How to Improve Process Efficiency? Strategies, Tools, and Best Practices
The competition is fiercer than ever, so organizations are looking for ways to win. Process efficiency plays a critical role in a company’s success.
Process efficiency lies at the heart of operational excellence, influencing productivity, cost-effectiveness, customer satisfaction, and, profitability.
Transform your organization’s operational performance through proven waste elimination techniques
Learn the core principles that drive continuous improvement and competitive advantage with Lean Fundamentals.
By streamlining processes and eliminating waste, businesses can unlock untapped potential, speed up growth, and establish a sustainable competitive advantage.
Key Highlights
- Process efficiency is a critical aspect that can impact a company’s bottom line, productivity, cost-effectiveness, customer satisfaction, and competitive advantage.
- It involves streamlining processes, eliminating waste, and optimizing resources.
- Benefits of efficient processes include increased productivity, cost savings, improved customer satisfaction, and a sustainable competitive edge.
- Types of process efficiency include efficiency, labor productivity, throughput, and resource efficiency.
We will explore process efficiency definitions, benefits, types, and the strategies necessary to achieve operational excellence.
Understanding Process Efficiency
Process efficiency is a measure of how a business utilizes its resources, including time, effort, and capital, to achieve desired outcomes.
An efficient process maximizes output while minimizing resource consumption, eliminating waste, and optimizing workflow. Analyzes how much output a process produces compared to the inputs it requires.
Methodologies like Six Sigma and Lean provide structured frameworks for achieving this efficiency, and professionals can enhance their ability to implement these approaches through six sigma certification.
Benefits of Efficient Processes
The pursuit of process efficiency is not merely a theoretical exercise; it yields tangible and far-reaching benefits for organizations. By optimizing processes, businesses can experience:
- Increased Productivity: Efficient processes eliminate unnecessary steps, redundancies, and bottlenecks, allowing employees to focus their efforts on value-adding activities. This, in turn, leads to higher output and improved overall productivity.
- Cost Savings: Streamlined processes reduce waste, minimize errors, and optimize resource utilization, resulting in significant cost savings. These savings can be reinvested into growth initiatives, research, and development, or passed on to customers through competitive pricing.
- Improved Customer Satisfaction: Efficient processes enable organizations to deliver products or services faster, with higher quality, and fewer errors. This enhanced customer experience translates into increased satisfaction, loyalty, and positive word-of-mouth, all of which contribute to a stronger brand reputation and market position.
- Competitive Advantage: Efficiency can be the differentiating factor that sets an organization apart from its competitors. By continuously refining and optimizing processes, businesses can gain a sustainable competitive edge.
Types of Process Efficiency
Process efficiency encompasses various aspects of an organization’s operations. To understand and measure efficiency holistically, it is crucial to recognize the different types of process efficiency:
- Overall Efficiency: This metric evaluates the overall performance of a process by comparing the total output generated to the total inputs consumed. It provides a comprehensive view of the process’s effectiveness and helps identify areas for improvement.
- Labor Productivity: Labor productivity measures the output generated per unit of labor input, such as the value of products or services produced per hour worked. Improving labor productivity is essential for optimizing resource utilization and maximizing workforce efficiency.
- Throughput: Throughput refers to the rate at which a process generates output over a given period. It is a crucial metric for production environments, where maximizing throughput while maintaining quality standards is a key objective.
- Resource Efficiency: Resource efficiency focuses on the optimal utilization of raw materials, energy, and other resources required for production or service delivery. By minimizing waste and maximizing resource utilization, organizations can reduce costs and minimize their environmental impact.
By understanding and measuring these different types of process efficiency, businesses can pinpoint specific areas for improvement and implement targeted strategies to achieve operational excellence.
Identifying and Addressing Inefficient Processes
While the pursuit of process efficiency is laudable, the reality is that many organizations grapple with inefficient processes that hinder their growth and competitiveness.
Identifying and addressing these inefficiencies is a crucial first step toward achieving operational excellence.
Common Causes of Inefficient Processes
Inefficient processes can stem from a variety of factors, and recognizing these underlying causes is essential for effective remediation.
Some of the most common culprits include:
Lack of Skills
Inadequate training or a skills gap among employees can lead to inefficient execution of processes. Employees may struggle to understand or follow established procedures, resulting in errors, rework, and wasted time and resources.
Addressing this through targeted training, such as six sigma certification, can equip employees with the methodologies needed to improve process execution.
Poor Documentation
Poorly documented processes can breed confusion, miscommunication, and inconsistencies in execution. Without clear and up-to-date documentation, employees may rely on outdated or inaccurate information, leading to deviations from best practices and inefficiencies.
Shadow Processes
In organizations with gaps or outdated bureaucracy, employees may develop their informal processes, known as “shadow processes“, to circumvent perceived roadblocks. While well-intentioned, these shadow processes can introduce inefficiencies, conflicts, and risks to the organization.
Lack of Common Terminology
Inconsistent use of terminology across departments or teams can lead to misunderstandings and miscommunication, hampering process efficiency. Establishing a shared vocabulary and clear definitions is crucial for seamless collaboration and effective execution.
Process Mapping and Analysis Techniques
To identify and address inefficiencies, organizations must first gain a comprehensive understanding of their processes. This is where process mapping and analysis techniques come into play.
Some of the most effective tools in this domain include:
Process Mapping
Visually representing the sequence of activities, decisions, and handoffs within a process through flowcharts, swimlane diagrams, or other visual aids.
Process mapping provides a clear picture of the current state, enabling organizations to identify redundancies, bottlenecks, and opportunities for improvement.
Value Stream Mapping (VSM)
A lean methodology that maps the end-to-end flow of materials and information required to deliver a product or service to the customer. VSM helps organizations identify and eliminate non-value-added activities, reducing waste and improving efficiency.
Root Cause Analysis (RCA)
A structured approach to identifying the underlying causes of problems or inefficiencies. By understanding the root causes, organizations can develop targeted solutions that address the fundamental issues rather than treating symptoms.
Professionals can enhance their ability to perform this analysis effectively with root cause analysis training, which provides specialized techniques and tools.
Bottleneck Analysis
A technique for identifying and resolving constraints or bottlenecks that limit the overall capacity or throughput of a process. By alleviating bottlenecks, organizations can improve process flow, reduce cycle times, and enhance efficiency.
Uncover Hidden Process Inefficiencies with Root Cause Analysis Training
Develop advanced diagnostic skills to identify and eliminate process bottlenecks.
Key Performance Indicators (KPIs) for Measuring Process Efficiency
Measuring process efficiency is crucial for tracking progress, identifying areas for improvement, and making data-driven decisions.
Key Performance Indicators (KPIs) serve as quantifiable metrics that provide insights into the efficiency and effectiveness of processes.
Some commonly used KPIs for measuring process efficiency include:
- Cycle Time: The total time required to complete a process from start to finish, including any delays or waiting periods. Shorter cycle times generally indicate higher efficiency.
- Throughput: The rate at which a process generates output or completes transactions over a given period. Higher throughput typically signifies greater efficiency, provided quality standards are maintained.
- First-Pass Yield: The percentage of units or transactions that complete the process correctly on the first attempt, without requiring rework or correction. A higher first-pass yield indicates fewer inefficiencies and errors.
- Cost per Unit: The total cost associated with producing a single unit of output, including labor, materials, and overhead. Lower cost per unit can be an indicator of improved process efficiency.
- Customer Satisfaction: While not directly measuring process efficiency, customer satisfaction can serve as a proxy for understanding the effectiveness of processes and identifying areas for improvement.
By establishing relevant KPIs and consistently monitoring them, organizations can gain valuable insights into their process efficiency, enabling data-driven decision-making and targeted improvement efforts.
Strategies for Improving Process Efficiency
Having identified the root causes of inefficiencies and established a robust framework for measuring process performance, the next crucial step is to implement strategies that drive sustainable improvements.
Process Improvement Methodologies
Organizations can leverage a variety of well-established process improvement methodologies to drive efficiency and operational excellence.
Lean Manufacturing
Originating in the automotive industry, lean manufacturing focuses on eliminating waste and non-value-added activities to streamline processes.
By identifying and addressing sources of waste, such as overproduction, waiting times, transportation, and defects, lean principles enable organizations to optimize resource utilization and enhance efficiency.
For those new to these concepts, a lean introduction course can provide a solid foundation in waste elimination and process optimization.
Six Sigma
A data-driven methodology that emphasizes the reduction of process variation and defects, Six Sigma employs a structured approach known as DMAIC (Define, Measure, Analyze, Improve, Control).
By leveraging statistical analysis and root cause identification, Six Sigma initiatives can significantly improve process consistency, quality, and efficiency.
Kaizen
Rooted in the Japanese philosophy of continuous improvement, Kaizen encourages organizations to embrace a mindset of incremental, ongoing changes.
Through a culture of collaboration, employee empowerment, and a relentless pursuit of perfection, Kaizen drives small but consistent improvements that collectively yield substantial efficiency gains.
Business Process Reengineering (BPR)
In some cases, organizations may need to undertake a more radical transformation of their processes. BPR involves fundamentally rethinking and redesigning processes from the ground up, rather than making incremental improvements.
This approach can be particularly effective when existing processes are outdated or no longer aligned with organizational goals.
Workflow Automation and Process Optimization Tools
In addition to leveraging proven methodologies, organizations can harness the power of technology to streamline and optimize their processes. Workflow automation and process optimization tools offer a range of capabilities that can significantly enhance efficiency:
- Business Process Management (BPM) Software: BPM solutions enable organizations to model, automate, and continuously optimize their processes. These tools provide visibility into process flows, facilitate collaboration, and automate repetitive tasks, reducing manual effort and minimizing errors.
- Robotic Process Automation (RPA): RPA technology uses software robots or “bots” to automate repetitive, rule-based tasks that were previously performed manually.
- Process Mining and Analytics: Process mining tools leverage data from information systems to provide insights into how processes are executed.
- Workflow Management Systems: Designed to automate and streamline workflows, these systems enable organizations to define, execute, and monitor processes across various departments and teams.
Change Management and Digital Adoption
While implementing new methodologies and tools is crucial, successful process improvement initiatives also require effective change management and digital adoption strategies.
Resistance to change and lack of user adoption can undermine even the most well-designed processes and technologies. To overcome these challenges, organizations should:
Leverage Digital Adoption Platforms (DAPs)
DAPs provide in-app guidance, contextual walkthroughs, and training materials directly within the software interfaces employees use daily.
By embedding learning and support resources into the workflow, DAPs can accelerate user adoption, minimize disruptions, and ensure seamless transitions to new processes and technologies.
Employ Change Management Models
Proven change management models, such as Kotter’s 8-Step Process, ADKAR, or the Prosci ADKAR Model, offer structured approaches to managing the people side of change.
These models guide organizations through stages like creating a sense of urgency, building coalitions, empowering employees, and sustaining change, ensuring successful transformation initiatives.
Foster a Culture of Continuous Improvement
Beyond implementing specific methodologies or tools, organizations should cultivate a mindset of continuous improvement.
By encouraging employee participation, recognizing achievements, and providing ongoing training and support, businesses can create an environment where process optimization becomes an integral part of the organizational culture.
By combining proven process improvement methodologies, leveraging workflow automation and optimization tools, and implementing effective change management and digital adoption strategies, organizations can unlock the full potential of process efficiency.
Implementing and Monitoring Process Efficiency Improvements
Having explored the strategies and approaches for enhancing process efficiency, we now turn our attention to the crucial phase of implementation and ongoing monitoring.
Communicating and Training for Process Changes
Effective communication and training are essential components of any successful process improvement initiative.
Failure to adequately prepare and equip stakeholders can lead to resistance, confusion, and suboptimal adoption, undermining the intended benefits of the changes. To ensure a smooth transition and maximize the impact of process improvements, organizations should:
- Develop a comprehensive communication plan: Clearly articulate the rationale, goals, and expected outcomes of the process changes to all affected stakeholders, including employees, customers, and suppliers.
- Involve stakeholders early: Engage key stakeholders throughout the process improvement journey, soliciting their input, addressing concerns, and fostering a sense of ownership.
- Provide comprehensive training: Implement a robust training program that equips employees with the knowledge and skills necessary to navigate the new processes effectively.
- Assign process champions: Identify and empower process champions within the organization – individuals who can serve as advocates, mentors, and subject matter experts for the new processes.
By prioritizing clear communication and comprehensive training, organizations can overcome resistance, foster understanding, and equip their workforce with the tools and knowledge necessary to successfully embrace and implement process improvements.
Continuous Improvement and Process Monitoring
Process improvement is not a one-time endeavor but rather an ongoing journey.
To maintain operational excellence and ensure that processes remain efficient and aligned with organizational goals, a culture of continuous improvement and rigorous process monitoring must be cultivated.
This can be achieved through the following practices:
- Implement a structured approach, such as the Plan-Do-Check-Act (PDCA) cycle or the Kaizen methodology, to drive iterative improvements.
- Continuously collect and analyze data on key process performance indicators (KPIs), such as cycle time, throughput, defect rates, and customer satisfaction.
- Foster an environment where employees at all levels are empowered to identify opportunities for improvement and share their ideas and observations.
- Establish a cadence for comprehensive process reviews, involving cross-functional teams and subject matter experts.
With a mindset of continuous improvement and implementing robust process monitoring mechanisms, organizations can ensure that their processes remain agile, adaptable, and responsive to changing market conditions, customer demands, and technological advancements.
Quality Management Systems and Process Audits
To maintain the integrity and effectiveness of process improvements, organizations should leverage quality management systems and conduct regular process audits.
These practices provide a structured approach to monitoring, assessing, and refining processes, ensuring compliance with industry standards, regulatory requirements, and internal policies. Key considerations include:
- Implementing a Quality Management System (QMS): A QMS, such as ISO 9001, provides a framework for establishing, documenting, and maintaining an organization’s quality management processes.
- Conducting process audits: Regular audits of key processes are essential for identifying deviations, non-conformances, and opportunities for improvement.
- Utilizing audit findings: Audit findings should be thoroughly analyzed, and corrective and preventive actions should be implemented to address identified issues.
- Fostering a culture of quality: Cultivate an organizational culture that values quality and embraces the principles of continuous improvement.
By integrating quality management systems and conducting regular process audits, organizations can ensure that their processes remain efficient, compliant, and aligned with industry best practices, while continuously identifying and addressing areas for improvement.
Case Studies
Throughout my career as a Master Black Belt, I have had the privilege of working with numerous organizations across diverse industries, guiding them through transformative process improvement initiatives.
These experiences have provided invaluable insights into the challenges, strategies, and best practices that drive successful process efficiency efforts.
Success Stories from Companies That Improved Process Efficiency
Automotive Manufacturing Company:
One of the world’s leading automotive manufacturers recognized the need to streamline its supply chain processes to reduce costs and improve delivery times.
By implementing lean principles and value stream mapping, the company identified and eliminated non-value-added activities, optimized material flow, and enhanced supplier collaboration.
The result was a 25% reduction in inventory carrying costs, a 40% improvement in on-time delivery performance, and substantial savings in logistics expenses.
Healthcare Provider
A major healthcare system sought to enhance the efficiency of its patient admission and discharge processes, which had become plagued by bottlenecks, delays, and dissatisfied patients.
Through a combination of process mapping, root cause analysis, and workflow automation, the organization streamlined communication channels, eliminated redundant steps and integrated real-time bed availability tracking.
This comprehensive approach resulted in a 30% reduction in patient wait times, improved staff utilization, and significantly higher patient satisfaction scores.
Financial Services Firm
Recognizing the need to improve their account opening and onboarding processes, a prominent financial services firm embarked on a business process reengineering initiative.
By leveraging process mining techniques and customer journey mapping, the firm redesigned its processes from the ground up, eliminating redundancies, automating data entry tasks, and implementing digital signature capabilities.
The results were remarkable, with a 60% reduction in processing times, a 75% decrease in manual errors, and a substantial improvement in customer satisfaction metrics.
Retail Distribution Center
To address inefficiencies in its order fulfillment processes, a large retail distribution center implemented a comprehensive process improvement strategy.
This included the adoption of lean methodologies, the integration of warehouse management software, and the deployment of robotic process automation for repetitive tasks.
The outcome was a 40% increase in throughput, a significant reduction in order processing errors, and improved labor productivity, positioning the distribution center as a leader in its industry.
Lessons Learned and Best Practices
From these diverse success stories, several key lessons, and best practices emerge:
- Engage stakeholders early and often: Successful process improvement initiatives involve active collaboration with stakeholders from the outset, fostering buy-in, addressing concerns, and leveraging collective expertise.
- Adopt a data-driven approach: Leverage process mining, performance data, and analytics to gain comprehensive insights, identify improvement opportunities, and measure the impact of changes.
- Embrace a culture of continuous improvement: Foster an organizational mindset that encourages ongoing evaluation, experimentation, and refinement of processes to maintain operational excellence.
- Leverage technology as an enabler: Harness the power of workflow automation, process optimization tools, and digital adoption platforms to streamline processes, increase efficiency, and facilitate seamless transitions.
- Invest in training and change management: Effective communication, comprehensive training, and robust change management strategies are critical for ensuring successful adoption and sustained process improvements.
- Align with organizational goals: Ensure that process improvement initiatives are aligned with the overarching strategic objectives and priorities of the organization, delivering tangible value and competitive advantages.
By learning from these examples and embracing best practices, organizations can navigate the complexities of process improvement initiatives and unlock the full potential of operational excellence.
Lead Transformative Process Improvement Initiatives
Become the change agent your organization needs to achieve operational excellence with Lean Six Sigma Green Belt Certification.
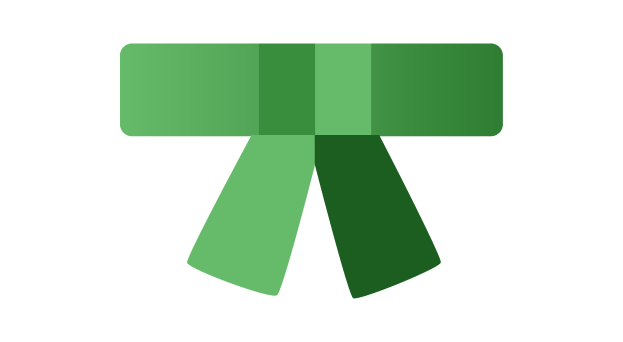
Future Trends and Innovations in Process Efficiency
As we look ahead, process efficiency is poised to grow rapidly, driven by upcoming technologies, shifting business paradigms, and a heightened emphasis on agility and adaptability.
Emerging Technologies and Automation
The rapid pace of technological advancement is opening up new frontiers in process efficiency. Several emerging technologies and automation solutions hold significant promise:
A suite of cutting-edge technologies is poised to revolutionize process efficiency in the coming years. Artificial intelligence and machine learning will leverage vast process data to identify patterns, predict issues, and prescribe optimizations.
The Internet of Things and sensor proliferation will provide real-time visibility into process performance across the value chain.
Next-generation robotic process automation will go beyond repetitive tasks by incorporating cognitive capabilities to handle complex processes and unstructured data dynamically.
Meanwhile, blockchain and distributed ledger technologies will ensure transparency, traceability, and trusted data sharing across multi-party processes.
By strategically integrating these emerging technologies, organizations can drive unprecedented levels of operational agility, optimization, and competitive advantage.
With the power of advanced analytics and performance metrics, organizations can gain unprecedented visibility into their processes, enabling them to continuously optimize, adapt, and drive operational excellence.
SixSigma.us offers both Live Virtual classes as well as Online Self-Paced training. Most option includes access to the same great Master Black Belt instructors that teach our World Class in-person sessions. Sign-up today!
Virtual Classroom Training Programs Self-Paced Online Training Programs