Continuous Improvement Strategies: A Guide to Sustainable Business Excellence
Standing still means falling behind. According to McKinsey, companies that successfully implement lean and continuous improvement strategies can achieve significant improvements in productivity and operational costs, often in the range of 20–30% depending on the context and industry
Continuous improvement strategies goes beyond simple tweaks to existing processes. It’s a systematic approach to enhancing products, services, and processes through ongoing, incremental changes.
Unlock the fundamental skills to drive organizational excellence
Transform your understanding of process improvement with Lean Six Sigma Yellow Belt Certification.
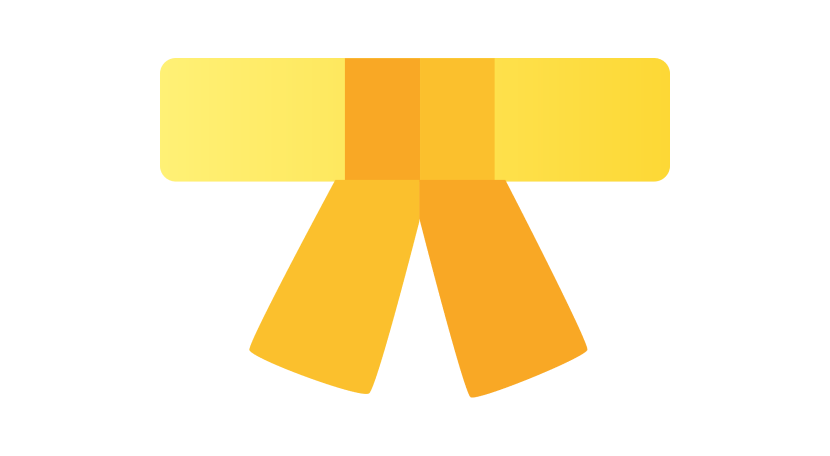
Rather than waiting for major problems to emerge, organizations that embrace continuous improvement as a business strategy proactively identify opportunities for enhancement, test solutions, measure results, and repeat the cycle.
Key Highlights
- Proven CI methodologies for immediate results
- Step-by-step implementation frameworks
- Industry-specific application techniques
- Measurement tools for tracking success
- Future trends reshaping CI practices
Before diving into specific methodologies like Six Sigma, let’s establish a solid foundation of what makes continuous improvement strategies so powerful and how they’ve evolved to become essential business tools.
What are Continuous Improvement Strategies?
Continuous improvement strategies represent more than just a set of tools—they embody a business philosophy focused on making small, consistent enhancements to processes, products, and services over time.
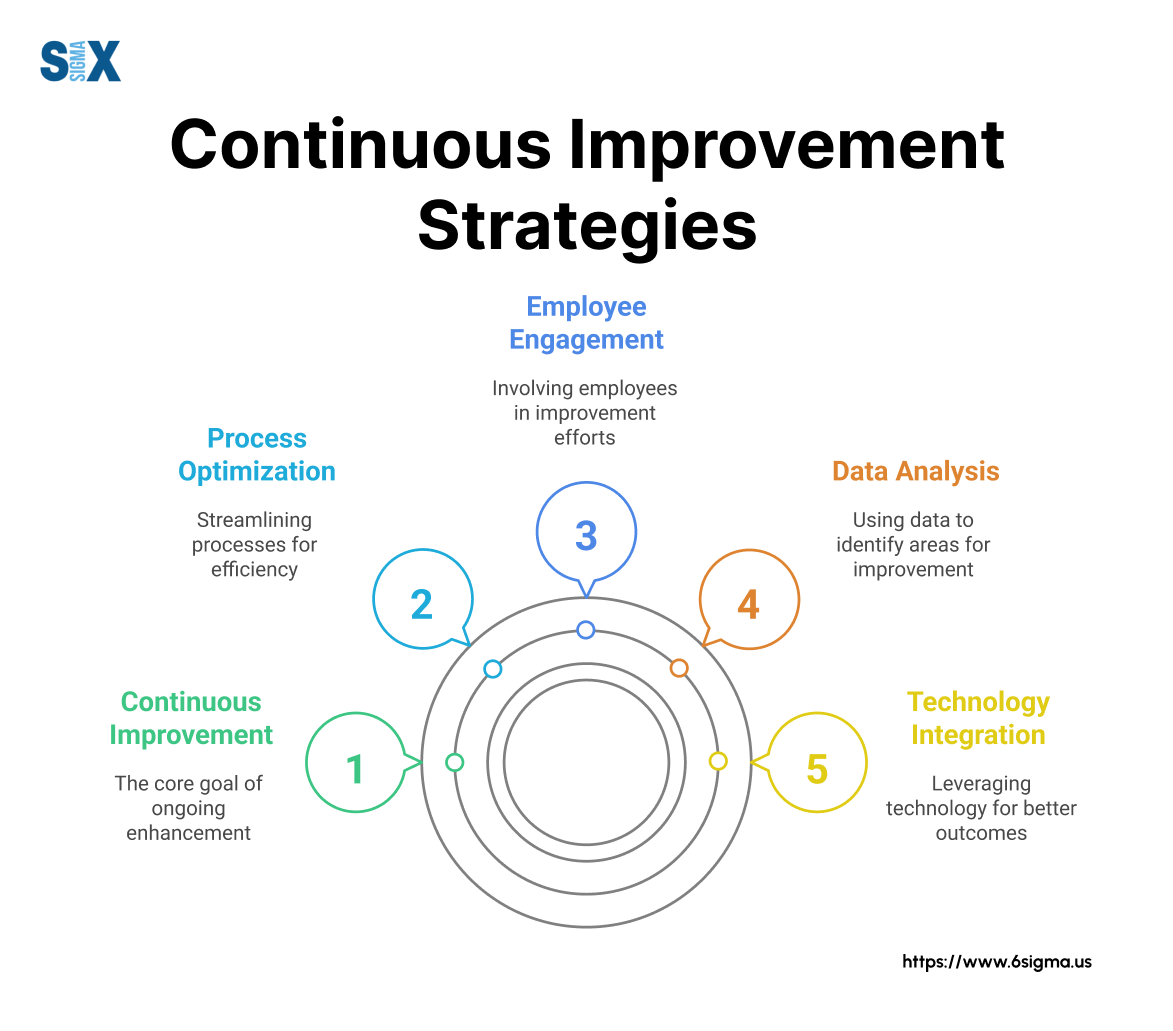
Unlike traditional approaches that wait for major problems before taking action, continuous improvement operates on the principle that even the most efficient processes can be made better through regular evaluation and refinement.
The power of these strategies lies in their cumulative effect. While a single 1% improvement might seem insignificant, when applied consistently across multiple areas, these small changes compound dramatically.
Organizations that implement a continuous improvement strategy plan typically build their approach around several key principles:
- Customer focus: Understanding that value is ultimately defined by customer needs
- Process orientation: Viewing work as interconnected processes rather than isolated tasks
- Data-driven decision making: Using metrics rather than assumptions to guide changes
- Employee involvement: Engaging team members at all levels in improvement efforts
- Systematic approach: Following structured methodologies rather than random fixes
These principles work together to create a self-reinforcing system. When employees actively participate in improvement initiatives, they develop deeper insights into processes.
The Business Case for Continuous Improvement
The financial impact of implementing continuous improvement business strategy extends far beyond cost-cutting.
Companies that excel at continuous improvement report significant advantages across multiple performance indicators:
Toyota, the pioneer of many continuous improvement techniques, saved over $100 million through employee suggestions in a single year.
Even smaller organizations report substantial returns—a mid-sized manufacturing company in the Midwest documented $2.5 million in savings after 18 months of implementing basic continuous improvement methods.
Beyond direct financial returns, organizations gain competitive advantages through:
- Increased agility: Faster response to market changes and customer demands
- Higher quality: Fewer defects and service failures
- Improved employee engagement: Lower turnover and higher productivity
- Enhanced innovation: More ideas generated and implemented
- Greater customer loyalty: Better experiences leading to repeat business
Perhaps most importantly, continuous improvement creates sustainable business advantages. While competitors might copy a single innovation, they cannot easily replicate a culture that consistently generates improvements year after year.
This explains why companies with mature continuous improvement programs typically outperform their industry peers by 3-5% in profit margins.
Continuous Improvement Maturity Assessment Quiz
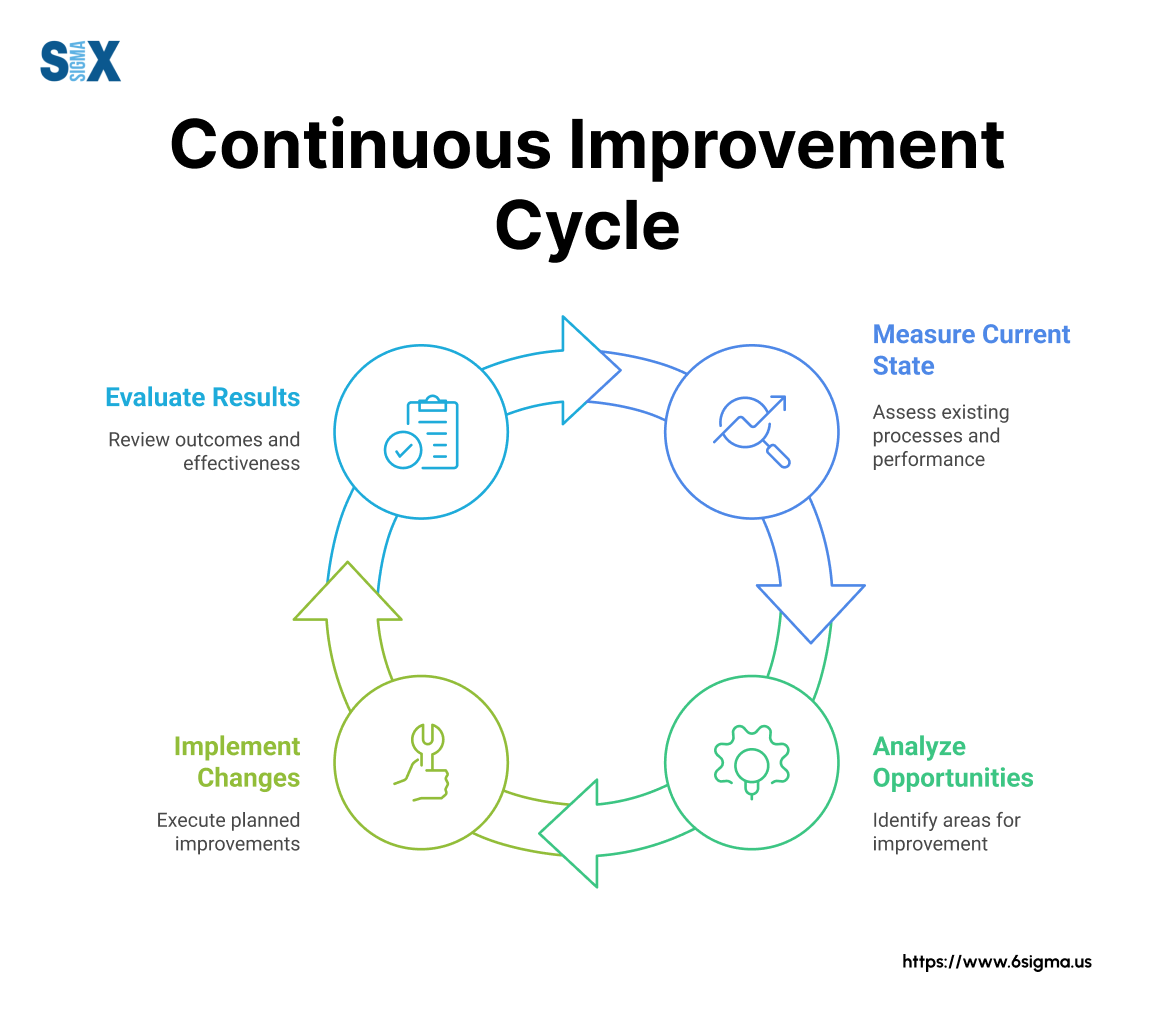
Leading Continuous Improvement Methodologies
Organizations seeking proven continuous improvement strategies often turn to Lean Six Sigma, which combines two powerful methodologies into a single framework.
This approach merges Lean's focus on eliminating waste with Six Sigma's emphasis on reducing variation and defects.
Lean Six Sigma projects typically follow the DMAIC methodology—Define, Measure, Analyze, Improve, and Control. This structured approach ensures teams tackle problems systematically rather than jumping to solutions.
For example, a healthcare organization might use DMAIC to reduce emergency room wait times by first defining what "wait time" means, measuring current performance, analyzing root causes, implementing targeted improvements, and establishing controls to maintain gains.
Organizations implementing Lean Six Sigma typically develop internal expertise through a belt-based certification system:
Yellow Belts understand basic concepts and support projects part-time. Our Six Sigma Yellow Belt certification program provides team members with fundamental knowledge to participate effectively in improvement initiatives.
Green Belts lead smaller projects while maintaining their regular job responsibilities. Our Six Sigma Green Belt certification and training program equips professionals with the tools to analyze processes and implement solutions.
Black Belts work full-time on complex projects and mentor Green Belts. Our Six Sigma Black Belt certification program signifies advanced expertise in statistical analysis and change management.
Master Black Belts develop deployment strategies and train other belts. A Six Sigma Master Black Belt certification represents the highest level of technical and leadership expertise.
White Belts receive basic awareness training to support the overall initiative. Our Six Sigma White Belt certification program introduces employees to improvement concepts.
Many organizations integrate Six Sigma certification with other continuous improvement strategies to create customized approaches.
For instance, combining Lean Six Sigma with Agile methods allows teams to deliver incremental improvements while maintaining statistical rigor.
Become the go-to problem solver in your organization
Grow your professional toolkit with advanced process analysis skills with Lean Six Sigma Green Belt Certification.
Other Key Methodologies
While Lean Six Sigma dominates many continuous improvement discussions, several other methodologies offer valuable approaches to organizational excellence:
Kaizen, meaning "change for better" in Japanese, focuses on making small, incremental improvements through employee involvement.
Unlike project-based approaches, Kaizen embeds improvement into daily work. Toyota famously implements over a million employee improvement suggestions annually through their Kaizen program.
This approach works particularly well in organizations seeking to build a grassroots culture of continuous improvement.
The PDCA (Plan-Do-Check-Act) Cycle provides a simple yet powerful framework for testing improvements before full implementation. First, teams plan a change, then implement it on a small scale, check results against expectations, and finally act on what they learned.
A retail chain might use PDCA to test a new customer service approach in one store before rolling it out company-wide.
Total Quality Management (TQM) emphasizes customer satisfaction through organization-wide quality efforts. This methodology integrates quality management into all activities and functions.
While less structured than Six Sigma, TQM establishes quality as everyone's responsibility rather than delegating it to a specific department.
The Fundamentals of Lean focus specifically on eliminating eight types of waste: defects, overproduction, waiting, non-utilized talent, transportation, inventory, motion, and extra-processing.
Organizations practicing lean management continuous improvement typically start by mapping value streams to identify non-value-adding activities.
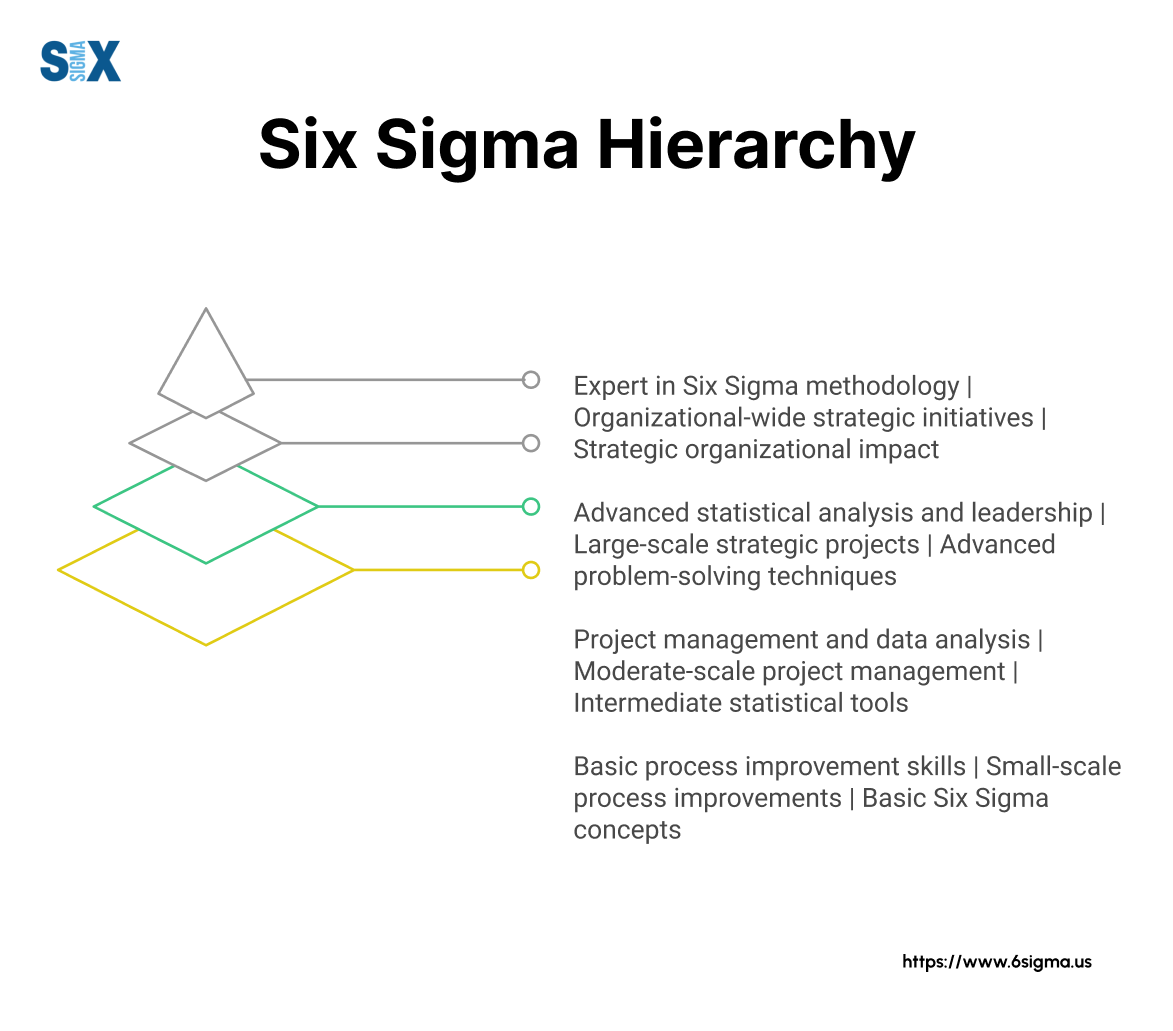
Implementation Framework for Continuous Improvement
Translating continuous improvement strategies from concept to reality requires a structured approach that balances methodical planning with cultural transformation.
Assessment and Planning
Successfully implementing continuous improvement strategies requires thoughtful preparation rather than rushing into tools and techniques. Organizations that achieve lasting results typically begin with a structured assessment of their current state.
The first step involves evaluating organizational readiness across several dimensions. This includes examining existing processes, identifying pain points, and assessing the current culture's receptiveness to change.
Goal setting follows assessment and should align continuous improvement objectives with broader business strategies.
Effective goals follow SMART criteria (Specific, Measurable, Achievable, Relevant, Time-bound) and connect to meaningful business outcomes.
Rather than vague aspirations like "improve quality", successful organizations set concrete targets such as "reduce customer complaints by 25% within six months" or "decrease order fulfillment time from 5 days to 2 days by Q3".
Resource allocation decisions significantly impact implementation success. Organizations must determine staffing needs, training requirements, technology investments, and time commitments.
Many continuous improvement strategy examples show that dedicated resources yield better results than part-time efforts.
For instance, Toyota allocates specific personnel to improvement activities rather than expecting employees to squeeze improvement work between regular duties.
Building a CI Culture
Even the most sophisticated continuous improvement strategies fail without a supportive culture. Building this culture requires deliberate effort across multiple fronts.
Leadership commitment stands as the most critical success factor. When executives demonstrate visible support through actions rather than just words, employees take improvement seriously.
This commitment manifests in budget allocations, personal participation in improvement activities, and recognition of improvement efforts.
Danaher Corporation, known for its exceptional continuous improvement results, requires all executives to participate in kaizen events and regularly review progress on improvement initiatives.
Employee engagement transforms continuous improvement from an imposed program to a natural way of working.
Successful organizations create mechanisms for employees to identify problems and suggest improvements.
Toyota's famous suggestion system generates millions of implemented ideas annually because employees know their input matters.
Training and development provide employees with both technical tools and problem-solving mindsets. While formal workshops teach specific methodologies, ongoing coaching helps employees apply these skills to real-world situations.
Measurement systems and rewards should reinforce continuous improvement behaviors.
When organizations measure and celebrate both improvement activities (like problems solved) and results (like cost savings), they signal what truly matters.
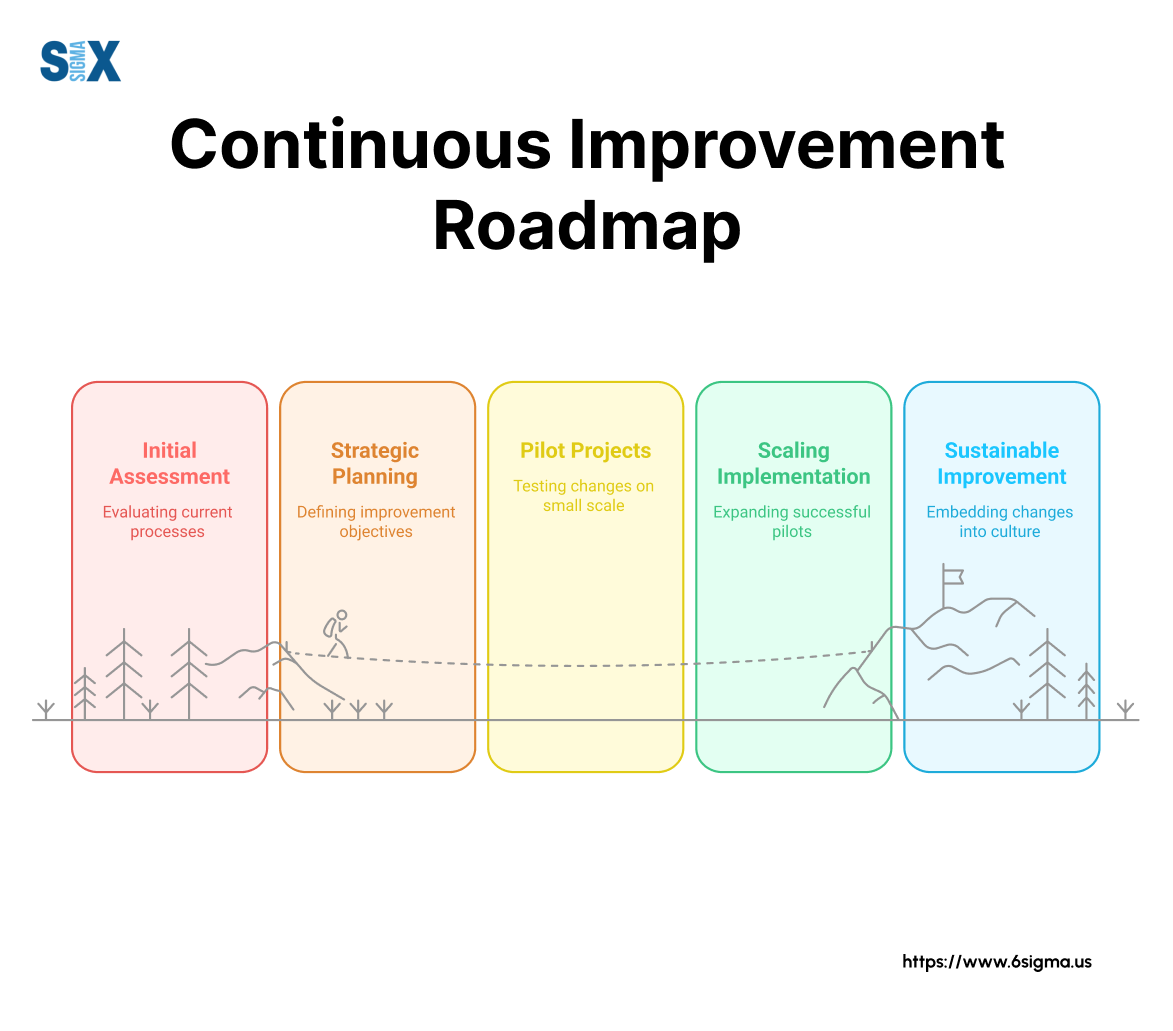
Industry-Specific Applications of Continuous Improvement
While the principles of continuous improvement remain consistent across sectors, their application varies significantly based on industry context, challenges, and opportunities.
Manufacturing Excellence
Manufacturing continuous improvement has the longest history, with roots in Toyota's production system developed in the mid-20th century.
Today's manufacturing leaders have refined these approaches into powerful systems that drive competitive advantage.
Harley-Davidson's turnaround represents one of the most dramatic manufacturing continuous improvement success stories.
Facing potential bankruptcy in the 1980s, the motorcycle manufacturer implemented a comprehensive improvement system that reduced production time from 72 days to just 2 days.
Their approach combined waste elimination with quality management, resulting in a 50% reduction in defects and saving the iconic American brand.
Boeing applied similar strategies to aircraft production, reducing assembly time for the 737 by 50% through value stream mapping and process standardization.
Their improvement teams identified and eliminated non-value-adding steps while maintaining strict safety and quality standards.
Best practices in manufacturing improvement typically include:
- Visual management systems that make process performance immediately visible
- Standard work documentation that captures the current best method
- Quick changeover techniques that reduce downtime between production runs
- Preventive maintenance programs that minimize equipment failures
- Pull systems that produce only what customers need when they need it
Organizations new to manufacturing improvement often begin with an introduction to Lean, focused on the "5S" methodology—Sort, Set in order, Shine, Standardize, and Sustain.
This creates an organized workspace that exposes waste and inefficiency, providing a foundation for more advanced continuous improvement strategies.
Service Industry Adaptation
Service organizations face unique challenges when implementing continuous improvement strategies for service organizations.
Unlike manufacturing, service processes often have higher variability, less visibility, and more direct customer interaction. Despite these differences, leading service providers have successfully adapted manufacturing-based improvement approaches.
Technology companies like IBM and Microsoft have integrated continuous improvement with Agile development methodologies.
This hybrid approach combines the iterative nature of Agile with the measurement rigor of Six Sigma certification programs. The result is faster software development with fewer defects and better alignment with customer needs.
Regardless of industry, successful continuous improvement strategies share common elements: they focus on customer value, involve employees at all levels, use data to drive decisions, and maintain a long-term perspective rather than seeking quick fixes.
Measuring Success and Overcoming Challenges
Even the most thoughtfully designed continuous improvement strategies require robust measurement systems and strategies for navigating common obstacles that emerge during implementation.
Key Performance Indicators
Effective measurement begins with selecting the right metrics to track progress. Organizations often make the mistake of tracking too many indicators, creating information overload rather than actionable insights.
Successful continuous improvement programs typically focus on a balanced set of metrics across four categories:
Quality metrics measure defect rates, error frequency, and customer satisfaction. These indicators reveal how well processes meet requirements and expectations.
A software company might track bug rates per thousand lines of code, while a call center might monitor first-call resolution percentages.
Time metrics capture cycle times, lead times, and response times. These measurements highlight process efficiency and customer experience. A manufacturing operation might track the time from order to delivery, while a hospital emergency department might measure door-to-doctor time.
Cost metrics include both direct expenses and hidden costs like rework, scrap, and excessive inventory.
These indicators connect improvement efforts to financial performance. Organizations often track cost of poor quality (COPQ) to quantify waste from defects, delays, and customer complaints.
Employee engagement metrics measure participation rates in improvement activities, suggestion implementation, and staff satisfaction. These indicators predict the sustainability of improvement efforts.
Companies like Toyota track the number of implemented employee suggestions as a leading indicator of their continuous improvement health.
Tracking methods have evolved significantly with digital technologies. Modern organizations use real-time dashboards that display KPIs visually and allow drill-down into problem areas.
These systems often include automated data collection to eliminate manual reporting burdens. When metrics show unexpected results, teams conduct root cause analysis to identify underlying issues rather than treating symptoms.
The most mature continuous improvement programs establish a clear connection between process metrics and business outcomes. This linkage demonstrates the strategic value of improvement efforts and secures ongoing executive support.
Common Challenges and Solutions
Even well-designed continuous improvement strategies encounter obstacles. Recognizing these challenges and having mitigation plans separates successful implementations from failed initiatives.
Resistance to change represents the most pervasive challenge. Employees may view improvement efforts as threats to their jobs or criticism of their current work.
Successful organizations address this by involving employees in identifying problems and developing solutions rather than imposing changes from above.
They also communicate the "why" behind improvement initiatives, connecting changes to customer benefits and organizational sustainability rather than just cost reduction.
Measurement challenges arise when organizations struggle to quantify the impact of their improvement efforts.
Effective programs establish clear baselines before making changes and use control groups where possible to isolate the effects of specific interventions. They also recognize that some benefits, like improved employee morale or enhanced customer loyalty, may take time to appear in financial results.
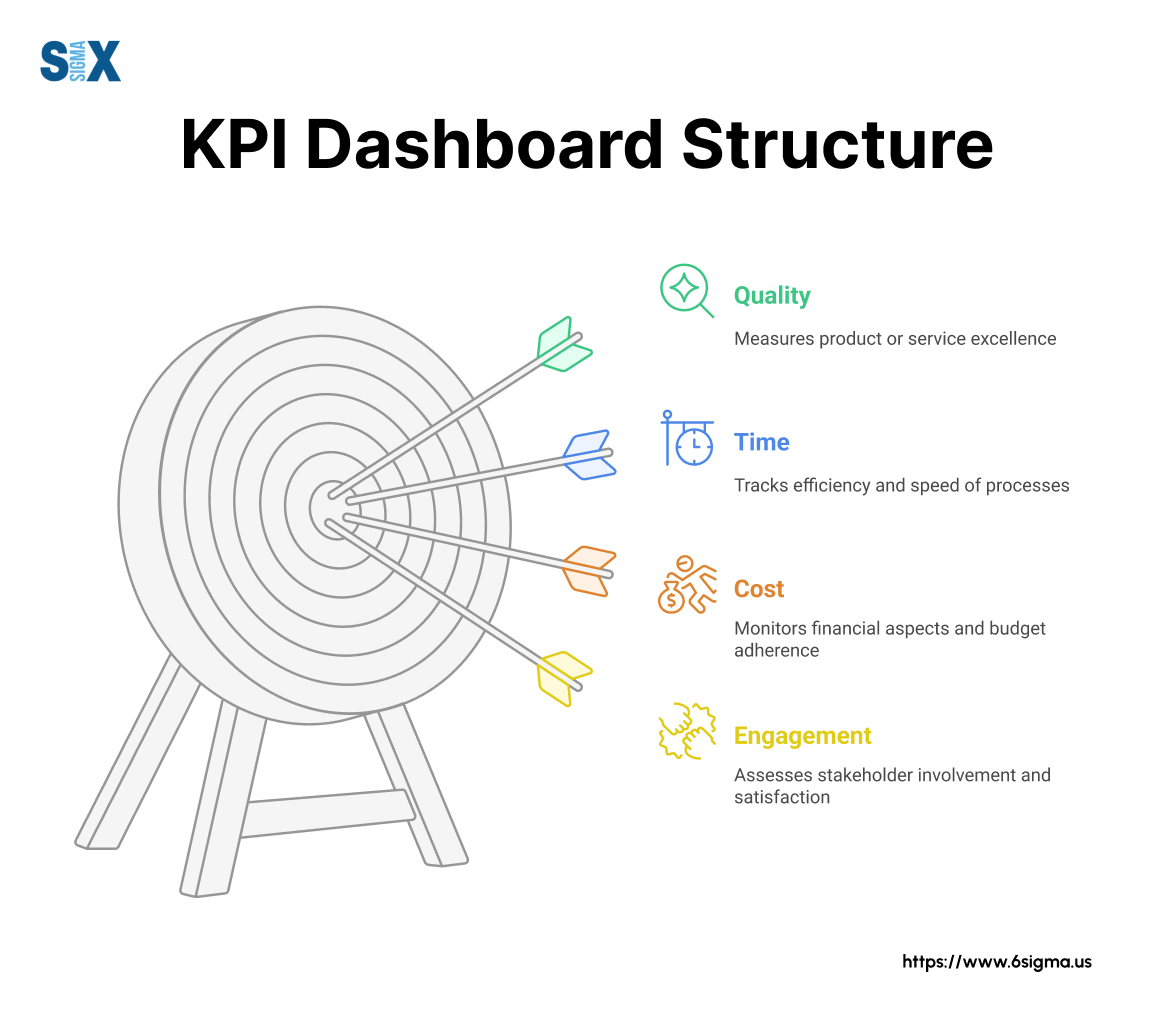
Future Trends and Innovation in Continuous Improvement
The field of continuous improvement strategies continues to evolve as new technologies and business models emerge.
Forward-thinking organizations are already exploring several key trends that promise to reshape how companies approach operational excellence.
Artificial intelligence and machine learning are transforming continuous improvement by identifying patterns and opportunities that humans might miss.
Predictive analytics can now forecast potential quality issues before they occur, allowing preventive action rather than reactive problem-solving.
Companies like Siemens use AI to analyze production data in real-time, automatically adjusting machine parameters to optimize quality and efficiency. This shift from manual analysis to algorithmic optimization dramatically accelerates the improvement cycle.
Digital twins—virtual replicas of physical processes—enable organizations to test improvement ideas in simulated environments before implementing them in the real world.
This capability reduces risk and increases the success rate of improvement initiatives. Manufacturers like GE use digital twins to optimize equipment maintenance schedules, while logistics companies simulate supply chain changes to identify potential disruptions before they affect customers.
Remote work has accelerated the adoption of virtual continuous improvement tools. Digital kanban boards, online gemba walks using video technology, and collaborative process mapping platforms allow distributed teams to engage in improvement activities regardless of location.
These tools have proven particularly valuable for global organizations managing improvement across multiple sites.
Sustainability-focused continuous improvement represents another emerging trend. Organizations increasingly recognize that eliminating waste often delivers environmental benefits alongside operational improvements.
Companies like Unilever and Patagonia have integrated environmental metrics into their continuous improvement frameworks, measuring carbon footprint reduction alongside traditional efficiency gains.
Cross-industry methodology blending continues to produce innovative approaches. Healthcare organizations borrow from manufacturing, while software companies adapt techniques from service industries.
This cross-pollination creates hybrid methodologies tailored to specific organizational contexts rather than rigid adherence to established frameworks.
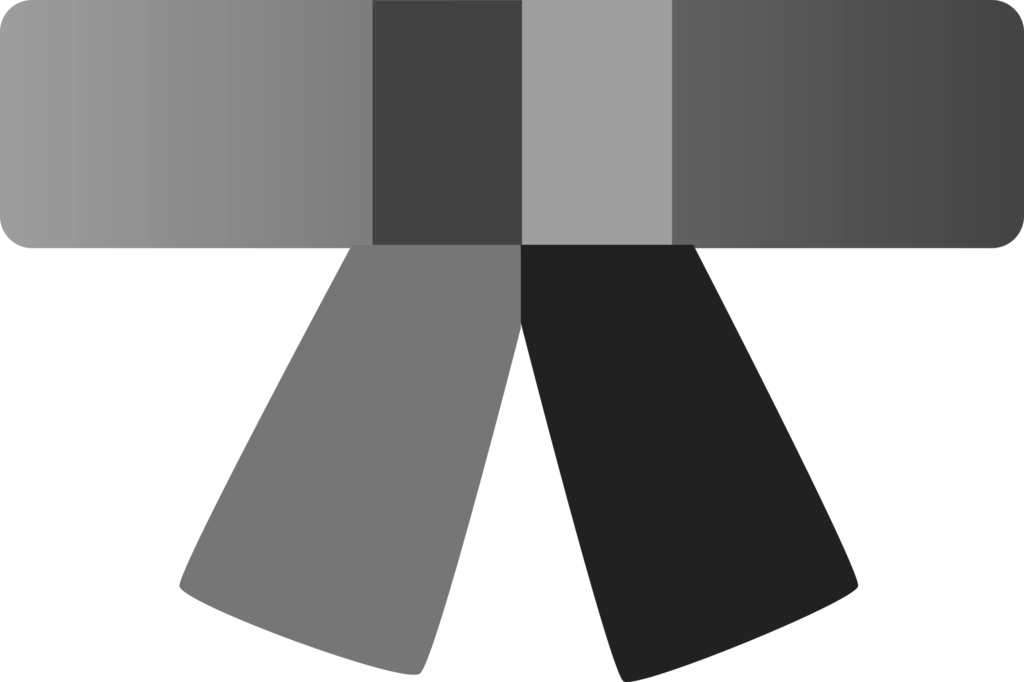
Develop advanced expertise in statistical analysis and change management
Position yourself as a strategic improvement leader with Six Sigma Black Belt Certification.
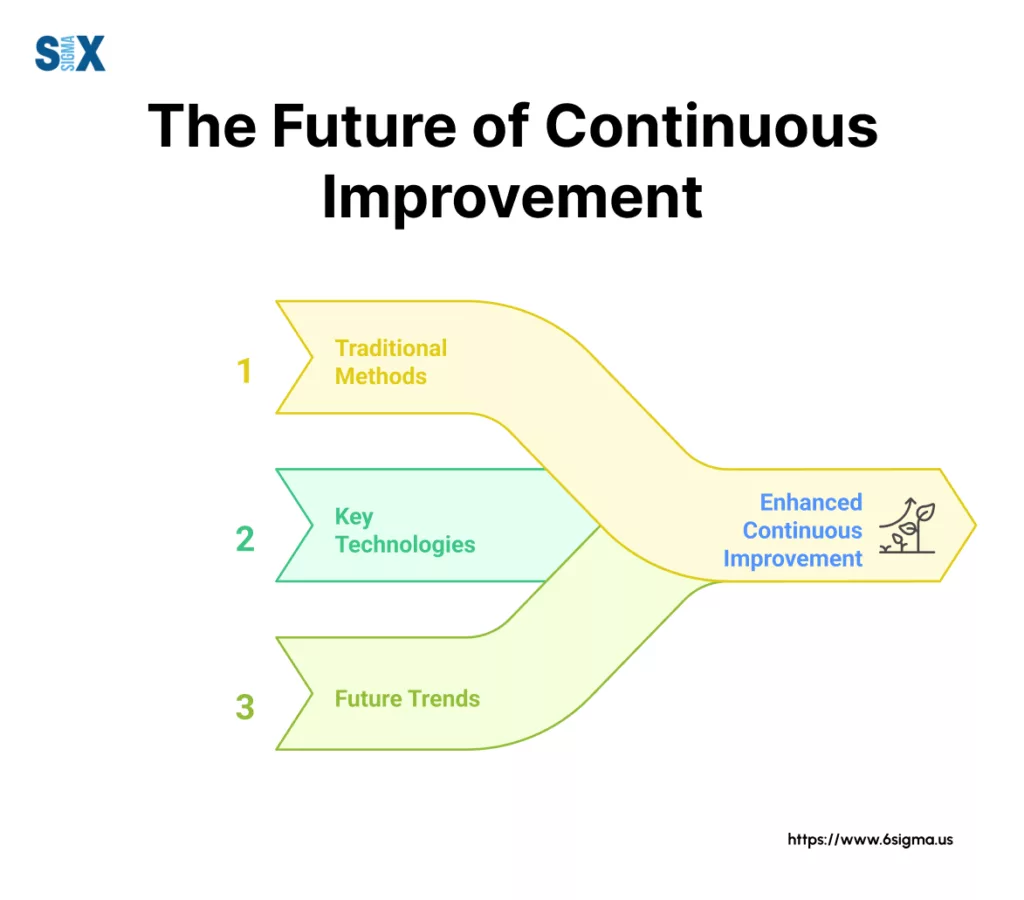
Conclusion and Next Steps
Effective continuous improvement strategies provide organizations with powerful tools to enhance quality, reduce costs, and increase customer satisfaction.
From manufacturing pioneers to service industry innovators, companies that systematically pursue improvement gain sustainable advantages over competitors who rely on sporadic change initiatives.
The journey toward continuous improvement begins with understanding your organization's current state and selecting appropriate methodologies that align with your business goals and culture.
Whether you choose Lean, Six Sigma, Kaizen, or a customized approach, success depends on leadership commitment, employee engagement, and systematic measurement of results.
To start implementing continuous improvement in your organization:
- Assess your current processes and identify high-impact improvement opportunities
- Select an appropriate methodology based on your specific challenges and resources
- Develop internal expertise through training and external support where needed
- Begin with focused pilot projects that demonstrate value quickly
- Build systems to sustain improvements and prevent regression
The organizations that thrive in the coming decade will be those that make continuous improvement part of their DNA rather than treating it as a temporary initiative.
By embedding improvement thinking into daily operations and strategic planning, these companies will adapt more quickly to changing markets and customer needs while maintaining operational excellence.
Ready to transform your organization through continuous improvement? Explore our specialized certification programs and implementation support services to accelerate your journey toward operational excellence.
SixSigma.us offers both Live Virtual classes as well as Online Self-Paced training. Most option includes access to the same great Master Black Belt instructors that teach our World Class in-person sessions. Sign-up today!
Virtual Classroom Training Programs Self-Paced Online Training Programs