Six Sigma Principles. Process Capability Index (Cpk) for Business Success
The process capability index, or Cp and Cpk for short, is a crucial tool for monitoring and controlling how much variation a process encounters about its specification limitations.
These statistical measures offer insightful information about how well a process is operating and what actions could be required to make improvements.
Master Statistical Process Control with Green Belt Certification
Become a key driver of operational excellence in your organization
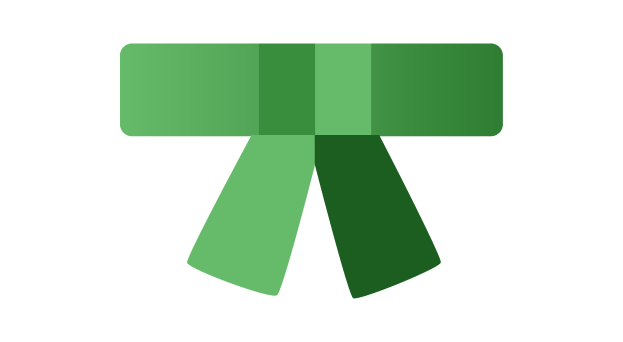
Quick Overview
- Formulas that account for process variation and specification restrictions are used to calculate Cp and Cpk.
- Understanding how to interpret Cp and Cpk statistics can help determine whether a process can reliably meet criteria.
- Statistical process control, often taught in six sigma certification programs, is one strategy that can be used to improve process capabilities.
Understanding Process Capability Index (Cp and Cpk)
The process capability index, also known as Cp and Cpk, is a statistical metric used to measure the ability of a manufacturing process to produce output that meets specific quality requirements or specifications.
It provides a quantitative way to assess how well a process is performing compared to its natural variation or tolerance limits.
The process capability index has two main components:
- Cp (Process Capability): This measures the potential or inherent capability of a process to produce output within the specified tolerance limits, assuming the process is centered.
Cp looks at the ratio of the specification limits to the natural variation or spread of the process.
- Cpk (Process Capability Index): This measures the actual capability of the process, taking into account both the process variation and the centering of the process relative to the specification limits.
Cpk accounts for any shift or drift in the process mean away from the target or midpoint of the specifications.
Learn how Cp and Cpk fit into the Lean Six Sigma methodology.
Our FREE Lean Six Sigma Overview course introduces you to a comprehensive toolkit for process improvement and capability analysis.
Both Cp and Cpk are calculated based on the process standard deviation and the specification limits:
Cp = (Upper Specification Limit – Lower Specification Limit) / (6 * Process Standard Deviation)
Cpk = Minimum of [(Upper Specification Limit – Process Mean) / (3 * Process Standard Deviation),
(Process Mean – Lower Specification Limit) / (3 * Process Standard Deviation)]
The key difference between Cp and Cpk is that Cp only considers the process variation, while Cpk also factors in the centering or location of the process relative to the specification limits.
Understanding how to calculate, interpret, and improve the process capability index is crucial for manufacturers and quality professionals looking to optimize their processes and deliver consistent, high-quality products.
Calculating Process Capability Index (Cp and Cpk)
The process capability index is a statistical measure used to quantify how capable a process is of producing output within specification limits. There are two main process capability indices – Cp (process capability) and Cpk (process capability index).
Calculating Process Capability (Cp)
The process capability (Cp) is calculated using the following formula:
Cp = (Upper Specification Limit – Lower Specification Limit) / (6 * Standard Deviation)
Where:
- Upper Specification Limit (USL) is the maximum acceptable value for the process
- Lower Specification Limit (LSL) is the minimum acceptable value for the process
- Standard Deviation (σ) is a measure of the spread or variability in the process
The Cp index compares the natural process variation to the allowable specification limits. A higher Cp value indicates a more capable process.
Interpreting Cp:
- Cp < 1 – Process is not capable, output frequently outside specification limits
- Cp = 1 – Process is just barely capable, 99.73% of output within specification limits
- Cp > 1 – Process is capable, 99.73% of output within specification limits
- Cp > 1.33 – Process is highly capable, with 99.99% of output within specification limits
Calculating Process Capability Index (Cpk)
The process capability index (Cpk) takes into account both the process variation and the centering of the process relative to the specification limits. Cpk is calculated using the following formula:
Cpk = Minimum of [(USL – μ) / (3σ), (μ – LSL) / (3σ)]
Where:
- μ is the process mean or average
- σ is the process standard deviation
Cpk considers how centered the process is relative to the specification limits. A higher Cpk value indicates a more capable and centered process.
Interpreting Cpk:
- Cpk < 1 – Process is not capable, output frequently outside specification limits
- Cpk = 1 – Process is just barely capable, 99.73% of output within specification limits
- Cpk > 1 – Process is capable, 99.73% of output within specification limits
- Cpk > 1.33 – Process is highly capable, with 99.99% of output within specification limits
The key difference between Cp and Cpk is that Cpk accounts for the centering of the process, while Cp only considers the spread of the process relative to the specification limits.
Cpk is generally considered a more robust and comprehensive measure of process capability.
Apply Cp and Cpk calculations and other statistical techniques using industry-standard software
Our FREE Introduction to Statistics and Graphical Analysis with Minitab course offers practical training in using statistical software for process capability studies.
Interpreting Process Capability Index Results
Once you have calculated the process capability index (Cp and Cpk) for your process, the next step is to interpret the results.
The values of Cp and Cpk provide insights into how well your process is performing and whether it is meeting the required specifications.
Process Capability (Cp)
The process capability index Cp tells you how capable your process is of meeting the specified tolerances or requirements. Specifically, Cp compares the natural variability of the process (6σ) to the allowed variability (the specification limits).
A Cp value of 1.00 or greater indicates that the natural variability of the process is smaller than the allowed variability, meaning the process is capable of consistently meeting the specifications.
The higher the Cp value, the more capable the process is. Here’s a general interpretation of Cp values:
- Cp < 1.00 – Process is not capable of meeting specifications
- Cp = 1.00 – Process is barely capable of meeting specifications
- Cp > 1.00 – Process is capable of meeting specifications
- Cp ≥ 1.33 – Process is highly capable of meeting specifications
It’s important to note that Cp only looks at the process spread and does not take into account the centering of the process. This is where the Cpk index comes into play.
Process Capability Index (Cpk)
The process capability index Cpk considers both the process spread and the centering of the process to the specification limits. Cpk is the minimum of the two ratios: (Upper Spec Limit – Mean) / 3σ and (Mean – Lower Spec Limit) / 3σ.
The Cpk value indicates how well the process is centered within the specification limits. A Cpk value of 1.00 or greater indicates that the process is both capable and well-centered. Here’s a general interpretation of Cpk values:
- Cpk < 1.00 – Process is not capable and/or not well-centered
- Cpk = 1.00 – Process is barely capable and/or centered
- Cpk > 1.00 – Process is capable and well-centered
- Cpk ≥ 1.33 – Process is highly capable and well-centered
It’s important to note that both Cp and Cpk should be considered when evaluating process capability.
A process may have a high Cp value but a low Cpk value, indicating that the process is capable but not well-centered. Ideally, you want both Cp and Cpk to be 1.33 or greater for a highly capable and well-centered process.
By interpreting the Cp and Cpk values, you can gain valuable insights into the performance of your process and identify areas for improvement.
Improving Process Capability
Once you have calculated the process capability index (Cp and Cpk) for your process, the next step is to work on improving the capability if it is not meeting your desired standards.
There are several strategies and techniques you can employ to enhance the process capability and ensure your process is producing high-quality outputs consistently.
Reduce Process Variation
One of the primary ways to improve process capability is to reduce the overall variation present in the process.
Process variation can be caused by several factors including raw material inconsistencies, equipment issues, environmental conditions, operator errors, and more.
By identifying and addressing the root causes of variation through root cause analysis training, you can tighten the process distribution and improve the Cp and Cpk values.
Common methods for reducing process variation include:
- Statistical Process Control (SPC) – Implementing SPC techniques like control charts can help you monitor the process in real time and quickly detect and address any shifts or instability.
- Mistake-Proofing – Poka-yoke or mistake-proofing devices and procedures can be put in place to prevent human errors and process defects.
- Preventive Maintenance – Regularly scheduled maintenance and calibration of equipment can help minimize variation caused by tool wear, drift, or malfunction.
- Six Sigma – Utilize the DMAIC (Define, Measure, Analyze, Improve, Control) Six Sigma methodology to systematically identify and eliminate sources of variation, which is thought through our Six Sigma certification programs.
Six Sigma certification helps professionals understand better the required concepts to reduce process variation and boost productivity.
Process Optimization
In addition to reducing variation, you can also work to optimize the process itself to improve capability. This may involve adjusting process parameters, updating equipment, changing raw materials, or redesigning the workflow.
Common optimization techniques include:
- Design of Experiments (DOE) – Systematically test different process variables to determine the optimal settings for maximum capability.
- Lean Manufacturing – Apply lean principles to eliminate waste, improve flow, and enhance overall process efficiency.
- Process Mapping – Create detailed process maps to visualize the workflow and identify opportunities for improvement.
- Automation – Automate manual, error-prone process steps to improve consistency and reduce human variation.
Ongoing Monitoring and Adjustment
Improving process capability is an ongoing effort that requires continuous monitoring, evaluation, and adjustment.
Even after making improvements, it’s important to regularly re-assess the Cp and Cpk values and make further refinements as needed.
Establish a cadence for capability studies, such as monthly or quarterly, to track trends over time. Continuously gather data, analyze process performance, and make incremental changes to sustain and enhance the process capability.
Remember, improving process capability is a journey, not a one-time event. By consistently applying these strategies and techniques, you can drive continuous improvement and ensure your processes are operating at peak efficiency and quality.
Case Studies and Examples of Process Capability Index (Cpk)
Now that we have a solid understanding of the process capability index, let’s look at some examples and case studies to see how it is applied in practice.
Process Capability in Manufacturing
One of the most common applications of process capability analysis is in manufacturing environments.
Let’s look at an example from an automotive parts manufacturer.
The company produces transmission gears that need to meet very tight dimensional tolerances. They conducted a process capability study on the gear production process and found that the Cpk value was only 0.82.
This indicated that the process was not capable of consistently producing gears within the required specification limits.
To improve the process capability, the company implemented the following steps:
- Analyzed the sources of process variation through a detailed FMEA (Failure Mode and Effects Analysis).
- Made adjustments to the machinery and tooling to reduce variation.
- Implemented statistical process control (SPC) to monitor the process on an ongoing basis.
- Provided additional training to machine operators on process control techniques.
After these improvements, the company was able to achieve a Cpk value of 1.21, indicating a highly capable process that could reliably meet the tight tolerance requirements.
Lead process improvement initiatives and implement advanced statistical techniques like Cp and Cpk with our Lean Six Sigma Green Belt course and manage complex projects using a wide range of process improvement tools.
Process Capability in Software Development
Process capability analysis is not limited to just manufacturing – it can be applied to any repeatable process.
For example, let’s look at how a software development team used process capability to improve their development lifecycle.
The team was tasked with developing a new customer-facing web application. They defined key quality metrics such as defects per thousand lines of code and on-time delivery.
A process capability study revealed that their current development process had a Cpk of only 0.78 for these metrics.
To improve, the team implemented the following changes:
- Adopted Agile development practices to increase process visibility and responsiveness.
- Automated unit and integration testing to catch defects earlier.
- Implemented Kanban boards to better manage workflow and reduce work-in-progress.
- Provided training to developers on coding best practices and process improvement techniques.
After 6 months, the team’s process capability study showed a Cpk of 1.15 for their key metrics, indicating a significant improvement in their development process.
These examples illustrate how process capability analysis can be used in both manufacturing and service-based environments to identify opportunities for improvement and drive measurable results.
SixSigma.us offers both Live Virtual classes as well as Online Self-Paced training. Most option includes access to the same great Master Black Belt instructors that teach our World Class in-person sessions. Sign-up today!
Virtual Classroom Training Programs Self-Paced Online Training Programs