Understanding, Analyzing, and Controlling Common Cause Variation
The pursuit of consistency is fundamental to operational success, yet variability seems unavoidable due to the nature of people, processes, and work environments.
While random fluctuations are expected in any system, too much variability negatively impacts an organization’s quality, productivity, and ability to meet customer demands.
Understanding common cause variation and implementing strategies to monitor and minimize its effects is therefore critical for organizations seeking continuous improvement.
Turn complex process variations into strategic improvements
Become the expert who drives operational excellence with Lean Six Sigma Green Belt Certification.
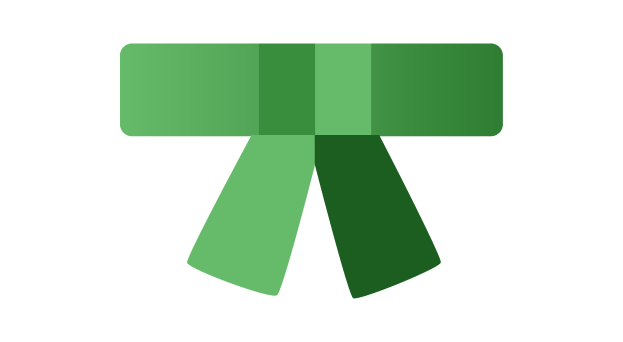
Common cause variation refers to random, natural variation inherent in stable processes. Unlike fluctuations from unstable processes or changes in inputs, common cause variation originates from factors within the system itself that interact randomly but predictably.
For example, common causes could include minor differences in environmental conditions, raw materials, or operator technique.
Equipped with methods to interpret process metrics and address root causes, professionals can transform obstacles into opportunities to better meet specifications.
What is Common Cause Variation?
Common cause variation refers to the natural or random variability inherent in any stable process. Unlike unpredictable changes from external factors, common cause variation originates from ever-present differences within the process itself that interact to produce measurable fluctuation.
In statistical process control (SPC), common cause variation manifests on control charts as random oscillation within the statistically calculated upper and lower control limits.
Points falling outside control limits or displaying non-random patterns indicate special cause variation from unstable inputs.
Properly interpreting control charts enables professionals to distinguish between the two and determine appropriate actions.
For example, minor disparities in environmental humidity each day may lead to subtle variations in a chemical process’s yield.
As long as temperatures remain in an expected range per the control chart, reacting to daily swings overcorrects the natural variability.
Confusing special and common causes can lead to overadjusting a statistically stable process, known as tampering. This often inadvertently increases variation instead of improving consistency.
Understanding common causes empowers organizations to quantify normal variation’s impact on meeting quality or productivity specifications.
While complete elimination of fluctuation may not be feasible or economical, monitoring metrics over time helps identify causes to address at a root level.
We will explore analytical strategies to control variability while avoiding overreaction. First, properly differentiating between the types of variation provides crucial context.
Importance of Understanding Common Cause Variation
Grasping the implications of common cause variation is vital for organizations seeking sustainable growth. Fluctuations within an expected range seem harmless on the surface.
However, failing to monitor and interpret process variability can significantly hinder quality, efficiency, and workplace culture over time.
Impact on Organizational Performance
Productivity
While complete elimination of common cause variation may not be feasible, excessive fluctuation directly reduces output and value delivery.
For example, order processing time could vary from 5 – 15 minutes. If the upper control limit reaches 20 minutes, customer wait times extend, costs per order climb, and less gets accomplished per employee.
Quality
High variability also jeopardizes quality, disproportionately increasing defects and rework.
In software testing, random differences in QA engineer diligence could lead to sporadic release defects despite other stable inputs.
Monitoring variability triggers reviewing inspection procedures before poor quality becomes rampant.
Employee Morale
Additionally, high common cause variation strains employees. Operators feel helpless to control seemingly random workflow disruption.
Volatility with no known cause exacerbates stress and prompts overreactions. Data-driven variability analysis prevents jumping to faulty conclusions while calming fears of lurking problems.
Statistical thinking reveals that no process is perfect.
There will always be some common cause. However, armed with methods to distinguish between inherent and unstable variation, organizations can determine optimal levels per their objectives.
Strategies for Managing Variability
While complete elimination of common cause fluctuation is often impractical, organizations can implement methods to control variability to optimal levels that meet specifications. Strategies include real-time monitoring, defining internal metrics, and leveraging employee perspectives to address root causes.
Statistical Process Control
Statistical process control (SPC) utilizes data visualization tools such as control charts to dynamically track fluctuation and distinguish between common and special cause variations.
Control limits mathematically set using standard deviations alert analysts to points indicating instability.
This prevents tampering with stable processes while rapidly detecting signals of unexpected change needing intervention.
Setting Metrics & Monitoring
Additionally, clearly defining internal key process indicators and customer requirements enables variability analysis relative to measurable targets, not just statistical control.
Does the current process spread meet benchmark defect rates? Does delivery time deviation still meet on-time shipment SLAs?
Monitoring quantifies the capability to stay within acceptable parameters.
Employee Involvement
Finally, engaging cross-functional teams in examining metrics uncovers hidden factors driving common cause variation.
Operators comprehend nuances and limitations of equipment, while process architects map variability’s ripple effect on downstream processes. Inclusion breeds employee ownership of solutions tailored to local conditions.
Combined, these interlocking efforts provide organizations with enduring mechanisms to track, assess, and address the impacts of common cause variation using data instead of assumptions.
Analyzing Common Cause Variation
Interpreting process data enables fact-based variability analysis.
Statistical process control (SPC) provides techniques to distinguish between stable and unstable fluctuation as well as assess capability relative to specifications.
Statistical Process Control (SPC) Charts
SPC control charts graphically display metrics over time, triggering signals when points stray outside statistically expected variation.
By visually separating normal and abnormal shifts, teams avoid tampering with stable processes while rapidly detecting signals needing intervention.
Learn to decode complex process signals and drive breakthrough improvements
Elevate your analytical skills to world-class performance levels with Lean Six Sigma Black Belt Certification.
Types of Charts
There are specific control chart types matching discrete, continuous, or count data. X-bar and R-charts work for continuous measurements, while p-charts monitor attribute data.
Correctly matching analysis methods to data ensures statistical significance.
Control Limits
Control limits are mathematically calculated from historical data using standard deviations to plot upper and lower boundaries.
Control limits only have meaning relative to points calculated from the same process under similar conditions. Comparing across processes risks false signals.
Process Capability Analysis
While control charts evaluate stability, capability analysis examines if current variation can meet requirements.
Simple visual tools like process capability indices quantify the ability to meet engineering tolerances. This prevents over-controlling a statistically stable process that simply needs redesigning.
In addition to control chart signals, regularly assessing process metrics against targets highlights control gaps. This informs improvement prioritization based on specifications, not just statistical control.
Detecting & Analyzing Variation
The visual nature of SPC control charts empowers rapid interpretation of common cause vs special cause variation.
By encoding complex statistical calculations into graphical data points assessed against control limits, patterns clearly emerge to inform the next steps.
Visual Representation of Data
Control charts provide an intuitive format to instantly signal exceptional values compared to the mathematically expected range per the process.
This prevents relying on gut intuition that risks tampering with stable processes. Outlier points stand out visually for further investigation into assignable causes.
Finding Trends & Patterns
Additionally, annotated charts allow analysts to highlight trends over time and call attention to non-random patterns that suggest special causes.
This contrasts with inherent point oscillation from common cause variation that appears randomly distributed.
Assessing Process Stability
Finally, control charts quantitatively assess process stability. Control limits based on standard deviations of historical data define the expected pattern for variation.
Pending no signals points landing inside thresholds indicate statistically steady performance to compare against requirements.
Application of SPC Charts
Manufacturing Quality – Control charts plotting defect rates over time signal rising scrap counts. This prompts analysis into causes before failures cascade. Investigation reveals that worn tooling increases inherent machine variability. Proactive retooling reduces defect rate variability by 30%.
Call Center Staffing – An X-bar chart tracking call handle time detects no out-of-control signals. However, high common cause variation leads to frequent service level breaches. Optimizing staff coverage to account for handling time volatility maintains SLAs.
Equipped to distinguish between types of variation and paired with running capability analysis, control charts provide simple yet powerful visibility to drive data-based variability reduction.
Real-World Examples
Understanding the theory around common cause is helpful, but seeing variability analysis applied to real-world scenarios cements comprehension.
Let’s examine a case study demonstrating how manufacturing plants in particular leverage statistical thinking to improve quality and efficiency.
Case Study 1 – Manufacturing Industry
Due to the interconnected nature of machinery, materials, and human involvement, manufacturing processes inevitably experience innate variation even in stable environments.
Monitoring and controlling common cause fluctuation then becomes pivotal.
Assembly Lines
Take for example an automotive assembly line. Production output inherently varies based on minor differences in equipment wear, material thickness, and operator attention.
Statistical control charts help quantify expected whip-in finished door fits and finishes over time.
Quality Control
Resulting visibility quickly alerts quality technicians to panels veering out of specification so that root cause investigation occurs before downstream defects multiply.
Maintaining station-level control charts also reveals whether variation falls within stable, expected bands.
Defect Prevention
Armed with real-time quality measures, engineers proactively address common causes like jig wear before high volatility requires reworking costly assemblies.
Statistical thinking prevents overadjusting stable processes, instead indicating when fundamental improvements pay off. This shifts efforts upstream to prevent defects at their root.
Manufacturing processes rich with variability sources hugely benefit from Canalysis to guide incremental and breakthrough changes.
Case Study 2 – Service Sector
Like manufacturing, services also endure innate variability from environmental factors, employees, and customer differences that require monitoring and control.
Restaurants
In restaurant kitchens, order preparation time fluctuates based on complexity, equipment functionality, and chef diligence.
Control charts help set customer wait time expectations by revealing stable process bandwidth. Slow service alerts owners toList troubleshoot delays before customers notice.
Call Centers
Call center metrics also vary given representative ability, question types, and call complexity. Tracking handle time variability ensures adequate staffing to meet service level agreements during peaks.
This prevents long hold times despite the average pace of meeting targets.
Hospitality
Finally, factors like room layouts, guest preferences, and housekeeper techniques mean inevitable variations in hotel room cleaning times.
Common cause analysis gives managers expected turnaround ranges to optimize checkout and check-in scheduling.
Across industries, no process demonstrates perfect consistency due to common causes.
Statistically monitoring key indicators lights the path to excellence by exposing opportunities amidst complexity and chaos.
Continual Improvement Framework
SPC control charts, analytical problem-solving methods, and variability reduction techniques combine to create an iterative improvement framework based on objective data.
This sustains incremental gains over time vs short-lived gains from reactionary interventions or assumptions.
Importance of Addressing Variation
Higher Consistency
Addressing special causes when indicated and optimizing controllers for minimal common cause fluctuation directly translates to more uniform output.
This tightens specifications, prevents overprocessing, and stabilizes cycle times.
Less Waste
In addition, tampering with stable processes generates unnecessary adjustments and activity. Eliminating this from misreading variation reduces wasteful effort, freeing capacity for value.
Standardizing chaos invites failure demand.
Improved Performance
Perhaps most powerfully, statistically managing operations grants permission for cultural change by creating urgency to engage frontline teams.
Making data-driven decisions grows capabilities organization-wide.
This evolves mindsets to prevent reactionary changes, instead leveraging facts for continual improvement at pace and scale.
Implementing Strategies
Enabled by technology infrastructure to automate data acquisition, three primary elements ensure analyzing common causes drives enduring positive trajectory:
Data Collection Systems
Effective analysis requires timely metrics indicative of process stability and sources of variation. IoT sensors and database integrations provide a steady stream of leading and lagging indicators to populate analytical tools.
Employee Involvement
Engaging teams throughout data interpretation and solution development uncovers hidden variables while fostering buy-in to drive adoption. Shop floor insights explain pattern causes and guide practical solutions.
Ongoing Monitoring & Measurement
Finally, consistent monitoring against quantifiable targets maintains vigilance, providing feedback loops to institutionalize gains. Control dashboards make signals visible across dispersed facilities. Complacency risk means a permanent measurement mindset.
Best Practices
Based on the key lessons around understanding, analyzing, and controlling common cause variation, here are best practices to drive continual improvement:
Adopt Statistical Thinking
Cultivate data-driven decision-making and statistical perspectives recognizing inherent process variability. Move from reactive to proactive mindsets leveraging analytics.
Implement Real-Time Monitoring
Utilize control charts and dashboards to monitor metrics. Visually detecting signals and trends provides objective flags for change vs tampering with stable processes.
Perform Root Cause Analysis
Investigate signals and patterns to address special cause variation at its source for sustainable change. Understand impacts across interconnected processes.
Optimize Stable Processes
Improve components driving common cause variation to “shrink the bandwidth” after ensuring stability. This prevents chasing phantom problems while driving up capability.
Continually Refine Targets
Get comfortable with gradual ratcheting of benchmarks in quality and efficiency KPIs to stretch performance. Meet increasingly stringent goals via analytics.
Equipped to interpret data, confront tough questions, and improve holistically, professionals transform common causes into uncommon competitive separation through people, processes, and technology.
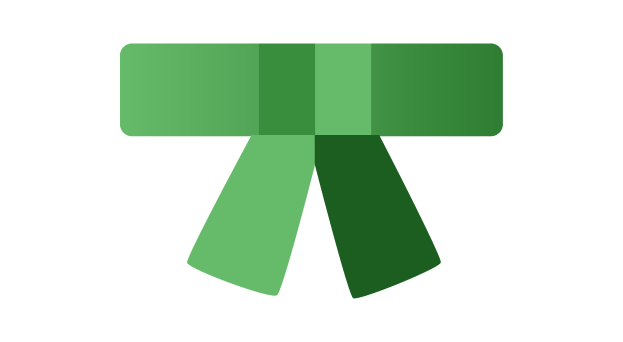
Transform your organization with fact-based improvement strategies
Unlock the power of statistical thinking and process improvement Lean Six Sigma Green Belt Certification.
Key Takeaways
This exploration of common cause variation aimed to progress readers along the journey of statistical thinking to drive data-based operational excellence.
In a nutshell:
- Common cause variation is natural randomness indistinguishable from noise that demands analytical interpretation.
- Monitoring metrics over time enables fact-based, not reactive, decisions aligning changes with business objectives.
- Control charts provide visual boundary guidance to signal exceptional values from expected variability.
- Addressing root causes proactively, even small ones, prevents volatility from cascading into major issues.
- Incrementally optimizing stable processes compounded over time yields significant performance gains.
Process variability frequently paralyzes progress by breeding misguided firefighting.
But armed with statistical thinking to confront the complexities, professionals transform obstacles into opportunities to deliver consistent value.
What meaningful measure will you monitor and improve tomorrow?
SixSigma.us offers both Live Virtual classes as well as Online Self-Paced training. Most option includes access to the same great Master Black Belt instructors that teach our World Class in-person sessions. Sign-up today!
Virtual Classroom Training Programs Self-Paced Online Training Programs