Jidoka – Toyota Production System. A Complete Guide (2024)
Jidoka, often referred to as “autonomation” or “intelligent automation,” is a fundamental principle of the renowned Toyota Production System (TPS) and a cornerstone of lean manufacturing.
This powerful quality control concept empowers workers to detect defects, stop production, and address quality issues immediately, rather than allowing problems to propagate through the manufacturing process.
Want to transform your understanding of operational excellence?
Discover the core principles that drive world-class manufacturing performance with Lean Fundamentals Certification.
Key Highlights
- Jidoka is a key principle of the Toyota Production System (TPS) and lean manufacturing
- It empowers workers to detect defects, stop production, and address quality issues
- The four core elements of Jidoka are: detecting abnormalities, stopping production, taking corrective actions, and preventing recurrence
- Jidoka utilizes automation, error-proofing, and operator empowerment to improve quality and efficiency
- Modern Jidoka integrates with technologies like IoT, AI, and data analytics for enhanced quality control
- Implementing Jidoka effectively requires management commitment, communication, and a step-by-step approach
- Jidoka delivers benefits such as improved product quality, increased productivity, reduced waste, and a culture of continuous improvement
What is Jidoka?
The word “Jidoka” is derived from the Japanese word “自働” which translates to “automation with a human touch.”
At its core, Jidoka is about building quality into the production process, rather than relying solely on post-production inspection.
By empowering operators to identify and respond to abnormalities, it helps organizations achieve higher levels of quality, efficiency, and continuous improvement.
Jidoka, a core principle of the Toyota Production System (TPS), is a quality control technique that empowers workers to stop production when a defect is detected.
Brief History and Origins of Jidoka
The concept of Jidoka was pioneered by Sakichi Toyoda, the founder of Toyota Industries, in the early 1900s. Toyoda developed an automatic loom that could detect a broken thread and stop the machine automatically, preventing the production of defective fabrics.
This innovation laid the foundation for the Jidoka principle, which was later expanded and integrated into the broader Toyota Production System.
Jidoka as a Key Principle of Lean Manufacturing
Jidoka is one of the two pillars of the Toyota Production System, along with just-in-time (JIT) production. While JIT focuses on the efficient flow of materials and information, Jidoka ensures that quality is built into the manufacturing process.
By empowering workers to stop the production line when a problem is detected, Jidoka helps to identify and resolve issues at the source, preventing the propagation of defects throughout the system.
This, in turn, supports the lean manufacturing principles of waste reduction, continuous improvement, and customer satisfaction.
The Four Elements
- Detecting abnormalities
- Stopping production
- Taking corrective actions
- Preventing recurrence
The Four Elements of Jidoka
At the heart of the Jidoka philosophy are four key elements that work together to ensure quality and prevent defects. Let’s take a closer look at each of these components:
Detecting Abnormalities
The first step is being able to quickly and accurately detect any abnormalities or defects in the manufacturing process. This can be achieved through a combination of automation, sensors, and empowered human operators.
Automated systems and smart technologies can be programmed to continuously monitor production and identify issues as they arise. Meanwhile, well-trained operators are taught to be hyper-vigilant, using their senses and expertise to spot even the slightest irregularities.
The key is creating a culture where everyone is responsible for quality control.
Stopping Production
When an abnormality is detected, the next critical step is to immediately stop the production line. This is a core tenet – giving operators the authority and obligation to halt the process if they notice a problem.
By stopping the line, companies can prevent further defects from being produced and accumulating. It also ensures that the issue can be addressed in real time before it snowballs.
Stopping production may seem counterintuitive, but it’s a necessary evil that leads to long-term gains in quality and efficiency.
Taking Corrective Actions
With production halted, the next phase is to rapidly investigate the root cause of the problem and take corrective actions. This is where the problem-solving and continuous improvement aspects of Jidoka come into play.
Cross-functional teams will quickly gather data, analyze the issue, and implement fixes to resolve the immediate concern. But they don’t stop there – they also work to understand why the problem occurred in the first place so they can put preventative measures in place.
Preventing Recurrence
The final element is perhaps the most important – ensuring that the same defect or abnormality never happens again.
This could involve updating standard operating procedures, providing additional training for operators, upgrading equipment, or implementing poka-yoke (mistake-proofing) systems. The goal is to create a self-regulating production process that is highly resistant to errors.
By addressing the root cause and putting controls in place, companies can achieve a true culture of quality and prevent recurring problems.
These four interconnected components – detecting abnormalities, stopping production, taking corrective actions, and preventing recurrence – form the foundation of the Jidoka philosophy.
When executed effectively, this approach leads to improved quality, reduced waste, and a more efficient, reliable manufacturing process.
Jidoka in Practice
Implementing the principles of Jidoka in a manufacturing environment involves several key practices that empower operators and enhance quality control. Let’s explore these practical applications in more detail.
Automation and Sensor-Based Defect Detection
One of the core tenets of Jidoka is the ability to detect abnormalities and defects as soon as they occur. This is often achieved through the integration of automation and sensor-based technologies.
Manufacturers can install a variety of sensors, cameras, and other monitoring devices throughout the production line to continuously scan for quality issues.
These systems are programmed to automatically stop the line or trigger an alert the moment a defect is identified, preventing the problem from propagating further down the line.
This level of real-time defect detection is a hallmark of Jidoka, as it empowers the production process to self-regulate and maintain quality standards without relying solely on manual inspections.
By integrating these automated quality control measures, manufacturers can significantly reduce the chances of defective products reaching the customer.
Manual Quality Control and Jidoka Tags
While automation plays a crucial role, Jidoka also emphasizes the importance of manual quality control measures. Operators are trained to visually inspect products and components at various stages of the manufacturing process.
If an issue is detected, the operator has the authority to pull a Jidoka cord or press a Jidoka button, which immediately stops the production line.
These tags or cords serve as a visual cue to the entire team that a problem has been identified, and prompt immediate action to investigate and resolve the issue.
This empowers operators to be actively engaged in the quality control process, fostering a culture of ownership and continuous improvement.
Empowering Operators to Stop the Line
A key principle of Jidoka is the concept of “Autonomation”, which refers to the ability of operators to stop the production line whenever they detect a problem.
This empowerment is a crucial aspect of the Jidoka approach, as it encourages operators to take ownership of quality and actively participate in problem-solving.
By giving operators the authority to halt the line, Jidoka ensures that issues are addressed at the source, rather than allowing defective products to continue down the line.
This not only improves quality but also fosters a sense of responsibility and collaboration among the workforce, as everyone is invested in maintaining high standards.
Implementing Root Cause Analysis and Problem-Solving
When a production line is stopped due to a quality issue, Jidoka emphasizes the importance of conducting a thorough root cause analysis to understand the underlying problem.
Operators and team members are trained in problem-solving techniques, such as the 5 Whys method, to systematically identify the root cause of the defect.
This focus on problem-solving is a key component of Jidoka, as it helps to prevent the recurrence of the same issues.
By implementing corrective actions and implementing countermeasures, manufacturers can address the root cause and ensure that the problem does not reappear in the future. This proactive approach to quality control is a hallmark of the Jidoka philosophy.
Tired of recurring quality issues in your manufacturing process?
Learn how to systematically identify and eliminate root causes with Root Cause Analysis Training.
Jidoka and Modern Technology
As the principles continue to evolve, the integration of modern technologies has played a crucial role in enhancing its capabilities and expanding its applications beyond the realm of traditional manufacturing.
For teams leveraging IoT and AI in quality control, our Six Sigma Black Belt certification program provides deeper insights into data-driven problem-solving.
Integrating IoT, AI, and Data Analytics for Enhanced Jidoka
The advent of the Industrial Internet of Things (IIoT) has revolutionized the way Jidoka is implemented in the modern manufacturing landscape.
By connecting production equipment, sensors, and control systems, manufacturers can now gather real-time data on the production process.
This data can then be analyzed using advanced analytics and artificial intelligence (AI) algorithms to detect anomalies, predict potential issues, and trigger immediate corrective actions.
For example, IoT-enabled sensors can monitor the performance of machines, detect deviations from optimal operating parameters, and automatically halt production if a problem is detected.
AI-powered systems can then analyze the data, identify the root cause of the issue, and recommend appropriate corrective measures, empowering operators to take swift action and prevent the recurrence of defects.
Furthermore, the integration of data analytics has enabled manufacturers to gain deeper insights into their production processes, allowing them to optimize workflow, reduce waste, and continuously improve quality.
By leveraging predictive analytics, companies can anticipate potential problems before they occur, enabling proactive maintenance and enhancing overall equipment effectiveness (OEE).
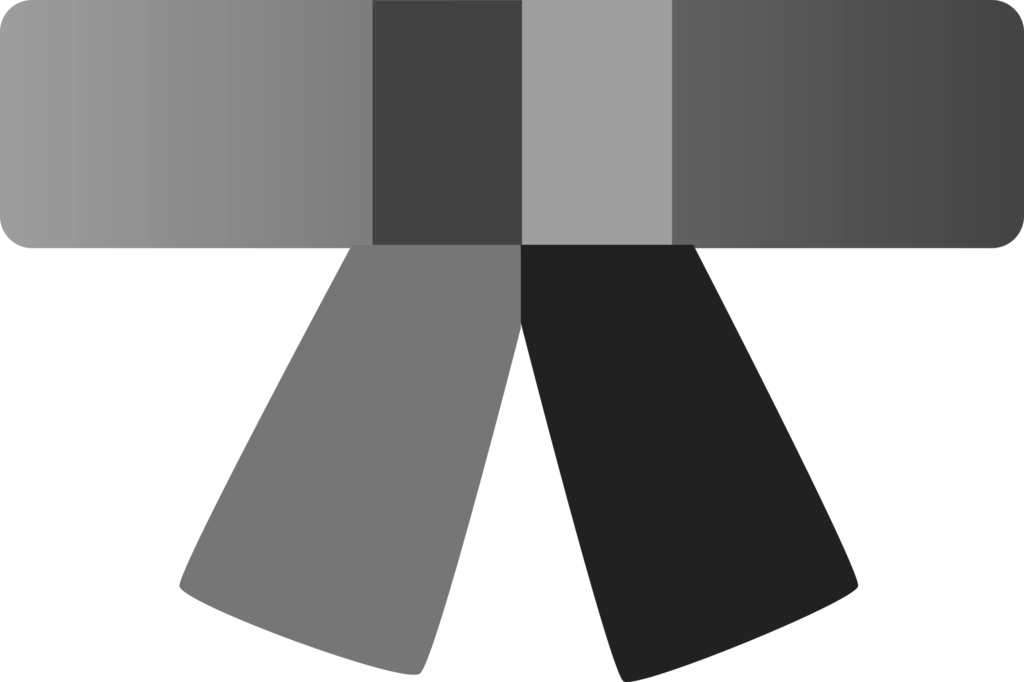
Ready to leverage IoT and AI for breakthrough quality improvements?
Master advanced problem-solving methodologies that transform manufacturing with Six Sigma Black Belt Certification.
Jidoka Applications Beyond Manufacturing
While Jidoka was initially developed and implemented within the manufacturing industry, its principles and practices have since been adapted and applied to various other sectors, showcasing the versatility and scalability of this lean manufacturing concept.
In the healthcare industry, for instance, Jidoka principles have been employed to improve patient safety and quality of care.
By incorporating Jidoka-inspired practices, such as error-proofing and real-time defect detection, healthcare organizations can minimize the risk of medical errors and enhance the overall patient experience.
Similarly, the transportation sector has also benefited from the adoption of Jidoka.
In the aviation industry, for example, these systems can automatically detect and respond to potential safety issues, such as engine malfunctions or structural anomalies, ensuring the safe operation of aircraft.
Leveraging Technology to Improve Quality and Efficiency
The integration of modern technologies, such as IoT, AI, and data analytics, has not only enhanced the capabilities of Jidoka but has also enabled manufacturers to achieve new levels of quality and efficiency.
By leveraging these technologies, companies can automate the detection and correction of defects, reducing the reliance on manual inspections and empowering operators to focus on more value-added tasks.
This, in turn, leads to improved product quality, reduced waste, and increased productivity.
Furthermore, the real-time data and insights provided by these technologies allow manufacturers to make more informed decisions, optimize their processes, and respond to changing market demands more effectively.
This agility and responsiveness are crucial in today’s fast-paced, competitive business environment.
The integration of modern technologies has transformed the way Jidoka is implemented, expanding its applications beyond the traditional manufacturing sector and enabling companies to achieve new levels of quality, efficiency, and continuous improvement.
Implementing Jidoka: A Step-by-Step Guide
Implementing the Jidoka principle in your organization requires a well-structured and comprehensive approach. Here’s a step-by-step guide to help you get started:
Demonstrating Management Commitment
Successful implementation of Jidoka begins with strong leadership and management commitment.
The top-level management must fully understand and embrace this philosophy, as their support and involvement will set the tone for the entire organization.
This includes allocating the necessary resources, providing training, and actively championing the Jidoka initiative across all levels of the organization.
Communicating the Jidoka Message
Once the management commitment is established, the next step is to effectively communicate the Jidoka message throughout the organization.
This involves educating employees on the principles, benefits, and the practical applications, alongside foundational knowledge in the fundamentals of Lean to create a holistic understanding of operational excellence.
Regular training sessions, workshops, and visual displays can help reinforce the Jidoka message and ensure that everyone in the organization is aligned with the goals and objectives.
Conducting Readiness Assessment
Before implementing Jidoka, it’s crucial to assess the readiness of your organization. This includes evaluating your current processes, identifying potential bottlenecks, and assessing the level of employee engagement and understanding of quality control principles.
A thorough readiness assessment will help you identify the areas that require the most attention and develop a tailored implementation plan.
Executing Practical Applications
With the foundation laid, the next step is to start executing practical Jidoka applications within your organization.
This may involve implementing automation and sensor-based defect detection, empowering operators to stop the production line, and establishing robust root cause analysis and problem-solving processes.
It’s important to start with small, manageable pilot projects and gradually scale up as the organization becomes more comfortable with the Jidoka approach.
Throughout the implementation process, it’s essential to continuously monitor and measure the impact of Jidoka on your operations. This will help you identify areas for improvement, refine your approach, and ensure that the benefits are being realized across the organization.
Remember, implementing Jidoka is not a one-time event but a continuous journey of improvement.
Follow this step-by-step guide and maintain a steadfast commitment to quality and efficiency to successfully integrate Jidoka into your organization and reap the numerous benefits it offers.
Benefits of Jidoka
Implementing the principles of Jidoka in your manufacturing operations can unlock a wide range of benefits that positively impact your business. Let’s take a closer look at some of the key advantages.
Improved Product Quality and Customer Satisfaction
At the heart of Jidoka is a relentless focus on quality. By empowering operators to detect and respond to abnormalities, it helps organizations catch defects early in the production process before they make their way to the customer.
This proactive approach to quality control ensures that only high-quality products reach the end user, leading to increased customer satisfaction and loyalty. When defects are minimized, rework and scrap are reduced, further enhancing the overall quality of the final product.
Increased Process Efficiency and Productivity
Jidoka drives efficiency by automating the detection and response to quality issues, reducing the need for constant human supervision.
By automatically stopping the production line when a problem is detected, Jidoka allows operators to focus on addressing the root cause rather than constantly monitoring the process.
This frees up personnel to engage in more value-added activities, improving overall process efficiency and productivity.
Additionally, the built-in error-proofing mechanisms of Jidoka help eliminate wasteful activities, such as rework and unnecessary inspections, further boosting efficiency.
Reduced Waste and Cost Savings
By preventing defects from reaching the customer, Jidoka helps organizations avoid the significant costs associated with product returns, warranty claims, and customer dissatisfaction.
Moreover, the reduction in scrap, rework, and inventory levels resulting from Jidoka’s quality-focused approach leads to substantial cost savings.
Jidoka also supports the principles of lean manufacturing, helping companies eliminate waste in their processes and optimize resource utilization, ultimately enhancing their bottom line.
Fostering a Culture of Continuous Improvement
Jidoka is not just a set of tools and techniques; it’s a mindset that empowers employees to take ownership of quality and actively participate in the improvement of processes.
By giving operators the authority to stop production and address problems, Jidoka fosters a culture of problem-solving and continuous improvement.
This, in turn, encourages team members to be more engaged, proactive, and committed to the organization’s quality objectives, further enhancing the overall effectiveness of the Jidoka implementation.
The benefits of Jidoka extend beyond the immediate improvements in quality and efficiency; they also contribute to the development of a strong quality culture and a mindset of continuous improvement that can drive long-term organizational success.
A Quick Recap
We explored the key aspects of Jidoka, a fundamental principle of lean manufacturing.
Jidoka, also known as “autonomation” or “intelligent automation,” is a critical component of the Toyota Production System that empowers operators to detect and respond to quality issues, stop the production line, and implement corrective actions to prevent recurrence.
The four key elements of Jidoka – detecting abnormalities, stopping production, taking corrective actions, and preventing recurrence – form the backbone of this powerful quality control methodology.
By integrating automation, sensor-based defect detection, and operator empowerment, Jidoka enables organizations to achieve superior product quality, increased process efficiency, and a culture of continuous improvement.
For readers interested in further exploring quality improvement methodologies, pursuing our six sigma certification program can provide a comprehensive framework and tools similar to those embodied in Jidoka.
As modern manufacturing continues to evolve, the importance of Jidoka has only grown. With the advent of Industry 4.0 technologies, such as the Internet of Things (IoT), artificial intelligence, and advanced data analytics, organizations can further enhance their Jidoka capabilities, driving even greater quality, productivity, and waste reduction.
The successful implementation of Jidoka requires a strong commitment from management, effective communication of the Jidoka principles, and a comprehensive readiness assessment to ensure the necessary processes, tools, and mindset are in place.
By taking a step-by-step approach and leveraging Jidoka’s proven benefits, organizations can transform their manufacturing operations, improve customer satisfaction, and position themselves for long-term success.
We encourage readers to explore the Jidoka philosophy, assess its applicability within their organizations, and take the necessary steps to implement this powerful lean manufacturing technique.
By embracing Jidoka, businesses can unlock new levels of quality, efficiency, and operational excellence, positioning themselves for a bright and sustainable future.
SixSigma.us offers both Live Virtual classes as well as Online Self-Paced training. Most option includes access to the same great Master Black Belt instructors that teach our World Class in-person sessions. Sign-up today!
Virtual Classroom Training Programs Self-Paced Online Training Programs