Lean Daily Management: The Ultimate Guide to Transforming Operational Excellence
Implementing Lean Daily Management System reported a 25% increase in operational efficiency (which can be interpreted as a boost in productivity) and a 15% improvement in profit margins.
These aren’t just impressive numbers—they represent the real-world impact of a management approach that’s transforming how businesses operate.
Transform your operational approach with expert-guided online learning
Unlock the secrets of lean methodology from the comfort of your workspace with Lean Introduction.
Lean daily management brings structure and visibility to your day-to-day operations, turning chaos into clarity and problems into opportunities. It’s the bridge connecting your strategic goals to daily execution, ensuring everyone stays aligned and focused on what truly matters.
For those already familiar with process improvement, you’ll find that Lean daily management complements your six sigma certification knowledge perfectly, creating a powerful combination for operational excellence.
Key Highlights
- What makes Lean Daily Management truly effective
- Key components for successful implementation
- Practical tools for immediate application
- Real results from diverse industries
What Is Lean Daily Management?
Lean daily management represents a structured approach to running operations that focuses on maintaining standards, identifying problems quickly, and driving continuous improvement through daily activities.
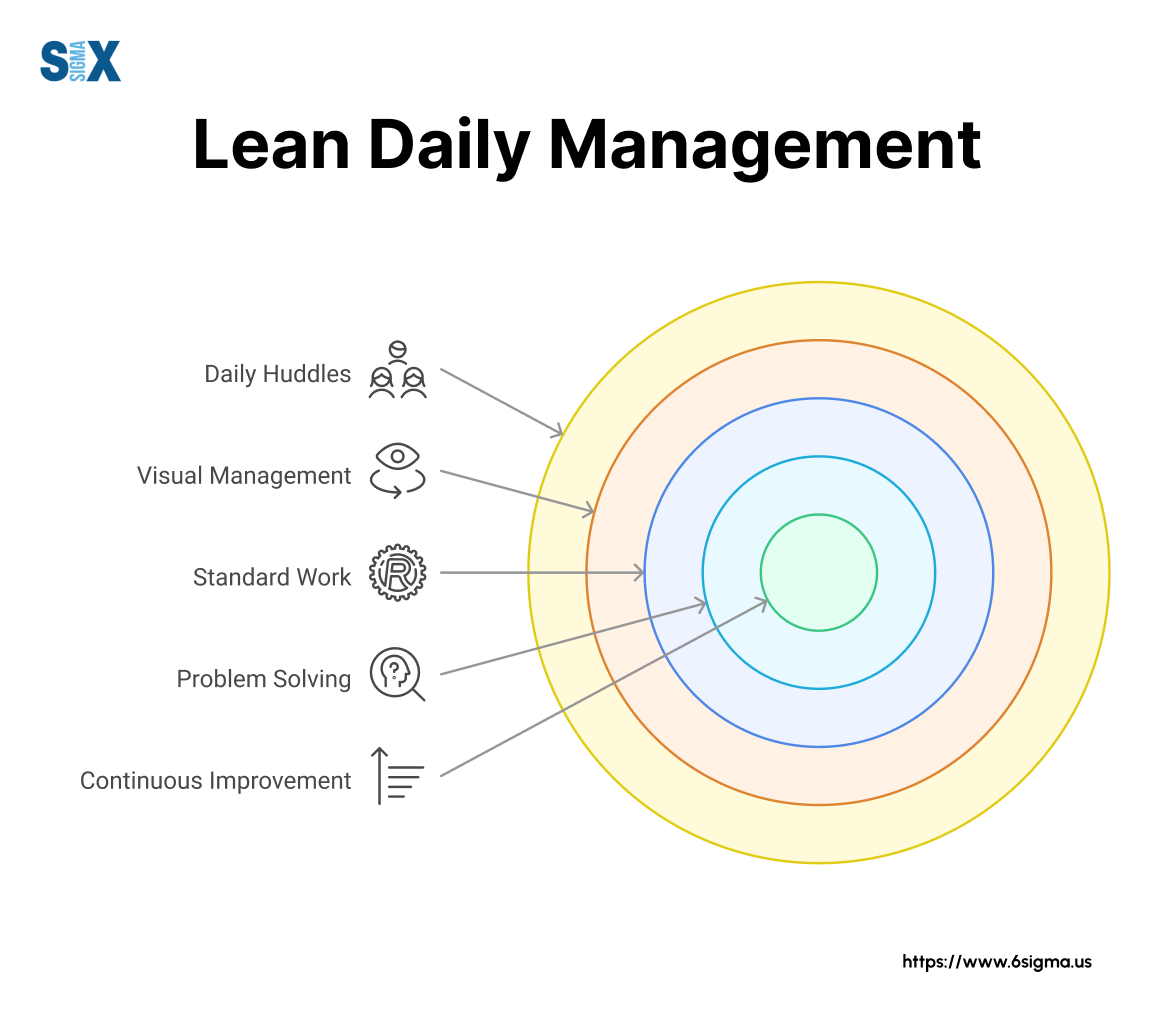
This system emerged from Toyota’s production methods in the 1950s but has since evolved into a versatile management framework used across industries from manufacturing to healthcare.
The definition of lean daily management centers on creating regular, consistent processes that help teams spot issues before they become major problems.
Unlike traditional management that often reacts to issues after they occur, Lean Daily Management establishes rhythms and routines that prevent problems through proactive oversight.
Four key principles form the foundation of any effective lean daily management system:
- Visual transparency – making performance visible to everyone
- Regular cadence – establishing predictable review cycles
- Problem-solving focus – addressing root causes rather than symptoms
- Leader engagement – requiring hands-on involvement from management
These principles work together to create an environment where teams can quickly identify deviations from standards and address them immediately. The daily management approach connects directly to broader lean introduction concepts, providing the day-to-day execution framework that makes lean philosophy practical.
What truly sets lean daily management apart from traditional approaches is its emphasis on process over results.
While conventional management often fixates on outcomes and metrics, Lean Daily Management focuses on stabilizing and improving the processes that deliver those results.
This shift creates sustainable improvement rather than short-term fixes that fail to address underlying issues.
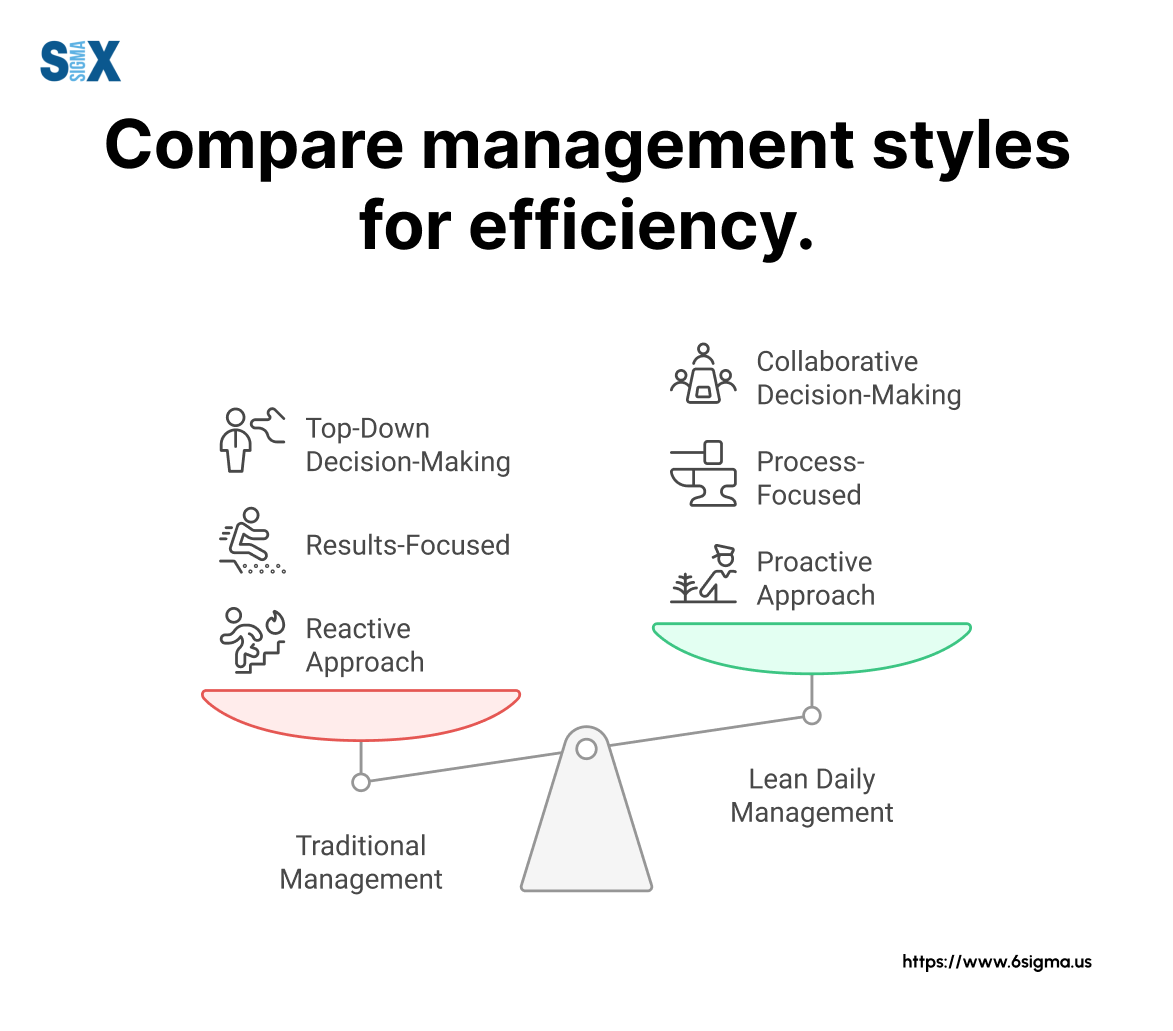
Essential Components of a Lean Daily Management System
A robust lean daily management system consists of several interconnected elements that work together to create structure and drive improvement.
When properly implemented, these components establish the foundation for sustainable operational excellence.
Leader Standard Work (LSW)
Leader Standard Work transforms management from a reactive, firefighting activity into a proactive, structured approach.
LSW defines the specific tasks, checks, and activities leaders must complete on a daily, weekly, and monthly basis to maintain system health.
The power of LSW comes from its ability to shift leadership focus from putting out fires to preventing them in the first place.
When leaders follow standardized routines, they catch problems earlier, coach more effectively, and ensure critical processes receive proper attention.
Effective LSW typically includes three key elements: gemba walks (direct observation of work), performance metric reviews, and coaching interactions.
These activities get scheduled into leaders’ calendars with the same priority as any other critical business function.
For implementation, start small with just a few critical daily activities before expanding. Many organizations begin with a simple checklist approach, then evolve to more sophisticated tracking as the lean daily management system matures.
The goal isn’t perfect adherence but rather creating predictable leadership engagement that teams can count on.
Visual Management Tools and Lean Daily Management
Visual management forms the nervous system of any lean daily management board, making performance, problems, and priorities immediately visible to everyone. These tools eliminate the need to hunt for information by displaying critical data where work happens.
The most common visual tool in a daily management system board is the metrics board. These boards typically track five categories using the SQCDP framework:
- Safety: Incidents, near misses, safety observations
- Quality: Defects, errors, customer complaints
- Cost: Expenses, resource utilization, waste
- Delivery: On-time performance, cycle time, throughput
- People: Attendance, training, engagement
Organizations implement these visual systems in various formats. Traditional physical boards offer high visibility and tactile engagement during team huddles.
Digital solutions provide real-time updates and remote access, particularly valuable for distributed teams. Many companies use a hybrid approach, maintaining physical boards for daily team engagement while backing them with digital systems for data collection and analysis.
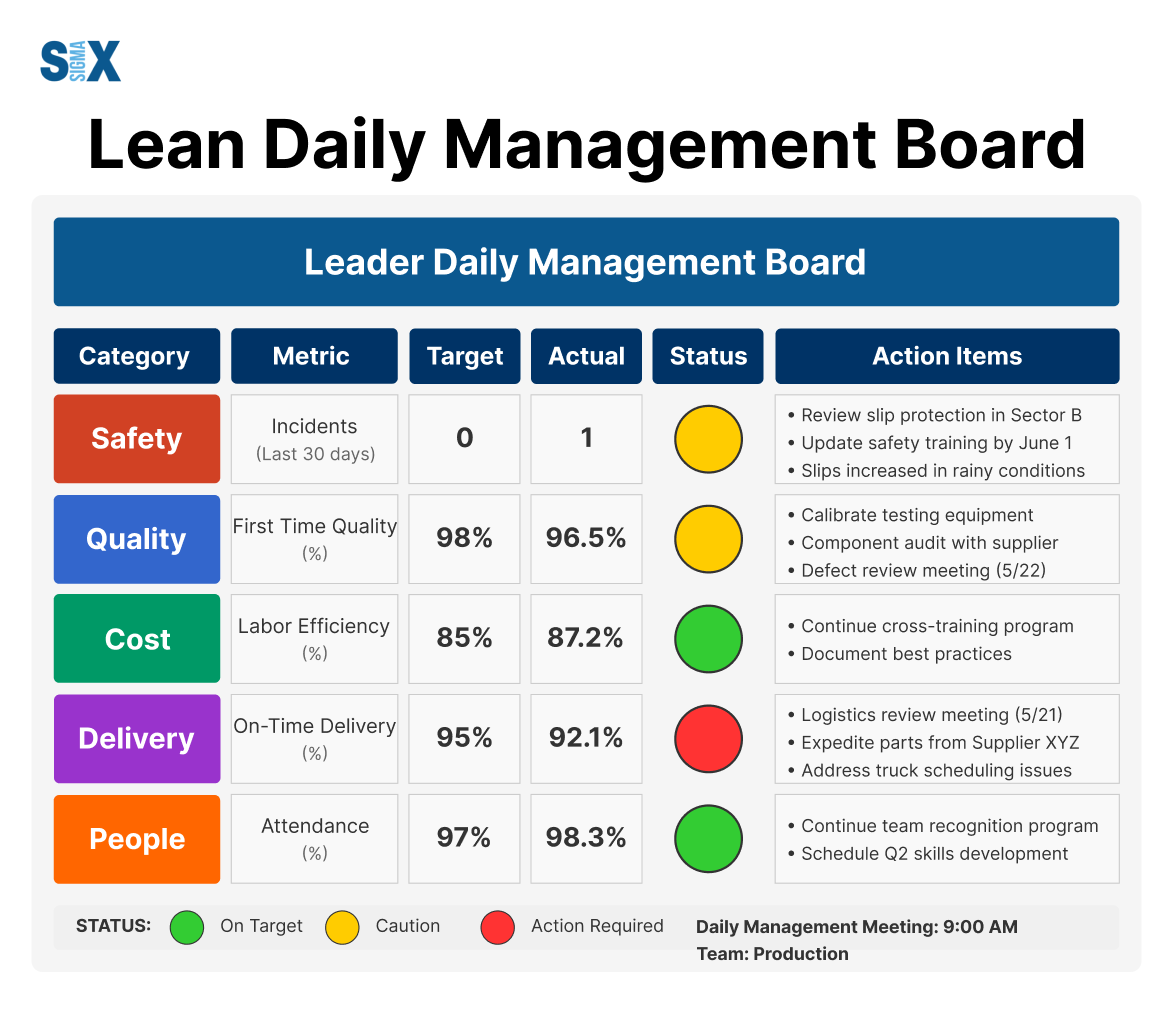
Daily Accountability Processes
The heartbeat of any lean daily management system lies in its regular accountability processes. These structured interactions connect people to performance and drive improvement actions through consistent follow-up.
Tiered huddles form the backbone of this accountability structure. These brief, focused meetings typically follow a cascade pattern:
- Frontline team huddles (5-10 minutes) at shift start
- Supervisor-level huddles (10-15 minutes) shortly after
- Manager-level huddles (15-20 minutes) following supervisor meetings
- Executive huddles (20-30 minutes) to address escalated issues
This tiered approach ensures problems get addressed at the appropriate level while creating clear escalation paths for issues requiring additional resources or authority.
Each level focuses on metrics relevant to their sphere of influence within the daily management system.
Effective communication protocols maintain huddle efficiency. These include standard agendas, time limits, visual cues for status, and clear problem-solving assignments.
The goal isn’t discussion for its own sake but rather focused problem identification and accountability for improvement actions.
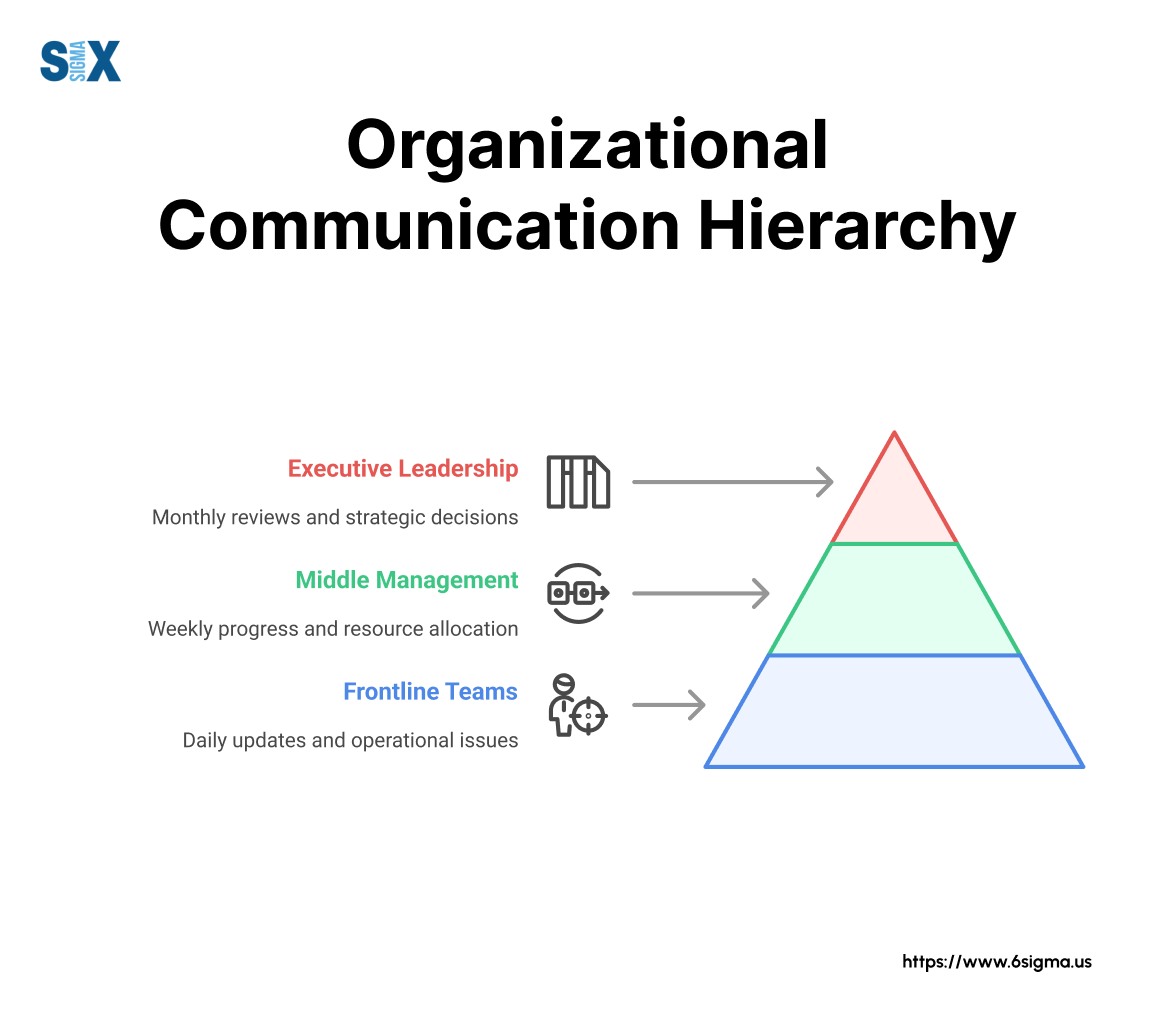
Deep dive into lean principles with hands-on, instructor-led training
Gain internationally-recognized certification and practical project experience with Lean Fundamentals.
Implementing a Lean Daily Management System
Successful implementation of lean daily management requires thoughtful planning and execution.
Organizations that rush into implementation without proper preparation often struggle to sustain their systems.
A methodical approach increases your chances of creating lasting change and meaningful results.
Assessment and Planning Phase
Before launching lean daily management training, smart organizations take time to assess their current state and readiness for change.
This assessment typically examines several key dimensions: leadership commitment, organizational culture, existing management systems, and available resources.
The readiness assessment should identify potential barriers to implementation. Common obstacles include competing priorities, cultural resistance to transparency, and lack of leadership bandwidth.
Identifying these challenges early allows you to develop mitigation strategies before they derail your efforts.
Resource allocation decisions flow directly from your assessment findings. Most organizations underestimate the time investment required, particularly from leaders.
Be realistic about the hours needed for training, coaching, and daily practice. Financial resources matter too—budget for visual management materials, possible technology solutions, and external expertise if needed.
Training represents a critical success factor in lean daily management implementation. Different roles require different training approaches.
Leaders need coaching on standard work practices and effective gemba walks. Facilitators need skills in running effective huddles and problem-solving techniques.
For deeper technical expertise, many organizations find value in formal six sigma certification for key team members who will drive more complex improvements.
Implementation Steps of Lean Daily Management
Successful lean daily management rollouts typically follow a pilot-first approach. Select a single department or value stream with a supportive leader and reasonable complexity.
This controlled environment allows you to test your approach, demonstrate success, and learn valuable lessons before wider deployment.
Your pilot program design should include clear scope boundaries, success metrics, and a realistic timeline. Most effective pilots run for 8-12 weeks—long enough to establish routines but short enough to maintain momentum.
During this period, expect to make frequent adjustments as you learn what works in your specific environment.
When expanding beyond the pilot, a phased roll-out strategy works better than a big-bang approach. Each phase should target logical organizational groupings, with lessons from earlier phases informing later implementations.
This approach builds internal capability while preventing resource overload.
Change management considerations often determine success or failure in lean daily management implementation.
The shift to transparent, data-driven daily management can feel threatening to both leaders and frontline staff.
Address concerns openly, celebrate early wins, and connect the system to meaningful outcomes that matter to participants. Remember that technical excellence without cultural acceptance rarely leads to sustainable results.
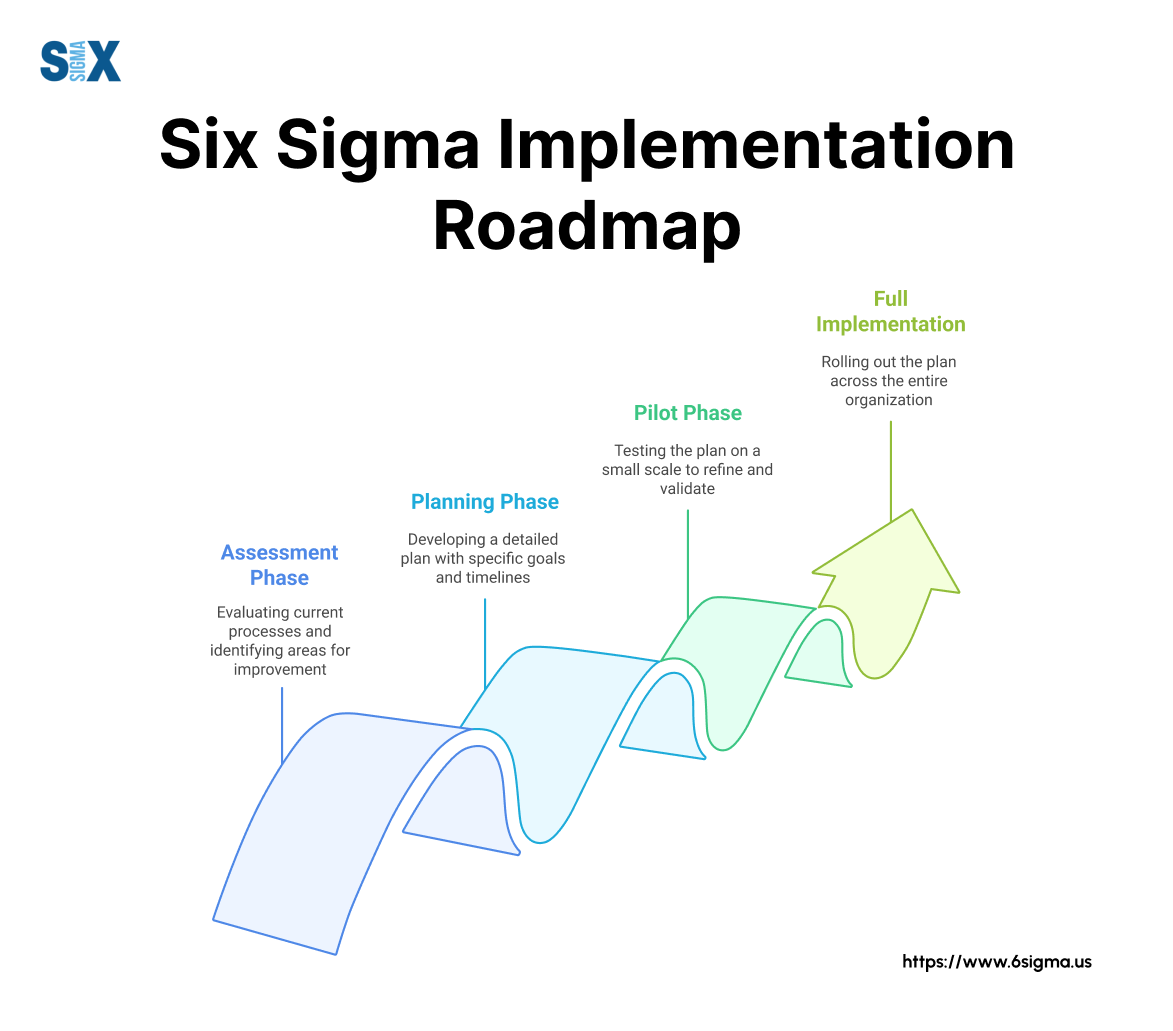
Problem-Solving in Lean Daily Management
Effective problem-solving sits at the heart of lean daily management. While visual boards and huddles make issues visible, it’s the structured problem-solving approach that transforms this visibility into actual improvement.
The best lean daily management systems incorporate simple yet powerful methods that teams can apply consistently.
Many organizations enhance their lean daily management with Six Sigma tools to tackle more complex problems.
The root cause analysis techniques from Six Sigma provide depth when simple fixes aren’t sufficient. Methods like the 5 Whys, fishbone diagrams, and Pareto analysis help teams dig beneath symptoms to address underlying causes.
These tools work particularly well for persistent issues that resist quick solutions.
The PDCA cycle (Plan-Do-Check-Act) provides the fundamental rhythm for problem-solving within lean daily management. Teams identify problems during daily huddles, develop countermeasures, test solutions in small experiments, and standardize effective approaches.
This scientific method creates a learning loop that prevents the same problems from recurring while building team problem-solving muscles.
Successful organizations typically develop a tiered problem-solving approach. Simple issues get addressed through quick daily actions, while more complex problems trigger formal A3 thinking or project-based improvement events.
This tiered approach ensures that problem-solving efforts match the complexity of the issue, preventing both overthinking simple fixes and underpowering complex challenges.

Measuring Success and Continuous Improvement
Measuring the impact of your lean daily management system provides vital feedback on effectiveness while highlighting opportunities for refinement.
Smart organizations track both process metrics (how well the system itself functions) and outcome metrics (business results the system helps achieve).
Process metrics typically include huddle attendance, action item completion rates, and leader standard work adherence.
These indicators reveal whether the daily management system operates as designed. Outcome metrics vary by organization but often include productivity, quality, safety, and cost measures that align with strategic objectives.
Developing effective KPIs requires balancing leading and lagging indicators.
Leading indicators like near-miss reporting or process adherence predict future performance, while lagging indicators like defect rates or productivity confirm actual results.
The best lean daily management systems incorporate both types to provide a complete picture of performance.
As your system matures, continuous improvement becomes increasingly important. Regular gemba walks, system audits, and periodic refresher training help prevent backsliding.
For organizations seeking to deepen their practice, exploring lean fundamentals provides additional tools and concepts to enhance your daily management approach.
Moving Ahead
Lean daily management transforms how organizations operate by creating structure, visibility, and accountability in daily work.
The system connects strategic goals to frontline execution through visual management, leader standard work, and disciplined daily routines. When properly implemented, it drives substantial improvements in efficiency, quality, and employee engagement.
Success requires commitment to the fundamental principles: visual transparency, regular cadence, problem-solving focus, and leader engagement. Organizations that maintain these principles while adapting specific practices to their unique environment see the greatest benefits.
Ready to begin your lean daily management journey? Start with a realistic assessment of your current state, then develop a phased implementation plan that builds capability gradually.
Focus first on establishing the basic rhythm of visual management and daily huddles before adding more sophisticated elements.
Remember that consistency matters more than perfection—even a simple system applied diligently will deliver meaningful results.
SixSigma.us offers both Live Virtual classes as well as Online Self-Paced training. Most option includes access to the same great Master Black Belt instructors that teach our World Class in-person sessions. Sign-up today!
Virtual Classroom Training Programs Self-Paced Online Training Programs