Kanban Inventory Management in Lean Manufacturing. Everything to Know
Effective stock handling proves crucial for reducing costs while satisfying customers. Common methods yield excess, lengthened wait times, and inflated carrying fees.
Kanban presents a lean, visual alternative. Derived from Toyota Production Systems, the Japanese “signal card” optimizes materials and work-in-progress transparency across making.
Pull-based, it employs visual cues and cards regulating flows between steps. Implementing reveals bottlenecks, cuts lead times, and maintains optimal stocks through just-in-time manufacturing, continuous improvement, and waste reduction.
Built on the fundamentals of lean eliminating non-value and maximizing proficiency, Kanban visualizes processes end-to-end. Limiting concurrent jobs empowers identifying optimization avenues to savings and heightened satisfaction.
Accessible yet powerful, the system shepherds optimized materials through visible pull signals. Finished only as needed, work streams seamlessly toward refined perfection. All benefits as flexibility, quality, and affordability heighten in tandem for businesses and clientele alike.
Key Highlights
- Originating from Toyota’s Production System, Kanban streamlines material handling through visual signals. A pull-based system employing cards regulating flows between steps, it aims to streamline operations while slashing waste.
- At the core of Kanban lie lean principles like just-in-time making, continuous refinement, and optimizing stock levels. Visualizing processes end-to-end empowers identifying variances to remedy. Limiting concurrent jobs enhances the transparency of bottlenecks.
- Adopted across manufacturing, software development, and supply chains, Kanban proves a powerful yet accessible tool. Maintaining work-in-progress visibility and optimizing throughput, heightens quality, flexibility, and affordability.
- Businesses directly benefit as customer satisfaction rises in tandem. Less remains idle while more reaches clients precisely as demanded. With waste vanquished, every resource strengthens the value delivered through each link of the supply chain.
- A proven performer, Kanban consistently nurtures profitable prosperity by streamlining material flows and cultivating constant, considerate improvement wherever implemented. All progress as optional work dissolves and essential work shines.
What is Kanban Inventory Management?
Kanban emerged from Toyota’s renowned Production System, translated as “visual signal”. At its core, Kanban represents a pull-based philosophy regulating inventory via real demand, not forecasting.
In practice, work-in-progress and stock quantities remain strictly capped. Visual cues like Kanban cards initiate replenishment from upstream processes as the next step requires. This coordinated replenishment fosters efficient, uninterrupted flows.
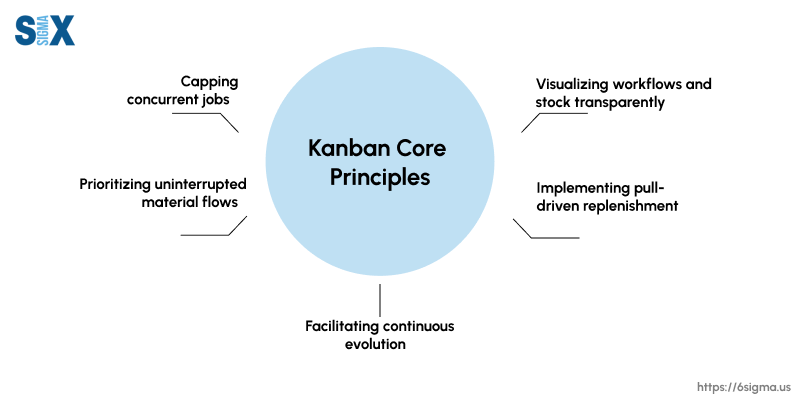
Several principles underpin Kanban’s efficacy:
- Visualizing workflows and stock transparently
- Capping concurrent jobs
- Prioritizing uninterrupted material flows
- Implementing pull-driven replenishment
- Facilitating continuous evolution
Adhering to these lean fundamentals, kanban eliminates excess, bottlenecks, and waste while satisfying customers promptly. Companies optimize stock levels, accelerate throughput, and increase responsiveness.
Accessible yet powerful, kanban’s regimented pull signals streamline operations sustainability. Visualized limits identify and remedy inefficiencies that burden output and inflate costs.
Businesses thrive with leaner, swifter operations guided by kanban’s problem-solving spirit.
How Kanban Works for Inventory Management
At its core, kanban is a pull system for inventory management. This means that production is driven by actual customer demand rather than forecasts or speculation. When a customer order is received, it triggers the replenishment of that inventory.
The kanban system uses visual signals, typically kanban cards, to indicate when more inventory needs to be ordered or produced.
These cards contain important information like part numbers, quantities, storage locations, etc. As inventory is consumed, the cards are transferred from the “completed” area of the kanban board back to the production queue as a signal to make more.
This creates a continuous flow where work is pulled through the system based on customer demand.
Work in progress (WIP) is capped at predetermined limits to avoid overproduction and optimize workflow. Bottlenecks become immediately visible so they can be addressed. Consider our root cause analysis training to equip your team with the skills to identify and eliminate the underlying causes of inefficiencies.
Kanban forces small batch sizes and frequent replenishment cycles. Inventory levels are kept as low as possible by only producing what is needed, when it’s needed.
This aligns inventory with actual consumption rates and eliminates waste from overproduction, excess storage, obsolescence, etc.
Suppliers are integrated into the Kanban loop as well. As materials are consumed, the supplier kanban cards are cycled back to trigger new material deliveries on a just-in-time basis.
This synchronizes the entire supply chain into a smooth, continuous flow.
Types of Kanban Systems
Several different types of kanban systems can be implemented for inventory management, depending on the specific needs and processes of an organization. The three main types are:
Production Kanban
The production kanban system is focused on the manufacturing process itself. It utilizes signal cards to trigger the movement or production of product components between work centers on the factory floor.
As demands from downstream processes are fulfilled, new kanban cards are issued to initiate replenishment of those components.
Withdrawal Kanban
The withdrawal kanban system is centered on inventory storage areas like warehouses. It uses cards to authorize the transfer (withdrawal) of materials from storage to the point of use or consumption.
When inventory is withdrawn, new cards are issued to signal replenishment orders to suppliers or upstream production processes.
Supplier Kanban
As the name implies, the supplier kanban system extends the pull mechanism beyond the factory to coordinate with external suppliers and vendors.
It allows manufacturers to streamline their supply chain by sending suppliers kanban cards that indicate future material requirements based on actual demand and consumption.
Within these three main kanban system types, there can be variations in the specific signaling devices used (e.g. cards, empty bins, electronic signals) and the logistics of how the loops are managed.
Some organizations also combine elements of the different kanban systems based on their unique needs.
The key principle in any Kanban inventory approach is to create a pull-based flow where work and movement of materials are driven by actual demand rather than forecasts or projections.
This reduces waste from overproduction while increasing inventory visibility and control.
Benefits of Kanban Inventory Management
One of the primary benefits of implementing a Kanban inventory management system is increased inventory visibility.
The visual nature of Kanban, with its signal cards and boards depicting workflow stages, allows you to see your inventory levels and stock positions at a glance.
This real-time visibility reduces the bullwhip effect and demand variability by providing an accurate view of what is truly needed.
Kanban leads to lower inventory carrying costs by promoting just-in-time production and pull-based flow.
Excess inventory is considered waste under lean principles. Kanban systems help optimize stock levels by linking customer demand to production and replenishment signals. This avoids costs from overproduction and excessive storage of inventory.
With its emphasis on continuous improvement, kanban facilitates process optimization by identifying bottlenecks, reducing lead times, and smoothing workflow.
Visual cues quickly reveal where work is piling up so countermeasures can be implemented. Over time, this incrementally streamlines processes and boosts throughput.
Kanban inventory management reduces waste through its visual workplace, pull system, and focus on flow. Stockouts, overproduction, excess motion, and waiting time are minimized. This waste reduction translates into cost savings and productivity gains.
The Kanban method improves supplier relationships by providing transparency into real consumption rates and inventory needs.
Suppliers can synchronize their production with your replenishment signals, avoiding shortages or excess inventory bloat in the supply chain.
Overall, the benefits of kanban for inventory management include increased visibility, lower carrying costs, process optimization, waste reduction, and improved supply chain collaboration – all key factors in achieving lean, just-in-time inventory control.
Implementing Kanban: A Step-by-Step Guide
Implementing a Kanban inventory management system requires careful planning and execution. Here’s a step-by-step guide to help you get started:
1. Map Your Workflow Stages
The first step is to identify and map out the different stages of your workflow or production process.
This could include stages like “raw materials,” “work in progress,” “finished goods,” and “shipment.” Visual signals (kanban cards) will be used to trigger the movement of inventory between these stages.
2. Determine WIP Limits
One of the key principles of kanban is limiting work in progress (WIP) to prevent bottlenecks and optimize workflow.
Determine the maximum WIP limits for each workflow stage based on factors like available capacity, lead times, and demand variability.
3. Design Your Kanban Cards/Signals
Kanban cards or signals are visual cues that authorize the movement of inventory. Design simple, easy-to-understand cards that contain relevant information like part numbers, quantities, and workflow stages.
4. Implement Pull System with Kanban Inventory System
In a Kanban pull system, downstream processes “pull” inventory from upstream processes based on demand. This helps minimize waste and overproduction.
Establish rules for how kanban cards will trigger replenishment or production.
5. Train Your Team
Ensure that all team members involved in the inventory management process understand the Kanban principles, visual signals, and standard operating procedures.
Proper training is crucial for successful kanban implementation.
Additionally, consider providing training in related methodologies; Our six sigma green belt certification program equips team members with skills to lead improvement projects effectively.
6. Start with a Pilot
Instead of implementing kanban across your entire operation, start with a pilot project in a specific area or product line.
This will allow you to test the system, identify potential issues, and make necessary adjustments before scaling up.
7. Continuously Improve
Kanban is built on the principle of continuous improvement (kaizen). Regularly review your Kanban system, gather feedback from team members, and make improvements to streamline processes, reduce waste, and enhance inventory visibility.
8. Integrate Technology
While kanban is a visual system, integrating technology like kanban software or inventory management tools can help you track inventory levels, analyze data, and optimize your kanban loop more effectively.
By following these steps, you can successfully implement a Kanban inventory management system tailored to your specific needs and requirements.
When to Use Kanban Inventory Management: Best Fit Scenarios
The Kanban inventory management system is well-suited for various scenarios and industries. Here are some of the best-fit scenarios where implementing a kanban system can be highly beneficial:
1. High-mix, Low-volume Production
Kanban is an excellent choice for businesses that produce a wide variety of products in smaller quantities.
This is because the Kanban system allows for flexibility and responsiveness to changing customer demands.
With visual signals and pull-based replenishment, businesses can quickly adapt to shifts in product mix without accumulating excessive inventory.
2. Repetitive Manufacturing with Kanban Inventory
Industries that involve repetitive manufacturing processes, such as automotive, electronics, or consumer goods, can greatly benefit from the kanban system.
The continuous flow of materials and the visual cues provided by kanban cards help streamline the production process, reducing waste and improving efficiency.
3. Lean Manufacturing Initiatives
Companies that have embraced lean manufacturing principles often adopt the kanban system as a key component of their lean initiatives.
Kanban aligns perfectly with lean principles like waste reduction, continuous improvement, and just-in-time production, making it an ideal fit for organizations pursuing lean transformation.
4. Complex Supply Chains
In industries with complex supply chains involving multiple suppliers and components, the Kanban system can help maintain inventory visibility and control.
By implementing supplier kanban and withdrawal kanban systems, companies can effectively manage the flow of materials and components from suppliers, reducing the risk of stockouts or excess inventory.
5. Seasonal or Fluctuating Demand with Kanban Inventory
Businesses that experience seasonal or fluctuating demand patterns can benefit from the flexibility of the Kanban system.
With its ability to quickly adjust stock levels and production rates, kanban allows companies to respond to changes in demand without carrying excessive inventory during low seasons or experiencing stockouts during peak periods.
6. Service Industries
While kanban originated in manufacturing, its principles can also be applied to service industries. Service providers, such as healthcare facilities, IT support companies or call centers, can use Kanban boards to visualize and manage their workflows, ensuring efficient resource allocation and timely service delivery.
It’s important to note that while kanban is a powerful inventory management system, its effectiveness depends on factors such as the nature of the business, the complexity of the supply chain, and the organization’s commitment to continuous improvement.
A thorough analysis of the company’s specific needs and processes is essential before implementing a kanban system.
Case Studies and Examples of Kanban Inventory Management
To better understand how kanban inventory management works in practice, let’s look at some real-world examples and case studies:
Toyota Motor Corporation
Toyota is widely credited with developing the kanban system as part of their legendary Toyota Production System (TPS).
The kanban approach to inventory control originated in Toyota’s manufacturing plants in the late 1940s as a way to create a more efficient “pull” system.
By using visual kanban cards to signal demand and trigger production, Toyota was able to minimize excess inventory and work-in-progress while maximizing just-in-time production.
This allowed Toyota to reduce waste, improve workflow, and respond quickly to changes in customer demand.
Eriks Inc.
Eriks is an industrial service provider that implemented a Kanban system across 60 distribution centers to better manage their inventory of maintenance, repair, and operation (MRO) supplies.
By using kanban cards and signals, Eriks was able to reduce inventory levels by 25% while still improving product availability.
Their kanban approach involved vendor-managed inventory where suppliers monitored kanban bins and replenished stock automatically based on actual usage and demand signals.
This eliminated the need for manual ordering and forecasting while optimizing inventory turns.
Sunshine Makers, Inc.
This California-based nutraceutical manufacturer struggled with excess work-in-progress inventory before adopting a kanban system.
By implementing Kanban pull signals between production stages, they were able to visualize and control WIP levels more effectively.
Sunshine Makers combined kanban with other lean manufacturing techniques like 5S workplace organization.
As a result, they reduced manufacturing lead times by 50% and achieved a 20% productivity improvement while cutting WIP inventory.
These examples from different industries highlight some of the powerful inventory management and operational benefits that a well-designed Kanban system can provide.
From automotive giants to smaller manufacturers, kanban has proven to be an effective approach for optimizing inventory levels.
Getting Ahead with Kanban Inventory System
Kanban is a powerful inventory management system that can help businesses streamline their operations, reduce waste, and improve efficiency.
By implementing visual signals, limiting work-in-progress, and embracing a pull system, companies can better align their production with actual demand, minimizing excess inventory and associated carrying costs.
While Kanban originated in the manufacturing sector, its principles can be applied to a wide range of industries, from healthcare to software development.
The key is to carefully analyze your workflow, identify bottlenecks and sources of waste, and design a Kanban system tailored to your specific needs.
As with any operational change, implementing Kanban requires commitment, training, and a culture of continuous improvement.
It’s essential to involve all stakeholders, from frontline workers to executives, in the process and provide ongoing support and coaching.
For companies looking to optimize their inventory management, Kanban offers a proven and flexible solution.
To take your process improvement efforts to the next level, explore our six sigma certification programs that can provide your team with advanced tools and methodologies.
By embracing lean principles, visual management, and a focus on customer demand, businesses can stay ahead of the competition and position themselves for long-term success in an ever-changing marketplace.
SixSigma.us offers both Live Virtual classes as well as Online Self-Paced training. Most option includes access to the same great Master Black Belt instructors that teach our World Class in-person sessions. Sign-up today!
Virtual Classroom Training Programs Self-Paced Online Training Programs