The Zero Defects Concept: Mastering Quality Excellence in Business
Did you know that poor quality costs organizations an average of 15-20% of their annual revenue? In some manufacturing sectors, this figure can climb as high as 40%.
These staggering numbers highlight why quality management has become a cornerstone of successful business operations.
Master Zero Defects with Lean Six Sigma Green Belt Training
Learn proven strategies to eliminate errors and boost performance
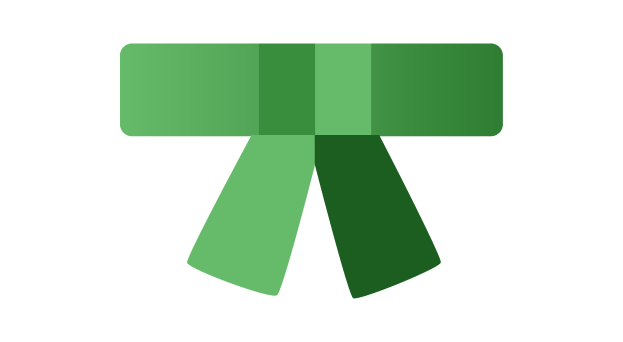
Among the various quality philosophies that have emerged over the decades, the zero defects concept stands out as a particularly influential approach that continues to shape how organizations view quality.
The zero defects definition centers on the idea that products and services should be delivered without any flaws—the first time, every time. Rather than accepting a certain level of errors as inevitable, this philosophy challenges organizations to aim for perfection through prevention rather than inspection and correction.
Quality management has evolved significantly, from basic inspection to modern approaches like six sigma certification programs that complement zero defects initiatives
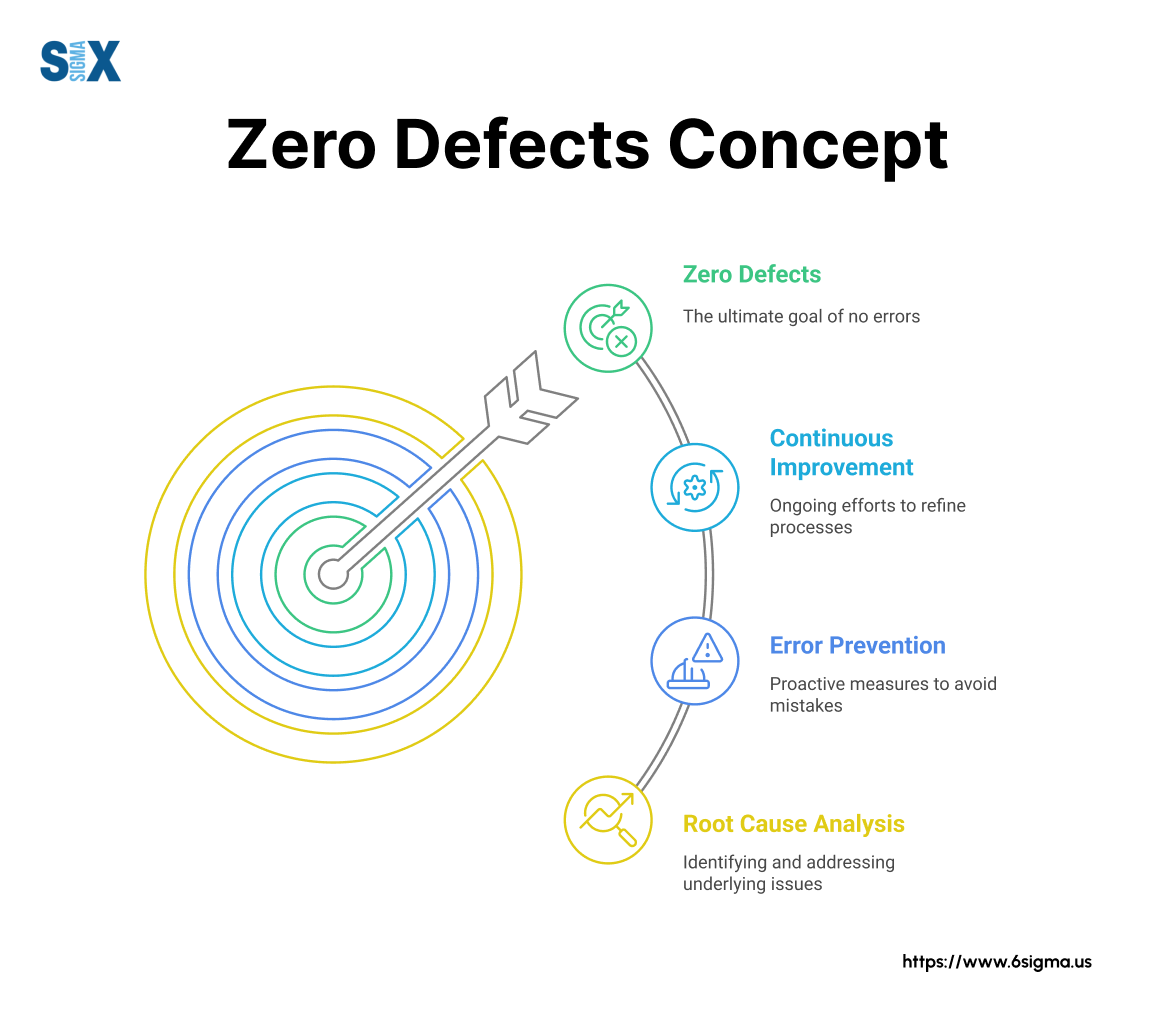
Key Highlights
- What zero defects truly means
- How to implement this quality approach
- Why prevention beats detection
- When this concept works best
- Which tools drive defect elimination
What Is The Zero Defects Concept?
The zero defects concept represents a quality management approach that aims to eliminate errors completely from products, services, and processes.
Unlike quality systems that accept a certain percentage of defects as normal, this philosophy maintains that mistakes are not inevitable and that every task should be performed correctly the first time.
This idea emerged in the 1960s during the space race era when Martin Marietta, an aerospace manufacturer, reduced defects by 54% in just one year through a focused quality program.
Their success caught the attention of quality expert Philip Crosby, who formalized the approach and brought it into mainstream business thinking.
Crosby, through his influential 1979 book “Quality is Free“, established the zero defect philosophy as a management standard. He argued that quality isn’t expensive—what costs money is all the actions involved in failing to create quality from the beginning.
His work challenged the prevailing belief that errors were unavoidable in complex manufacturing processes.
Many people misunderstand the zero defects concept as demanding absolute perfection, which creates resistance to implementation. However, the true focus lies in prevention rather than perfection.
The approach doesn’t expect humans never to make mistakes; instead, it establishes systems that prevent errors from occurring or reaching customers.
Philip Crosby’s zero defects framework rests on four fundamental principles:
- Quality means conformance to requirements, not goodness
- Prevention is the only system that produces quality
- The performance standard must be Zero Defects
- Quality is measured by the price of nonconformance
This philosophy marked a significant shift from traditional quality control methods that relied heavily on inspection to catch defects after they occurred.
Instead, Crosby advocated designing processes that eliminate the possibility of errors happening in the first place—a preventive rather than corrective approach that continues to influence quality management today.
Organizations often combine this approach with lean principles to create robust quality management systems.
The Philosophy Behind Zero Defects
The philosophy of zero defects represents a fundamental shift in how organizations approach quality.
Rather than viewing defects as an expected part of production or service delivery, this philosophy establishes error-free work as both the standard and the expectation.
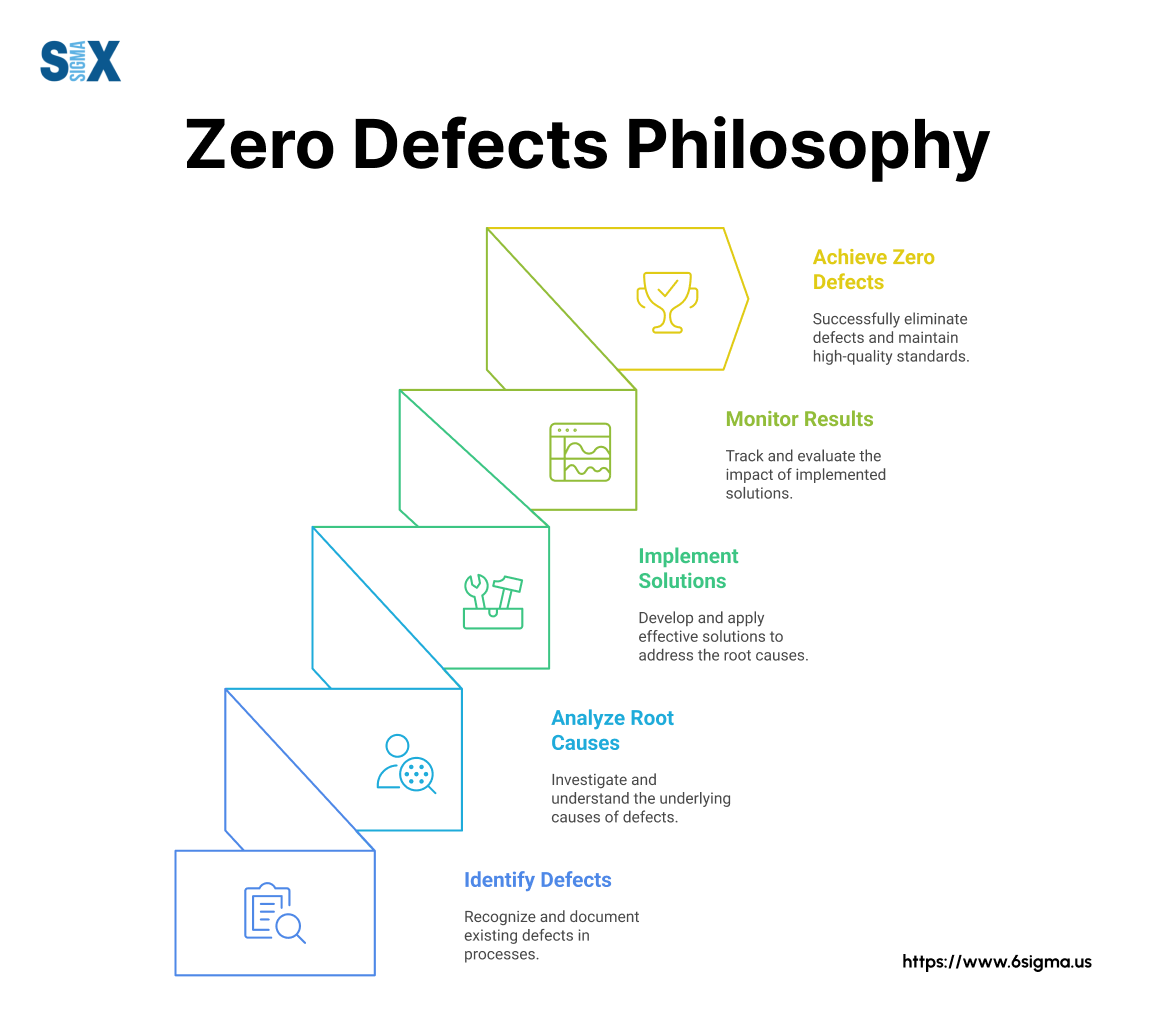
Core Principles of the Zero Defects Concept
Four essential principles form the foundation of the zero defects concept.
First, quality must be defined as conformance to requirements, not as an abstract notion of “goodness” or “excellence.” When requirements are clearly established, teams can precisely measure whether they’ve been met.
Second, quality comes from prevention, not correction. The cost of preventing errors is almost always lower than the cost of fixing them after they occur.
Third, the only acceptable performance standard is zero defects. Setting any other target implicitly communicates that some errors are acceptable.
Fourth, quality is measured by the price of non-conformance. Organizations must quantify what errors cost them in terms of rework, wasted materials, lost customers, and damaged reputation.
Prevention vs. Detection
Traditional quality approaches often rely heavily on inspection to catch defects before products reach customers.
The zero defect mindset flips this model by focusing resources on preventing defects from occurring in the first place.
Prevention strategies include thorough process design, standardized work procedures, mistake-proofing techniques, and addressing root causes of potential problems.
This approach recognizes that inspection can only find defects—it cannot create quality. When organizations build quality into their processes from the beginning, they reduce the need for extensive inspection while achieving better results.
Quality Culture Development
Perhaps the most challenging aspect of implementing the philosophy of zero defects is developing an organizational culture that embraces these principles.
This cultural shift requires:
- Management demonstrating visible commitment to quality standards
- Clear communication of expectations to all employees
- Recognition and celebration of quality achievements
- Training programs that equip workers with necessary skills
- Systems that enable employees to identify and resolve quality issues
The zero defect mindset flourishes when every employee understands their role in delivering quality and feels empowered to take necessary actions.
Organizations that successfully develop this culture find that quality becomes a source of pride rather than merely a requirement to meet.
This philosophy represents more than just a quality program—it’s a fundamental way of thinking about work, responsibility, and excellence that transforms how organizations operate.
When organizations master lean fundamentals , they create an environment where zero defects initiatives can thrive more effectively.
Zero Defects in Lean Manufacturing
Modern manufacturing environments have increasingly adopted the zero defects concept as a critical component of their quality strategy.
This approach aligns naturally with lean manufacturing principles, creating powerful synergies that drive both quality improvements and operational efficiency.
Integration of the Zero Defects Concept with Lean Principles
The zero defect manufacturing philosophy meshes seamlessly with lean thinking.
Both methodologies share a focus on eliminating waste—with defects representing one of the most costly forms of waste in any production system.
When a company implements zero defects manufacturing, they naturally address several lean wastes simultaneously:
Defects waste materials and resources that went into creating the flawed product. They also waste the labor hours spent producing items that cannot be sold at full value.
Overprocessing occurs when organizations build extensive inspection and rework systems rather than preventing defects initially.
Waiting happens when production stops due to quality issues that could have been prevented.
Many manufacturers find that their lean initiatives gain momentum when paired with a zero defects approach.
For example, Toyota’s production system—often considered the gold standard of lean manufacturing—incorporates the concept of jidoka (automation with human intelligence) that stops production immediately when defects occur, preventing their multiplication and enabling immediate problem-solving.
Role in Quality Management
Within quality management systems, the zero defects concept serves as both a philosophy and a practical approach.
Unlike statistical quality control methods that might accept a certain percentage of defects as inevitable, zero defect manufacturing establishes perfection as the only acceptable standard.
This approach drives organizations to implement error-proofing devices (poka-yoke), visual management systems, and standardized work procedures that prevent errors from occurring.
For instance, automotive manufacturers might install sensors that verify correct component placement before allowing assembly to proceed, or use color-coded connectors that physically cannot be connected incorrectly.
The role of this philosophy extends beyond the production floor. It influences how organizations design products, select suppliers, train employees, and measure performance.
Companies that embrace zero defects manufacturing typically develop more robust supplier quality programs and invest more heavily in employee skill development.
Comparison with Six Sigma
While both the zero defects concept and Six Sigma target quality improvement, they differ in several important ways:
Six Sigma accepts a statistical approach to quality, aiming for 3.4 defects per million opportunities—extremely good, but not literally zero.
The zero defects concept establishes zero as the only acceptable target, though practitioners recognize perfection may not always be achieved.
Six Sigma relies heavily on statistical tools and data analysis to drive improvements. Zero defects emphasizes prevention through proper training, clear standards, and error-proofing.
Six Sigma typically organizes improvement work through formal projects led by specially trained experts. Zero defects functions more as a philosophy that guides daily work for all employees.
Many organizations find value in combining elements of both approaches.
The statistical rigor and problem-solving methodology of Six Sigma can help identify where and why defects occur, while the zero defects concept provides the philosophical foundation and cultural elements needed for sustained quality excellence.
Many organizations find value in combining zero defects with other methodologies. Professionals often pursue six sigma certification to strengthen their quality improvement capabilities.
Those seeking advanced expertise typically progress to six sigma black belt certification for comprehensive problem-solving skills.
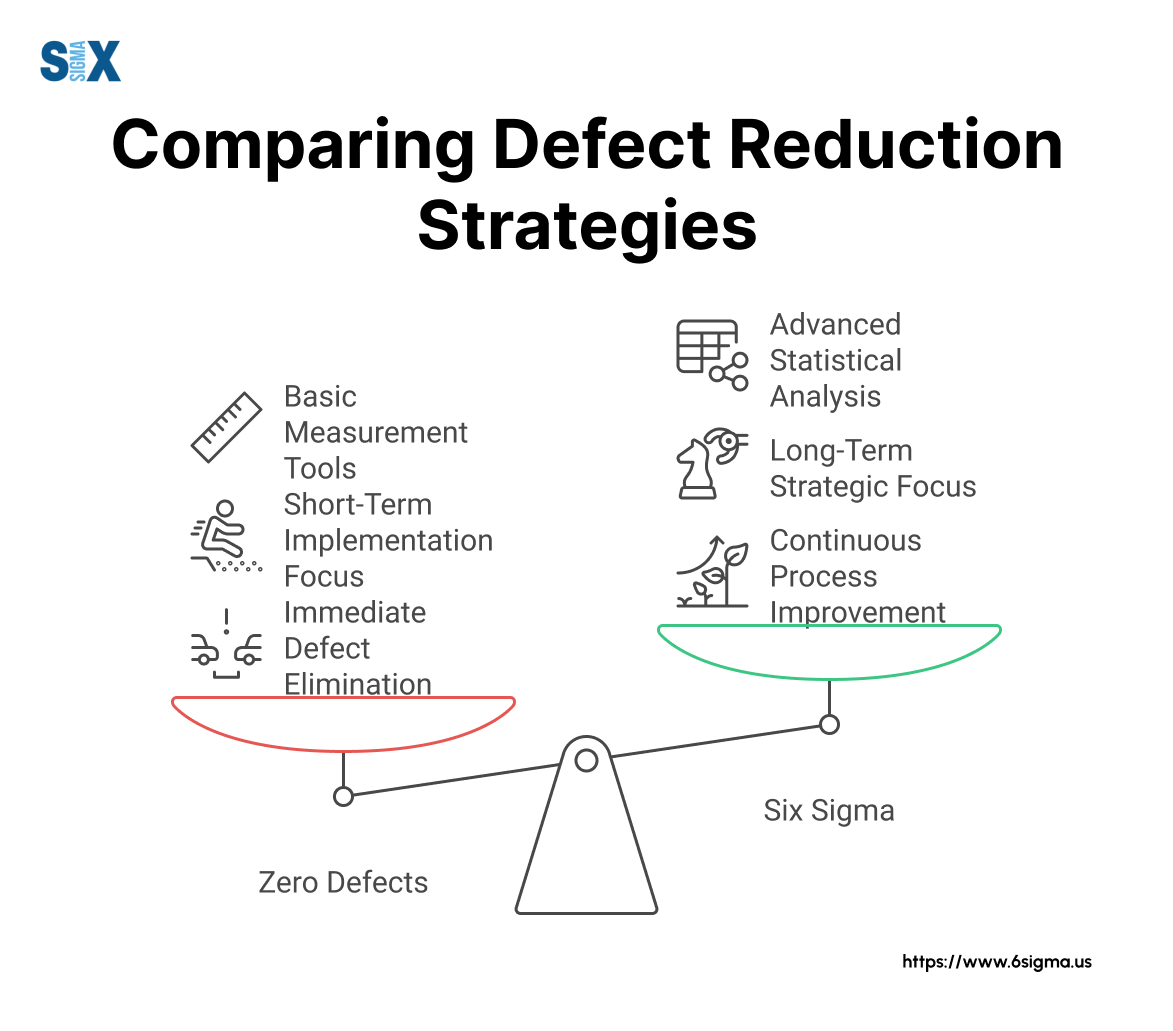
Implement Zero Defects in Manufacturing!
Discover how to integrate zero defects into lean manufacturing with Lean Six Sigma Green Belt Certification.
Implementing Zero Defects
Moving from theory to practice in the zero defects concept requires structured implementation and organizational commitment.
Crosby’s 14 Steps
Philip Crosby outlined a 14-step program for achieving zero defects that remains relevant today.
These steps provide a roadmap for organizations beginning their quality journey:
- Management commitment must be established and communicated throughout the organization.
- Quality improvement teams with representatives from each department should be formed to guide the implementation.
- Quality measurement appropriate to each activity must be established where none exists.
- The cost of quality should be evaluated to identify where quality improvement will be profitable.
- Quality awareness must be raised among all employees through regular communication.
- Corrective action procedures should be implemented to address problems identified.
- Establish a zero defects committee and program to prepare for the formal launch.
- Supervisor training ensures all managers can actively fulfill their role in the quality process.
- Hold a “Zero Defects Day” to signal to employees that the company has a new performance standard.
- Goal setting encourages individuals to establish improvement targets for themselves and their groups.
- Error cause removal involves employees communicating to management the obstacles they face in achieving error-free work.
- Recognition programs acknowledge those who participate and meet quality goals.
- Quality councils bring quality professionals together regularly to share experiences and ideas.
- Do it all over again to emphasize that quality improvement never ends.
These steps provide structure, but successful implementation requires tailoring them to fit specific organizational contexts and challenges.
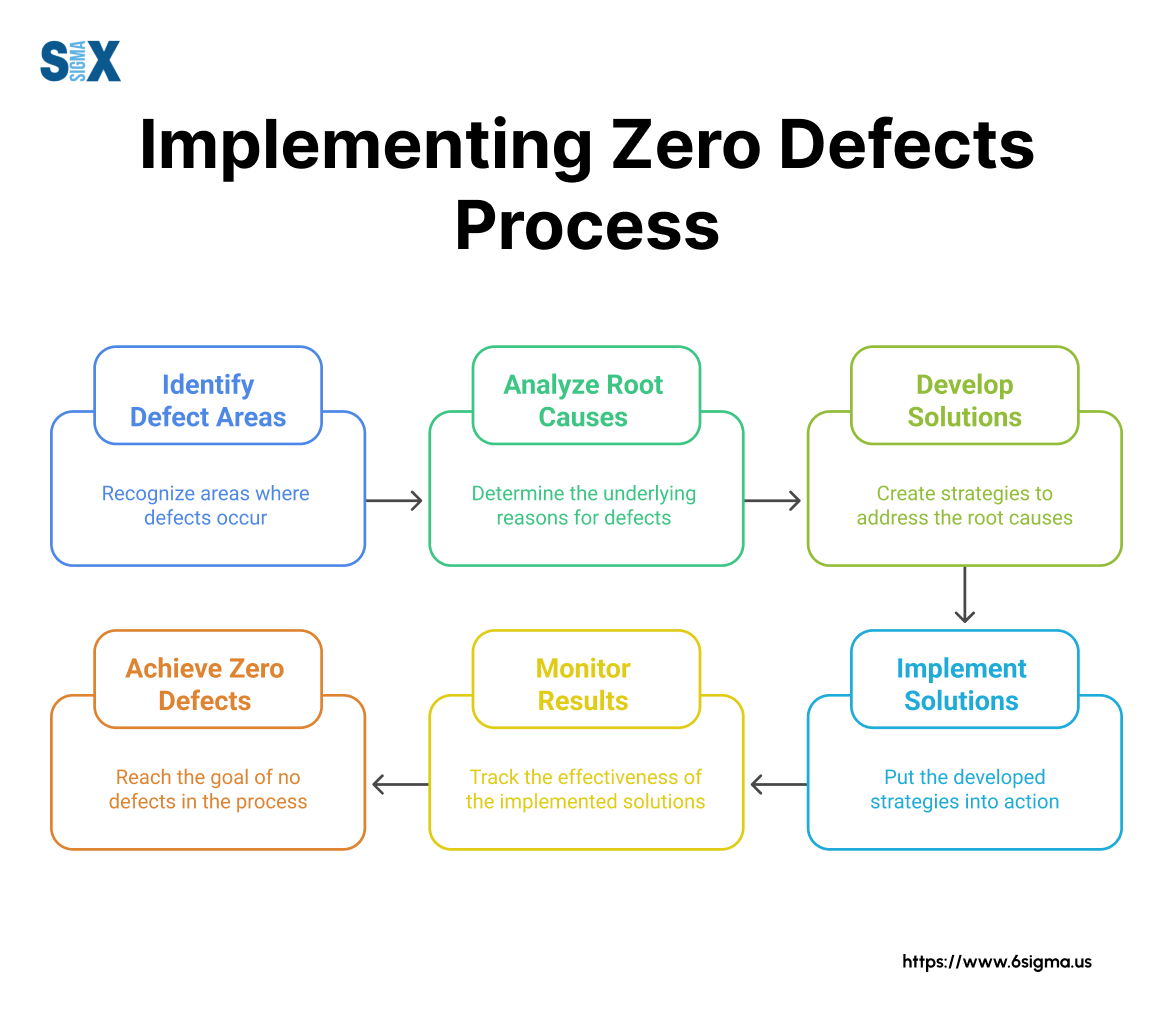
Tools and Techniques
Several practical tools support zero defect quality implementation:
Poka-Yoke (mistake-proofing) devices physically prevent errors from occurring. For example, a manufacturing assembly might include components that can only fit together in the correct orientation.
Statistical Process Control (SPC) monitors processes to detect variations that might lead to defects, allowing for correction before defects occur.
Quality circles bring together small groups of employees to identify, analyze, and solve work-related problems, particularly those affecting quality.
Standard Operating Procedures (SOPs) document the correct way to perform tasks, reducing variation and preventing errors caused by inconsistent methods.
Visual management tools make standards visible and deviations obvious, enabling quick identification and correction of potential quality issues.
These tools work most effectively when integrated into daily operations rather than applied as isolated techniques.
Cultural Transformation
Perhaps the most challenging aspect of implementing the zero defects concept is the required cultural transformation.
Technical tools alone cannot achieve zero defect quality without corresponding changes in organizational values, beliefs, and behaviors.
This transformation begins with leadership demonstrating genuine commitment to quality through their decisions, resource allocation, and personal behavior.
When employees see leaders prioritizing quality over short-term production goals, they understand the organization truly values defect-free work.
Training plays a crucial role in cultural transformation. Employees need both technical skills to perform their work correctly and problem-solving skills to address quality issues as they arise. Effective training programs emphasize not just how to do tasks but why quality matters.
Effective implementation requires strong root cause analysis skills to identify and address the source of potential defects before they occur.
Learn to identify and eliminate the source of quality issues
Develop problem-solving skills that prevent defects with Root Cause Analysis Training.
Challenges and Solutions
While the zero defects concept offers significant benefits, organizations frequently encounter obstacles during implementation.
Common Implementation Barriers of the Zero Defects Concept
Several barriers typically emerge when organizations pursue zero defects quality. Misunderstanding the concept represents one of the most significant hurdles.
Many employees and even managers interpret “zero defects” as demanding absolute perfection, creating anxiety and resistance. This misinterpretation leads to the belief that the standard is unrealistic and unattainable.
Resource constraints also present challenges. Implementing new quality systems requires investment in training, tools, and sometimes equipment modifications.
Organizations facing budget pressures may hesitate to allocate these resources, particularly when benefits might not materialize immediately.
Existing organizational culture can work against zero defects quality initiatives. Companies with a history of accepting defects as normal or blaming individuals rather than examining processes will find the transition particularly difficult.
The entrenched mindset of “we’ve always done it this way” becomes a powerful force of resistance.
Overcoming Resistance
Successful organizations address these challenges through strategic approaches. Clear communication stands as the first critical step in overcoming resistance.
Leaders must explain that the zero defects concept focuses on prevention and continuous improvement rather than punishing imperfection. Emphasizing that the goal is to design systems that make it easier to do things right helps alleviate anxiety.
Pilot programs demonstrate value before full-scale implementation. By selecting a specific process or department for initial implementation, organizations can generate success stories that build momentum. These early wins provide tangible evidence of the benefits and help convert skeptics.
Measuring Success with the Zero Defects Concept
Effective measurement systems prove essential for sustaining zero defects quality initiatives. Organizations need both process measures (leading indicators) and outcome measures (lagging indicators) to evaluate progress.
Process measures might include the percentage of employees trained in quality methods, the number of error-proofing devices implemented, or the frequency of quality audits.
These metrics indicate whether the organization is taking the actions necessary to prevent defects.
Outcome measures track actual quality results, such as defect rates, customer complaints, warranty claims, or rework costs.
These metrics reveal whether prevention efforts are producing the desired effects. The most mature organizations also measure the cost of quality, tracking both prevention costs and failure costs to demonstrate the financial impact of their quality initiatives.
Regular review of these metrics helps organizations identify areas needing additional attention and celebrate progress.
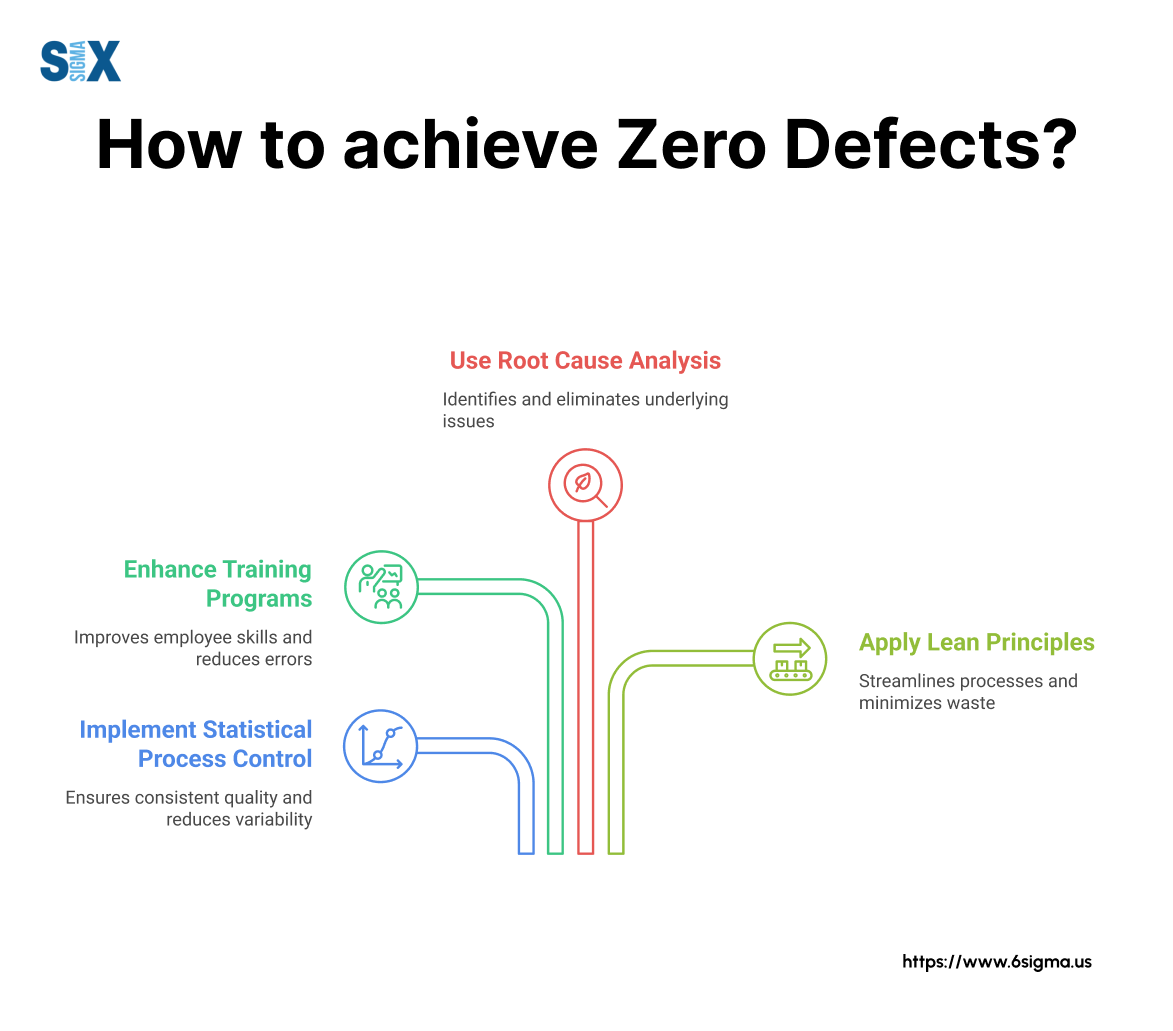
Future of Zero Defects
The zero defects concept, while rooted in mid-20th century manufacturing, continues to evolve with technological advancements and changing business environments.
Technology Integration
Modern technology offers powerful tools for achieving zero defect quality that weren’t available when Crosby first developed his philosophy.
Machine learning algorithms now detect subtle patterns that might indicate potential defects before they occur.
Automation technologies eliminate human error in repetitive tasks while maintaining consistency that manual processes struggle to achieve.
Digital twins—virtual replicas of physical products or processes—enable companies to simulate and test changes before implementation, identifying potential quality issues without risking actual production.
Industry 4.0 Impact of Zero Defects Concept
The fourth industrial revolution, characterized by smart factories and interconnected systems, creates new possibilities for the zero defects concept.
Real-time monitoring through Internet of Things (IoT) sensors provides immediate feedback on process conditions, enabling instant corrections when parameters drift toward potential defect territory.
Blockchain technology offers unprecedented traceability throughout supply chains, helping organizations identify and address quality issues at their source.
When combined with supplier quality management programs, this transparency strengthens quality control across organizational boundaries.
Emerging Trends
Several emerging trends are reshaping how organizations approach zero defect quality.
Customer-defined quality has gained prominence, with organizations seeking to understand and deliver on increasingly personalized expectations rather than applying universal standards.
This shift requires more flexible quality systems that can adapt to varying requirements.
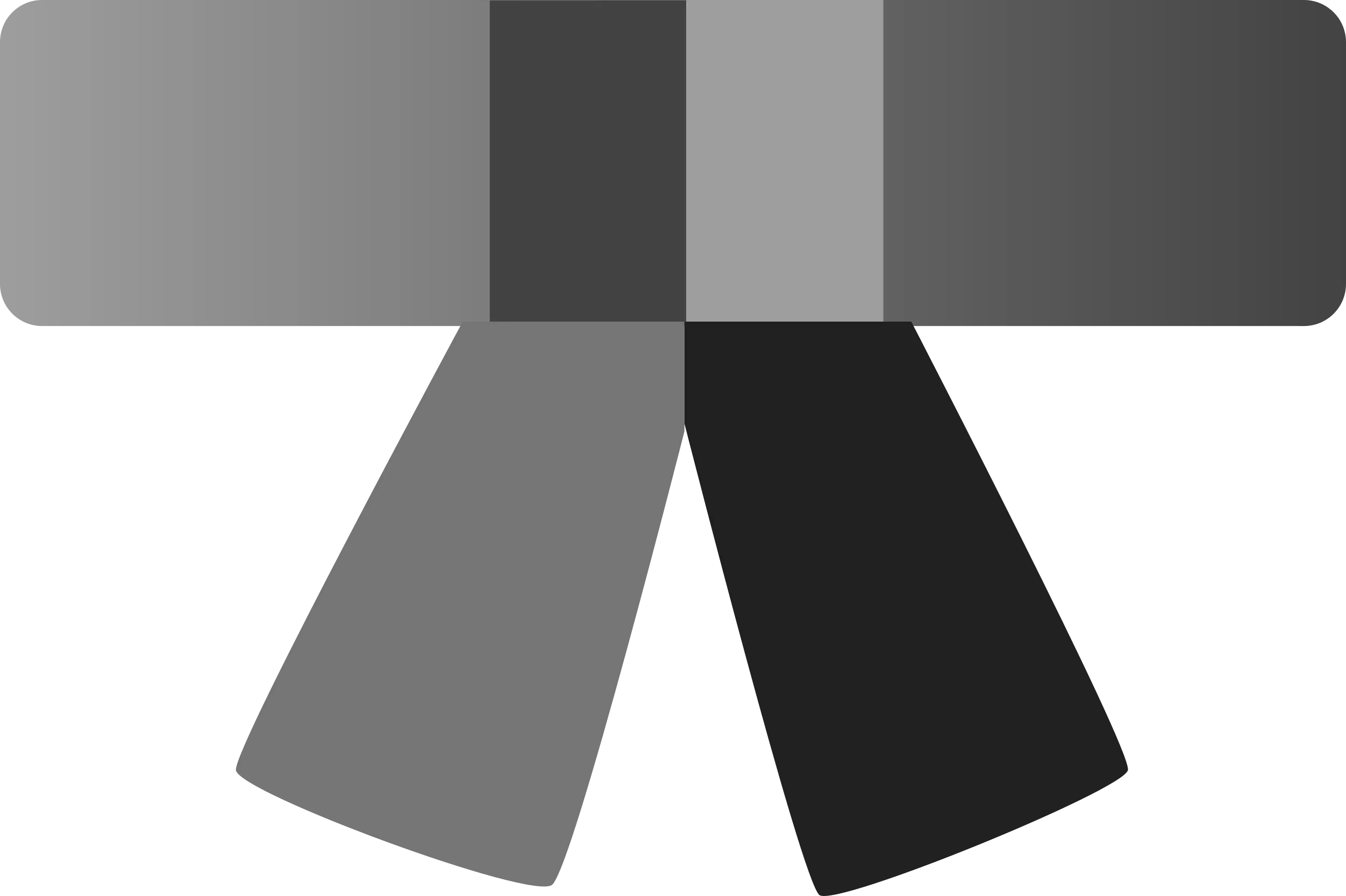
Advance Your Quality Management Expertise
Become a quality improvement leader and gain advanced skills to drive organizational excellence with
Six Sigma Black Belt Certification.
Conclusion
The zero defects concept remains a powerful approach to quality management that delivers significant benefits when properly implemented.
From its origins in aerospace manufacturing to today’s digital enterprises, the core philosophy of prevention over correction continues to prove its value.
Organizations that successfully implement this approach typically experience reduced costs, improved customer satisfaction, and enhanced employee engagement.
They create cultures where quality becomes everyone’s responsibility rather than the domain of specialized departments.
To begin your journey toward zero defect quality, start by assessing your current quality costs and establishing clear requirements for your products and processes. Build prevention into your systems, invest in employee training, and measure both your efforts and results consistently.
SixSigma.us offers both Live Virtual classes as well as Online Self-Paced training. Most option includes access to the same great Master Black Belt instructors that teach our World Class in-person sessions. Sign-up today!
Virtual Classroom Training Programs Self-Paced Online Training Programs