Comprehensive Guide to Capability Analysis for Process Improvement
Capability analysis is a powerful statistical technique that allows companies to quantify their ability to meet customer specifications and requirements.
By evaluating the performance of a process or characteristic against defined tolerance limits, capability analysis provides valuable insights into process potential and actual performance levels.
Learn to quantify and improve process performance
Master Capability Analysis with Lean Six Sigma Green Belt Certification!
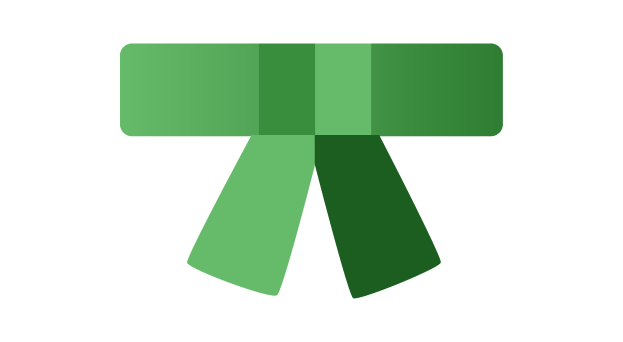
Key Highlights
- Capability analysis is a critical tool for ensuring process performance meets specifications and requirements.
It involves calculating capability indices like Cp, Cpk, and Cpm to quantify process potential and actual performance. - Capability studies help identify sources of variation, validate measurement systems, and drive process improvements.
- Statistical assumptions like normality, stability, and independence must be verified for valid capability analysis.
- Advanced techniques exist for analyzing non-normal data and accounting for process drift.
- Software tools streamline capability calculations, charting, and monitoring for quality control.
- Interpreting capability results correctly is crucial for making data-driven decisions on process capability.
- Case studies illustrate best practices across industries like manufacturing, services, and Six Sigma programs.
What is Capability Analysis
Capability analysis is a statistical technique used to evaluate the performance of a process or system to specified requirements or specifications.
It is a crucial tool in quality control and process improvement initiatives, helping organizations identify potential issues and opportunities for optimization.
Definition and Objectives of Capability Analysis
Capability analysis aims to quantify the ability of a process to produce outputs that consistently meet defined specifications or tolerances. The primary objectives of conducting a capability analysis include:
- Determining if a process is capable of operating within established specifications or tolerances.
- Identifying sources of variation that may be causing defects or inconsistencies in the process output.
- Providing a baseline for monitoring process performance over time.
- Assisting in setting realistic and achievable specifications or tolerances for a process.
- Supporting data-driven decision-making for process improvement efforts.
Importance in Quality Control
In the context of quality control, capability analysis plays a vital role in ensuring that products or services consistently meet customer requirements and industry standards. By analyzing process performance, organizations can:
- Reduce the risk of producing defective or non-conforming outputs.
- Improve product or service quality, leading to increased customer satisfaction.
- Identify opportunities for process optimization and cost savings.
- Comply with regulatory requirements and quality management system standards.
- Enhance competitiveness by delivering consistent and reliable products or services.
Applications and Use Cases of Capability Analysis
Capability analysis finds applications across various industries and domains, including manufacturing, healthcare, finance, and service sectors. Some common use cases for capability analysis include:
- Manufacturing processes: Evaluating the capability of production lines, machinery, or assembly operations to meet dimensional or performance specifications.
- Service operations: Assessing the capability of service delivery processes, such as call center response times or transaction processing times, to meet service-level agreements (SLAs).
- Quality control: Monitoring the capability of inspection or testing processes to detect defects or non-conformities within specified limits.
- Process design: Determining the capability of a proposed process or system to meet target specifications during the design phase.
- Supplier evaluation: Assessing the capability of suppliers or vendors to consistently provide materials or components that meet quality requirements.
By conducting capability analysis, organizations can proactively identify and address potential issues, ensuring that their processes consistently deliver outputs that meet or exceed customer expectations and industry standards.
Process Capability Indices and Ratios
Process capability indices are statistical measures used to quantify the ability of a process to produce output within specified limits.
These indices provide valuable insights into the performance and potential of a process, enabling informed decisions about process improvements.
Cp, Cpk, Cpm – calculations and interpretations
The most commonly used process capability indices are:
- Cp (Process Capability Ratio): Cp compares the allowable process spread (upper specification limit – lower specification limit) to the actual process spread (6 times the process standard deviation).
A Cp value greater than 1.33 is generally considered acceptable for most applications. - Cpk (Process Capability Index): Cpk accounts for process centering in addition to spread. It is the minimum of two values: the distance from the process mean to the nearest specification limit divided by half the process spread.
A Cpk value greater than 1.33 is desirable. - Cpm (Process Capability Index for Non-Normal Data): When data is non-normal, Cpm provides a more robust capability measure by incorporating the process mean and standard deviation along with sample skewness and kurtosis.
Interpreting these indices involves comparing their values to established benchmarks. Higher values indicate better capability to meet specifications consistently.
Process capability ratios for normal and non-normal data
For normal data distributions, Cp and Cpk are the preferred indices. However, many real-world processes exhibit non-normal behavior.
In such cases, Cpm or other distribution-specific indices like Cpm-square are more appropriate measures of process capability.
Capability analysis assumptions and limitations
Key assumptions in capability analysis include stable processes, adequate sample sizes, and independence of data points.
Limitations arise when these assumptions are violated or when the process exhibits time-varying behavior, multi-modality, or other complexities.
It’s crucial to understand the underlying statistical assumptions and carefully interpret capability indices within the context of the specific process under study.
Complementing indices with visual tools like histograms and control charts can provide a more comprehensive process assessment.
Data Collection and Analysis Methods
Conducting an effective capability analysis requires collecting accurate and representative data on the process or product characteristic being studied.
There are several key methods and techniques involved in this stage:
Sampling Techniques
Most capability studies cannot measure every single unit produced, so sampling methods are employed to obtain a representative subset of the output for analysis.
Some common sampling approaches include:
- Random sampling: Units are selected entirely at random from the population.
- Stratified sampling: The population is divided into different groups (strata) and samples are drawn from each stratum.
- Cluster sampling: The population is divided into clusters and samples are randomly selected clusters.
The sample size must be large enough to allow for valid statistical inferences about the process capability. This size depends on the process distribution, specifications, and confidence level required.
Measurement System Analysis (MSA)
Before collecting data, it’s critical to ensure your measurement system (instruments, appraisers, methods, etc.) is accurate and precise.
MSA techniques like gage repeatability and reproducibility (GR&R) studies quantify the amount of variation caused by the measurement system itself.
This prevents inaccurate conclusions about the true process capability.
Statistical Process Control (SPC) Charts
SPC charts are extremely useful tools in capability analysis for monitoring the process over time and checking if it remains in statistical control.
By tracking statistics like the mean, range, or deviations from the center line, you can identify issues like drifts, trends, or assignable causes of variation. Only data from an in-control state should be used for current capability calculations.
Control charts are also used for pre-control (before calculating capability indices) and monitoring the improved process capability in the future.
Some common SPC charts are X-bar/R, X-bar/S, Individual/Moving Range, and more. The control chart chosen depends on the data type, subgroup size, and study objectives.
Capability Analysis Tools and Software
Conducting capability analysis requires specialized statistical tools and software. There are several options available, ranging from comprehensive statistical packages to online calculators and automated solutions.
Minitab and Other Statistical Packages
Minitab is one of the most widely used software for capability analysis and other quality improvement techniques.
It provides a suite of tools for calculating process capability indices (Cp, Cpk, Cpm), creating control charts, performing normality tests, and more. Other popular statistical software like JMP, SAS, and R also offer comprehensive capability analysis capabilities.
These packages allow you to import data, perform assumptions checking, calculate indices, and generate detailed reports.
Many also integrate with manufacturing databases and data acquisition systems for seamless analysis. While powerful, statistical packages can have a steep learning curve and may require training.
Online Calculators and Tools
For quick calculations or when full-fledged software is not available, online process capability calculators can be useful. These web-based tools allow you to input sample data and specification limits to compute basic capability metrics like Cp and Cpk.
Some examples of free online capability calculators include those offered by NIST/SEMATECH, Sigma-Shortcut, and StatisticsHowTo.com. While convenient, these tools tend to have limited functionality compared to comprehensive packages.
Automating Capability Studies
In a production environment, manual capability analyses can be cumbersome, especially with large data sets. Many manufacturers opt to automate the process using software solutions that integrate with their statistical process control (SPC) and quality data systems.
Solutions like QI Macros, Hertzler Systems, and Infinity QS provide capabilities to schedule routine capability analyses, set up rules for analysis, and generate reports automatically. This enables frequent monitoring of process performance metrics in real-time.
When selecting capability analysis tools, considerations include data integration needs, analytical requirements, cost, training resources, and user interface preferences. Having the right software is crucial for efficient, accurate, and insightful capability assessments.
Interpreting Capability Analysis Results
After collecting the necessary data and performing the capability analysis calculations, the next critical step is to correctly interpret the results.
This will allow you to determine if the process meets specifications and requirements, identify potential sources of excessive variation, and provide recommendations for process improvement.
Meeting Specifications and Requirements
The key process capability indices like Cp, Cpk, and Cpm provide insights into whether the process is capable of operating within the specified limits.
A Cp value greater than 1.33 is generally considered a capable process for meeting requirements. However, the Cpk is more useful as it accounts for process centering between the specifications.
A Cpk value below 1.33 indicates that the process mean is too close to one of the specification limits, increasing the likelihood of producing non-conforming units.
Processes with Cpk below 1 are considered incapable. The Cpm further modifies Cpk by including any non-normal distribution effects.
When interpreting these indices, it’s important to consider the application and consequences of non-conformance. More critical processes may require higher capability levels like Cpk > 1.67.
The process capability requirements should be clearly defined upfront.
Identifying Sources of Variation with Capability Analysis
Even capable processes can benefit from reducing overall variation. The capability analysis results, combined with other statistical methods like control charts, can pinpoint potential sources of excessive variation – both common cause and assignable cause.
Common causes are inherent to the process and require process improvements to reduce variation. These could include inadequate machinery, unclear work instructions, or untrained operators.
Assignable causes are specific circumstances that require immediate correction, such as a broken tool or incorrect settings.
Pareto analysis of defect data can identify the vital few root causes driving the majority of issues. Process mapping may reveal non-value-added activities introducing unnecessary variation. Gauge R&R studies ensure measurement systems are adequate.
Develop advanced diagnostic skills to identify and eliminate performance bottlenecks
Learn systematic approaches to understanding and resolving complex process challenges with
Root Cause Analysis Training.
Process Improvement Recommendations
Based on the capability analysis interpretation, specific recommendations can be made to improve process performance and reduce variation:
- Adjust machine settings or replace worn components to re-center the process
- Implement systematic PM schedules to maintain equipment
- Improve work instructions with visual aids for clarity
- Conduct comprehensive operator training on best practices
- Upgrade measurement devices or gage calibration procedures
- Streamline process flow by eliminating non-value-added steps
- Implement lean techniques like 5S and mistake-proofing
- Transition to more capable machinery or automate manual operations
- Adjust specification limits if they are too tightly constrained
The recommendations should provide detailed, actionable steps while considering the technical and economic feasibility of the organization. Prioritizing the areas of improvement by their potential impact is also valuable.
Ultimately, the goal of interpreting capability analysis is to leverage the results to achieve a stable, predictable, and continuously improving process that consistently meets customer requirements.
Case Studies and Best Practices of Capability Analysis
To better understand how capability analysis works in real-world scenarios, let’s look at some case studies from the manufacturing and service industries.
Applications of Capability Analysis in the Manufacturing Industry
One common application is analyzing the capability of a machine to produce parts within specified tolerances. An automotive manufacturer conducted a capability study on a milling machine producing engine cylinder liners.
Based on the process capability indices and control charts, they determined the process was not capable of meeting the tight specifications. The root cause was excessive tool wear causing increased variation over time.
By implementing a tool replacement program and optimizing machining parameters, they were able to improve capability and reduce scrap rates.
In another case, a food processing plant analyzed the capability of their bottling line to fill containers within the approved weight range. The initial capability ratios indicated the process was not centered on the target weight.
By making minor adjustments to the filling equipment, they were able to re-center the process and achieve satisfactory capability levels.
Service Industry Applications
Capability analysis techniques can also be applied to service processes beyond just manufacturing. A hospital examined the capability of their emergency department to meet a target of admitting patients from the waiting room within 30 minutes of arrival.
Historical data and control charts revealed the admissions process was not capable, with excessive delays during peak hours.
Applying lean Six Sigma methods, they streamlined intake procedures and staffing levels, achieving consistent on-time admissions.
A call center analyzed their agents’ ability to handle customer calls within a specified time limit based on call type. The capability analysis pinpointed certain call scripts and languages with poor capability ratios.
This led to improved training materials and better forecasting of multilingual staffing needs.
Key Takeaways and Pitfalls to Avoid
While capability analysis is a powerful methodology, there are some common pitfalls to be aware of:
- Ensuring the quality of input data – bad measurements will lead to inaccurate conclusions
- Properly accounting for non-normal data distributions when calculating indices
- Not mistaking a capable process for one that is centered on the target
- Maintaining ongoing process control once capability is achieved
Some best practices include:
- Using capability analysis proactively before problems arise
- Applying the techniques consistently across all processes
- Involving cross-functional teams in studies for different perspectives
- Documenting procedures and calculations for future reference
- Monitoring capability on a regular basis, not just one-time studies
By following proven methodologies and learning from these examples, companies can maximize the benefits of capability analysis for their quality improvement efforts.
SixSigma.us offers both Live Virtual classes as well as Online Self-Paced training. Most option includes access to the same great Master Black Belt instructors that teach our World Class in-person sessions. Sign-up today!
Virtual Classroom Training Programs Self-Paced Online Training Programs