Process Deviation for Manufacturing and Operational Success
Strict adherence to defined manufacturing and operational processes is crucial in regulated industries to ensure quality, safety, and compliance. However, unplanned variations/deviation in process do occasionally occur due to human or equipment factors.
Such “process deviations” from approved specifications can range from minor to major and potentially compromise standards if not promptly addressed. Identifying, investigating, and resolving deviations is thus critical for quality management.
By thoroughly reviewing documentation of any unintended departures from established workflows, organizations can gain valuable insights.
Analyzing root causes and impacts of variations helps strengthen processes to better support personnel performing valuable work.
With a shared commitment to principles of product and public safety, process deviation management serves as an opportunity. Through collaborative problem solving, systems may be enhanced to further fulfill vital responsibilities supporting overall well-being.
Key Highlights
- A process deviation happens when something unplanned goes differently than how it’s meant to during production. It means straying from the intended steps, guidelines, or requirements for making a product.
- This can occur in many important industries like medicine making, food, and chemicals. In these areas, closely following every detail of the process is key for quality and safety.
- Deviations can seriously impact things if not addressed. They may cause defects, fail to meet important regulations, or potentially risk health.
- By looking into deviations, companies can keep products up to standard, make sure rules are still being obeyed, and continuously enhance their methods.
- An effective way to manage this involves watching for process deviation, finding the root reasons, taking corrective actions, and documenting everything learned for the future.
- Keeping detailed records also allows companies to prove to overseers that they are meeting all requirements.
- Overall, carefully handling any unexpected changes helps maintain the quality people expect from important Industries. It ensures production stays reliable and safe.
What is Process Deviations?
A process deviation refers to any unexpected change from the usual steps when making a product.
This could happen in industries like food, medicine, chemicals, and others where carefully following procedures is important for safety and quality.
Process deviation issues can range from minor, like a small temperature change during heating, to major problems like equipment failure or human mistakes that significantly impact the final result.
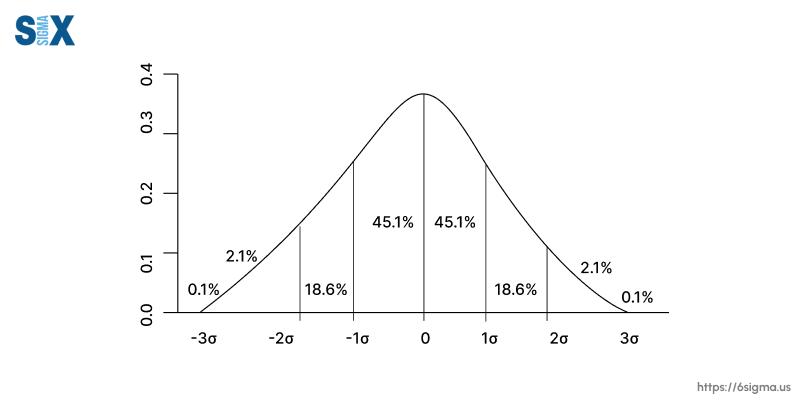
It’s crucial to watch for, investigate, and fix process deviations to keep production under control. This minimizes risks and helps ensure consistent outcomes.
Managing deviations well is key. Teams must detect what’s different, look at what caused it, implement solutions to fix and prevent recurrence, and thoroughly document everything.
Regulatory bodies like the FDA also strongly encourage proper deviation handling. This confirms groups are complying with good manufacturing practice standards and rules.
By proactively addressing process deviation upfront, manufacturers can strengthen their production management.
As a result, products benefit from improved quality while reducing waste. It also helps maintain customer trust and allows a clear demonstration of regulatory adherence.
Facing deviations head-on sets teams up for continued safety, efficiency, and compliance.
Types of Process Deviation
Process deviation can occur in many different forms within manufacturing processes and operations. Some common types include:
Equipment/Facility Deviations
These involve process deviation from specified equipment operating parameters, facility environmental conditions (temperature, humidity, etc.), or preventive maintenance schedules.
Examples are out-of-calibration equipment, HVAC system failures, or missed preventive maintenance activities.
Process Parameter Deviations
These occur when critical process parameters like time, temperature, pressure, speed, flow rate, etc. deviate from their specified ranges during manufacturing operations.
Strict adherence to validated process parameters is crucial for product quality.
Material/Component Deviations
These involve using incorrect raw materials, components that need to meet specifications, or deviating from approved material suppliers.
Quality issues can arise from substandard incoming materials.
Procedural Deviation in Process
Human errors leading to process deviation from approved manufacturing procedures, protocols, or standard operating procedures (SOPs) fall into this category.
Proper training and following documented instructions are vital.
Utility Process Deviation
Deviations related to utilities like water, gases, electrical power, compressed air, etc. not meeting specified quality standards or experiencing unexpected interruptions.
Packaging/Labeling Deviations
These cover issues with product packaging materials, packaging processes, or errors in batch records and labeling that could impact product quality or traceability.
Causes of Process Deviation
Process deviation can arise from a variety of factors, both human and systemic. Understanding the root causes is crucial for implementing effective corrective and preventive actions. Some common causes of process deviation include:
Human Factors
- Lack of training or inadequate understanding of procedures
- Fatigue or complacency leading to errors
- Intentional non-compliance or shortcuts taken
- Poor communication or miscommunication between shifts/teams
- Insufficient staffing levels or high employee turnover
Equipment/Facility Issues contributing to Process Deviation
- Equipment malfunctions, breakdowns, or improper maintenance
- Obsolete or outdated equipment lacking process control capabilities
- Utility failures (power, air, water, etc.)
- Environmental conditions outside acceptable limits (temperature, humidity, etc.)
- Facility layout or workflow issues causing process bottlenecks
Process Deviation due to Raw Material Variability
- Inconsistent quality of incoming raw materials
- Lack of supplier qualification and monitoring
- Changes in raw material sources or formulations
Process Design Flaws
- Inadequate process validation during product/process development
- Processes not developed with sufficient understanding of process variability
- Processes operating outside their established design space
- Insufficient process monitoring and control systems
Management System Weaknesses
- Lack of management commitment and oversight
- Inadequate standard operating procedures (SOPs) or outdated documentation
- Deficiencies in training programs and competency assessments
- Poor change management processes for deviations from approved processes
- Inadequate resources allocated for process monitoring and data analysis
Detecting and Investigating Process Deviation
Identifying process deviation promptly is crucial for maintaining product quality, regulatory compliance, and overall process performance. Several methods and tools can be employed for detecting process deviation:
Process Monitoring: Continuous monitoring of critical process parameters and quality attributes through statistical process control (SPC) tools like control charts can detect when a process deviates from its normal operating conditions or specification limits.
Control charts visually represent process variability over time, enabling early detection of trends or shifts that may indicate a deviation.
Data Analysis: Analyzing process data using statistical techniques can reveal patterns, anomalies, or deviations that may not be immediately apparent.
This could involve techniques like regression analysis, capability studies, or advanced data analytics methods like machine learning algorithms.
Process Audits: Regular process audits or inspections can uncover deviations from standard operating procedures (SOPs), good manufacturing practices (GMPs), or other regulatory requirements. These audits may be conducted internally or by external regulatory bodies.
Customer Complaints: Customer feedback, complaints, or reports of product quality issues can sometimes be the first indication of a process deviation that needs to be investigated.
Once a potential process deviation is detected, a thorough investigation should be conducted to determine the root cause. This typically involves:
- Assembling a cross-functional team with relevant expertise (e.g., process engineers, quality assurance, production personnel).
- Gathering and analyzing relevant data, records, and documentation related to the suspected process deviation.
- Conducting root cause analysis (RCA) techniques like fishbone diagrams, 5 Whys, or fault tree analysis to identify the underlying cause(s) of the process deviation.
- Verifying the root cause through additional testing, experimentation, or data analysis as needed.
The investigation should also assess the potential impact of the deviation on product quality, safety, and regulatory compliance.
Corrective and Preventive Actions
When a process deviation occurs, it is crucial to take corrective actions to address the immediate issue and preventive actions to reduce the likelihood of recurrence.
This involves a systematic approach to root cause analysis and implementation of effective solutions.
Corrective Actions
Corrective actions are immediate steps taken to rectify the identified nonconformity or process deviation. These may include:
- Reworking or reprocessing affected products/materials
- Segregating and controlling nonconforming products
- Initiating product recalls if necessary
- Stopping the process to make adjustments or repairs
- Retraining personnel on proper procedures
The key is to contain the issue swiftly and mitigate any negative impacts on product quality, safety, or regulatory compliance.
Root Cause Analysis
To implement effective preventive actions, the root cause(s) of the deviation must be determined through methodical investigation and data analysis techniques like:
- 5 Whys analysis
- Fishbone (Ishikawa) diagrams
- Fault tree analysis
- Process mapping and value stream mapping
This systematic approach helps identify underlying process, material, environmental, or human factors contributing to the nonconformity.
Preventive Actions
Once root causes are identified, preventive actions can be established to preclude recurrence. These may involve:
- Modifying processes, materials, equipment, or environment
- Implementing mistake-proofing techniques (poka-yoke)
- Enhancing process monitoring and control plans
- Revising standard operating procedures (SOPs)
- Improving personnel training programs
The preventive actions should be risk-based, focusing on higher-risk processes and more severe potential consequences of deviations.
Effectiveness checks are critical to ensure that implemented solutions deliver the intended results.
Regulatory Compliance and Documentation for Process Deviation
Process deviation can have serious implications for regulatory compliance, especially in highly regulated industries such as food, pharmaceuticals, and medical devices.
Regulatory agencies like the FDA provide strict guidelines and requirements for documenting, investigating, and addressing process deviation.
All process deviations must be thoroughly documented, including details on when the deviation occurred, what processes were affected, the potential root causes, and any immediate corrective actions taken.
This documentation serves as a record that can be reviewed by auditors to ensure proper procedures are followed.
Companies must have a robust deviation management system in place to track process deviation, investigate them thoroughly, and implement appropriate CAPA (corrective and preventive actions) plans.
The documentation trails created during this process are critical for demonstrating compliance during regulatory inspections.
Standard operating procedures (SOPs) should clearly define how process deviations are handled, including roles, responsibilities, escalation paths, and approval requirements.
SOPs ensure consistency and provide a framework for training employees on process deviation management.
Beyond internal documentation, companies may also need to notify regulatory bodies of certain deviations, depending on the potential impact on product quality and safety.
Failure to properly document and address deviations can result in regulatory penalties and actions.
Proper documentation demonstrates a company’s commitment to quality and proactive approach to identifying and resolving process issues before they lead to defects or non-compliant products reaching the market.
Comprehensive deviation records are an essential component of a robust quality management system.
Continuous Improvement and Process Optimization
Process deviation can highlight areas where improvements are needed, such as inefficient procedures, inadequate training, or outdated equipment.
Process optimization involves more substantial changes or redesigns aimed at achieving significant improvements in process performance, quality, or cost-effectiveness.
This may involve implementing new technologies, redesigning process flows, or adopting advanced process control and monitoring techniques.
By analyzing the root causes of process deviations, organizations can pinpoint bottlenecks, constraints, or inherent process limitations that need to be addressed through optimization efforts.
Effective continuous improvement and process optimization initiatives rely on data-driven decision-making.
Statistical process control (SPC) tools, such as control charts and process capability studies, can help organizations monitor process performance, identify sources of process variability, and quantify the impact of improvement efforts.
Regular process audits and management reviews also play a crucial role in identifying opportunities for optimization and ensuring that improvements are sustained over time.
Engaging employees and fostering a culture of continuous improvement is essential for the success of these efforts.
Providing training and education on process monitoring, data analysis, and problem-solving techniques can empower employees to identify and address process deviations proactively.
Encouraging cross-functional collaboration and knowledge sharing can also facilitate the identification and implementation of best practices across the organization.
SixSigma.us offers both Live Virtual classes as well as Online Self-Paced training. Most option includes access to the same great Master Black Belt instructors that teach our World Class in-person sessions. Sign-up today!
Virtual Classroom Training Programs Self-Paced Online Training Programs