I-MR Chart in Lean Six Sigma. Everything You Need to Know
Maintaining a consistent product/service quality is imperative for success in modern times. Techniques like Statistical Process Control (SPC) empower organizations to monitor, assess, and control process variation, powering better quality with lesser resource consumption and driving continuous improvement efforts like Six Sigma.
SPC has various tools in its arsenal, among which the I-MR (Individual and Moving Range) chart stands out as a powerful and versatile method for monitoring and controlling processes where data is collected from individual observations or measurements.
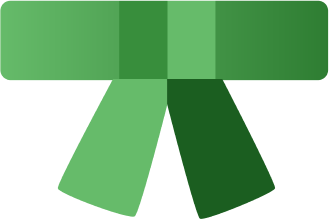
Master Process Control with Statistical Tools
I-MR charts are crucial for effective process monitoring. Lean Six Sigma Green Belt certification empowers you with the knowledge of SPC tools like I-MR charts to analyze data, control process variation, and drive significant improvements.
The I-MR chart is quite useful, especially in situations where a collection of data in rational subgroups is impossible.
For example, continuous processes, high-mix low-volume production, measurements taken at irregular intervals, etc.
I-MR charts are also quite effective in monitoring processes with individual data points, unlike traditional control charts like the X-bar and R charts, which require subgroup data.
Key Highlights of I-MR Chart
- The I-MR (Individual and Moving Range) chart is a powerful statistical process control tool used to monitor and control process variability over time.
- It is particularly useful when data is collected from individual observations or measurements, rather than subgroups.
- The I-MR chart consists of two separate charts: the Individual (I) chart and the Moving Range (MR) chart.
- The I chart tracks the actual values of individual observations, while the MR chart monitors the variability between consecutive observations.
- Gain crucial insights monitor and improve processes effectively.
- It is widely used in various industries like manufacturing, healthcare, construction, and service sectors, to ensure continuous process improvement and quality control.
What are I-MR Charts?
An I-MR chart consists of two complementary components – the Individuals (I) chart and the Moving Range (MR) chart.
The Individual chart plots the data points over time, giving you visibility into the process level. Meanwhile, the Moving Range chart tracks the variability between consecutive observations, providing insights into process stability.
Together, these two charts give you a comprehensive view of your process performance.
This is particularly valuable when it’s impractical or impossible to collect larger sample sizes, such as in many manufacturing, service, healthcare, and construction environments where you may only have individual observations or minimal subgroups to work with.
By closely monitoring both the process level and process variability using the I-MR approach, organizations can quickly identify potential issues or deviations from the desired performance targets.
This allows you to take timely corrective actions to maintain process stability and drive continuous quality improvement.
Fundamental Concepts of I-MR Chart
The I-MR chart, also known as the Individuals and Moving Range chart, is a type of control chart used in statistical process control (SPC).
It monitors and analyzes processes where only individual observations or measurements are available, rather than rational subgroup data.
This makes the I-MR chart particularly useful in situations where collecting and organizing data into subgroups is impractical or impossible.
The I-MR chart consists of two concurrently plotted charts:
- The Individuals (I) Chart: This chart plots the actual individual values or measurements over time. It is used to detect shifts or trends in the process level or mean.
- The Moving Range (MR) Chart: This chart plots the moving ranges of two consecutive individual observations. The moving range provides an estimate of the process variability based on the spread of the data.
Together, the I and MR charts allow you to monitor both the central tendency (using the I chart) and variability (using the MR chart) of a process simultaneously. This dual monitoring approach is critical for achieving statistical process control and maintaining a stable process.
Key Elements of an I-MR Chart
– Center Line (CL): The average of all individual observations for the I chart, and the average of the moving ranges for the MR chart.
– Control Limits: Statistically calculated upper and lower limits that define the threshold for out-of-control signals on each chart.
By analyzing patterns and signals on the I-MR charts, such as points beyond the control limits or non-random patterns, process abnormalities or sources of excessive variation can be detected.
This information can then be used to take corrective actions and improve the process capability and performance.
Data Collection and Preparation for I-MR Chart
Proper data collection and preparation are crucial steps for constructing effective I-MR charts. These control charts rely on individual observations, making the data collection process particularly important.
Data Collection
I-MR charts are designed to monitor processes where it is impractical or impossible to collect rational subgroup data.
In such cases, individual observations are recorded sequentially over time. The data collection frequency depends on the process being monitored and the desired level of control.
More frequent data collection allows for the timely detection of process shifts but increases the resource requirements.
It is essential to collect data that accurately represents the process being studied. Factors like operator skill, measurement system variation, and environmental conditions should be taken into account to ensure the data’s integrity.
Sample Size Considerations
While I-MR charts can theoretically plot an unlimited number of individual observations, practical considerations often limit the sample size. A larger sample size enhances sensitivity to process shifts but increases the chart’s complexity and resource needs.
Many practitioners recommend a maximum of 25-30 data points on an I-MR chart before starting a new chart. This balance between sample size and chart readability allows for effective process monitoring while preventing the chart from becoming overly cluttered.
Data Preparation
Before constructing the I-MR charts, the collected data should be organized and checked for completeness and accuracy.
Any missing or erroneous data points should be addressed through appropriate methods, such as interpolation or removal, based on established guidelines.
Rational Subgrouping
In some cases, it may be possible to group the individual observations into rational subgroups based on factors like periods, operators, or machines.
If rational subgroups can be formed, it is generally preferable to use other control charts, such as the X-bar and R charts, which are more sensitive to process shifts.
By following proper data collection and preparation procedures, organizations can ensure that the I-MR charts accurately reflect the process being monitored, enabling effective process control and continuous improvement efforts.
Constructing and Interpreting I-MR Charts
Constructing accurate I-MR control charts is crucial for effective process monitoring and control. The steps involved are:
Plotting Individual Values (I Chart)
- Calculate the average of all individual data points to get the center-line
- Calculate the control limits as:
Upper Control Limit (UCL) = X̄ + 3(MR̄)/1.128
Lower Control Limit (LCL) = X̄ – 3(MR̄)/1.128
Where MR̄ is the average of the moving ranges
Plotting Moving Range (MR Chart)
- Calculate moving ranges between consecutive data points
- Plot the moving ranges on the MR chart
- Calculate the center line as MR̄ (average of moving ranges)
- Set upper control limit (UCL) as UCL = 3.27(MR̄)
- Lower control limit is usually set at 0
Interpreting the Charts
- If any individual point falls outside the control limits on the I chart, it signals an out-of-control process
- Look for patterns like runs, trends, and hugging on the I chart using Western Electric rules
- On the MR chart, any point beyond UCL indicates excessive variation between consecutive points
Control chart interpretation requires an understanding of the process, statistical thinking, and the context of data. Identifying true signals amidst noise is key to taking effective corrective actions for process improvements.
The charts should be regularly monitored, with control limits periodically revised as more data becomes available. Software tools can automate control chart generation and rule-based interpretation for efficient process control.
Process Monitoring and Control with an I-MR Chart
The primary purpose of an I-MR chart is to monitor and control a process over time. By analyzing the patterns on the control charts, you can detect issues with the process and take corrective actions before many nonconforming units are produced.
Monitoring Process Stability with I-MR Chart
The I-MR chart allows you to monitor the stability of a process by examining whether the individual data points fall within the control limits.
If points fall outside the control limits or show any nonrandom patterns, this indicates the process is out-of-control and should be investigated for assignable causes of variation.
Out-of-Control Signals
There are several tests based on run rules, such as the Western Electric rules or Nelson rules, that can detect non-random patterns that may indicate the process is out of control, even if no points fall outside the control limits.
Common out-of-control signals include runs above/below the mean, hugging of the control limits, and other anomalous patterns.
Process Capability
In addition to monitoring process stability, the I-MR chart can provide insight into the capability of the process.
The moving range (MR) part of the chart estimates the variability within the process. This can be compared against specification limits to assess if the process is capable of consistently meeting requirements.
Corrective Actions
When an out-of-control condition is detected on an I-MR chart, it triggers the need for corrective actions.
This involves identifying and eliminating the root causes of the excessive variation through techniques like brainstorming, cause-and-effect diagrams, and other structured problem-solving methods used in Six Sigma Green Belt certification and continuous improvement initiatives.
Achieving and Sustaining Control with I-MR Chart
The ultimate goal of using I-MR charts is to bring the process into a state of statistical control by reducing common and assignable causes of variation.
Once the process is stable and capable, ongoing monitoring with I-MR charts helps sustain that state of control and enables real-time interventions if the process starts deviating again.
By continuously monitoring and controlling the process with I-MR charts, organizations can improve quality, reduce costs associated with nonconforming products/services, and drive ongoing efforts for process improvement and optimization.
Combining SPC with Lean fundamentals like waste reduction can amplify process efficiency gains.
Applications and Case Studies of I-MR Chart
The I-MR chart finds extensive applications across various industries for monitoring and controlling process variability.
Its ability to analyze individual observations makes it particularly useful in scenarios where subgrouping is impractical or impossible.
Manufacturing Processes
In manufacturing environments, the I-MR chart is commonly used to monitor critical quality characteristics of individual units or products.
Examples include monitoring the dimensions of machined components, fill weights of packaged goods and electrical properties of electronic devices.
The chart helps identify sources of excessive variation, such as tool wear, machine adjustments, or material inconsistencies.
Healthcare
Healthcare organizations employ I-MR charts to monitor various processes and ensure quality of care. Some applications include tracking patient wait times, monitoring laboratory test results, and analyzing medication dosage levels.
By detecting abnormal variations, healthcare providers can take corrective actions to improve patient safety and service quality.
Service Industries
Service industries, such as call centers, financial services, and hospitality, utilize I-MR charts to monitor individual customer interactions or transactions.
For instance, call centers can track call handling times, banks can monitor processing times for loan applications, and hotels can analyze check-in/check-out durations.
These charts help identify bottlenecks, inefficiencies, or training needs within the service delivery process.
Construction
In the construction industry, I-MR charts are used to monitor various quality characteristics of individual construction components or activities.
Examples include monitoring the compressive strength of concrete samples, tracking the thickness of applied coatings, and analyzing the levelness of floor installations.
These charts aid in ensuring construction quality and identifying potential issues before they escalate.
Case Study 1: Automotive Component Manufacturer
An automotive component manufacturer used I-MR charts to monitor the diameter of engine valve stems produced on a machining line.
The charts helped identify a gradual increase in variation, which was traced back to tool wear.
By implementing a tool replacement schedule based on the control chart signals, the manufacturer reduced scrap rates and improved process capability.
Case Study 2: Hospital Laboratory
A hospital laboratory implemented I-MR charts to monitor individual patient test results for a critical diagnostic marker.
The charts revealed occasional out-of-control signals, which led to the discovery of equipment calibration issues and improper sample handling procedures.
Addressing these root causes improved the accuracy and reliability of the laboratory testing process.
These examples illustrate the versatility of the I-MR chart in diverse industries and processes.
By continuously monitoring individual observations, organizations can detect abnormal variations, identify root causes, and implement corrective actions to maintain process stability and improve overall quality.
Software and Tools for I-MR Charts
Creating and analyzing I-MR charts manually can be time-consuming and prone to errors, especially when dealing with large datasets or multiple processes.
Fortunately, various software tools and applications are available to streamline the process of constructing, monitoring, and interpreting I-MR charts.
These tools can significantly enhance efficiency, accuracy, and data visualization, making it easier to identify and address process issues.
1. Statistical Software Packages:
- Minitab: Minitab is a comprehensive statistical software package widely used in industries for quality control and process improvement.
It offers a user-friendly interface for creating and analyzing I-MR charts, along with a range of other control charts and statistical tools. - JMP: Developed by the SAS Institute, JMP is a powerful data analysis software that includes robust capabilities for constructing and interpreting I-MR charts.
It supports advanced features such as control chart rules, process capability analysis, and customizable control limits.
2. Spreadsheet Applications:
- Microsoft Excel: Excel is a widely available and versatile spreadsheet application that can be used to create I-MR charts.
With built-in functions and add-ins, users can construct control charts, calculate control limits, and visualize data trends. - Google Sheets: As a cloud-based alternative to Excel, Google Sheets offers similar functionality for creating and analyzing I-MR charts.
It allows for real-time collaboration and data sharing, making it a convenient option for team-based projects.
3. Dedicated Control Chart Software:
- QI Macros: QI Macros is a specialized software package designed for creating and analyzing various types of control charts, including I-MR charts.
It offers advanced features like control chart rules, process capability analysis, and customizable reports. - SPC XL: SPC XL is an Excel add-in specifically designed for statistical process control (SPC) applications.
It provides a comprehensive set of tools for constructing and interpreting I-MR charts, as well as other control charts and SPC techniques.
4. Online Tools and Web Applications:
- Control Chart Simulators: Several online tools and web applications offer interactive simulations and visualizations of I-MR charts.
These tools can be useful for educational purposes, training, or quick data analysis without installing dedicated software. - Cloud-based SPC Solutions: Some software vendors offer cloud-based SPC solutions that allow users to create, monitor, and share I-MR charts and other control charts through a web interface, enabling remote access and collaboration.
When selecting software or tools for I-MR charts, it’s essential to consider factors such as ease of use, data integration capabilities, advanced analysis features, reporting and visualization options, and compatibility with existing systems or workflows.
Additionally, some industries or organizations may have specific software requirements or preferences based on their quality management systems or regulatory compliance needs.
Regardless of the chosen software or tool, it’s crucial to ensure that users receive proper training and understand the underlying principles of I-MR charts and statistical process control.
This knowledge, combined with the right tools, can significantly enhance the effectiveness of process monitoring and continuous improvement efforts within an organization.
SixSigma.us offers both Live Virtual classes as well as Online Self-Paced training. Most option includes access to the same great Master Black Belt instructors that teach our World Class in-person sessions. Sign-up today!
Virtual Classroom Training Programs Self-Paced Online Training Programs