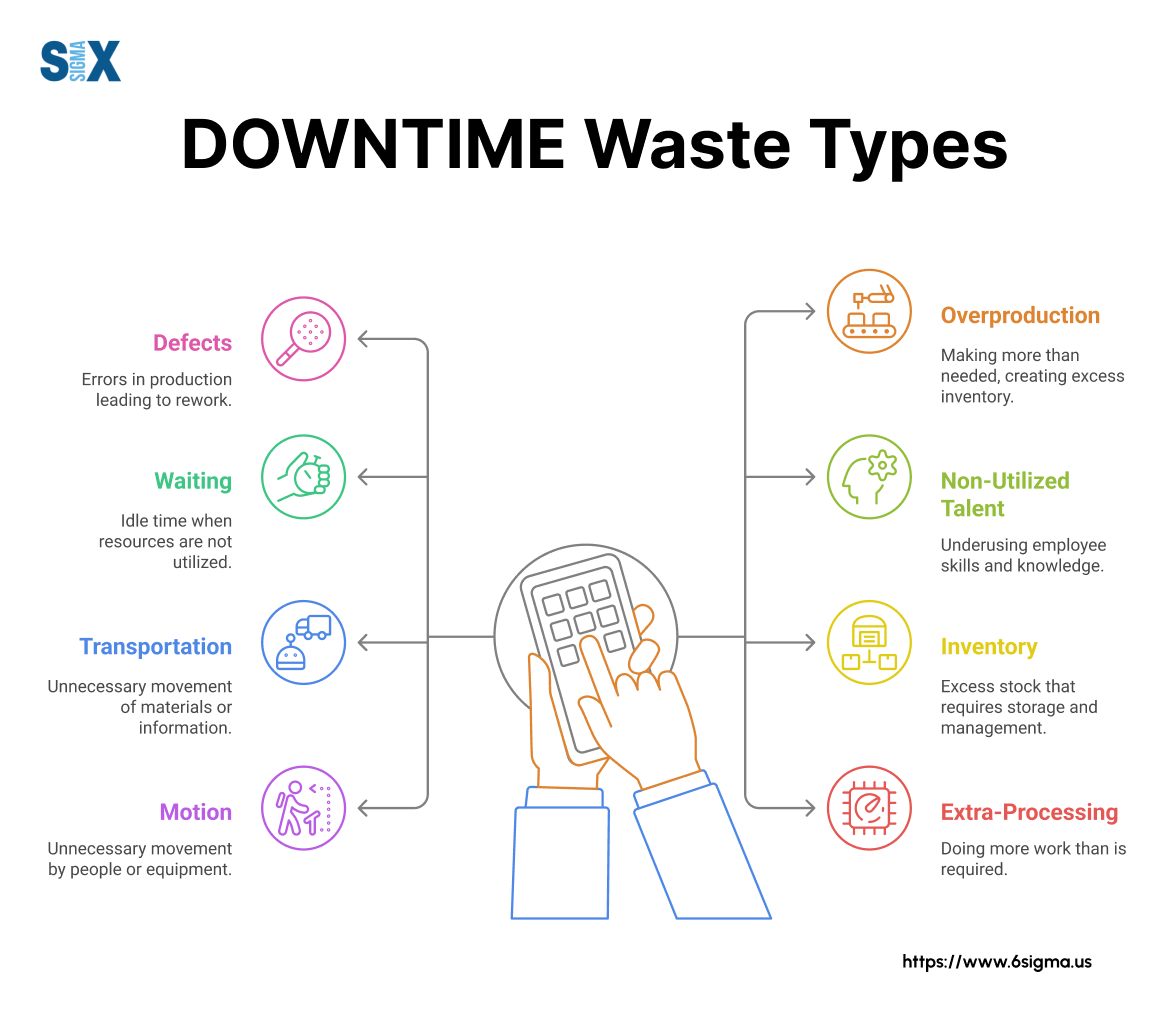
Implementing Lean Enterprise
Transforming an organization into a lean enterprise requires more than simply adopting a few tools or techniques.
Successful implementation demands a structured approach that builds momentum through early wins while laying the foundation for long-term cultural change.
Assessment Phase
The lean enterprise journey begins with an honest assessment of current state. This involves evaluating organizational readiness, mapping key value streams, and identifying critical improvement opportunities.
The assessment should examine both operational metrics and cultural factors like leadership commitment and employee engagement.
During this phase, it’s crucial to gather data about customer needs and experiences.
- What do customers truly value?
- Where do current processes fail to deliver that value?
Healthcare organizations embarking on digital health transformation often discover significant gaps between patient expectations and service delivery during this assessment.
Planning and Strategy
With assessment data in hand, organizations must develop a lean implementation strategy that aligns with business objectives.
This strategy should identify priority value streams, establish clear goals, allocate necessary resources, and create a governance structure to guide the transformation. The most effective strategies balance short-term wins with longer-term capability building.
Leadership alignment proves critical during this phase. Without visible executive support, lean enterprise initiatives often stall when they encounter resistance.
Pilot Projects of Lean Enterprise
Rather than attempting organization-wide transformation immediately, successful lean enterprises start with focused pilot projects.
These pilots target high-impact processes where improvements will be visible and meaningful. The pilot approach allows teams to learn and adapt lean methods to their specific context while generating early wins that build credibility and momentum.
Pilot selection requires strategic thinking. The ideal pilot addresses a significant business problem, involves manageable scope, and offers potential for measurable results within 3-6 months.
Scaling Across Organization
Once pilot projects demonstrate success, organizations can begin scaling lean enterprise principles across the broader organization.
This expansion requires systematic knowledge transfer, capability building, and infrastructure development.
Successful scaling strategies typically include developing internal lean experts, establishing standardized improvement methodologies, and creating mechanisms to share lessons learned.
Communication plays a vital role during scaling. Organizations must celebrate and publicize successes, address concerns openly, and continually reinforce the connection between lean initiatives and strategic priorities.
Throughout implementation, organizations should recognize that becoming a lean enterprise represents a journey, not a destination.
The most successful transformations evolve over time, adapting to changing business conditions while maintaining unwavering focus on customer value and waste elimination.
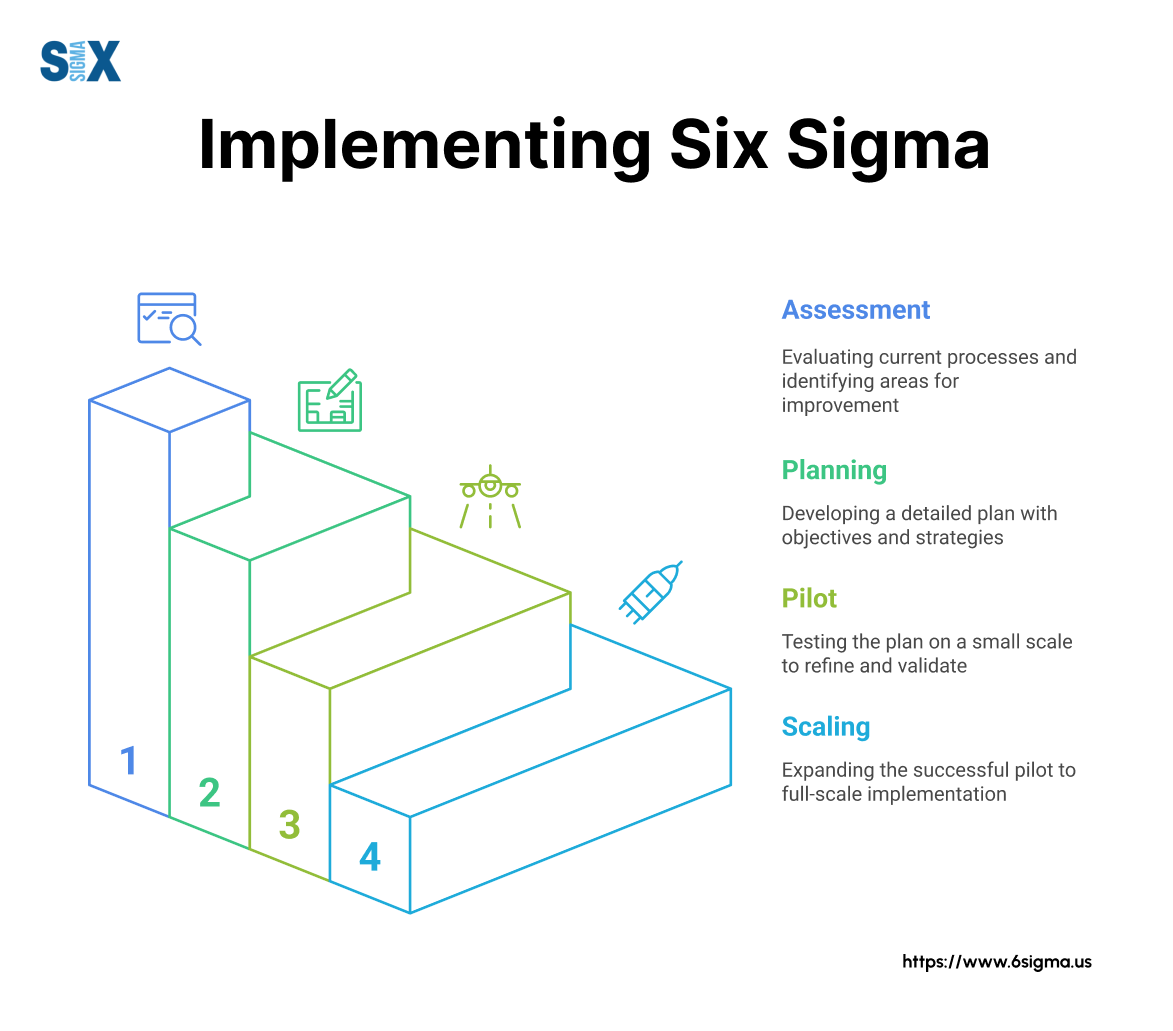
Waste Calculator Tool for Lean Enterprise Implementation
Step 1: Industry Selection
Step 2: Organization Size
Step 3: Current Process Assessment
Step 4: Financial Impact Estimation
Step 5: Results Display
Step 6: Next Steps Recommendation
Digital Transformation in Lean Enterprise
The convergence of lean enterprise principles with digital technologies creates powerful opportunities for organizations to achieve unprecedented levels of efficiency and customer value.
Digital tools not only accelerate traditional lean improvements but enable entirely new approaches to eliminating waste and optimizing flow.
Healthcare organizations demonstrate this synergy through digital health transformation initiatives that reimagine patient care delivery.
By applying lean principles to digital workflows, these organizations eliminate redundant documentation, reduce waiting time, and improve care coordination.
For example, one major hospital system used lean value stream mapping to redesign their digital patient intake process, reducing administrative time by 67% while improving data accuracy.
Telemedicine Applications
Telemedicine represents another area where lean enterprise thinking enhances digital implementation.
Organizations that apply lean principles to telemedicine design focus relentlessly on the patient experience, eliminating unnecessary steps and creating intuitive interfaces.
The most successful implementations map the entire virtual care journey—from appointment scheduling through follow-up care—to identify and eliminate digital friction points.
This lean approach to telemedicine design results in higher utilization rates and better clinical outcomes compared to technology-first implementations.
AI in healthcare
AI in healthcare delivers maximum value when deployed within a lean enterprise framework.
Rather than implementing AI solutions in isolation, leading organizations first optimize clinical workflows using lean methods, then strategically insert AI capabilities to address specific value-adding opportunities.
This approach prevents the common problem of layering new technology onto broken processes.
One healthcare network used this strategy when implementing AI-powered diagnostic support, first streamlining radiologist workflows before introducing algorithm-based image analysis.
The most successful digital transformations recognize that technology alone cannot deliver sustainable improvement.
By combining lean enterprise principles with digital capabilities, organizations create solutions that genuinely transform operations rather than simply digitizing existing inefficiencies.
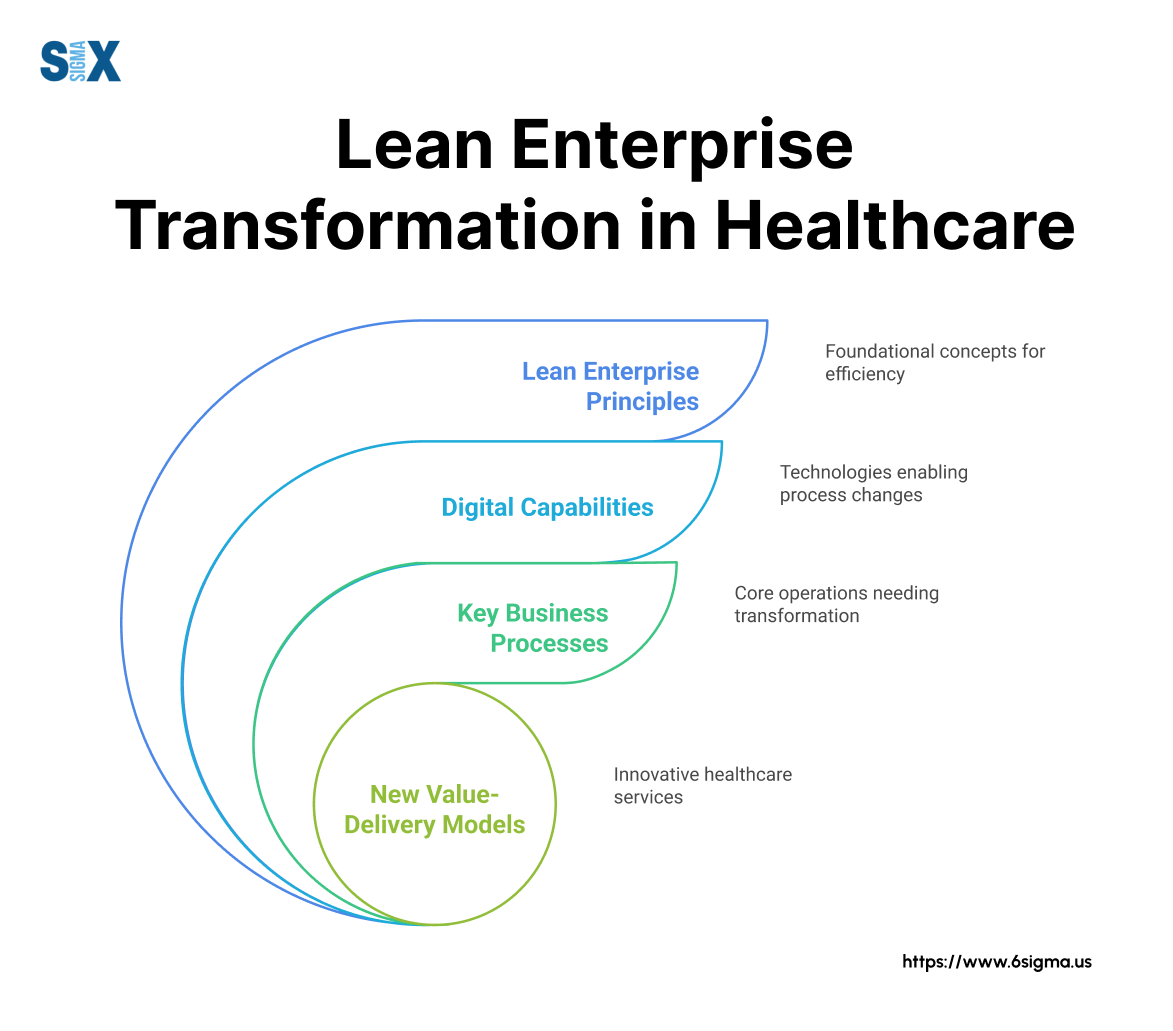
Future of Lean Enterprise
The lean enterprise methodology continues to evolve, shaped by changing business environments, technological advances, and emerging management practices.
Several key trends point to how lean thinking will develop in coming years.
Emerging Trends
First, lean enterprise principles increasingly merge with agile methodologies, creating hybrid approaches that combine lean’s focus on waste elimination with agile’s emphasis on adaptation and customer feedback.
This convergence proves particularly powerful in knowledge work environments where traditional lean tools designed for physical processes require modification.
Organizations that successfully blend these methodologies develop the ability to both eliminate waste and rapidly respond to changing market conditions.
Technology Integration in Lean Enterprise
Second, advanced analytics and machine learning transform how organizations identify improvement opportunities. Traditional lean enterprise implementations relied heavily on direct observation and manual analysis.
Today’s leading organizations leverage predictive analytics to identify patterns of waste and inefficiency that would be invisible to human observers.
Predictive Analytics
Third, lean enterprise concepts extend beyond organizational boundaries to optimize entire value networks.
Rather than focusing solely on internal operations, forward-thinking organizations apply lean principles across supplier relationships, distribution channels, and customer interactions.
Finally, sustainability concerns increasingly integrate with lean enterprise thinking.
Organizations recognize that eliminating waste aligns perfectly with environmental goals, creating opportunities to simultaneously reduce costs and environmental impact.
This alignment between operational excellence and sustainability creates powerful motivation for continued lean enterprise adoption.
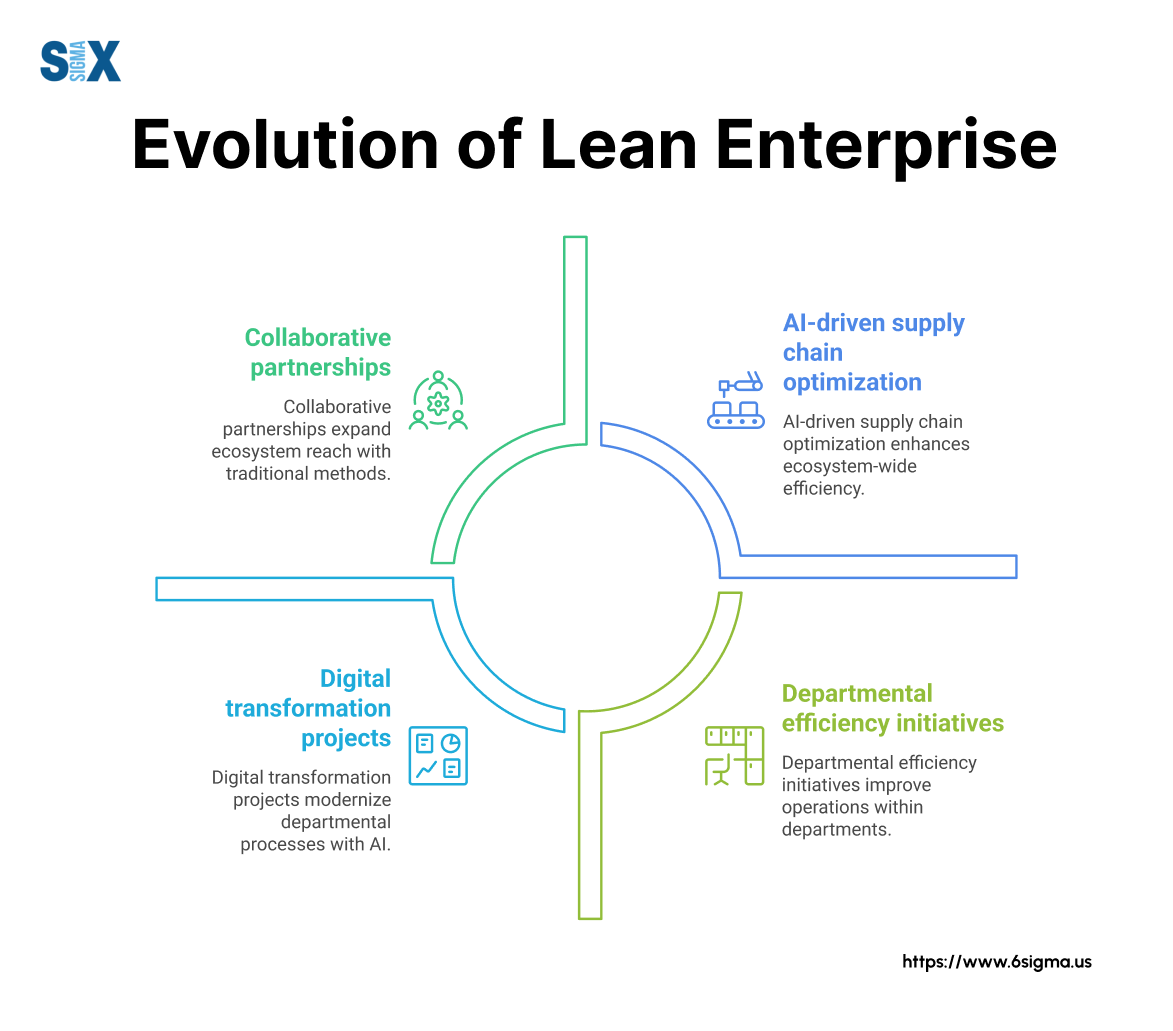
Moving Ahead with Lean Enterprise
Lean enterprise represents a proven approach to organizational transformation that delivers sustainable competitive advantage.
By focusing relentlessly on customer value, eliminating waste, and creating smooth flow throughout operations, organizations can achieve remarkable improvements in quality, cost, and delivery performance.
Transform Your Skills, Transform Your Organization
Start your lean enterprise journey from anywhere with Lean Introduction Training & Certification.
The journey begins with understanding the fundamentals of Lean — the five core principles and eight wastes—but succeeds through thoughtful implementation.
Organizations must balance technical tools with cultural change, recognizing that sustainable transformation requires both process excellence and people engagement.
The integration of lean principles with Six Sigma methodologies and digital technologies creates even more powerful improvement capabilities.
The future belongs to organizations that combine lean enterprise principles with emerging technologies and expanded scope, creating agile, efficient operations that deliver exceptional customer value while minimizing environmental impact.
SixSigma.us offers both Live Virtual classes as well as Online Self-Paced training. Most option includes access to the same great Master Black Belt instructors that teach our World Class in-person sessions. Sign-up today!
Virtual Classroom Training Programs Self-Paced Online Training Programs