Kanban in Lean Manufacturing: A Comprehensive Guide
In lean manufacturing and constant upgrading, one method standing the test of time is Kanban. It streamlines workflows, cuts waste, and spreads an excellent spirit across diverse industries.
Kanban, meaning “visual signal” in Japanese, forms a core lean building block. Originating from Toyota’s production way guided by pioneering engineer Taiichi Ohno’s brilliance.
Kanban is a just-in-time production style emphasizing clear workflow control and is obsessed with eliminating waste.
By leveraging visual cues like Kanban cards and boards, this approach empowers groups regulating materials and info flows. It guarantees work progresses seamlessly from one stage to the next. Driven by real customer needs rather than predictions.
Key Highlights
- Understand the fundamental principles and practices that underpin the Kanban system.
- Discover the inner workings of a Kanban system, delving into the roles of Kanban cards, boards, and work-in-progress (WIP) limits.
- Explore the key elements that constitute a robust Kanban implementation.
- Gain insights into the practical steps involved in implementing Kanban for lean manufacturing, including creating workflow visualizations, defining work policies and standards, managing workflow and bottlenecks, and leveraging feedback loops for problem-solving.
- Understand the synergistic relationship between Kanban and other lean tools, such as 5S workplace organization, Total Productive Maintenance (TPM), Quick Changeover (SMED), and Value Stream Mapping.
- Explore the challenges and solutions associated with Kanban implementation, such as managing demand fluctuations, addressing quality and process reliability issues, navigating change management and training requirements, and integrating with suppliers and logistics.
- Discover strategies for fostering a culture of continuous improvement with Kanban, including lowering Kanban quantities over time, encouraging collaborative problem-solving, embracing experimentation and innovation, and building a robust kaizen culture
What is Kanban in Lean Manufacturing?
In lean manufacturing, the Kanban system stands as a beacon of efficiency, guiding organizations toward the coveted goals of waste reduction and continuous improvement.
As a just-in-time production system, Kanban exemplifies the core principles of lean by emphasizing visual workflow management and the relentless pursuit of eliminating waste in all its forms – muda (non-value-adding work), muri (overburden), and mura (unevenness).
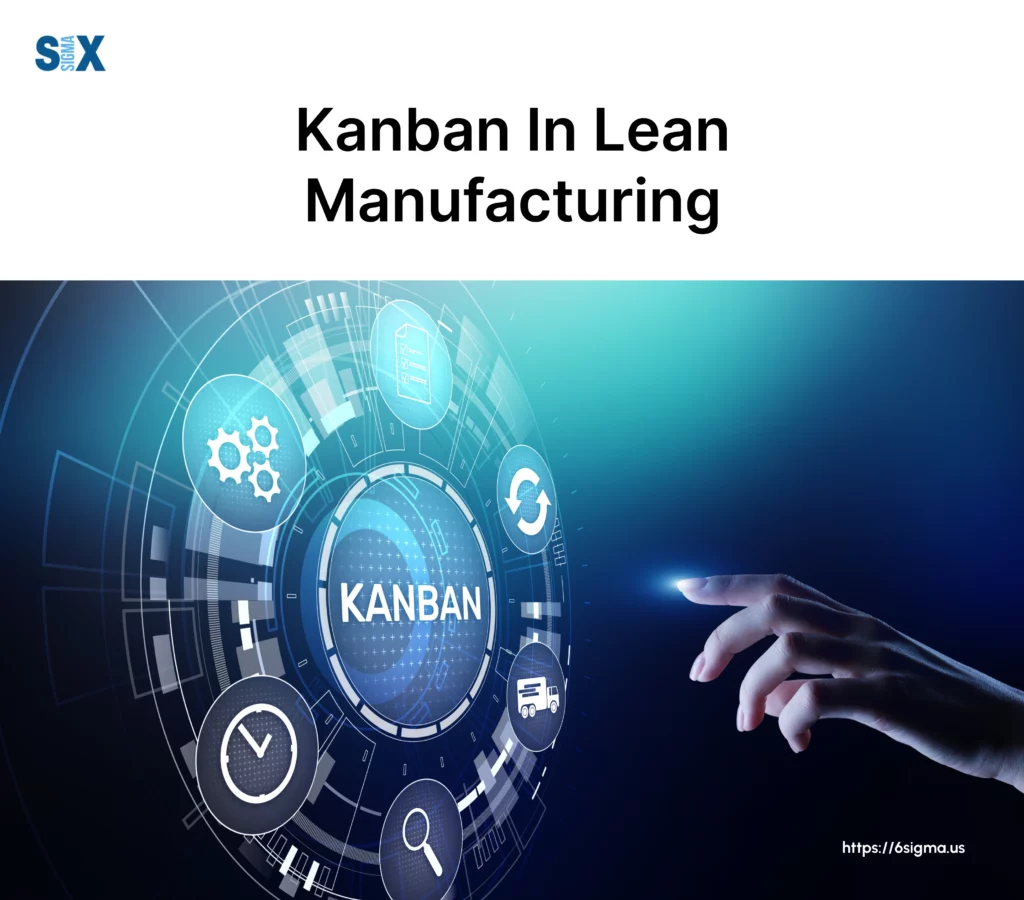
Kanban’s origins can be traced back to the ingenuity of the Toyota Production System, where Taiichi Ohno, a pioneering engineer, revolutionized the way we approach production processes.
Just-in-time production system
Kanban is a just-in-time (JIT) production system, where materials and components are produced and delivered precisely when needed, no sooner and no later.
This demand-driven approach eliminates the need for excessive inventory, reducing costs and freeing up valuable resources. By synchronizing production with customer demand, Kanban promotes the efficient use of resources and minimizes the risk of overproduction, a common pitfall in traditional manufacturing systems.
Visual workflow management
One of the hallmarks of the Kanban system is its emphasis on visual workflow management.
Using Kanban cards and boards, teams can visualize the flow of work, identify bottlenecks, and respond promptly to emerging challenges.
This visual representation fosters transparency, enhances communication, and empowers teams to make informed decisions, ultimately streamlining the entire production process.
Eliminate waste
Lean manufacturing is the relentless pursuit of eliminating waste, and Kanban is a powerful tool in this endeavor.
By addressing the three primary forms of waste – muda (non-value-adding work), muri (overburden), and mura (unevenness) – Kanban enables organizations to optimize their processes, reduce lead times, and enhance overall efficiency.
Whether it’s minimizing unnecessary movements, eliminating excess inventory, or smoothing out production flows, Kanban provides a systematic approach to identifying and eradicating waste, fostering a culture of continuous improvement.
Origins of Toyota Production System
The origins of Kanban can be traced back to the visionary Toyota Production System (TPS), which revolutionized the automotive industry with its lean manufacturing principles.
Developed by Taiichi Ohno and his colleagues at Toyota, Kanban was born out of the need to create a more efficient and responsive production system.
By introducing visual cues and limiting work-in-progress (WIP), Kanban enabled Toyota to streamline its operations, reduce waste, and respond swiftly to market demands, setting the stage for its global dominance in the automotive industry.
Kanban Principles and Practices
One of the guiding principles of Kanban is to start with the current processes in place. Rather than imposing drastic changes, Kanban encourages organizations to first understand and respect their existing workflows.
This approach minimizes disruption, fosters buy-in from employees, and allows for a smoother transition towards continuous improvement.
By starting with what is already familiar, teams can more easily identify areas for optimization and gradually implement improvements without causing unnecessary upheaval.
Incremental continuous improvement (kaizen)
Kanban embraces the philosophy of incremental continuous improvement, also known as kaizen.
Rather than pursuing radical, sweeping changes, Kanban advocates for a series of small, incremental steps that collectively lead to significant improvements over time.
This approach not only reduces resistance to change but also allows for a more sustainable and lasting transformation.
Respect existing roles and responsibilities
Effective implementation of Kanban requires respecting existing roles, responsibilities, and processes within an organization.
Rather than disrupting the established order, Kanban seeks to enhance and optimize what is already in place. This principle acknowledges the value of institutional knowledge and experience, recognizing that existing processes have evolved for valid reasons.
Leadership at all levels
Kanban empowers individuals at all levels of an organization to take ownership and demonstrate leadership in driving continuous improvement initiatives.
Rather than relying solely on top-down directives, Kanban encourages a bottom-up approach where employees at all levels are encouraged to identify areas for improvement, propose solutions, and actively participate in the implementation process.
This distributed leadership model not only fosters a sense of ownership and accountability but also taps into the collective expertise and insights of the entire workforce, creating a more engaged and motivated team.
How Does a Kanban System Work?
The Kanban system is an elegant yet powerful methodology that harnesses the power of visual cues and a demand-driven approach to streamline workflows and optimize production processes.
Kanban relies on a few key elements that work in harmony to create a lean, responsive, and efficient manufacturing environment.
Kanban cards/visual signals
Kanban cards, or visual signals, are the foundation of the Kanban system.
These simple yet effective tools represent individual work items or tasks, and their movement through the production process is tracked and controlled.
Kanban cards can take various forms, such as physical cards, digital representations, or even bins or containers, but their primary purpose is to provide a visual representation of the work in progress.
Kanban boards/visualization
Kanban boards are the visual backbone of the system, providing a comprehensive overview of the entire workflow.
These boards are typically divided into columns representing different stages of the production process, such as “To Do”, “In Progress”, and “Done”.
Kanban cards are placed in the appropriate columns, allowing teams to visualize the status of each work item and identify potential bottlenecks or areas for improvement.
Work in progress (WIP) limits
A key aspect of Kanban is the concept of work-in-progress (WIP) limits. These limits are set for each stage of the production process, ensuring that the amount of work flowing through the system is controlled and manageable.
By capping the number of Kanban cards allowed in each column, Kanban prevents overloading any particular stage, reduces the risk of bottlenecks, and promotes a smooth, uninterrupted flow of work.
WIP limits not only improve efficiency but also enhance quality by reducing the potential for errors and rework caused by multitasking or overburdening team members.
Pull production based on customer demand
Kanban is a pull-based system, meaning that production is driven by actual customer demand rather than forecasts or assumptions.
When a customer order is received, a Kanban card is introduced into the system, triggering the production of the required items.
This demand signal is then propagated upstream through the various stages of the production process, ensuring that each step receives the necessary materials and components just in time to fulfill the customer’s order.
Key Elements of Kanban
Production Kanban cards are the primary signals used to control the flow of materials and components through the manufacturing process.
These cards represent specific quantities of parts or assemblies that need to be produced, and they are typically attached to containers or bins that hold the physical items.
When a downstream process consumes the materials represented by a Production Kanban card, the card is returned to the upstream process, signaling the need for replenishment.
This continuous cycle of card movement and production ensures a consistent, demand-driven flow of materials throughout the value stream.
Transport/withdrawal of Kanban cards
In addition to Production Kanban cards, the Kanban system also employs Transport or Withdrawal Kanban cards.
These cards are used to initiate the movement of materials between different stages of the production process or between different locations.
When a process requires materials from a preceding stage, a Transport Kanban card is sent upstream, triggering the withdrawal and delivery of the necessary components.
This mechanism ensures that materials are available where and when they are needed, minimizing delays and fostering a smooth, uninterrupted flow of work.
Calculating kanban quantities
Determining the appropriate number of Kanban cards, and consequently the quantity of materials or components represented by each card, is a critical aspect of implementing an effective Kanban system.
The calculation typically involves factors such as daily demand, lead times, and safety stock levels.
By carefully balancing these variables, organizations can optimize inventory levels, minimize waste, and ensure a consistent and reliable supply of materials while maintaining the flexibility to respond to fluctuations in demand.
Inventory level management
Effective inventory management is a cornerstone of the Kanban system.
By closely monitoring and controlling the flow of materials through the production process, Kanban helps organizations maintain optimal inventory levels, reducing the risk of excess stock or stockouts.
This level of visibility and control not only improves operational efficiency but also enables organizations to make informed decisions about inventory management, such as setting appropriate reorder points, adjusting safety stock levels, or identifying opportunities for process improvements.
Implementing Kanban for Lean Manufacturing
Implementing the Kanban system in a lean manufacturing environment is a strategic endeavor that requires careful planning, execution, and ongoing monitoring.
While the principles of Kanban may seem straightforward, successful implementation relies on a systematic approach that addresses various aspects of the production process, from workflow visualization to continuous improvement.
Creating workflow visualizations
The first step in implementing Kanban for lean manufacturing is to create comprehensive workflow visualizations.
This involves mapping out the entire production process, identifying each stage, and representing it visually on a Kanban board or similar tool.
Defining work policies and standards
To ensure a successful Kanban implementation, it is essential to define clear work policies and standards.
These guidelines should cover areas such as quality criteria, priorities, due dates, and the criteria for moving work items from one stage to the next.
By establishing these policies and standards upfront, organizations can promote consistency, improve communication, and ensure that everyone involved in the production process is aligned with the same goals and expectations.
Managing workflow and bottlenecks
One of the key benefits of Kanban is its ability to identify and address bottlenecks in the production process.
By closely monitoring the flow of work and the status of Kanban cards on the board, teams can quickly identify areas where work is accumulating or stalling.
Proactive management of these bottlenecks is crucial to maintaining a smooth and efficient workflow. This may involve reallocating resources, implementing process improvements, or addressing underlying root causes that are hindering progress.
Feedback loops for problem-solving
Continuous improvement is a core principle of lean manufacturing, and Kanban provides a powerful mechanism for facilitating feedback loops and problem-solving.
By encouraging teams to report issues as soon as they arise, Kanban allows for immediate action to be taken to resolve problems and prevent them from escalating.
Regular retrospective meetings and feedback sessions enable teams to identify areas for improvement, analyze root causes, and implement corrective actions, fostering a culture of continuous learning and optimization.
Lean Tools With Kanban
While Kanban is a powerful tool for lean manufacturing, it is often most effective when combined with other lean principles and methodologies.
By integrating Kanban with complementary lean tools, organizations can achieve a more comprehensive and holistic approach to continuous improvement.
5S workplace organization
The 5S methodology – Sort, Set in Order, Shine, Standardize, and Sustain – is a foundational lean tool that complements the Kanban system by promoting a well-organized and efficient workplace.
By implementing 5S principles, organizations can create a visual workplace that supports the Kanban philosophy of transparency and visual management.
A well-organized environment not only enhances productivity and safety but also facilitates the smooth flow of materials and information, which is essential for the effective implementation of Kanban.
Total productive maintenance (TPM)
Total Productive Maintenance (TPM) is a lean tool focused on maximizing equipment effectiveness and reliability.
By implementing TPM practices, such as preventive maintenance, autonomous maintenance, and continuous improvement of equipment, organizations can reduce unplanned downtime, minimize defects, and increase overall equipment effectiveness (OEE).
TPM is particularly valuable when used in conjunction with Kanban, as it helps to ensure a consistent and reliable flow of materials through the production process.
Unreliable or frequently failing equipment can disrupt the smooth flow of Kanban cards and materials, leading to bottlenecks and inefficiencies.
Quick changeover (SMED)
Single-Minute Exchange of Die (SMED), or quick changeover, is a lean technique that focuses on reducing the time required to changeover or set up equipment for different product runs.
In many manufacturing environments, lengthy changeover times can lead to batch production, which can result in overproduction and excessive inventory.
By implementing SMED principles and streamlining changeover processes, organizations can reduce batch sizes, enabling a more frequent and responsive production flow that aligns with the principles of Kanban.
When combined with Kanban, SMED enables organizations to respond more rapidly to changes in customer demand, minimizing waste and promoting a truly demand-driven production system.
Value stream mapping
Value stream mapping is a lean tool that provides a comprehensive visualization of the entire value stream, from raw materials to the finished product in the hands of the customer.
By mapping the flow of materials and information, value stream mapping helps identify areas of waste, bottlenecks, and opportunities for improvement.
When used in conjunction with Kanban, value stream mapping can provide valuable insights into the overall production process, helping organizations optimize the placement of Kanban signals and identify potential areas for Kanban implementation.
Conclusion
Kanban represents a mindset shift empowering companies to cultivate a constantly upgrading culture. It nourishes a nimble attitude in navigating shifting customer needs and market moves.
We’ve seen how Kanban’s Toyota Production System origins established a revolutionary manufacturing outlook prioritizing waste removal. Also clear workflow control and chasing excellence relentlessly.
Kanban’s true strength lies in harnessing visual cues and needs-driven output. This synchronizes materials and info flows matching lean manufacturing’s just-in-time principles.
From cards and boards to limiting work-in-progress and pull systems, each element molds a seamless responsive production environment. It spreads visibility, teamwork, and an upgrading zeal.
Looking ahead, Kanban’s importance grows as it leapfrogs boundaries into other industries brilliantly. Its flexibility and versatility render it invaluable for handling modern manufacturing complexities while respecting lean thinking.
In parting, I encourage embracing Kanban’s transformative potential by leveraging principles and practices. Together let’s embark on constant improvement journeys, one card at a time. Witness profound impacts on our workplaces, teams, and the wider world.
SixSigma.us offers both Live Virtual classes as well as Online Self-Paced training. Most option includes access to the same great Master Black Belt instructors that teach our World Class in-person sessions. Sign-up today!
Virtual Classroom Training Programs Self-Paced Online Training Programs