First Time Yield (FTY): Driving Process Efficiency & Quality
Efficiency and minimizing re-dos are crucial for success. A major metric impacting streamlining and affordability directly is First Time Yield or FTY.
First Time Yield, a core Six Sigma building block, measures the percentage of units or products smoothly completing a process without defects or needing re-dos on the first try.
Focusing on First Time Yield, companies can spot chances for upgrades, smooth workflows and ultimately furnish higher quality outputs while slashing waste and reducing costs.
Over the course of my career, I’ve had the opportunity to collaborate with companies such as 3M, Dell, GE, and Intel, applying Six Sigma strategies to enhance operational performance.
Gaining expertise in these methodologies is often supported by Six Sigma certification, which provides structured tools and techniques for effective process improvement
Key Highlights:
- Understand the definition of First Time Yield (FTY) and its importance within the Six Sigma methodology for achieving process efficiency and quality.
- Learn the formula for calculating FTY and overcome common challenges in data accuracy and complex process environments.
- Uncover the hidden factory concept and its impact on First Time Yield, as well as techniques for rapid issue detection using FTY data.
- Explore the differences between First Time Yield (FTY) and Rolled Throughput Yield (RTY), and when to use each metric effectively.
- Discover proven strategies for improving First Time Yield, including continuous monitoring, employee training, process optimization, and supplier quality management.
- Gain insights into best practices and frequently asked questions related to FTY implementation and monitoring.
What is First Time Yield (FTY) and its Importance in Six Sigma?
Efficiency and quality are paramount. This is where the Six Sigma methodology, with its focus on First Time Yield (FTY), comes into play.
First Time Yield (FTY) is a quality metric that measures the percentage of units or products that pass through a process without any defects or the need for rework on the initial attempt.
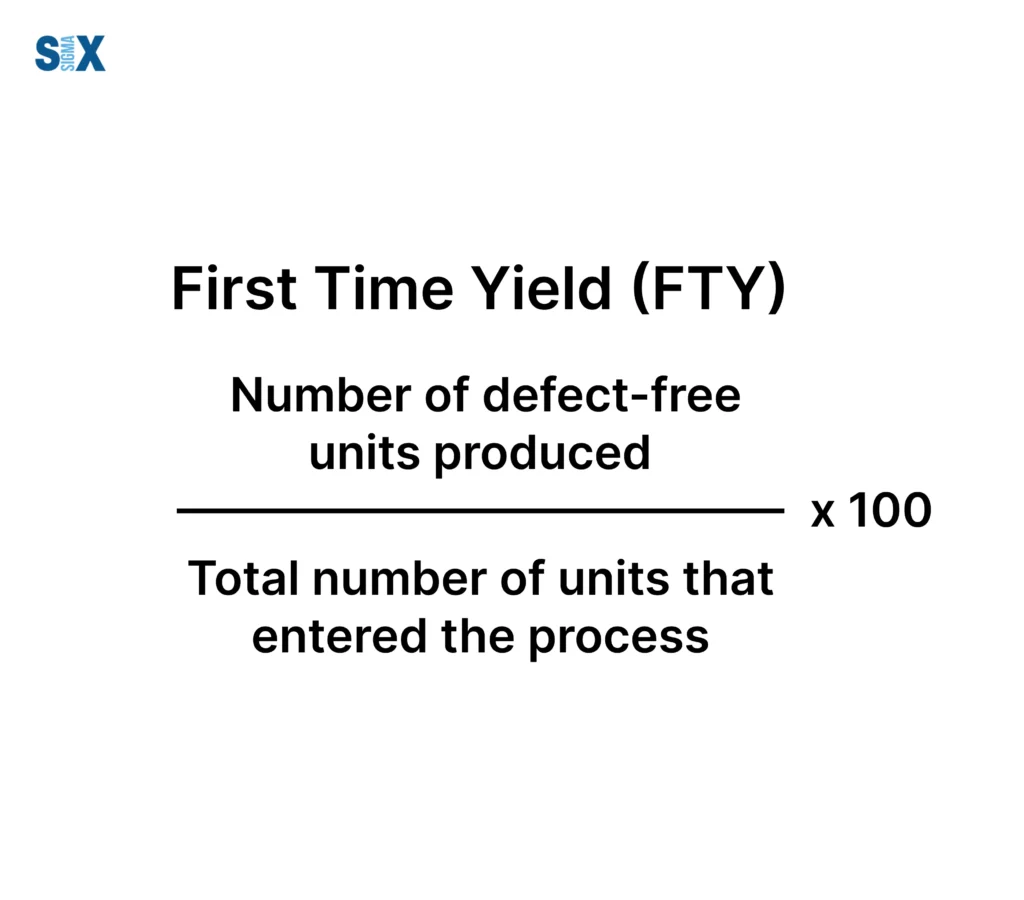
It directly assesses how well a process is performing in generating defect-free outputs from the get-go. The higher the FTY, the more efficient and cost-effective the process becomes.
Six Sigma methodology employs a data-driven approach to reduce variations and defects, serving as a foundation for process improvement. Six Sigma Certification programs help individuals master these techniques.
Within this framework, First Time Yield is a crucial indicator of process performance, providing valuable insights for continuous improvement initiatives.
Monitoring First Time Yield (FTY) data offers numerous benefits, including:
- Improved process efficiency: By identifying areas with low FTY, organizations can pinpoint and address inefficiencies, streamlining operations and reducing waste.
- Cost-effectiveness: A high FTY translates to fewer resources wasted on rework, scrap, or warranty claims, ultimately reducing operational costs.
- Enhanced customer satisfaction: Consistently delivering defect-free products or services is key to meeting and exceeding customer expectations, fostering long-term loyalty and trust.
Industry leaders, prioritizing First Time Yield has proven invaluable in driving sustainable success and maintaining a competitive edge in dynamic markets.
Calculating First Time Yield (FTY)
To effectively leverage the power of First Time Yield, it’s essential to understand how to calculate and interpret this metric accurately. The formula for FTY is relatively straightforward:
FTY = (Number of defect-free units produced / Total number of units that entered the process) × 100
For example, if a manufacturing process produces 90 defect-free units out of 100 units that entered the process, the FTY would be calculated as (90/100) × 100 = 90%.
While the calculation itself is simple, some challenges can arise in accurately determining FTY, particularly in complex processes or environments:
- Data accuracy and integrity: Incomplete or incorrect data can lead to misleading First Time Yield calculations and misguided corrective actions.
- Complex processes: When multiple departments or teams are involved, maintaining consistency in data collection methods becomes critical but challenging.
- Subjective definitions: The definition of a “defect” can vary from person to person, complicating the uniform calculation of FTY.
- Resource constraints: Adequate tools and skilled personnel are essential for accurate data collection and interpretation, which can be a challenge for some organizations.
To overcome these challenges, it’s crucial to establish standardized data collection processes, provide comprehensive training to personnel, and invest in robust data management systems.
By addressing these potential pitfalls, organizations can ensure that their FTY measurements serve as a reliable foundation for continuous improvement efforts.
Hidden Factory and its Impact on First Time Yield (FTY)
One of the key concepts that can significantly impact First Time Yield is the “hidden factory” – a term used to describe the rework and fix practices that become ingrained in standard operations.
These hidden factories arise when a system struggles to comply with required specifications on the first attempt, leading to the development of workarounds and rework processes.
While FTY calculations provide a measure of process effectiveness, they may not accurately reflect the true extent of rework occurring within an organization.
This is because First Time Yield focuses solely on the initial pass or fail of a unit, without considering the hidden factory of in-process inspection and rework.
In the tire inflation example we discussed earlier, the hidden factory accounted for 27.9% of production – a significant portion of resources devoted to rework and correction rather than value-added activities.
By uncovering hidden factories using root cause analysis techniques, organizations can systematically eliminate inefficiencies and reduce waste.
Furthermore, monitoring FTY data can aid in the rapid detection of issues within a process. Sudden dips or fluctuations in FTY can serve as early warning signs, allowing organizations to swiftly investigate and address potential problems before they escalate and negatively impact production efficiency or customer satisfaction.
First Time Yield (FTY) vs. Rolled Throughput Yield (RTY)
While First Time Yield (FTY) is a valuable metric for measuring the effectiveness of a single process step, it’s important to understand its relationship with another key Six Sigma metric: Rolled Throughput Yield (RTY).
RTY is a probability metric that quantifies the overall quality of a multi-step process by multiplying the Defects per Million Opportunities (DPMO) of each process step.
Unlike FTY, which focuses on a single step, RTY takes into account all defects and rework across the entire process, providing a more comprehensive view of cumulative process performance.
The key difference between RTY and FTY lies in their scope and application:
- FTY is suitable for measuring the likelihood of a single process step producing a defect-free output. It is most appropriate when the focus is on a specific step or when hidden factories are not a significant concern.
- RTY, on the other hand, is best utilized for measuring the cumulative effects of an entire multi-step process, taking into account all defects and rework across the entire value stream.
While First Time Yield provides valuable insights into individual process steps, RTY offers a more holistic understanding of overall process performance. By comprehending when to use FTY versus RTY, organizations can choose the most appropriate metric for their specific needs and accurately assess their processes, enabling targeted improvements to maximize efficiency and minimize rework.
Strategies for Improving First-Time Yield
Improving FTY is a continuous journey that requires a multifaceted approach. Based on my extensive experience working with leading organizations, I’ve identified several proven strategies that can drive significant improvements in FTY and, consequently, overall process efficiency.
Continuous monitoring of First Time Yield data
Consistent and proactive monitoring of FTY data is crucial for identifying discrepancies, imperfections, or emerging issues within the production process.
By collecting accurate, real-time quality data, organizations can make informed decisions for process improvement, reduce waste, ensure consistent product quality, and enhance customer satisfaction.
Employee training and involvement
Engaging employees through targeted training programs, such as the Six Sigma Green Belt certification, equips teams with advanced problem-solving skills for process optimization.
Organizations can tap into their valuable insights and foster a culture of continuous improvement by providing employees with the knowledge, skills, and resources necessary to effectively address issues in the production process.
Process optimization
Optimizing standard work, implementing accurate data collection systems, and monitoring equipment performance and health are key components of enhancing FTY.
Process optimization, a core focus of Six Sigma Black Belt training, involves analyzing workflows and deploying data-driven insights to eliminate bottlenecks
Supplier quality management
Ensuring that the raw materials and components supplied by vendors meet strict quality standards is a fundamental prerequisite for achieving high FTY.
Organizations should implement robust supplier vetting processes, establish clear quality expectations, and maintain open communication channels to address any quality-related concerns promptly.
By implementing these strategies in a coordinated and sustained manner, organizations can significantly enhance their First Time Yield, unlock operational efficiencies, and position themselves for long-term success in delivering high-quality products or services to their customers.
Best Practices
With FTY-related challenges and seeking guidance on best practices. Here are some tips and frequently asked questions that can help organizations maximize the value of First Time Yield:
Tips for improving First Time Yield (FTY):
- Rapid issue identification: Implement automated data collection systems and real-time monitoring to detect and address quality issues as they arise quickly.
- Automated data collection: Invest in robust data collection solutions to ensure accurate and timely FTY measurements, enabling data-driven decision-making.
- Frequent monitoring: Regularly monitor First Time Yield (FTY), as well as other yield metrics, as even a small dip can have significant impacts on quality, costs, and customer satisfaction.
Frequently Asked Questions:
While First Time Yield is a good indicator of potential issues, it may not capture the full extent of rework cycles or repairs. Utilizing test yields, which factor in the number of times a test is performed per group of products, in conjunction with FTY, can provide a more comprehensive understanding of total rework costs.
First Time Yield measures the ability of a product or service to pass a single step of a process on the first attempt, while throughput yield measures the ability to pass an entire string of steps that make up the process without any defects.
The frequency of First Time Yield monitoring depends on the specific requirements and quality standards of your system. As a general rule, FTY should be checked as often as your systems allow, ideally daily, to enable rapid identification and resolution of quality issues.
By implementing best practices, addressing common concerns, and leveraging the wealth of knowledge and experience within your organization, you can unlock the full potential of FTY and drive continuous improvement in your manufacturing or service delivery processes.
SixSigma.us offers both Live Virtual classes as well as Online Self-Paced training. Most option includes access to the same great Master Black Belt instructors that teach our World Class in-person sessions. Sign-up today!
Virtual Classroom Training Programs Self-Paced Online Training Programs