Understanding Turnaround Time: A Comprehensive Guide
Time is a precious commodity. Whether you’re a manufacturer trying to optimize production cycles, a logistics provider aiming to speed up deliveries, or a service provider wanting to boost customer satisfaction, truly grasping turnaround time could be huge.
Turnaround time, or TAT for short, measures the duration between a process starting and finishing.
It encompasses a task’s full lifespan, from when a request is submitted until the desired outcome arrives. Across many industries, turnaround time serves as an efficiency, productivity, and success gauge.
From refining manufacturing workflows to enhancing supply chain operations and bettering the customer experience, mastering trimming turnaround times can yield massive wins. Things like cost savings, increased earnings, and competitive advantages in the market.
Key Highlights
- Defining turnaround time and its variations across industries, such as cycle time, downtime, outages, and plant turnarounds.
- Understanding its critical importance for efficiency, productivity, profitability, customer satisfaction, market retention, cost reduction, and revenue generation.
- Calculating turnaround time using formulas that incorporate completion time, arrival time, burst time, waiting time, lead time, and throughput.
- Examining practical examples and use cases in manufacturing, computing, logistics, shipping, laboratory testing, and data processing.
- Identifying industry-specific and operational factors that can influence it, such as sample quality, instrument calibration, engineering considerations, preventive maintenance, scheduling, communication, and post-turnaround reporting.
- Exploring proven strategies to improve turnaround time, including effective planning and preparation, vertical integration, automation, workforce development, process optimization, waste elimination, and the incorporation of emerging technologies like drones and sensors.
- Showcasing success stories and case studies from various industries, including power generation, oil refining, manufacturing, warehouse logistics, e-commerce fulfillment, healthcare, and laboratory testing services.
- Examining the benefits of optimizing turnaround time, such as cost savings, increased revenue, improved safety, reduced downtime, and enhanced customer experiences and brand perception.
- Exploring future trends and emerging technologies that could revolutionize turnaround time management, including Industry 4.0, smart manufacturing, the Internet of Things (IoT), machine learning, predictive maintenance, collaborative robotics, and augmented reality.
What is Turnaround Time?
Turnaround time, often referred to as TAT, is a measure of the duration between the initiation of a process and its completion. It encompasses the entire lifecycle of a task, from the moment a request is submitted until the desired outcome is achieved.
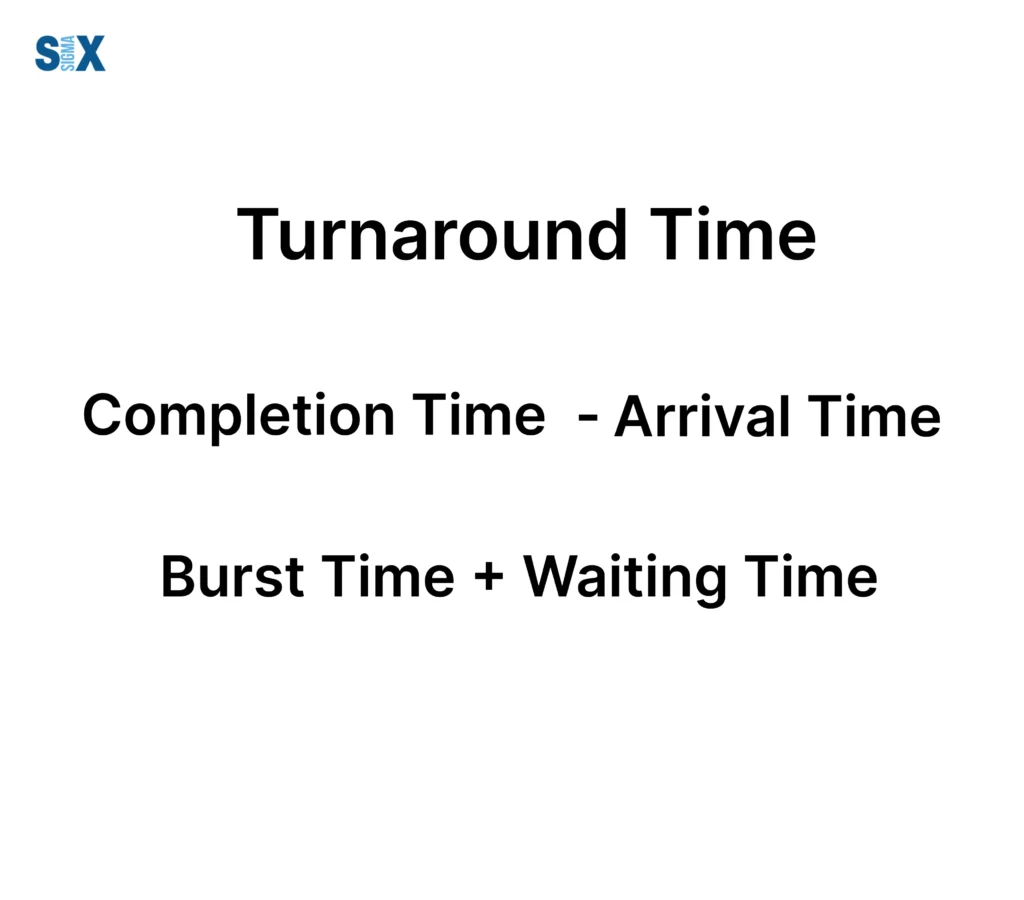
Depending on the industry, turnaround time may also be known by various other terms, such as:
- Cycle time: The time it takes for a machine or process to complete one cycle of operation.
- Downtime: The period during which a plant, facility, or asset is offline for maintenance, repairs, or upgrades.
- Outage: A planned or unplanned shutdown of operations for maintenance or emergency repairs.
- Plant turnaround: A temporary shutdown of an entire manufacturing plant or facility to conduct comprehensive maintenance, repairs, or upgrades.
Importance of Turnaround Time
Organizations pursuing Six Sigma certification often see accelerated improvements in efficiency, as these programs equip teams with methodologies to systematically eliminate waste and standardize processes.
The significance of turnaround time cannot be overstated, as it directly impacts several critical aspects of business operations:
- Efficiency and productivity: Minimizing turnaround time ensures that resources, equipment, and personnel are utilized optimally, maximizing output and minimizing idle time.
- Profitability: Shorter turnaround times translate into higher production volumes, reduced costs, and increased revenue potential.
- Customer satisfaction and market retention: Customers expect prompt service and timely deliveries, making turnaround time a crucial factor in maintaining customer loyalty and a competitive edge in the market.
- Cost reduction: By streamlining processes and eliminating unnecessary delays, businesses can significantly reduce operational costs associated with extended turnaround times.
- Revenue generation: Optimized turnaround times enable businesses to handle more orders, complete more projects, and generate higher revenue streams.
Calculating Turnaround Time
To manage and improve turnaround time effectively, it is essential to clearly understand how to calculate and quantify this metric accurately.
Turnaround Time Formula
The turnaround time formula is typically calculated using one of the following methods:
Turnaround Time = Completion Time – Arrival Time
Turnaround Time = Burst Time + Waiting Time
In these formulas, the key components are:
- Completion Time: The time at which a process or task is fully completed.
- Arrival Time: The time at which a request or process is initiated or submitted.
- Burst Time: The time required to execute a process or task without interruptions.
- Waiting Time: The duration a process or task spends in a queue or idle state before being executed.
It is also important to understand the relationship between turnaround time and other related metrics, such as lead time (the time between order placement and delivery) and throughput (the rate at which a system can process or produce outputs).
Practical Examples and Use Cases
Turnaround time is a critical metric across various industries and applications, including:
Manufacturing
- Measuring the time between the start and completion of a production cycle or the time required for maintenance, repairs, or upgrades.
- Computing: Calculating the duration between submitting a process for execution and receiving the output.
- Logistics: Tracking the time from order submission to order fulfillment and delivery.
- Shipping: Measuring the vessel turnaround time (VTT), which is the time a ship spends at a port between arrival and departure.
- Laboratory testing: Monitoring the time from sample submission to the release of verified test results.
- Data processing: Quantifying the time required to process and analyze data sets.
By understanding and calculating turnaround time accurately, businesses can identify bottlenecks, optimize processes, and make informed decisions to improve overall operational efficiency.
Factors Affecting Turnaround Time
While calculating turnaround time is essential, it is equally important to identify and address the various factors that can influence this metric. By understanding these factors, businesses can develop targeted strategies to mitigate their impact and achieve continuous improvement.
Industry-Specific Factors
Certain factors are unique to specific industries and can significantly impact turnaround time:
Quality of samples
In laboratory testing or manufacturing processes, the quality and purity of input materials can affect the time required for preparation, testing, and quality control.
Instrument calibration
Analytical instruments and equipment must undergo regular calibration and maintenance to ensure accurate and consistent results, which can temporarily impact turnaround times.
Engineering considerations
Complex engineering projects or equipment upgrades may require extensive planning, testing, and implementation, affecting turnaround times for plant shutdowns or maintenance periods.
Preventive maintenance
Regular preventive maintenance schedules can minimize unplanned downtimes but may also temporarily impact turnaround times.
Process standardization: Lack of standardized processes can lead to variability and inefficiencies, prolonging turnaround times.
Operational Factors
In addition to industry-specific factors, several operational aspects can influence turnaround time:
- Scheduling and coordination: Effective scheduling and coordination among various departments, teams, and stakeholders are crucial for minimizing delays and ensuring smooth operations.
- Communication: Clear and timely communication can prevent misunderstandings, reduce rework, and streamline processes, thereby improving turnaround times.
- Management during turnaround periods: Skilled management and oversight during critical turnaround periods, such as plant shutdowns or maintenance activities, can ensure efficient execution and minimize downtime.
- Post-turnaround reporting and analysis: Comprehensive reporting and analysis of turnaround periods can identify areas for improvement and inform future strategies for optimizing turnaround times.
By understanding and addressing both industry-specific and operational factors, businesses can develop holistic approaches to minimize disruptions and achieve consistent improvements in turnaround time.
Strategies to Improve Turnaround Time
These strategies encompass a range of approaches, including meticulous planning, process optimization, and the integration of emerging technologies.
Planning and Preparation
Effective planning and preparation are crucial for minimizing turnaround times and ensuring smooth operations:
- Identifying scope, scheduling, and dry runs: Clearly defining the scope of work, creating detailed schedules, and conducting dry runs can help identify potential bottlenecks and streamline processes before actual execution.
- Vertical integration and automation: Integrating various stages of the process vertically and automating repetitive or labor-intensive tasks can significantly reduce turnaround times and improve consistency.
- Training and workforce development: Investing in six sigma certification programs and developing a skilled workforce can ensure that tasks are executed efficiently, minimizing errors and rework, which often contribute to prolonged turnaround times.
Process Optimization
Continuous process optimization is essential for sustaining improvements in turnaround time:
Reducing bottlenecks and eliminating waste: Identifying and addressing bottlenecks, as well as eliminating non-value-added activities and redundancies, using frameworks taught in six sigma certification programs, can streamline workflows and reduce turnaround times.
Streamlining workflows and standardization: Implementing standardized and optimized workflows can minimize variability, improve consistency, and ensure that processes are executed efficiently, reducing turnaround times.
Incorporating new technologies: Leveraging emerging technologies, such as drones for inspections, sensors for real-time monitoring, and automation solutions, can significantly enhance efficiency and reduce turnaround times across various industries.
By combining strategic planning, process optimization, and technological integration, businesses can achieve significant and sustainable improvements in turnaround time, enhancing their competitive edge and driving long-term success.
Future Trends and Emerging Technologies
Clearly, constantly refining turnaround times will keep propelling industries forward. Fortunately, fast-advancing cutting-edge tech presents exciting chances to revolutionize how we approach and handle this key metric.
Industry 4.0 and Smart Manufacturing
The Fourth Industrial Revolution, or Industry 4.0, represents a manufacturing and factory operations overhaul. By seamlessly integrating advanced tech like IoT, machine learning and real-time monitoring, businesses unleash unprecedented streamlining and productivity levels.
Internet of Things (IoT)
Connected device and sensor proliferation allows real-time data gathering and analysis. This provides invaluable insights into workflows, equipment performance and potential bottlenecks. Following patterns empowers companies making smart choices and proactively addressing issues, minimizing downtime and optimizing turnaround times.
Machine Learning
Leveraging machine learning algorithm power to analyze vast data helps identify patterns and predict maintenance needs while refining processes. By anticipating potential disruptions, companies implement preventative steps reducing unplanned downtime and upgrading overall turnaround times.
Predictive Maintenance and Real-Time Monitoring
Advanced predictive maintenance plus real-time equipment and process monitoring helps businesses transition from reactive to proactive maintenance strategies. Spotting potential issues in advance allows scheduling work during planned downtime, minimizing disruptions and optimizing turnaround times.
The takeaway?
As automation and IoT redefine process management, professionals with Six Sigma certification will be critical to bridging technical advancements with operational excellence
Technologies are revolutionizing how we think about and manage turnaround times. By embracing advancements, we unlock opportunities refining processes from the inside out sustainably.
SixSigma.us offers both Live Virtual classes as well as Online Self-Paced training. Most option includes access to the same great Master Black Belt instructors that teach our World Class in-person sessions. Sign-up today!
Virtual Classroom Training Programs Self-Paced Online Training Programs